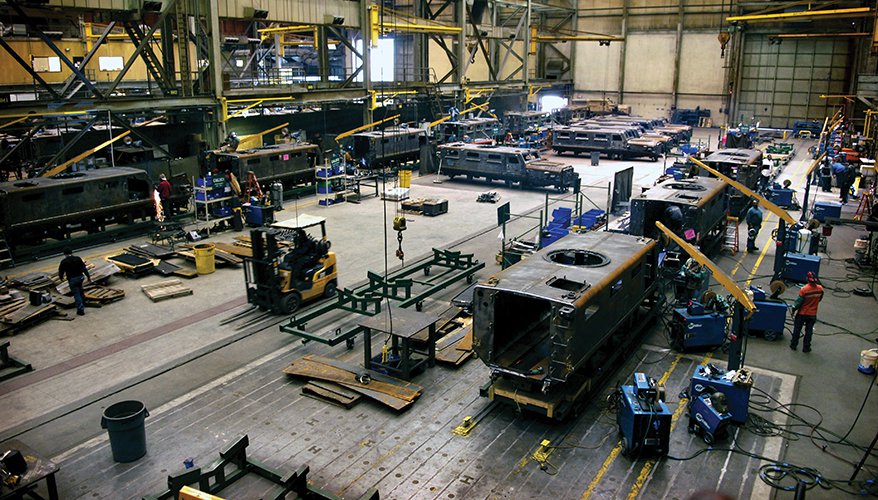
Integrated supply chain management is a process that allows a company to monitor and optimize the performance of its supply chain. This results in a more efficient and responsive production network. Your operations will be more efficient if your supply chain is more efficient and responsive. Integrated supply chain management can help you increase your profits and minimize waste. This means your products will be more reliable and affordable to make.
Integrated supply chain management can improve your order reliability. Your production schedule can be more responsive, inventory levels more accurate, and your delivery dates more flexible. Integrated supply chains are also better at managing risk. It can also reduce greenhouse gas emissions. This can help you meet your environmental goals.
The first step in integration is to draft a contract with your preferred vendors. These agreements should be tailored for your company's specific needs. The agreement should include details about your production schedule, the materials that you require, and the cost involved. Your preferred suppliers must also be able demonstrate how their services will benefit the organization. Higher volumes of goods and services can lead to lower prices.
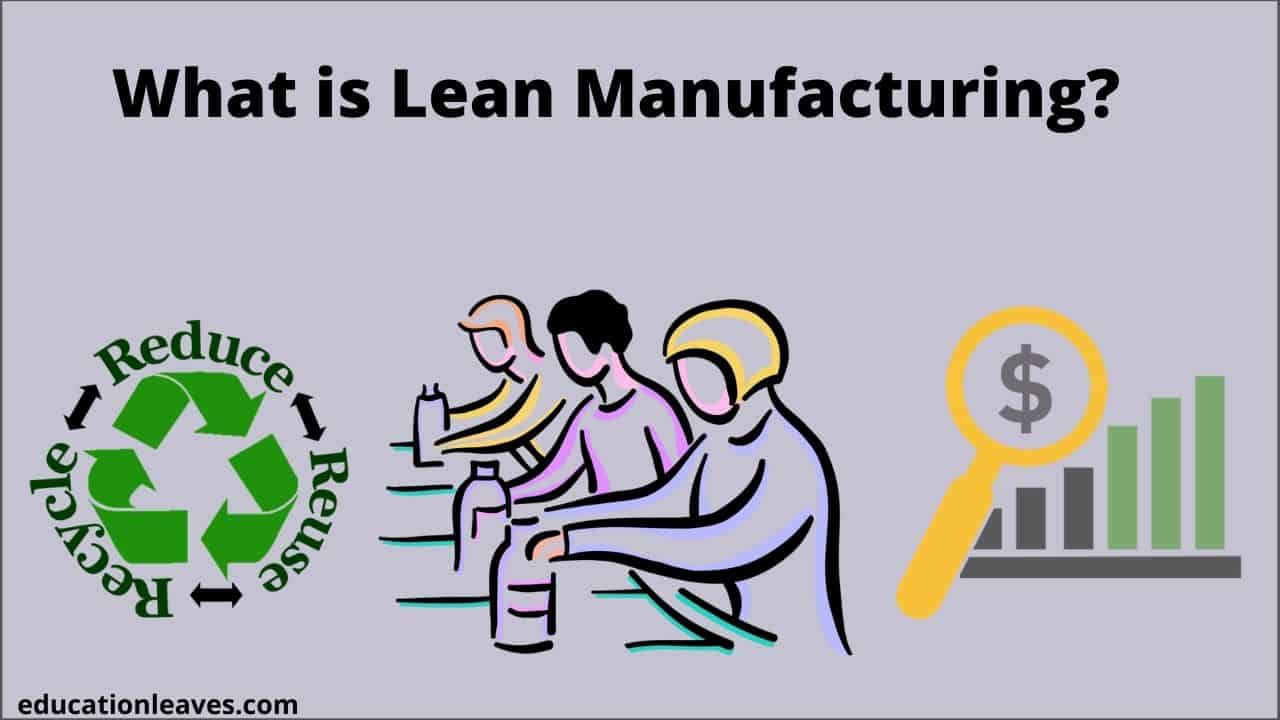
An important part of integrated supply chains management is a good understanding of your connections and how they affect you business. This helps identify areas for improvement and to avoid making mistakes. A comprehensive plan should be developed to address all your needs. This plan should be flexible enough for any production differences. This will help you avoid any delays.
Just-in time distribution is an example of an integrated supply system. This strategy helps to decrease operational costs and reduce warehouse space requirements. It can also improve forecast accuracy. For reducing greenhouse gas emission, it is also important to have an integrated supply system. Reduce your use of large, fixed assets to achieve this.
Vertical integration is when you have all of the necessary elements in place for a certain product. This could be a manufacturer or vendor. This could result in a higher share of profits for the manufacturer. You might also decide to purchase a widget manufacturer or a firm that manufactures widgets. This can allow you to control your competitor's business and ensure that you have a fair widget price.
Another example of an integrated supply chain is a container management strategy. This allows you to view inventory levels and make adjustments to your container pull strategies as needed. It also allows you to make changes to your production schedule in real time.
