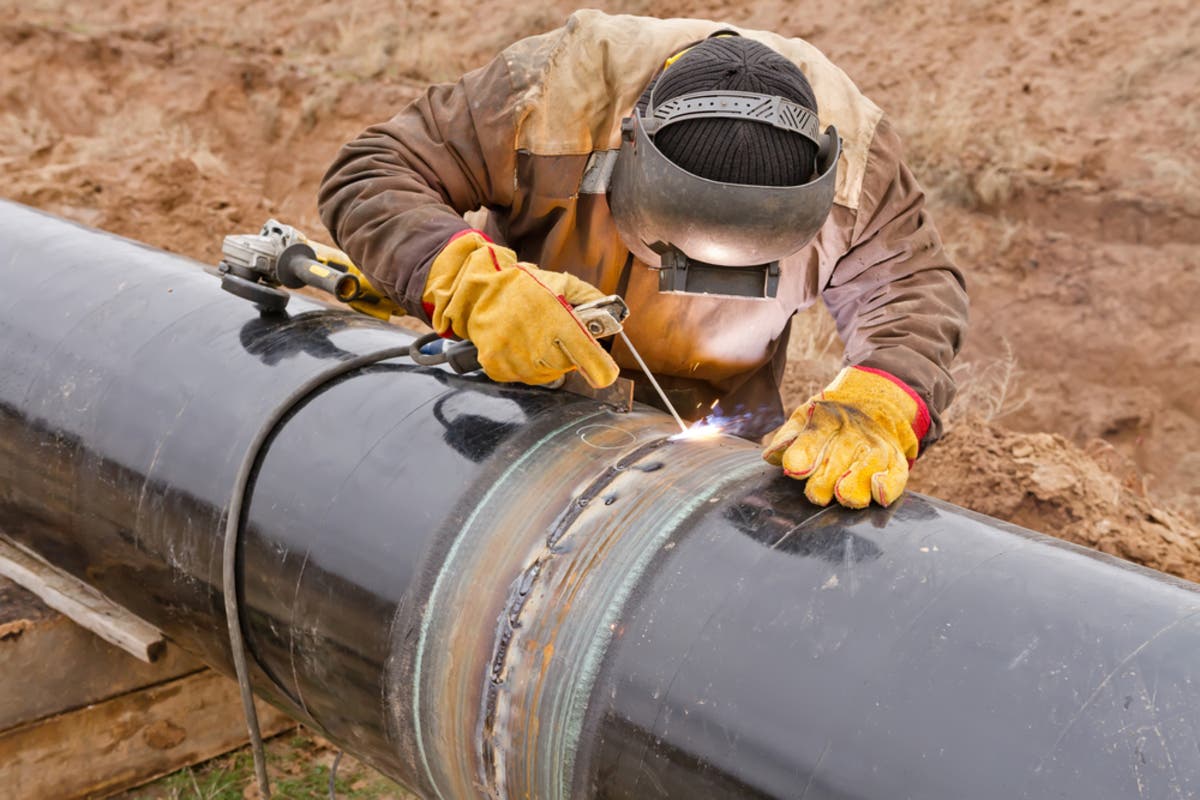
Supply Dynamics was established in Loveland (Ohio) in 2003. It provides technology solutions for manufacturers in highly distributed manufacturing environments. Supply Dynamics collaborates with the Defense Logistics Agency, (DLA), and the Navy. It provides visibility and control of the organization's supply chains from beginning to end. It helps manufacturers plan production and reduce the costs of raw materials. Supply Dynamics works with a variety of industries including aerospace, defense, manufacturing, and transportation.
Dynamics 365 Supply Chain Management (powered by Microsoft Cloud) is a Microsoft Cloud-powered software that enables organizations improve operational efficiency, streamline manufacturing, and build strong supply chain networks. It offers predictive analytics, flexibility, and unmatched visibility into the end-to-end supply chain. Its modules provide complete product lifecycle functionality and ensure that products reach customers on time.
