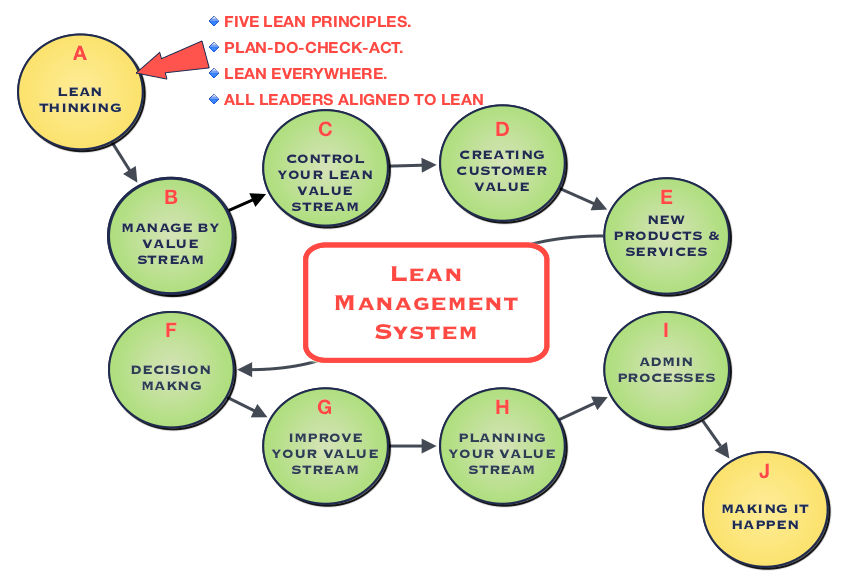
The bill of material (BOM) is an important part in the manufacturing process. It contains all necessary items for manufacturing end products. It is an essential document for businesses, regardless of whether they sell through retailers or directly to customers. It allows companies to track their stock, reduce waste and avoid production errors. It is also useful for companies to avoid stockouts.
A bill or materials is a detailed, tabular document that lists each component of an assembly. The document also lists the parts that will be used to construct the assembly. The parts and subassemblies may be purchased from outside sources or manufactured internally. It is necessary to identify each part with a unique serial number. This will allow the assembly team to identify the parts and gather them. Note any special requirements that may be required on the bill. These special requirements could result in delays or even mistakes during the manufacturing process.
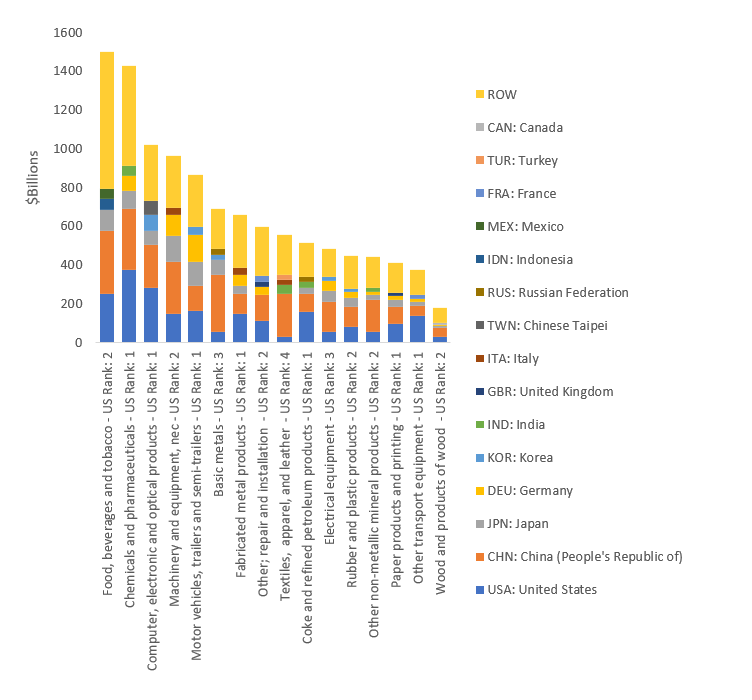
Companies find bills of materials important because they allow them to track raw materials and components. They can also be used to increase production. They are useful in preventing stockouts, and they allow companies to forecast sales. These documents also help companies to track the materials used for production and avoid over-ordering of materials.
A bill of materials is a list that details the materials, subassemblies, and components required to make a product. The bill also includes the labor and time needed to complete each stage. Importantly, the bill of material must also include the name and contact information for the suppliers for each component. Other details may be included if they are necessary for the production process. It is important you remember that the bill may differ from one company for another.
