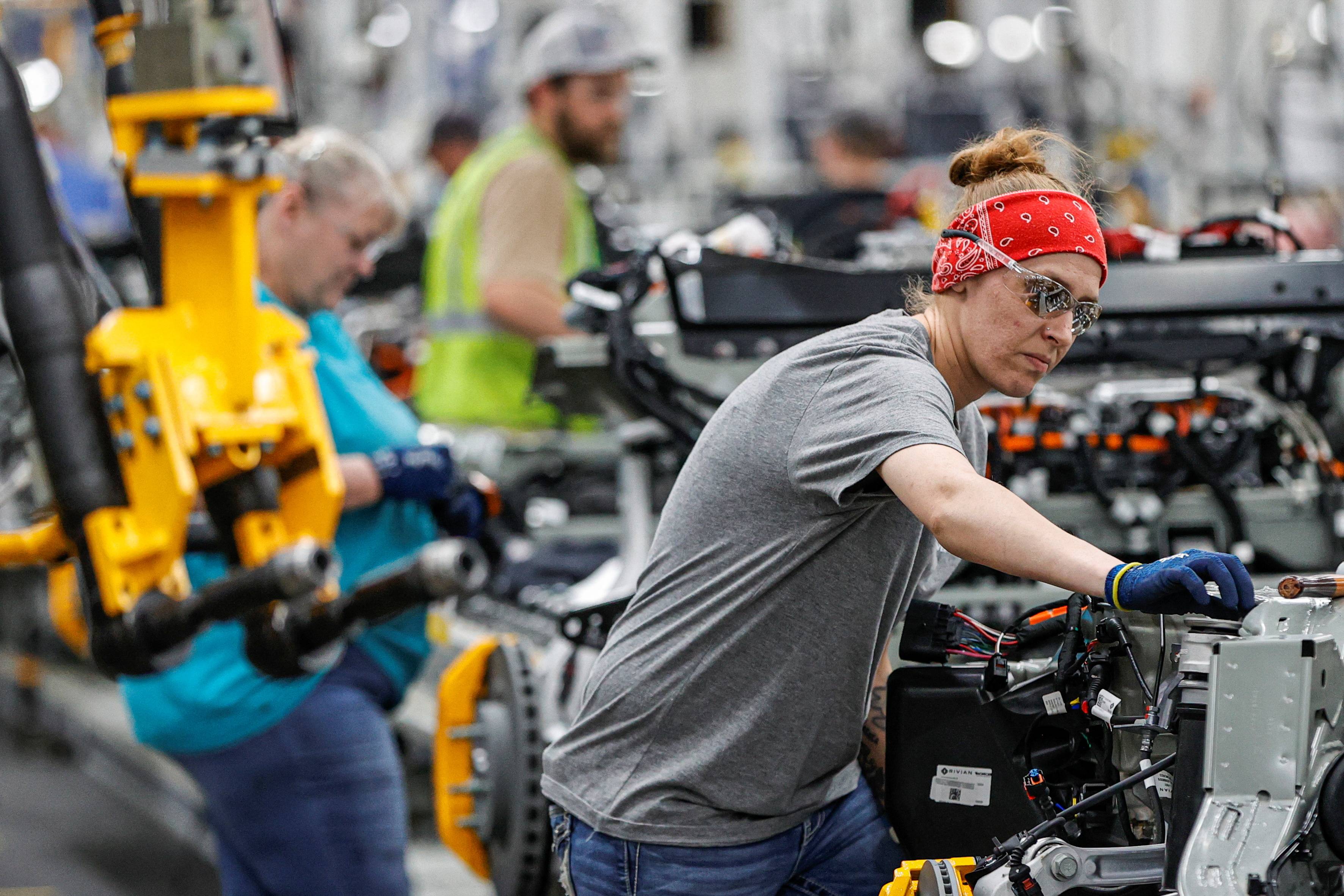
Materials engineers are responsible for the design, development, and research of new materials, which will enable future technology. They use metals, composites, ceramics, and plastics to create materials which meet specific chemical, mechanical, and electrical requirements.
What is a Materials Engineer?
A material engineer tests, processes and develops raw materials, which are then used to create a range of products including aircraft wings or computer chips. They can also be involved in the development of biomedical devices or golf clubs. These engineers analyze and assess the structures and properties in metals. ceramics, plastics. nanomaterials.