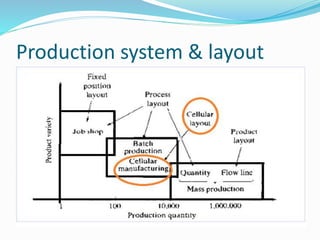
A supply chain management system that has clear goals is more effective. Integrated supply chains have one goal: to maximize performance and provide the best products for customers. You can reduce plastic waste by using an integrated supply network. This can help increase your profit margins and decrease your greenhouse gas emission.
FAQ
What are the responsibilities of a logistic manager?
Logistics managers are responsible for ensuring that all goods arrive in perfect condition and on time. This is achieved by using their knowledge and experience with the products of the company. He/she must also ensure sufficient stock to meet the demand.
How can manufacturing excess production be decreased?
Better inventory management is key to reducing excess production. This would reduce the time needed to manage inventory. By doing this, we could free up resources for other productive tasks.
A Kanban system is one way to achieve this. A Kanban board, a visual display to show the progress of work, is called a Kanban board. In a Kanban system, work items move through a sequence of states until they reach their final destination. Each state is assigned a different priority.
As an example, if work is progressing from one stage of the process to another, then the current task is complete and can be transferred to the next. It is possible to keep a task in the beginning stages until it gets to the end.
This allows work to move forward and ensures that no work is missed. A Kanban board allows managers to monitor how much work is being completed at any given moment. This information allows them to adjust their workflow based on real-time data.
Another way to control inventory levels is to implement lean manufacturing. Lean manufacturing seeks to eliminate waste from every step of the production cycle. Anything that does not contribute to the product's value is considered waste. The following are examples of common waste types:
-
Overproduction
-
Inventory
-
Unnecessary packaging
-
Exceed materials
These ideas can help manufacturers improve efficiency and reduce costs.
What are the essential elements of running a logistics firm?
To be a successful businessman in logistics, you will need many skills and knowledge. Good communication skills are essential to effectively communicate with your suppliers and clients. You will need to know how to interpret data and draw conclusions. You must be able manage stress and pressure under pressure. You must be creative and innovative to develop new ideas to improve efficiency. Strong leadership qualities are essential to motivate your team and help them achieve their organizational goals.
