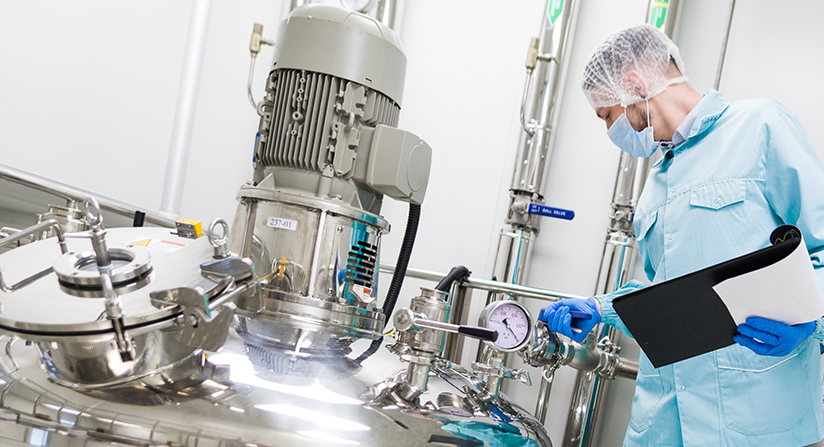
The technology industry is one of the most important industries in the US. This industry includes companies like Microsoft, Apple, and Intel, and they are responsible for making the internet and cell phones work. The technology sector is diverse and vast. Around 40 companies are estimated to be involved. The biggest player in this space is Apple, with its gargantuan juggernaut. Other technology companies can also be found in the industry.
Other major industries in the United States include aerospace, automobiles, and retail trade. Each of these industries is a pillar of the economy, and the list of industries in the US is growing by the day. Another industry worth mentioning is the financial services and healthcare sector. These industries are growing faster then most other parts of the economy.
The fictitious gadget called the "ol' Flintstone" is its name. It is small, but does a great job of providing wireless connectivity. Consumers were able to get the device for free in 2007. The best thing about the gadget is that it is small enough to be carried around in a pocket or purse, and it can even be used to recharge phones and tablets. The device is available in all 50 states, and you can also get it shipped to your house or office. It's a huge hit with consumers and is one of the most important industries in the US.
Other notable industries include the healthcare industry, which has pharmaceuticals as its biggest competitor. Healthcare is a complicated industry with many different types and levels of healthcare organizations. The industry has seen a rise in popularity since the swine flu pandemic. The federal government's complexity is also evident in this industry. The government's Occupational Employment Statistics (GES) program provides detailed statistics regarding the industry, including estimates about average wages and numbers of jobs. The list of industries in the US is growing by leaps and bounds, and there are many other industries to be discovered. You can find all relevant online resources that will help you learn more about the US economy and which industries are best to pick.
FAQ
What is production planning?
Production Planning involves developing a plan for all aspects of the production, including scheduling, budgeting, casting, crew, location, equipment, props, etc. This document aims to ensure that everything is planned and ready when you are ready to shoot. You should also have information to ensure the best possible results on set. This information includes locations, crew details and equipment requirements.
The first step is to decide what you want. You may have already chosen the location you want, or there are locations or sets you prefer. Once you've identified the locations and scenes you want to use, you can begin to plan what elements you need for each scene. Perhaps you have decided that you need to buy a car but aren't sure which model. You could look online for cars to see what options are available, and then narrow down your choices by selecting between different makes or models.
Once you have found the right vehicle, you can think about adding accessories. You might need to have people in the front seats. Maybe you need someone to move around in the back. You might want to change your interior color from black and white. These questions will help to determine the style and feel of your car. Also, think about what kind of shots you would like to capture. You will be filming close-ups and wide angles. Maybe the engine or steering wheel is what you are looking to film. These details will help identify the exact car you wish to film.
Once you have established all the details, you can create a schedule. A schedule will tell you when you need to start shooting and when you need to finish. You will need to know when you have to be there, what time you have to leave and when your return home. Everyone knows exactly what they should do and when. Hire extra staff by booking them ahead of time. It is not worth hiring someone who won’t show up because you didn’t tell him.
It is important to calculate the amount of filming days when you are creating your schedule. Some projects may only take a couple of days, while others could last for weeks. When you are creating your schedule, you should always keep in mind whether you need more than one shot per day or not. Multiple takes at the same place will result in higher costs and longer completion times. If you are unsure if you need multiple takes, it is better to err on the side of caution and shoot fewer takes rather than risk wasting money.
Budgeting is another crucial aspect of production plan. As it will allow you and your team to work within your financial means, setting a realistic budget is crucial. You can always lower the budget if you encounter unexpected problems. However, you shouldn't overestimate the amount of money you will spend. You will end up spending less money if you underestimate the cost of something.
Production planning is a detailed process. But, once you understand the workings of everything, it becomes easier for future projects to be planned.