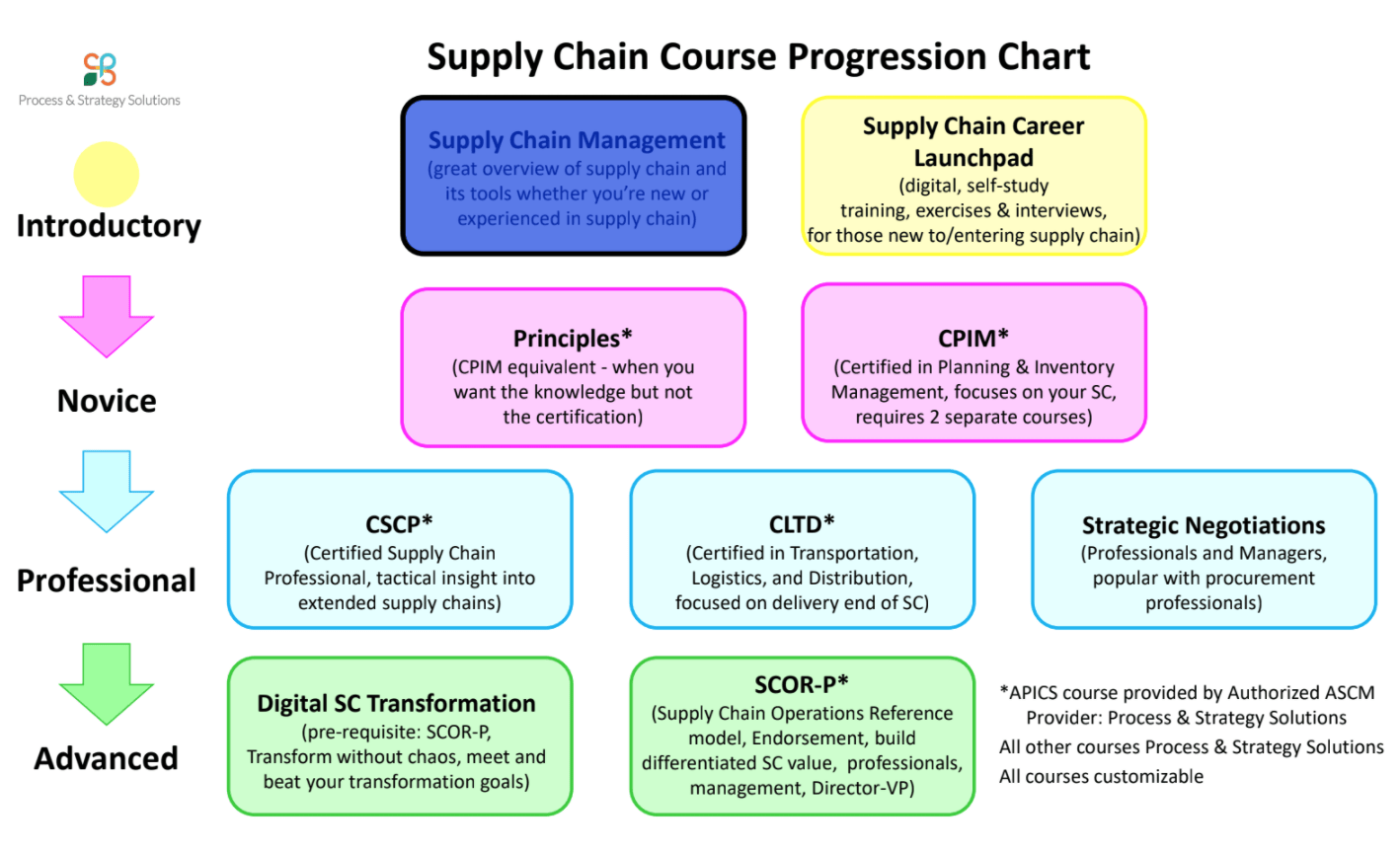
The Dynamics Supply Chain module has features that allow users configure items for discrete or continuous manufacturing, submitRFQs, check product quality, and submit purchase order submissions. It also allows users to create Gantt charts to provide transparency of all operations. Using the Visual Supply Schedule, users can see a forecast of inventory levels and anticipated supply and demand. When supply chain problems arise, they can adjust the schedules. It provides managers with the ability track the progress and status of job functions on different production floors.
Microsoft Dynamics 365 Supply Chain Management offers organizations a unified and predictive approach to managing customer demand and ensuring that the right materials and the right places are available at all times. It is also useful for businesses in anticipating customer needs and changing capacity. It integrates logistics, purchasing, and production, and it can be used for multiple sites and warehouses. It supports vendor-specific pricing and multiple inventory costing methods. It can also be used for transportation management. The solution supports inventory optimization, predictive analytics, and AI features.
Dynamics 365 also includes self-service capabilities for suppliers. Suppliers are able to accept or reject buy orders, issue POs with invoices, and enter shipment information. You can also use it to calculate inventory costs, including vendor-specific pricing, item-level and item-group pricing. It includes many inventory optimization features, such as the ability to create an order-specific inventory allocation plan.
