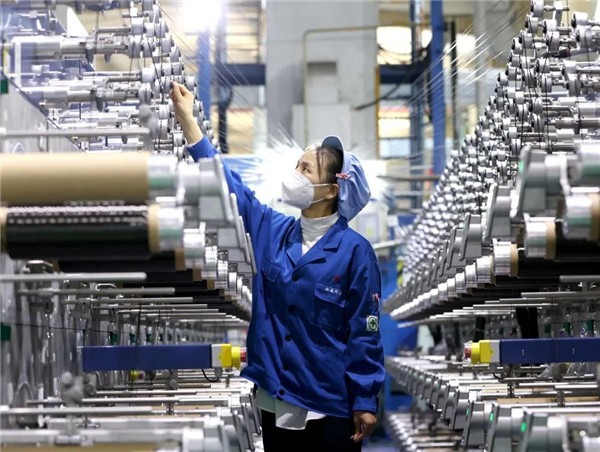
Visual management is the act of using visual signals to convey information. This allows for greater efficiency and clarity. Information is immediately identified. There are several kinds of visual control. Listed below are some of the most common examples. You can also read about visual control in Lean manufacturing. Continue reading for more information. This is a great way for your company to adopt lean manufacturing.
Lean manufacturing
One of the many methods used for visual management in lean manufacturing is the use of Andon, a Japanese word for status-display visualization. This technique allows supervisors and workers alike to see work-in progress, process flow, or any other pertinent information. Visual management allows for easy labeling of workspaces and materials as well as parts, finished goods, or waste. This helps identify inefficiencies and streamlines processes. These are just a few of the benefits that visual management can bring to lean manufacturing.
Visible tools for visual management are a crucial component of the Lean methodology. Clear visual signals enable supervisors to spot waste, improve flow, and avoid making mistakes. It can also help reduce safety concerns. By using visual indicators and floor markings, forklift operators can make sure they stay in the correct areas. Workers can work more efficiently by using visual management when lean manufacturing is used. In addition to reducing waste, visual management also minimizes safety risks.
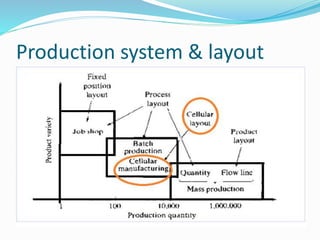
Process control charts
Process control charts are a powerful tool for visualizing performance metrics, setting a baseline for future improvement, and improving output. They are a way for managers, operators, and all other stakeholders to communicate and agree on common causes and the best path forward. These charts are especially useful for processes with unusual patterns of variation. Because they are very easy to make, process control charts can be used for visual management. They can also be used to show the status of any system or process.
The primary function of a control chart is to track process performance over time. These charts display the sequence of samples and measurements that allow managers to determine whether or not the process is stable. They can also serve as an analytical tool to spot problems and propose solutions. An operator can compare the process’s performance with the baseline by using the centerline in the control chart. The control limits generally have three standard deviations between the centerline and the edge.
FIFO lane
FIFO lanes may increase throughput or utilization of a system. You can think of a factory line or a fast food counter. Most of us have probably experienced the frustration that comes with standing in long lines to obtain something. The FiFo lane is a visual management tool that helps you control the flow of work. It establishes priority in queues and allows for visual management. You can create these lanes by using paint lines, marking roller conveyors or clearly marking shelves. The first job arriving from Process A would go into the first open position of a FIFO lane. The next job will be moved to the next vacant position.
Implementing time registration can be a great way to improve FIFO lane visual organization. Employees can log the date and time of each item that is placed in a FIFO lane when carts have been loaded. Some employees use digital counters to count how many products are in each FIFO lane. You can also install whiteboard stickers to write down times on carts. These whiteboard stickers will allow downstream employees to refer to the times and determine which order they should take.
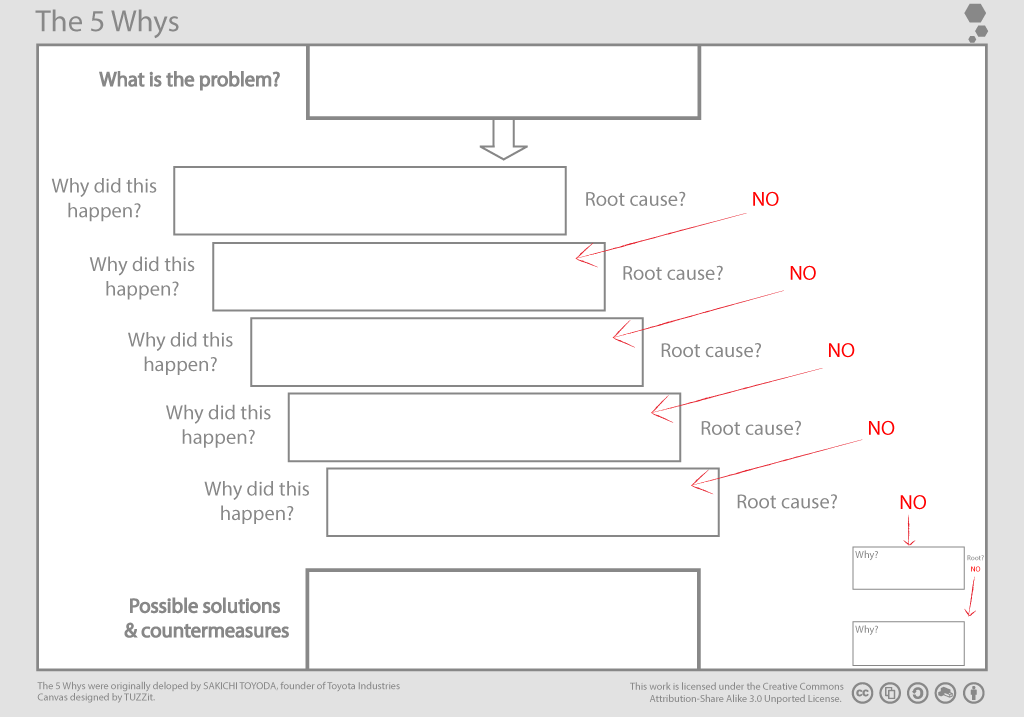
Lean daily management board
The Lean Daily Management Board was created by a multidisciplinary team based on five predetermined metrics: patient outcomes, documentation adherence, employee engagement, and productivity. Each day, the team met to review each area's progress. The team used a checklist to verify each daily activity, such as medication adherence and medication falls. To address any problems, they also used a problem-solving tool. Initial data collected January 2014 revealed a medication scan rate 75% and a rate of fall of 1.32/1000 days. These initial data weren't specific to patient care nor continuing education.