What are the four types of manufacturing?
Manufacturing refers the process of turning raw materials into useful products with machines and processes. It includes many different activities like designing, building and testing, packaging, shipping and selling, as well as servicing.
What are the responsibilities of a logistic manager?
A logistics manager makes sure that all goods are delivered on-time and in good condition. This is accomplished by using the experience and knowledge gained from working with company products. He/she should ensure that sufficient stock is available in order to meet customer demand.
What does it take for a logistics enterprise to succeed?
To be a successful businessman in logistics, you will need many skills and knowledge. To communicate effectively with clients and suppliers, you must be able to communicate well. You must be able analyze data and draw out conclusions. You must be able manage stress and pressure under pressure. In order to innovate and create new ways to improve efficiency, creativity is essential. Strong leadership qualities are essential to motivate your team and help them achieve their organizational goals.
It is important to be organized and efficient in order to meet tight deadlines.
What are the products and services of logistics?
Logistics refers to the movement of goods from one place to another.
These include all aspects related to transport such as packaging, loading and transporting, storing, transporting, unloading and warehousing inventory management, customer service. Distribution, returns, recycling are some of the options.
Logisticians ensure that products reach the right destination at the right moment and under safe conditions. They assist companies with their supply chain efficiency through information on demand forecasts. Stock levels, production times, and availability.
They coordinate with vendors and suppliers, keep track of shipments, monitor quality standards and perform inventory and order replenishment.
Statistics
- Job #1 is delivering the ordered product according to specifications: color, size, brand, and quantity. (netsuite.com)
- It's estimated that 10.8% of the U.S. GDP in 2020 was contributed to manufacturing. (investopedia.com)
- (2:04) MTO is a production technique wherein products are customized according to customer specifications, and production only starts after an order is received. (oracle.com)
- According to the United Nations Industrial Development Organization (UNIDO), China is the top manufacturer worldwide by 2019 output, producing 28.7% of the total global manufacturing output, followed by the United States, Japan, Germany, and India.[52][53] (en.wikipedia.org)
- According to a Statista study, U.S. businesses spent $1.63 trillion on logistics in 2019, moving goods from origin to end user through various supply chain network segments. (netsuite.com)
External Links
How To
How to use the Just In-Time Production Method
Just-in-time (JIT) is a method that is used to reduce costs and maximize efficiency in business processes. It is a process where you get the right amount of resources at the right moment when they are needed. This means that your only pay for the resources you actually use. The term was first coined by Frederick Taylor, who developed his theory while working as a foreman in the early 1900s. He saw how overtime was paid to workers for work that was delayed. He decided that workers would be more productive if they had enough time to complete their work before they started to work.
The idea behind JIT is that you should plan ahead and have everything ready so you don't waste money. You should also look at the entire project from start to finish and make sure that you have sufficient resources available to deal with any problems that arise during the course of your project. You'll be prepared to handle any potential problems if you know in advance. You won't have to pay more for unnecessary items.
There are many JIT methods.
-
Demand-driven: This is a type of JIT where you order the parts/materials needed for your project regularly. This will allow for you to track the material that you have left after using it. You'll also be able to estimate how long it will take to produce more.
-
Inventory-based: This type allows you to stock the materials needed for your projects ahead of time. This allows for you to anticipate how much you can sell.
-
Project-driven: This means that you have enough money to pay for your project. When you know how much you need, you'll purchase the appropriate amount of materials.
-
Resource-based JIT : This is probably the most popular type of JIT. Here, you allocate certain resources based on demand. For example, if there is a lot of work coming in, you will have more people assigned to them. If you don't receive many orders, then you'll assign fewer employees to handle the load.
-
Cost-based: This is the same as resource-based except that you don't care how many people there are but how much each one of them costs.
-
Price-based: This is a variant of cost-based. However, instead of focusing on the individual workers' costs, this looks at the total price of the company.
-
Material-based - This is a variant of cost-based. But instead of looking at the total company cost, you focus on how much raw material you spend per year.
-
Time-based JIT: This is another variant of resource-based JIT. Instead of focusing on how much each employee costs, you focus on how long it takes to complete the project.
-
Quality-based JIT: Another variation on resource-based JIT. Instead of thinking about how much each employee costs or how long it takes to manufacture something, you think about how good the quality of your product is.
-
Value-based: This is one of the newest forms of JIT. You don't worry about whether the products work or if they meet customer expectations. Instead, you are focused on adding value to the marketplace.
-
Stock-based: This stock-based method focuses on the actual quantity of products being made at any given time. It's used when you want to maximize production while minimizing inventory.
-
Just-in time (JIT), planning: This is a combination JIT/supply chain management. It refers to the process of scheduling the delivery of components as soon as they are ordered. It reduces lead times and improves throughput.