Supply Dynamics offers unique solutions for benchmarking metals prices. This technology allows manufacturers to react faster to market fluctuations. They can also anticipate and predict fluctuations in production costs. This technology allows manufacturers to lower the cost of raw materials and thus reduce waste. It also provides manufacturers with a blueprint for the bill-of-material data conversion process.

The master planning function automates the creation and processing of Production Orders that are based on open Purchase Orders. It also features an optimization plugin that lets users forecast changes in customer needs. Using AI capabilities, it can also help enhance the flow of goods distribution. Microsoft has certified Dynamics Supply Chain Management, making it an excellent solution for companies looking to create a strong supply network.
FAQ
How can manufacturing avoid production bottlenecks
The key to avoiding bottlenecks in production is to keep all processes running smoothly throughout the entire production cycle, from the time you receive an order until the time when the product ships.
This includes planning to meet capacity requirements and quality control.
Continuous improvement techniques like Six Sigma are the best way to achieve this.
Six Sigma Management System is a method to increase quality and reduce waste throughout your organization.
It emphasizes consistency and eliminating variance in your work.
Is automation necessary in manufacturing?
Not only are service providers and manufacturers important, but so is automation. Automation allows them to deliver services quicker and more efficiently. It reduces human errors and improves productivity, which in turn helps them lower their costs.
What is the role of a logistics manager
Logistics managers ensure that goods arrive on time and are unharmed. This is done by using his/her experience and knowledge of the company's products. He/she also needs to ensure adequate stock to meet demand.
How is a production manager different from a producer planner?
A production planner is more involved in the planning phase of the project than a project manger.
Statistics
- It's estimated that 10.8% of the U.S. GDP in 2020 was contributed to manufacturing. (investopedia.com)
- In the United States, for example, manufacturing makes up 15% of the economic output. (twi-global.com)
- According to a Statista study, U.S. businesses spent $1.63 trillion on logistics in 2019, moving goods from origin to end user through various supply chain network segments. (netsuite.com)
- In 2021, an estimated 12.1 million Americans work in the manufacturing sector.6 (investopedia.com)
- [54][55] These are the top 50 countries by the total value of manufacturing output in US dollars for its noted year according to World Bank.[56] (en.wikipedia.org)
External Links
How To
How to Use the Just In Time Method in Production
Just-in-time (JIT) is a method that is used to reduce costs and maximize efficiency in business processes. It's a way to ensure that you get the right resources at just the right time. This means that only what you use is charged to your account. Frederick Taylor was the first to coin this term. He developed it while working as a foreman during the early 1900s. After observing how workers were paid overtime for late work, he realized that overtime was a common practice. He decided to ensure workers have enough time to do their jobs before starting work to improve productivity.
The idea behind JIT is that you should plan ahead and have everything ready so you don't waste money. The entire project should be looked at from start to finish. You need to ensure you have enough resources to tackle any issues that might arise. You can anticipate problems and have enough equipment and people available to fix them. You won't have to pay more for unnecessary items.
There are different types of JIT methods:
-
Demand-driven JIT: You order the parts and materials you need for your project every other day. This will allow to track how much material has been used up. It will also allow you to predict how long it takes to produce more.
-
Inventory-based: You stock materials in advance to make your projects easier. This allows you predict the amount you can expect to sell.
-
Project-driven: This method allows you to set aside enough funds for your project. Knowing how much money you have available will help you purchase the correct amount of materials.
-
Resource-based JIT: This type of JIT is most commonly used. Here you can allocate certain resources based purely on demand. You might assign more people to help with orders if there are many. If there aren't many orders, you will assign fewer people.
-
Cost-based: This is the same as resource-based except that you don't care how many people there are but how much each one of them costs.
-
Price-based: This is similar to cost-based but instead of looking at individual workers' salaries, you look at the total company price.
-
Material-based: This is very similar to cost-based but instead of looking at total costs of the company you are concerned with how many raw materials you use on an average.
-
Time-based JIT: A variation on resource-based JIT. Instead of focusing on how much each employee costs, you focus on how long it takes to complete the project.
-
Quality-based JIT: Another variation on resource-based JIT. Instead of looking at the labor costs and time it takes to make a product, think about its quality.
-
Value-based JIT : This is the newest type of JIT. In this case, you're not concerned with how well the products perform or whether they meet customer expectations. Instead, your goal is to add value to the market.
-
Stock-based: This stock-based method focuses on the actual quantity of products being made at any given time. This is used to increase production and minimize inventory.
-
Just-in-time planning (JIT): This is a combination JIT and supply-chain management. It refers to the process of scheduling the delivery of components as soon as they are ordered. It is essential because it reduces lead-times and increases throughput.