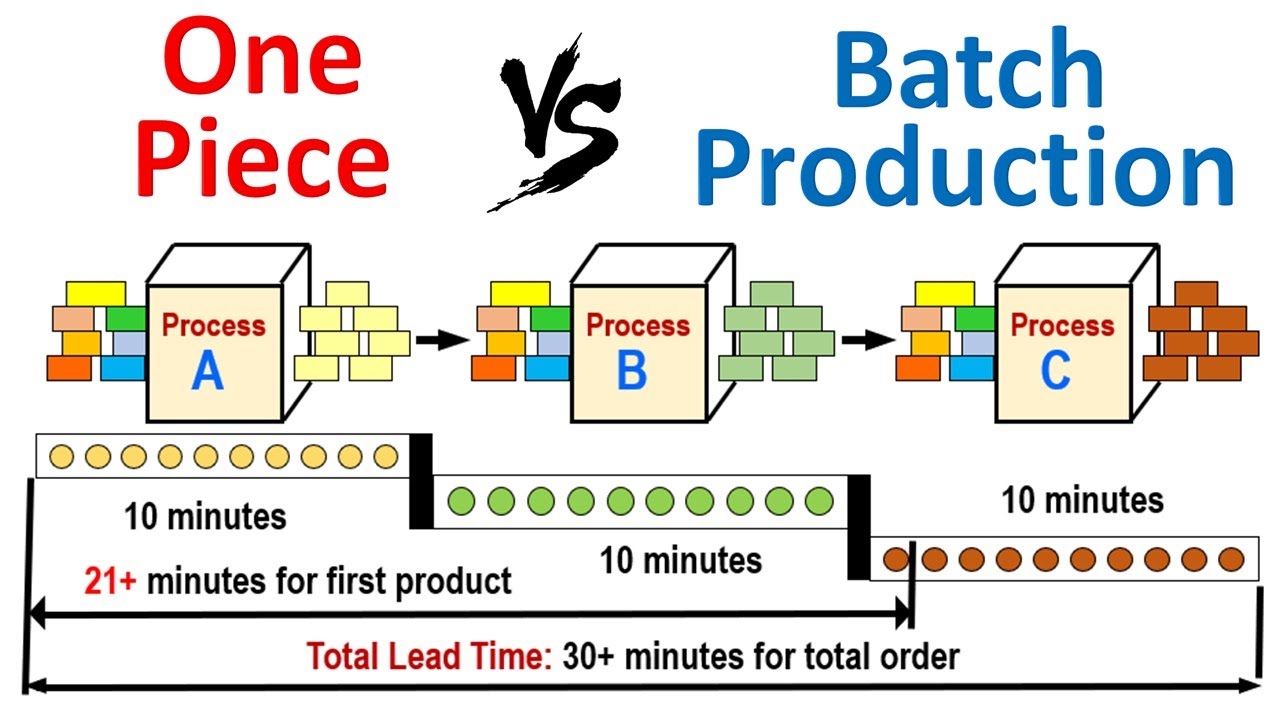
A logistics coordinator is responsible for making sure that goods arrive at the correct place at the right moment and are delivered in the most cost-effective and efficient manner. You'll be responsible for ensuring that goods get delivered to the customer in a timely fashion. Learn more about logistics in this article. You'll also learn about the role of a customer service specialist, Inventory analyst, and supply chain manager. Here are some of the most important jobs you will find in logistics.
Logistics coordinator
Monster lists thousands of logistics coordinator jobs. This job requires lots of hands-on experience. Candidates who have little or no industry experience will be expected to complete the apprenticeship or internship. If you have extensive previous experience in the logistics field, you may also want to consider applying for a job as a logistics coordinator.