Instead of simply looking at a company's performance over time, daily managing makes it visible. Managers can then respond to problems as soon as they happen. Poor performers stretch out work to avoid being asked to do more. Poor performers must be able to clearly see the stretching work and account for the additional time and effort required to complete the work. While daily management isn't meant to be punitive, it does highlight any processes that may be inefficient or ineffective. Those who cannot point to a process' failure should be evaluated as people issues.
FAQ
What skills are required to be a production manager?
A production planner must be organized, flexible, and able multitask to succeed. Also, you must be able and willing to communicate with clients and coworkers.
What is the difference between Production Planning, Scheduling and Production Planning?
Production Planning (PP), is the process of deciding what production needs to take place at any given time. Forecasting and identifying production capacity are two key elements to this process.
Scheduling refers to the process of allocating specific dates to tasks in order that they can be completed within a specified timeframe.
How can manufacturing efficiency improved?
First, identify the factors that affect production time. We must then find ways that we can improve these factors. If you don’t know how to start, look at which factors have the greatest impact upon production time. Once you have identified them, it is time to identify solutions.
What are the four types of manufacturing?
Manufacturing refers the process of turning raw materials into useful products with machines and processes. It includes many different activities like designing, building and testing, packaging, shipping and selling, as well as servicing.
Can some manufacturing processes be automated?
Yes! Since ancient times, automation has been in existence. The Egyptians discovered the wheel thousands and years ago. Today, robots assist in the assembly of lines.
In fact, there are several applications of robotics in manufacturing today. These include:
-
Robots for assembly line
-
Robot welding
-
Robot painting
-
Robotics inspection
-
Robots that create products
There are many other examples of how manufacturing could benefit from automation. For example, 3D printing allows us to make custom products without having to wait for weeks or months to get them manufactured.
Statistics
- Job #1 is delivering the ordered product according to specifications: color, size, brand, and quantity. (netsuite.com)
- (2:04) MTO is a production technique wherein products are customized according to customer specifications, and production only starts after an order is received. (oracle.com)
- In the United States, for example, manufacturing makes up 15% of the economic output. (twi-global.com)
- Many factories witnessed a 30% increase in output due to the shift to electric motors. (en.wikipedia.org)
- It's estimated that 10.8% of the U.S. GDP in 2020 was contributed to manufacturing. (investopedia.com)
External Links
How To
How to use the Just-In Time Method in Production
Just-intime (JIT), a method used to lower costs and improve efficiency in business processes, is called just-in-time. It's a way to ensure that you get the right resources at just the right time. This means that you only pay the amount you actually use. Frederick Taylor first coined this term while working in the early 1900s as a foreman. After observing how workers were paid overtime for late work, he realized that overtime was a common practice. He decided that workers would be more productive if they had enough time to complete their work before they started to work.
The idea behind JIT is that you should plan ahead and have everything ready so you don't waste money. The entire project should be looked at from start to finish. You need to ensure you have enough resources to tackle any issues that might arise. If you expect problems to arise, you will be able to provide the necessary equipment and personnel to address them. This way you won't be spending more on things that aren’t really needed.
There are many JIT methods.
-
Demand-driven JIT: You order the parts and materials you need for your project every other day. This will enable you to keep track of how much material is left after you use it. It will also allow you to predict how long it takes to produce more.
-
Inventory-based: This allows you to store the materials necessary for your projects in advance. This allows you to forecast how much you will sell.
-
Project-driven: This method allows you to set aside enough funds for your project. Knowing how much money you have available will help you purchase the correct amount of materials.
-
Resource-based JIT: This is the most popular form of JIT. You allocate resources based on the demand. You might assign more people to help with orders if there are many. If there aren't many orders, you will assign fewer people.
-
Cost-based: This approach is very similar to resource-based. However, you don't just care about the number of people you have; you also need to consider how much each person will cost.
-
Price-based: This is a variant of cost-based. However, instead of focusing on the individual workers' costs, this looks at the total price of the company.
-
Material-based: This is quite similar to cost-based, but instead of looking at the total cost of the company, you're concerned with how much raw materials you spend on average.
-
Time-based JIT: This is another variant of resource-based JIT. Instead of focusing on the cost of each employee, you will focus on the time it takes to complete a project.
-
Quality-based JIT: Another variation on resource-based JIT. Instead of focusing on the cost of each worker or how long it takes, think about how high quality your product is.
-
Value-based JIT: One of the most recent forms of JIT. You don't worry about whether the products work or if they meet customer expectations. Instead, your focus is on the value you bring to the market.
-
Stock-based is an inventory-based system that measures the number of items produced at any given moment. This method is useful when you want to increase production while decreasing inventory.
-
Just-intime planning (JIT), is a combination JIT/sales chain management. It's the process of scheduling delivery of components immediately after they are ordered. This is important as it reduces lead time and increases throughput.