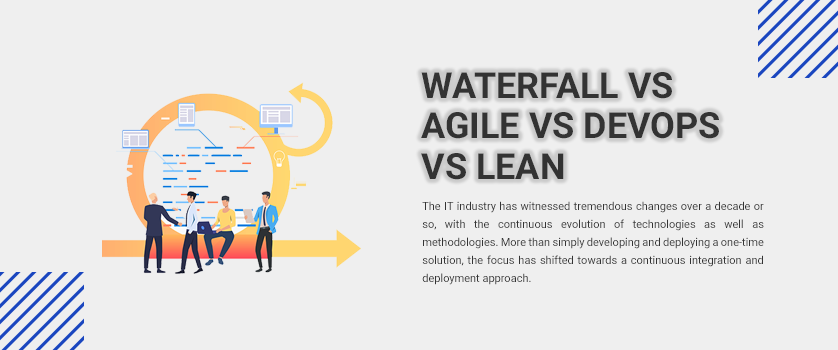
CEVA Logistics is a company that provides logistics services. These logistics companies offer several benefits to their employees. Here are some ways you can apply for a position in logistics at one of these companies. You can start by searching for jobs based on location.
Job description
CEVA Logistics has a variety of jobs for people with a variety of education and work experience. The company's core values are dedication to customer service and on-time delivery. The company also seeks individuals who are passionate about logistics and who are willing to work hard. The company will consider candidates who are enthusiastic about logistics and possess a positive attitude when they apply for a job.
CEVA Logistics needs a Process/Industrial Manager to develop new processes and improve efficiency. The ideal candidate must be self-motivated, energetic, and able work well with others. Their duties include designing and implementing process layouts, managing projects, and using analytical and modeling skills. To improve quality and efficiency, they must be proficient in robotics and other manufacturing processes.
Education is necessary
CEVA Logistics offers many opportunities for candidates interested in a career with the company, including sales rep and warehouse manager. You may also have the opportunity to become an operations supervisor, which oversees the day to day operations of the company. Many of these positions have a team under them. This position requires a bachelor's in logistics and supervisory experience.
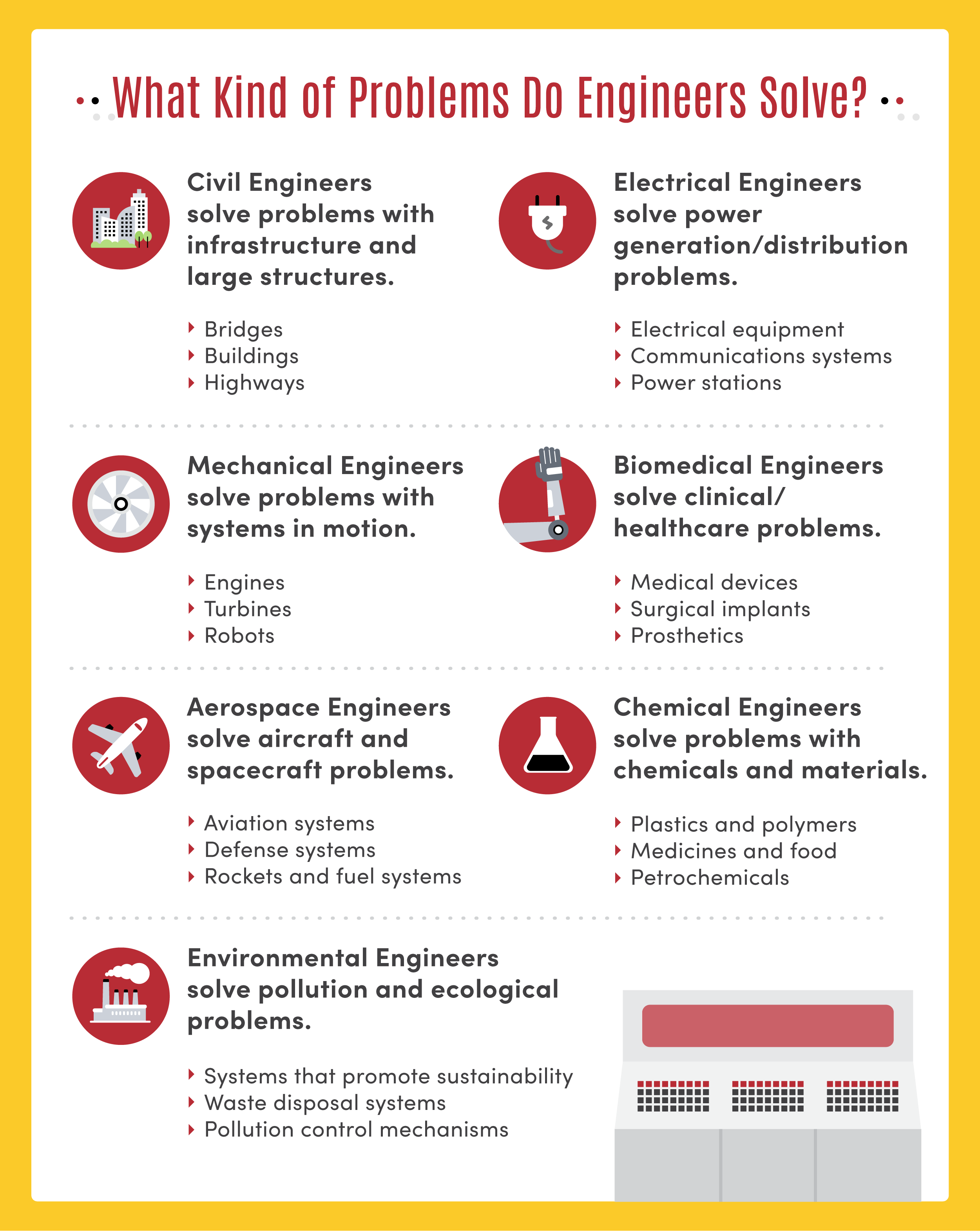
You can apply online, or through recruiters, if you are interested. Online applications require candidates to first create a career profile in the company's portal. Their LinkedIn accounts can be used to connect to their profile, upload their resumes and enter relevant information. After their profile is completed, they can select the region or country that interests them and contact a recruiter.
Salary range
The first step in applying for a CEVA Logistics job is to create an online profile through the company's Career Portal. This allows to link with your LinkedIn profile, upload your resume, and allow you to create a job application. You can also manually input information about skills, experience, and any other pertinent information. Next, choose a country or region where you are interested in working. After this step, you will be provided with contact information by a recruiter from that region.