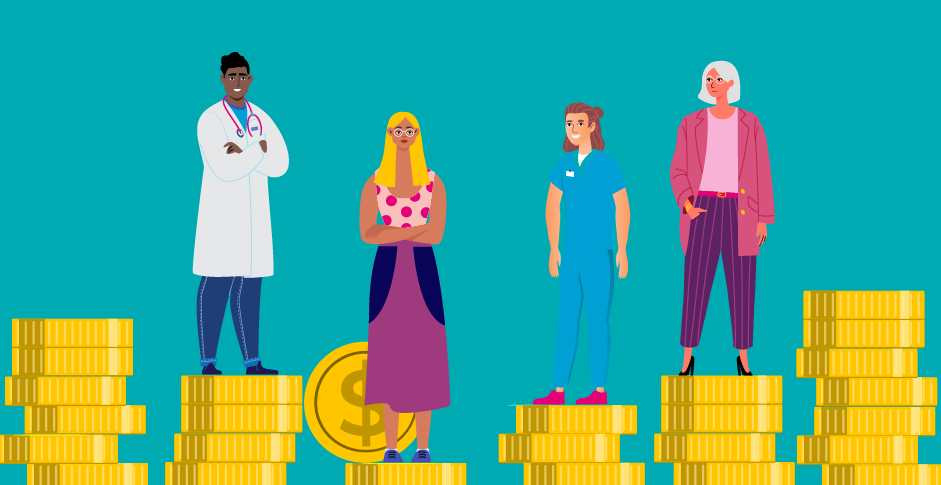
Customer service specialist
Customer service specialists manage and deliver customer service. They interact with customers on a daily basis, coordinate inland transportation, resolve customer complaints, and help them to resolve any issues. They manage customer relationships and also coordinate appointments, record special service requirements, and schedule transportation, warehousing and other activities. As a customer support specialist, you will also coordinate all necessary documents and documentation to ensure timely and affordable delivery.
Inventory analyst
An inventory analyst is responsible for maintaining service levels and improving overall inventory productivity. Their primary responsibilities include order fulfillment for TSC Feed programmes, as well managing the day to day activities of inventory replenishment. They support assortment and merchandise plans by managing inventory levels in their assigned product categories. They analyze trends and data, and plan article-site replenishment in stores. They may also assist with marketing and promotional activities. They often analyze sales data and create new strategies to improve business efficiency.
Supply chain manager
A supply chain manager oversees the movement and distribution of materials and goods from suppliers, manufacturers, customers, and other parties. This job requires a wide variety of skills. A bachelor's is often required. Employers also prefer applicants with a master's degree in business administration. You can apply for the job of supply chain manager in many ways. Learn more about this field. A business administration associate's degree is a good starting point if you want to work in supply chain management.
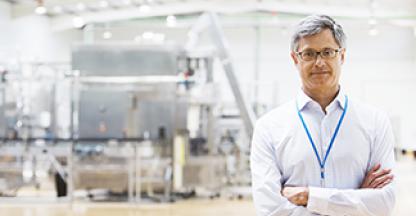
Freight agent
As you create your job description, be sure to include information about your cargo and freight agent responsibilities. So that potential candidates can see what they have to do every day, the job description should include a list of key responsibilities. Make sure to use strong action verbs in your description to get the attention of qualified applicants. You should also provide a detailed list with qualifications that you require to fill the job.
FAQ
What is production plan?
Production Planning involves developing a plan for all aspects of the production, including scheduling, budgeting, casting, crew, location, equipment, props, etc. This document is designed to make sure everything is ready for when you're ready to shoot. You should also have information to ensure the best possible results on set. This information includes locations, crew details and equipment requirements.
The first step is to outline what you want to film. You might have an idea of where you want to film, or you may have specific locations or sets in mind. Once you've identified the locations and scenes you want to use, you can begin to plan what elements you need for each scene. One example is if you are unsure of the exact model you want but decide that you require a car. You could look online for cars to see what options are available, and then narrow down your choices by selecting between different makes or models.
Once you have found the right car, you can start thinking about extras. Do you need people sitting in the front seats? Maybe you need someone to move around in the back. Maybe you'd like to change the interior from black to a white color. These questions will help you determine the exact look and feel of your car. Also, think about what kind of shots you would like to capture. You will be filming close-ups and wide angles. Maybe you want to show the engine and the steering wheel. All of these things will help you identify the exact style of car you want to film.
Once you've determined the above, it is time to start creating a calendar. A schedule will tell you when you need to start shooting and when you need to finish. A schedule for each day will detail when you should arrive at the location and when you need leave. So everyone is clear about what they need to do. It is possible to make arrangements in advance for additional staff if you are looking to hire. You should not hire anyone who doesn't show up because of your inaction.
It is important to calculate the amount of filming days when you are creating your schedule. Some projects can be completed in a matter of days or weeks. Others may take several days. You should consider whether you will need more than one shot per week when creating your schedule. Multiple shots at the same location can increase costs and make it more difficult to complete. It is better to be cautious and take fewer shots than you risk losing money if you are not sure if multiple takes are necessary.