In manufacturing processes, bills of material are used to ensure that the product functions correctly. They also help companies to plan and order materials, avoid waste, and reduce production errors. A bill of materials is used by manufacturers to identify raw materials and to calculate the amounts required for each product. Important to remember that the bill of materials is a roadmap for the finished product. It can be challenging to create a bill-of-materials, especially for products with many parts. There are software tools that allow you to create a bill.
To meet the specifications and needs of the project, a bill is made. It can be used to communicate with manufacturing and supply-chain partners, as well as as a blueprint. This document is useful for companies in order to avoid over-ordering materials and keep track of all components used in the production process.
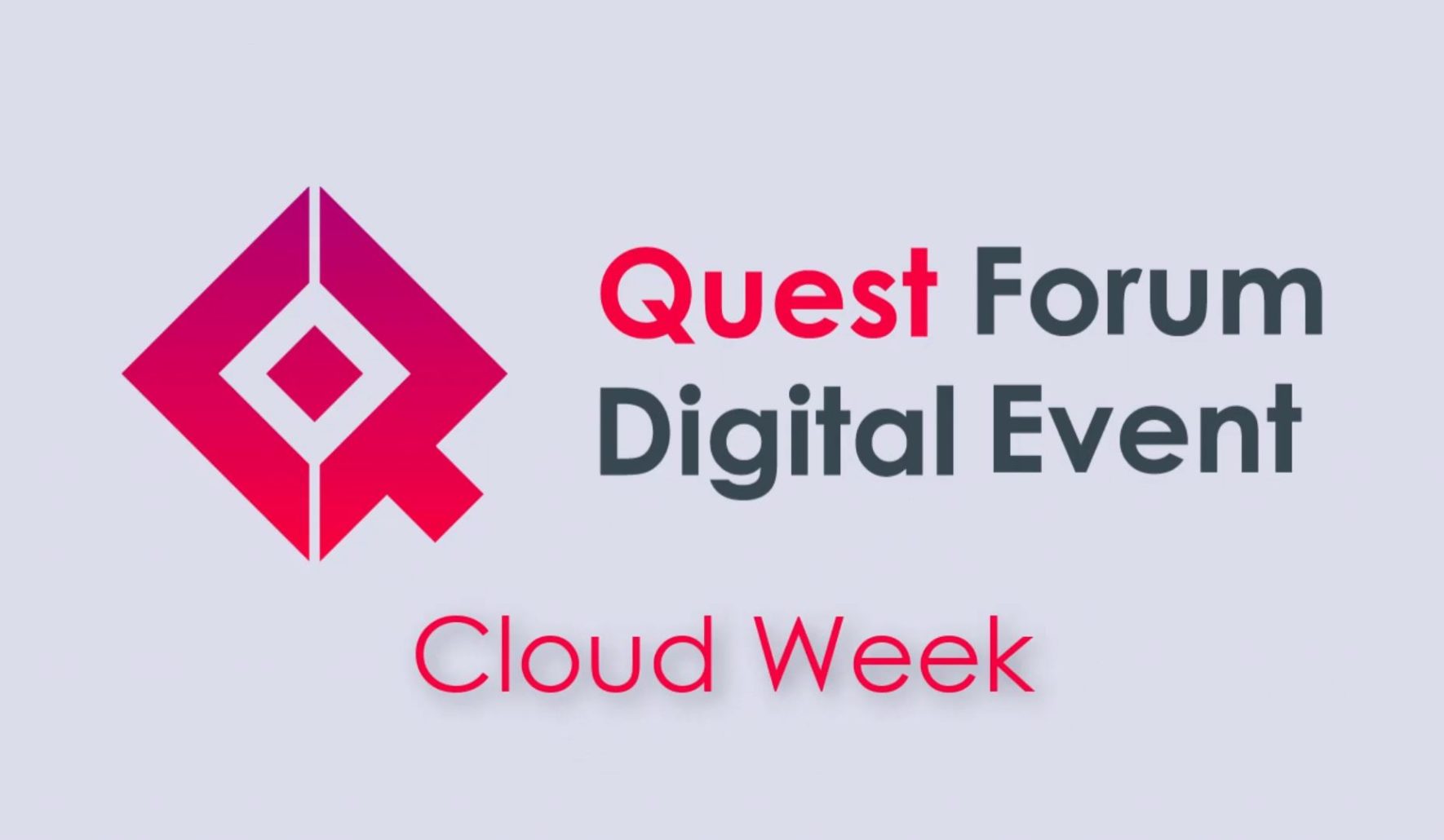
If you sell through retail channels or direct to customers, a bill for materials is essential. Bills of material allow for greater productivity and profits. They can be used to help companies avoid waste, make production mistakes, and reduce stockouts.
