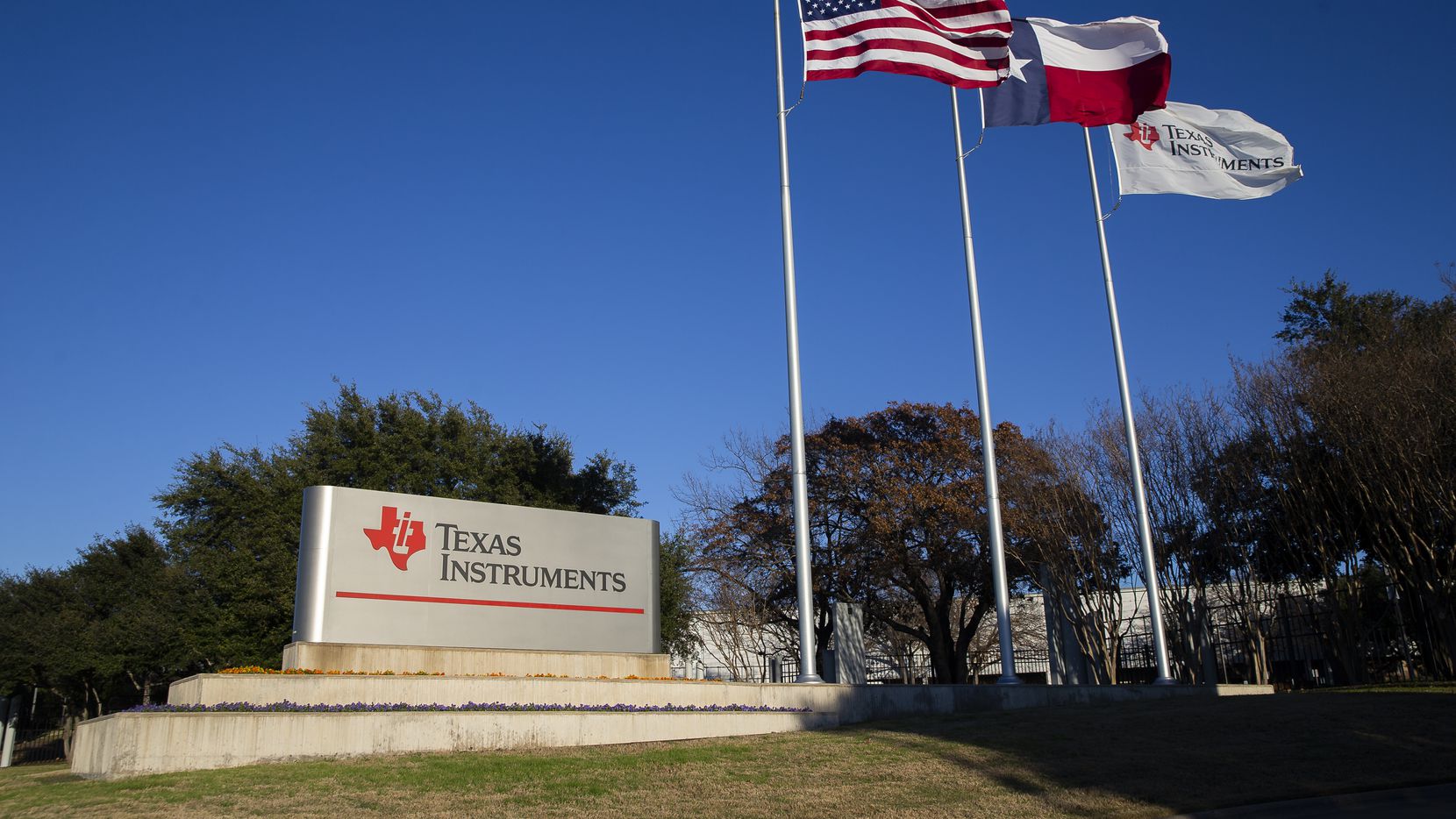
Heijunka, originally created by Toyota in Japan, is a lean production process that improves efficiency in multistep production processes. It reduces the amount of waste in the production process by ensuring that the production schedule is consistent with customer demand. It eliminates abrupt fluctuations in production, which also reduces waste. Heijunka allows manufacturers to respond to customer needs and maximize their profits.
Heijunka can be described as a method of coordinating small production batches across different manufacturing lines. It helps improve efficiency in multistep production processes, particularly when justintime principles are used. It is also part in the Toyota Production System. It reduces waste in production by leveling production through average volume, mixing products, as well as minimizing batch sizes.