You should also be organized and efficient to meet tight deadlines.
What is the role of a manager in manufacturing?
A manufacturing manager must ensure that all manufacturing processes are efficient and effective. They should also be aware of any problems within the company and act accordingly.
They must also be able to communicate with sales and marketing departments.
They should be up to date on the latest trends and be able apply this knowledge to increase productivity and efficiency.
What skills should a production planner have?
To become a successful production planner, you need to be organized, flexible, and able to multitask. It is also important to be able communicate with colleagues and clients.
Statistics
- According to the United Nations Industrial Development Organization (UNIDO), China is the top manufacturer worldwide by 2019 output, producing 28.7% of the total global manufacturing output, followed by the United States, Japan, Germany, and India.[52][53] (en.wikipedia.org)
- (2:04) MTO is a production technique wherein products are customized according to customer specifications, and production only starts after an order is received. (oracle.com)
- [54][55] These are the top 50 countries by the total value of manufacturing output in US dollars for its noted year according to World Bank.[56] (en.wikipedia.org)
- Job #1 is delivering the ordered product according to specifications: color, size, brand, and quantity. (netsuite.com)
- It's estimated that 10.8% of the U.S. GDP in 2020 was contributed to manufacturing. (investopedia.com)
External Links
How To
How to Use Lean Manufacturing for the Production of Goods
Lean manufacturing (or lean manufacturing) is a style of management that aims to increase efficiency, reduce waste and improve performance through continuous improvement. It was created in Japan by Taiichi Ohno during the 1970s and 80s. He received the Toyota Production System award (TPS), from Kanji Toyoda, founder of TPS. Michael L. Watkins published the first book on lean manufacturing in 1990.
Lean manufacturing is often defined as a set of principles used to improve the quality, speed, and cost of products and services. It emphasizes reducing defects and eliminating waste throughout the value chain. Lean manufacturing is called just-in-time (JIT), zero defect, total productive maintenance (TPM), or 5S. Lean manufacturing is about eliminating activities that do not add value, such as inspection, rework, and waiting.
Lean manufacturing improves product quality and costs. It also helps companies reach their goals quicker and decreases employee turnover. Lean Manufacturing is one of the most efficient ways to manage the entire value chains, including suppliers and customers as well distributors and retailers. Lean manufacturing practices are widespread in many industries. Toyota's philosophy is a great example of this. It has helped to create success in automobiles as well electronics, appliances and healthcare.
Five principles are the basis of lean manufacturing:
-
Define Value - Identify the value your business adds to society and what makes you different from competitors.
-
Reduce Waste – Eliminate all activities that don't add value throughout the supply chain.
-
Create Flow – Ensure that work flows smoothly throughout the process.
-
Standardize and simplify - Make your processes as consistent as possible.
-
Build Relationships - Establish personal relationships with both internal and external stakeholders.
Lean manufacturing isn’t new, but it has seen a renewed interest since 2008 due to the global financial crisis. To increase their competitiveness, many businesses have turned to lean manufacturing. Many economists believe lean manufacturing will play a major role in economic recovery.
Lean manufacturing has many benefits in the automotive sector. These include better customer satisfaction and lower inventory levels. They also result in lower operating costs.
It can be applied to any aspect of an organisation. Because it makes sure that all value chains are efficient and effectively managed, Lean Manufacturing is particularly helpful for organizations.
There are three main types of lean manufacturing:
-
Just-in-Time Manufacturing: Also known as "pull systems", this type of lean manufacturing uses just-in-time manufacturing (JIT). JIT means that components are assembled at the time of use and not manufactured in advance. This method reduces lead times, increases availability, and decreases inventory.
-
Zero Defects Manufacturing - ZDM: ZDM focuses its efforts on making sure that no defective units leave a manufacturing facility. It is better to repair a part than have it removed from the production line if it needs to be fixed. This also applies to finished products that need minor repairs before being shipped.
-
Continuous Improvement (CI), also known as Continuous Improvement, aims at improving the efficiency of operations through continuous identification and improvement to minimize or eliminate waste. Continuous Improvement involves continuous improvement of processes.