CEVA Logistics salaries vary depending on job title and experience. An Air Break Bulk Specialist makes $24,000 per year while the Vice President of CEVA Logistics earns $166,000 annually. There are differences in the compensation packages depending on where you live.
Localities
CEVA Logistics is a great place to start a career in logistics. The company has many job openings at various locations. They have different responsibilities, and different experience requirements. To apply for a job, simply type in the job title in the search box and your location. Search for Edison, NJ jobs to see available positions. You will need experience driving and be able and able to communicate with both internal and external customers.
CEVA Logistics offers many career opportunities, including supervisory positions. Supervisors oversee the day-to-day operations of the company. They coordinate the schedules and manage inventory. Operations supervisors are typically responsible for managing a team, coordinating schedules and overseeing employees. Leadership and management skills are essential.
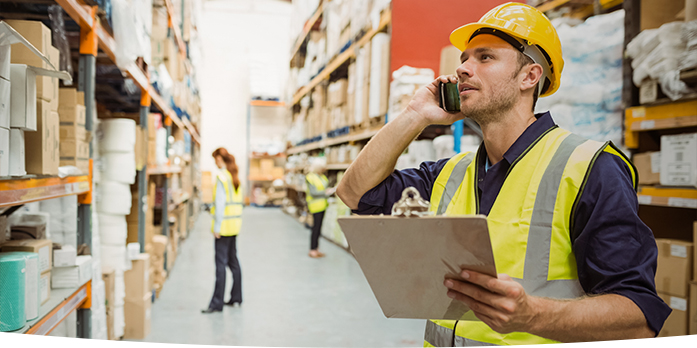
Applying online
CEVA Logistics has a position for you if you are looking for a job within the logistics industry. Ceva Logistics, an international logistics company, was established in 2006 as a result the merger of two Australian and Texan contracts logistics companies. The company's operations today span more than 950 locations across 170 countries. You can apply for part-time and full-time jobs.
While most jobs at CEVA require some prior experience, many positions can be filled as entry-level. Other positions may require little to no experience. You can find entry-level positions such as customer service representative, administrative clerk, or dispatcher.
FAQ
Why automate your factory?
Modern warehouses are increasingly dependent on automation. E-commerce has increased the demand for quicker delivery times and more efficient processes.
Warehouses need to adapt quickly to meet changing needs. To do so, they must invest heavily in technology. Automating warehouses has many benefits. These are some of the benefits that automation can bring to warehouses:
-
Increases throughput/productivity
-
Reduces errors
-
Improves accuracy
-
Safety is boosted
-
Eliminates bottlenecks
-
Allows companies scale more easily
-
Makes workers more efficient
-
It gives visibility to everything that happens inside the warehouse
-
Enhances customer experience
-
Improves employee satisfaction
-
Reduces downtime and improves uptime
-
This ensures that quality products are delivered promptly
-
Human error can be eliminated
-
It ensures compliance with regulations
What are the 7 Rs of logistics management?