The responsibilities of a materials engineer vary according to the specific type of materials that they are working with and the industry in which they are employed. But they are also responsible for creating budgets, assessing production cost, and supervising technicans.
What is the role of a materials scientist engineer?
A materials engineer works on a wide range of materials, including metals ceramics composites. The goal is to make the materials stronger, lighter, more durable. They can also develop new materials that improve existing ones.

What skills does a materials scientist need?
A bachelor's in engineering or materials sciences is required to become a material engineer. This degree must include both classroom and laboratory training with an emphasis placed on engineering principles. It may take up to a year to complete this program.
You can find a job as a materials engineer after graduation and you can expect to earn a salary of around PS25,000 a year. Your salary will rise significantly as you gain experience.
How to become materials engineer
The qualifications that you need to become a materials engineer differ between industries and employers. However, most jobs require at least a bachelor's degree in materials science or engineering. This will involve studies in chemistry, math, and physics.
As a materials scientist engineer, you'll need to have a bachelor's in a relevant subject such as engineering, chemistry, or physics. For higher-level positions in research, a master's degree or doctoral qualification is often required.
How much can I earn as a materials engineering?
The salaries of materials engineers can vary depending on their level of expertise, the industry in which they work and the size of the company. They can also expect to receive bonuses and other perks for their work.
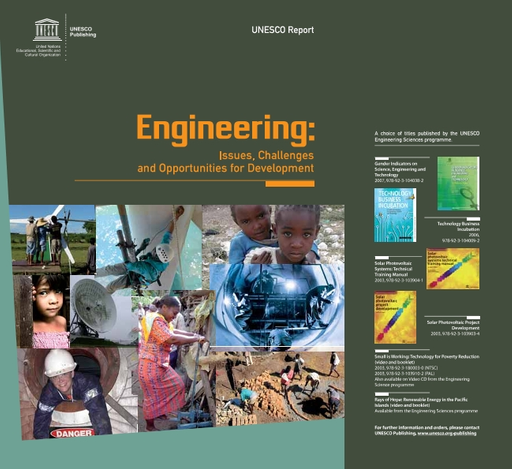
What will the future look like for the Materials Engineering career?
It is predicted that the future of materials engineering will be bright, and there are many opportunities available to those who choose to pursue this career. The increasing demand in the fields of medicine, architecture and communications for newer and more advanced materials has led to this.
Studying metallurgy or chemistry can lead to a career as a materials engineer. You can then pursue a career as a materials engineer. You can improve your research and development abilities by obtaining a degree in a field such as chemistry. You can gain more experience by working in an engineering firm specializing in specific fields of materials.
FAQ
What is production planning?
Production planning is the process of creating a plan that covers all aspects of production. This includes scheduling, budgeting and crew, location, equipment, props, and more. This document ensures that everything is prepared and available when you are ready for shooting. It should also contain information on achieving the best results on set. This includes shooting schedules, locations, cast lists, crew details, and equipment requirements.
First, you need to plan what you want to film. You may already know where you want the film to be shot, or perhaps you have specific locations and sets you wish to use. Once you have determined your scenes and locations, it is time to start figuring out the elements that you will need for each scene. You might decide you need a car, but not sure what make or model. You could look online for cars to see what options are available, and then narrow down your choices by selecting between different makes or models.
Once you have found the right vehicle, you can think about adding accessories. Are you looking for people to sit in the front seats? Maybe you need someone to move around in the back. You might want to change your interior color from black and white. These questions will help determine the look and feel you want for your car. The type of shots that you are looking for is another thing to consider. Do you want to film close-ups, or wider angles? Perhaps you want to show the engine or the steering wheel? All of these things will help you identify the exact style of car you want to film.
Once you've determined the above, it is time to start creating a calendar. The schedule will show you when to begin shooting and when to stop. Every day will have a time for you to arrive at the location, leave when you are leaving and return home when you are done. Everyone will know what they need and when. If you need to hire extra staff, you can make sure you book them in advance. You should not hire anyone who doesn't show up because of your inaction.
Also, consider how many days you will be filming your schedule. Some projects can be completed in a matter of days or weeks. Others may take several days. While creating your schedule, it is important to remember whether you will require more than one shot per day. Multiple takes of the same location will lead to higher costs and take more time. If you are unsure if you need multiple takes, it is better to err on the side of caution and shoot fewer takes rather than risk wasting money.