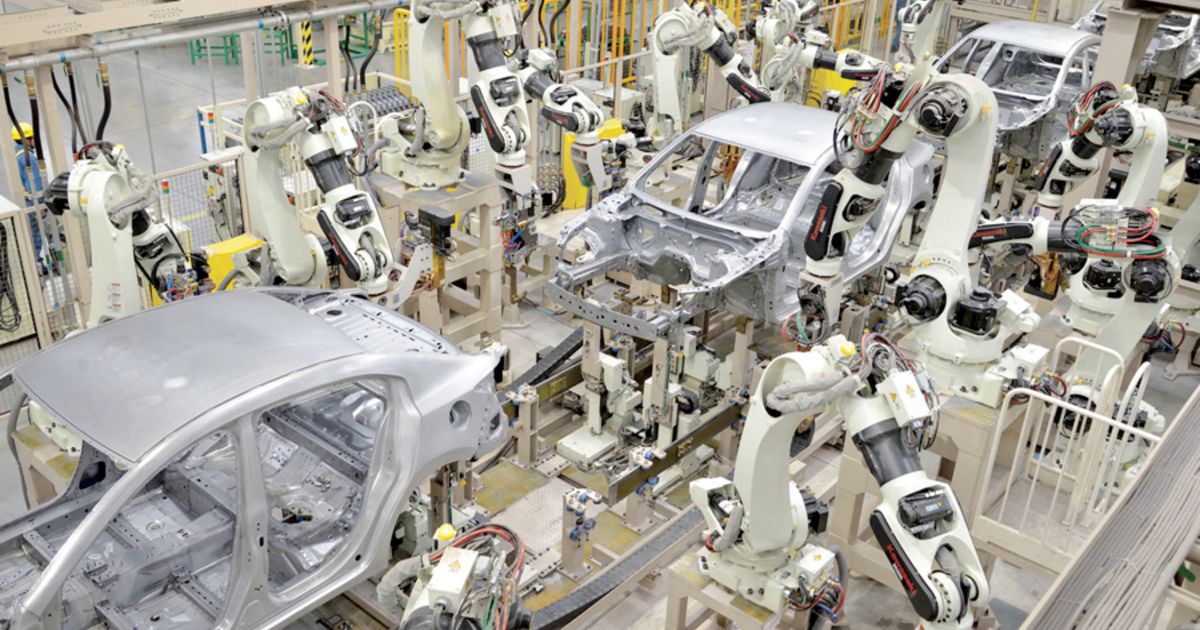
There are two ways you can implement Heijunka. The first is to use a heijunkabox, which is a grid made up of small boxes that can be fixed or mounted on a wall. It is a visual management tool that allows production personnel to schedule and visualize the production process. Magnetic cards are another method for implementing heijunka.
Toyota dealers use Heijunka to reduce changeover times. It is also part of Toyota's Lean manufacturing framework. Heijunka not only allows manufacturers to produce at the required speed but also reduces inventory and improves production. Heijunka helps to make better use of both labor and equipment. It promotes a lean production process that reduces waste and makes better products for customers.
The takt rate, also called the customer buying price, is essential in order to use heijunka. This is the amount of time it takes to complete a product to meet customer demand. Heijunka uses the time to decide the production pace. You can calculate how many products you want to make and at what rate customers will buy your products using the takttime. Back-office settings can also use the Takt Time to determine the rate at which customers purchase company products.
Production staff can visually plan and schedule their production using the heijunka boxes. You can also use the heijunka to help you visualize the production flow. Each product or component is represented by a row and column in the heijunka. Each product type is represented by the columns of boxes.
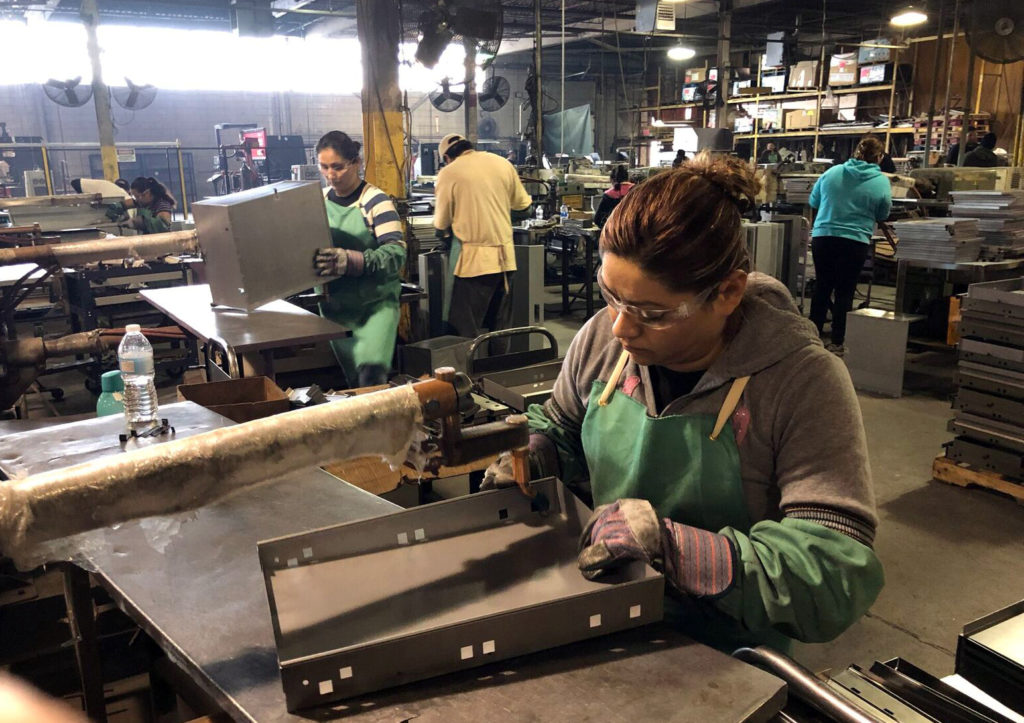
Heijunka Box (or Heijunka Box) is one of most commonly used visual management tools in manufacturing. This tool displays the relationships between component and product production. This tool provides visual representations of the production workload for each week. It is used in conjunction with kanban cards, which are colored cards that represent the amount of product required for a specific production step. Kanban card are usually removed from the heijunka box within a given time frame and delivered to the designated production area.