Another important aspect of production planning is setting budgets. It is important to set a realistic budget so you can work within your budget. It is possible to reduce the budget at any time if you experience unexpected problems. But, don't underestimate how much money you'll spend. You'll end up with less money after paying for other things if the cost is underestimated.
Planning production is a tedious process. Once you have a good understanding of how everything works together, planning future projects becomes easy.
Why is logistics important in manufacturing
Logistics are an integral part any business. They enable you to achieve outstanding results by helping manage product flow from raw materials through to finished goods.
Logistics are also important in reducing costs and improving efficiency.
What are the requirements to start a logistics business?
A successful logistics business requires a lot more than just knowledge. You must have good communication skills to interact effectively with your clients and suppliers. You need to understand how to analyze data and draw conclusions from it. You must be able manage stress and pressure under pressure. To improve efficiency, you must be innovative and creative. Strong leadership qualities are essential to motivate your team and help them achieve their organizational goals.
It is also important to be efficient and well organized in order meet deadlines.
What is the role of a logistics manager
A logistics manager ensures that all goods are delivered on time and without damage. This is done through his/her expertise and knowledge about the company's product range. He/she must also ensure sufficient stock to meet the demand.
What skills do production planners need?
You must be flexible and organized to become a productive production planner. You must also be able to communicate effectively with clients and colleagues.
What types of jobs can you find in logistics
There are many jobs available in logistics. Some examples are:
-
Warehouse workers: They load and unload trucks, pallets, and other cargo.
-
Transportation drivers - They drive trucks and trailers to deliver goods and carry out pick-ups.
-
Freight handlers – They sort and package freight at warehouses.
-
Inventory managers: They are responsible for the inventory and management of warehouses.
-
Sales representatives - They sell products.
-
Logistics coordinators – They plan and coordinate logistics operations.
-
Purchasing agents - They purchase goods and services needed for company operations.
-
Customer service representatives – They answer emails and phone calls from customers.
-
Ship clerks - They issue bills and process shipping orders.
-
Order fillers - They fill orders based on what is ordered and shipped.
-
Quality control inspectors – They inspect incoming and outgoing products to ensure that there are no defects.
-
Others - There is a variety of other jobs in logistics. These include transportation supervisors and cargo specialists.
What are the responsibilities of a manufacturing manager
A manufacturing manager has to ensure that all manufacturing processes work efficiently and effectively. They should also be aware and responsive to any company problems.
They should also be able communicate with other departments, such as sales or marketing.
They should also be aware of the latest trends in their industry and be able to use this information to help improve productivity and efficiency.
Statistics
- According to a Statista study, U.S. businesses spent $1.63 trillion on logistics in 2019, moving goods from origin to end user through various supply chain network segments. (netsuite.com)
- According to the United Nations Industrial Development Organization (UNIDO), China is the top manufacturer worldwide by 2019 output, producing 28.7% of the total global manufacturing output, followed by the United States, Japan, Germany, and India.[52][53] (en.wikipedia.org)
- It's estimated that 10.8% of the U.S. GDP in 2020 was contributed to manufacturing. (investopedia.com)
- In 2021, an estimated 12.1 million Americans work in the manufacturing sector.6 (investopedia.com)
- In the United States, for example, manufacturing makes up 15% of the economic output. (twi-global.com)
External Links
How To
How to Use the 5S to Increase Productivity In Manufacturing
5S stands in for "Sort", the "Set In Order", "Standardize", or "Separate". Toyota Motor Corporation created the 5S methodology in 1954. It allows companies to improve their work environment, thereby achieving greater efficiency.
This approach aims to standardize production procedures, making them predictable, repeatable, and easily measurable. It means tasks like cleaning, sorting or packing, labeling, and storing are done every day. Workers can be more productive by knowing what to expect.
There are five steps that you need to follow in order to implement 5S. Each step requires a different action, which increases efficiency. You can make it easy for people to find things later by sorting them. When you arrange items, you place them together. Then, after you separate your inventory into groups, you store those groups in containers that are easy to access. Finally, when you label your containers, you ensure everything is labeled correctly.
This requires employees to critically evaluate how they work. Employees should understand why they do the tasks they do, and then decide if there are better ways to accomplish them. They must learn new skills and techniques in order to implement the 5S system.
The 5S method increases efficiency and morale among employees. They will feel motivated to strive for higher levels of efficiency once they start to see results.