The acronym 7Rs of Logistics refers to the seven core principles of logistics management. It was created by the International Association of Business Logisticians and published in 2004 under its "Seven Principles of Logistics Management".
The following letters form the acronym:
-
Responsible – ensure that all actions are legal and don't cause harm to anyone else.
-
Reliable - You can have confidence that you will fulfill your promises.
-
Be responsible - Use resources efficiently and avoid wasting them.
-
Realistic – consider all aspects of operations, from cost-effectiveness to environmental impact.
-
Respectful - Treat people fairly and equitably
-
Resourceful - look for opportunities to save money and increase productivity.
-
Recognizable provides value-added products and services to customers
What is the importance of logistics in manufacturing?
Logistics are an essential component of any business. They help you achieve great results by helping you manage all aspects of product flow, from raw materials to finished goods.
Logistics play a key role in reducing expenses and increasing efficiency.
How does a production planner differ from a project manager?
The primary difference between a producer planner and a manager of a project is that the manager usually plans and organizes the whole project, while a production planner is only involved in the planning stage.
Statistics
- (2:04) MTO is a production technique wherein products are customized according to customer specifications, and production only starts after an order is received. (oracle.com)
- [54][55] These are the top 50 countries by the total value of manufacturing output in US dollars for its noted year according to World Bank.[56] (en.wikipedia.org)
- According to the United Nations Industrial Development Organization (UNIDO), China is the top manufacturer worldwide by 2019 output, producing 28.7% of the total global manufacturing output, followed by the United States, Japan, Germany, and India.[52][53] (en.wikipedia.org)
- According to a Statista study, U.S. businesses spent $1.63 trillion on logistics in 2019, moving goods from origin to end user through various supply chain network segments. (netsuite.com)
- In 2021, an estimated 12.1 million Americans work in the manufacturing sector.6 (investopedia.com)
External Links
How To
How to Use Lean Manufacturing for the Production of Goods
Lean manufacturing (or lean manufacturing) is a style of management that aims to increase efficiency, reduce waste and improve performance through continuous improvement. It was developed in Japan during the 1970s and 1980s by Taiichi Ohno, who received the Toyota Production System (TPS) award from TPS founder Kanji Toyoda. Michael L. Watkins published the book "The Machine That Changed the World", which was the first to be published about lean manufacturing.
Lean manufacturing refers to a set of principles that improve the quality, speed and costs of products and services. It is about eliminating defects and waste from all stages of the value stream. The five-steps of Lean Manufacturing are just-in time (JIT), zero defect and total productive maintenance (TPM), as well as 5S. Lean manufacturing is about eliminating activities that do not add value, such as inspection, rework, and waiting.
Lean manufacturing is a way for companies to achieve their goals faster, improve product quality, and lower costs. Lean manufacturing can be used to manage all aspects of the value chain. Customers, suppliers, distributors, retailers and employees are all included. Lean manufacturing is widely used in many industries. Toyota's philosophy has been a key driver of success in many industries, including automobiles and electronics.
Five principles are the basis of lean manufacturing:
-
Define value - Find out what your business contributes to society, and what makes it different from other competitors.
-
Reduce Waste – Eliminate all activities that don't add value throughout the supply chain.
-
Create Flow: Ensure that the work process flows without interruptions.
-
Standardize and Simplify – Make processes as consistent, repeatable, and as simple as possible.
-
Build relationships - Develop and maintain personal relationships with both your internal and external stakeholders.
Lean manufacturing is not a new concept, but it has been gaining popularity over the last few years due to a renewed interest in the economy following the global financial crisis of 2008. Many businesses have adopted lean production techniques to make them more competitive. Economists think that lean manufacturing is a crucial factor in economic recovery.
Lean manufacturing is now becoming a common practice in the automotive industry, with many benefits. These include higher customer satisfaction levels, reduced inventory levels as well as lower operating costs.
It can be applied to any aspect of an organisation. However, it is particularly useful when applied to the production side of an organization because it ensures that all steps in the value chain are efficient and effective.
There are three types principally of lean manufacturing:
-
Just-in-Time Manufacturing (JIT): This type of lean manufacturing is commonly referred to as "pull systems." JIT refers to a system in which components are assembled at the point of use instead of being produced ahead of time. This approach is designed to reduce lead times and increase the availability of components. It also reduces inventory.
-
Zero Defects Manufacturing (ZDM): ZDM focuses on ensuring that no defective units leave the manufacturing facility. If a part needs to be fixed during the assembly line, it should be repaired rather than scrapped. This is true even for finished products that only require minor repairs prior to shipping.
-
Continuous Improvement (CI), also known as Continuous Improvement, aims at improving the efficiency of operations through continuous identification and improvement to minimize or eliminate waste. Continuous improvement involves continuous improvement of processes and people as well as tools.