FAQ
What does it mean to be a manufacturer?
Manufacturing Industries refers to businesses that manufacture products. Consumers are people who purchase these goods. These companies employ many processes to achieve this purpose, such as production and distribution, retailing, management and so on. These companies produce goods using raw materials and other equipment. This includes all types and varieties of manufactured goods, such as food items, clothings, building supplies, furnitures, toys, electronics tools, machinery vehicles, pharmaceuticals medical devices, chemicals, among others.
What are the logistics products?
Logistics refers to the movement of goods from one place to another.
They encompass all aspects transport, including packaging and loading, transporting, storage, unloading.
Logisticians ensure that products reach the right destination at the right moment and under safe conditions. Logisticians assist companies in managing their supply chains by providing information such as demand forecasts, stock levels and production schedules.
They also keep track of shipments in transit, monitor quality standards, perform inventories and order replenishment, coordinate with suppliers and vendors, and provide support services for sales and marketing.
What is the difference between Production Planning, Scheduling and Production Planning?
Production Planning (PP), is the process of deciding what production needs to take place at any given time. Forecasting and identifying production capacity are two key elements to this process.
Scheduling involves the assignment of dates and times to tasks in order to complete them within the timeframe.
How can overproduction in manufacturing be reduced?
Improved inventory management is the key to reducing overproduction. This would reduce the amount of time spent on unnecessary activities such as purchasing, storing, and maintaining excess stock. This will allow us to free up resources for more productive tasks.
One way to do this is to adopt a Kanban system. A Kanban board can be used to monitor work progress. Kanban systems allow work items to move through different states until they reach their final destination. Each state represents a different priority.
When work is completed, it can be transferred to the next stage. However, if a task is still at the beginning stages, it will remain so until it reaches the end of the process.
This keeps work moving and ensures no work is lost. Managers can see how much work has been done and the status of each task at any time with a Kanban Board. This information allows them to adjust their workflow based on real-time data.
Lean manufacturing, another method to control inventory levels, is also an option. Lean manufacturing focuses on eliminating waste throughout the entire production chain. Anything that does not contribute to the product's value is considered waste. There are several types of waste that you might encounter:
-
Overproduction
-
Inventory
-
Packaging not required
-
Excess materials
By implementing these ideas, manufacturers can improve efficiency and cut costs.
What is the difference between a production planner and a project manager?
A production planner is more involved in the planning phase of the project than a project manger.
What does it mean to warehouse?
Warehouses and storage facilities are where goods are kept before being sold. It can be indoors or out. In some cases it could be both indoors and outdoors.
What are my options for learning more about manufacturing
You can learn the most about manufacturing by getting involved in it. But if that is not possible you can always read books and watch educational videos.
Statistics
- In 2021, an estimated 12.1 million Americans work in the manufacturing sector.6 (investopedia.com)
- Job #1 is delivering the ordered product according to specifications: color, size, brand, and quantity. (netsuite.com)
- It's estimated that 10.8% of the U.S. GDP in 2020 was contributed to manufacturing. (investopedia.com)
- You can multiply the result by 100 to get the total percent of monthly overhead. (investopedia.com)
- (2:04) MTO is a production technique wherein products are customized according to customer specifications, and production only starts after an order is received. (oracle.com)
External Links
How To
Six Sigma in Manufacturing:
Six Sigma can be described as "the use of statistical process control (SPC), techniques to achieve continuous improvement." Motorola's Quality Improvement Department developed it at their Tokyo plant in Japan in 1986. Six Sigma's core idea is to improve the quality of processes by standardizing and eliminating defects. In recent years, many companies have adopted this method because they believe there is no such thing as perfect products or services. The main goal of Six Sigma is to reduce variation from the mean value of production. This means that if you take a sample of your product, then measure its performance against the average, you can find out what percentage of the time the process deviates from the norm. If this deviation is too big, you know something needs fixing.
Understanding the nature of variability in your business is the first step to Six Sigma. Once you've understood that, you'll want to identify sources of variation. These variations can also be classified as random or systematic. Random variations are caused when people make mistakes. While systematic variations are caused outside of the process, they can occur. If you make widgets and some of them end up on the assembly line, then those are considered random variations. However, if you notice that every time you assemble a widget, it always falls apart at exactly the same place, then that would be a systematic problem.
Once you've identified the problem areas you need to find solutions. That solution might involve changing the way you do things or redesigning the process altogether. Once you have implemented the changes, it is important to test them again to ensure they work. If they don’t work, you’ll need to go back and rework the plan.