Budget setting is another important aspect in production planning. As it will allow you and your team to work within your financial means, setting a realistic budget is crucial. Remember that you can always reduce the budget later on if you run into unforeseen problems. You shouldn't underestimate the amount you'll spend. If you underestimate how much something costs, you'll have less money to pay for other items.
Production planning can be a complex process. However, once you know how everything works together it will become easier to plan future projects.
Can we automate some parts of manufacturing?
Yes! Automation has been around since ancient times. The Egyptians invented the wheel thousands of years ago. Today, robots assist in the assembly of lines.
In fact, there are several applications of robotics in manufacturing today. They include:
-
Line robots
-
Robot welding
-
Robot painting
-
Robotics inspection
-
Robots that produce products
Manufacturing can also be automated in many other ways. For instance, 3D printing allows us make custom products and not have to wait for months or even weeks to get them made.
What can I do to learn more about manufacturing?
Experience is the best way for you to learn about manufacturing. But if that is not possible you can always read books and watch educational videos.
How can overproduction in manufacturing be reduced?
In order to reduce excess production, you need to develop better inventory management methods. This would reduce the amount of time spent on unnecessary activities such as purchasing, storing, and maintaining excess stock. This would allow us to use our resources for more productive tasks.
This can be done by using a Kanban system. A Kanbanboard is a visual tool that allows you to keep track of the work being done. Kanban systems allow work items to move through different states until they reach their final destination. Each state is assigned a different priority.
For instance, when work moves from one stage to another, the current task is complete enough to be moved to the next stage. A task that is still in the initial stages of a process will be considered complete until it moves on to the next stage.
This allows you to keep work moving along while making sure that no work gets neglected. Managers can see how much work has been done and the status of each task at any time with a Kanban Board. This information allows them to adjust their workflow based on real-time data.
Lean manufacturing can also be used to reduce inventory levels. Lean manufacturing focuses on eliminating waste throughout the entire production chain. Waste includes anything that does not add value to the product. Some common types of waste include:
-
Overproduction
-
Inventory
-
Unnecessary packaging
-
Material surplus
Manufacturers can increase efficiency and decrease costs by implementing these ideas.
How does a Production Planner differ from a Project Manager?
The difference between a product planner and project manager is that a planer is typically the one who organizes and plans the entire project. A production planner, however, is mostly involved in the planning stages.
Statistics
- Many factories witnessed a 30% increase in output due to the shift to electric motors. (en.wikipedia.org)
- According to the United Nations Industrial Development Organization (UNIDO), China is the top manufacturer worldwide by 2019 output, producing 28.7% of the total global manufacturing output, followed by the United States, Japan, Germany, and India.[52][53] (en.wikipedia.org)
- You can multiply the result by 100 to get the total percent of monthly overhead. (investopedia.com)
- In 2021, an estimated 12.1 million Americans work in the manufacturing sector.6 (investopedia.com)
- [54][55] These are the top 50 countries by the total value of manufacturing output in US dollars for its noted year according to World Bank.[56] (en.wikipedia.org)
External Links
How To
How to Use Six Sigma in Manufacturing
Six Sigma is defined as "the application of statistical process control (SPC) techniques to achieve continuous improvement." It was developed by Motorola's Quality Improvement Department at their plant in Tokyo, Japan, in 1986. The basic idea behind Six Sigma is to improve quality by improving processes through standardization and eliminating defects. Since there are no perfect products, or services, this approach has been adopted by many companies over the years. Six Sigma aims to reduce variation in the production's mean value. If you take a sample and compare it with the average, you will be able to determine how much of the production process is different from the norm. If you notice a large deviation, then it is time to fix it.
The first step toward implementing Six Sigma is understanding how variability works in your business. Once you've understood that, you'll want to identify sources of variation. You'll also want to determine whether these variations are random or systematic. Random variations happen when people make errors; systematic variations are caused externally. For example, if you're making widgets, and some of them fall off the assembly line, those would be considered random variations. If however, you notice that each time you assemble a widget it falls apart in exactly the same spot, that is a problem.
After identifying the problem areas, you will need to devise solutions. The solution could involve changing how you do things, or redesigning your entire process. After implementing the new changes, you should test them again to see if they worked. If they don’t work, you’ll need to go back and rework the plan.