FAQ
How can manufacturing prevent production bottlenecks?
Avoiding production bottlenecks is as simple as keeping all processes running smoothly, from the time an order is received until the product ships.
This includes both quality control and capacity planning.
The best way to do this is to use continuous improvement techniques such as Six Sigma.
Six Sigma can be used to improve the quality and decrease waste in all areas of your company.
It's all about eliminating variation and creating consistency in work.
Why automate your warehouse
Modern warehouses are increasingly dependent on automation. Increased demand for efficient and faster delivery has resulted in a rise in e-commerce.
Warehouses need to adapt quickly to meet changing needs. In order to do this, they need to invest in technology. The benefits of automating warehouses are numerous. These are just a few reasons to invest in automation.
-
Increases throughput/productivity
-
Reduces errors
-
Increases accuracy
-
Boosts safety
-
Eliminates bottlenecks
-
Allows companies scale more easily
-
Increases efficiency of workers
-
The warehouse can be viewed from all angles.
-
Enhances customer experience
-
Improves employee satisfaction
-
Reducing downtime and increasing uptime
-
This ensures that quality products are delivered promptly
-
Removes human error
-
It helps ensure compliance with regulations
How can we improve manufacturing efficiency?
The first step is to identify the most important factors affecting production time. The next step is to identify the most important factors that affect production time. If you don’t know where to begin, consider which factors have the largest impact on production times. Once you've identified them, try to find solutions for each of those factors.
Statistics
- Job #1 is delivering the ordered product according to specifications: color, size, brand, and quantity. (netsuite.com)
- According to a Statista study, U.S. businesses spent $1.63 trillion on logistics in 2019, moving goods from origin to end user through various supply chain network segments. (netsuite.com)
- You can multiply the result by 100 to get the total percent of monthly overhead. (investopedia.com)
- According to the United Nations Industrial Development Organization (UNIDO), China is the top manufacturer worldwide by 2019 output, producing 28.7% of the total global manufacturing output, followed by the United States, Japan, Germany, and India.[52][53] (en.wikipedia.org)
- In the United States, for example, manufacturing makes up 15% of the economic output. (twi-global.com)
External Links
How To
How to Use Just-In-Time Production
Just-in-time is a way to cut costs and increase efficiency in business processes. This is where you have the right resources at the right time. This means that you only pay the amount you actually use. Frederick Taylor, a 1900s foreman, first coined the term. He noticed that workers were often paid overtime when they had to work late. He decided that workers would be more productive if they had enough time to complete their work before they started to work.
JIT teaches you to plan ahead and prepare everything so you don’t waste time. It is important to look at your entire project from beginning to end and ensure that you have enough resources to handle any issues that may arise. You will have the resources and people to solve any problems you anticipate. This way you won't be spending more on things that aren’t really needed.
There are different types of JIT methods:
-
Demand-driven JIT: You order the parts and materials you need for your project every other day. This will allow for you to track the material that you have left after using it. This will let you know how long it will be to produce more.
-
Inventory-based: This is a type where you stock the materials required for your projects in advance. This allows one to predict how much they will sell.
-
Project-driven: This method allows you to set aside enough funds for your project. Knowing how much money you have available will help you purchase the correct amount of materials.
-
Resource-based JIT: This type of JIT is most commonly used. This is where you assign resources based upon demand. For example, if there is a lot of work coming in, you will have more people assigned to them. If you don't receive many orders, then you'll assign fewer employees to handle the load.
-
Cost-based: This is a similar approach to resource-based but you are not only concerned with how many people you have, but also how much each one costs.
-
Price-based: This is very similar to cost-based, except that instead of looking at how much each individual worker costs, you look at the overall price of the company.
-
Material-based: This is quite similar to cost-based, but instead of looking at the total cost of the company, you're concerned with how much raw materials you spend on average.
-
Time-based: Another variation of resource-based JIT. Instead of focusing on how much each employee costs, you focus on how long it takes to complete the project.
-
Quality-based JIT - This is another form of resource-based JIT. Instead of focusing on the cost of each worker or how long it takes, think about how high quality your product is.
-
Value-based JIT: This is the latest form of JIT. You don't worry about whether the products work or if they meet customer expectations. Instead, you focus on the added value that you provide to your market.
-
Stock-based: This inventory-based approach focuses on how many items are being produced at any one time. It's useful when you want maximum production and minimal inventory.
-
Just-intime (JIT), planning is a combination JIT management and supply chain management. It refers to the process of scheduling the delivery of components as soon as they are ordered. This is important as it reduces lead time and increases throughput.