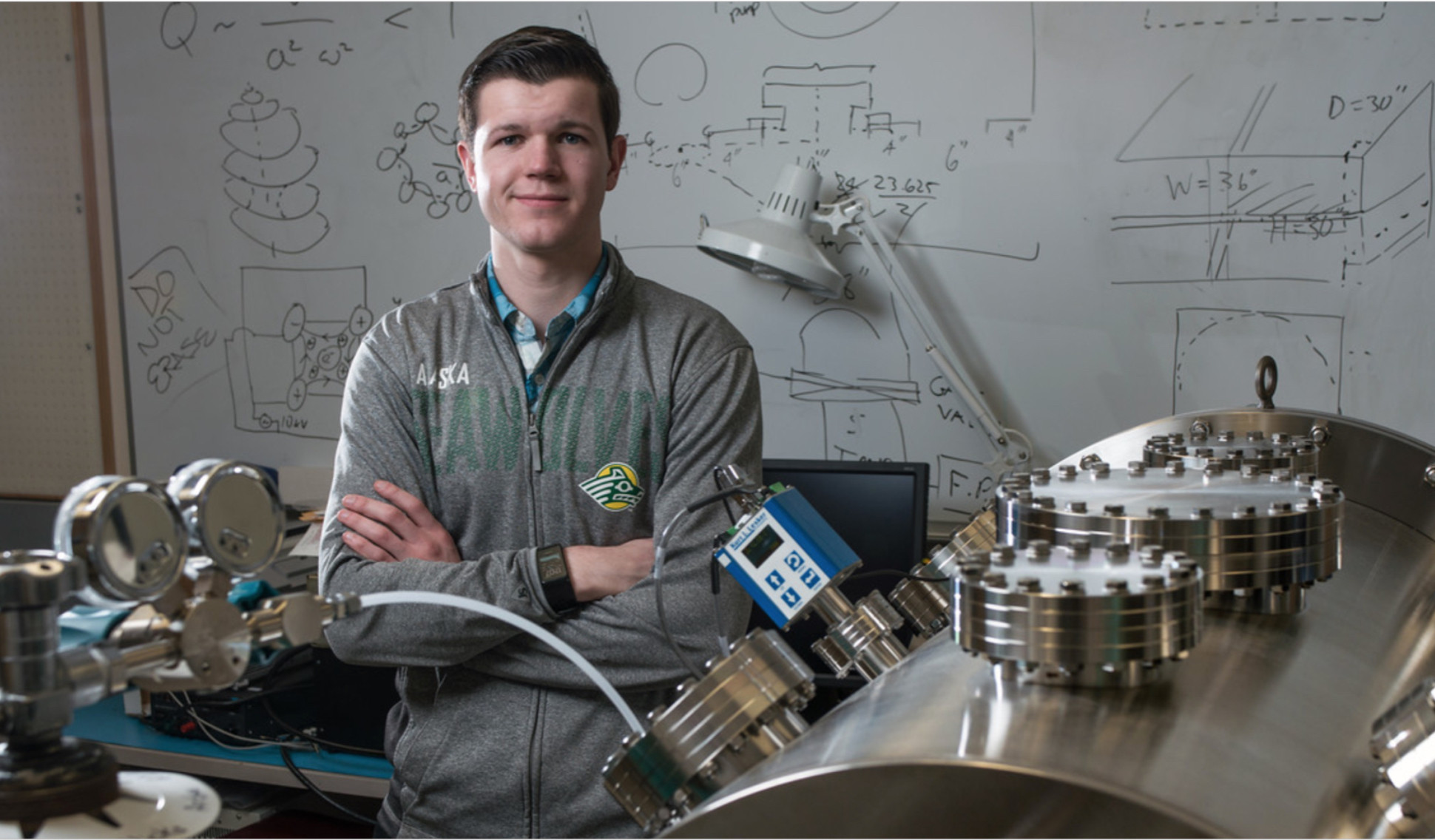
There are many manufacturers. But which one is right for you? Learn more about continuous manufacturing, process manufacturing, job shop manufacturing, and discrete manufacturing. Each type has its pros and cons. This article will detail the differences in these four types. You can choose the best model for your business based on your industry, location, and product type. Once you have chosen the best type for your business, you must consider sales, production, as well as quality control.
Discrete Manufacturing
Discrete production is when distinct products are manufactured. Toys, cars, and aeroplanes are just a few examples of discrete manufacturing. Discrete manufacturing allows companies to focus on individual products, rather than bulk production of all items. In other words, discrete manufacture allows for the creation of unique parts in an aeroplane using multiple manufacturing processes. High-tech products are made using discrete manufacturing.
Discrete manufacturing produces distinct items. Instead of producing many identical products discrete manufacturing creates items that are easily identifiable by serial numbers and labels. For example, a smartphone could be composed of several parts that were manufactured in different states. Each part is assembled only after the final product has been sold. The bag of your smartphone is the same. It could contain parts from different plants, such as the Missouri plant headquarters.
Process manufacturing
The process manufacturing branch is one that deals with formulas or recipes. The term process manufacturing is not the same as discrete manufacturing. This refers to manufacturing that involves individual units, bills or materials and the assembly of component parts. The two manufacturing methods have very different goals. However, each is an essential part of the manufacturing process. There are three main ways to distinguish process manufacturing from discrete manufacturing. Let's have a look at them all.
Batch process manufacturing is similar in many ways to continuous process manufacturing. However, it uses larger quantities and runs continuously. It is commonly used in pharmaceuticals as well as paper production, bookbinding and newspaper printing. However, it is not the right choice for every industry. This method is often too complicated and expensive for small-scale businesses. Therefore, most companies use this method when they need to create large quantities of the same product.
Job shop manufacturing
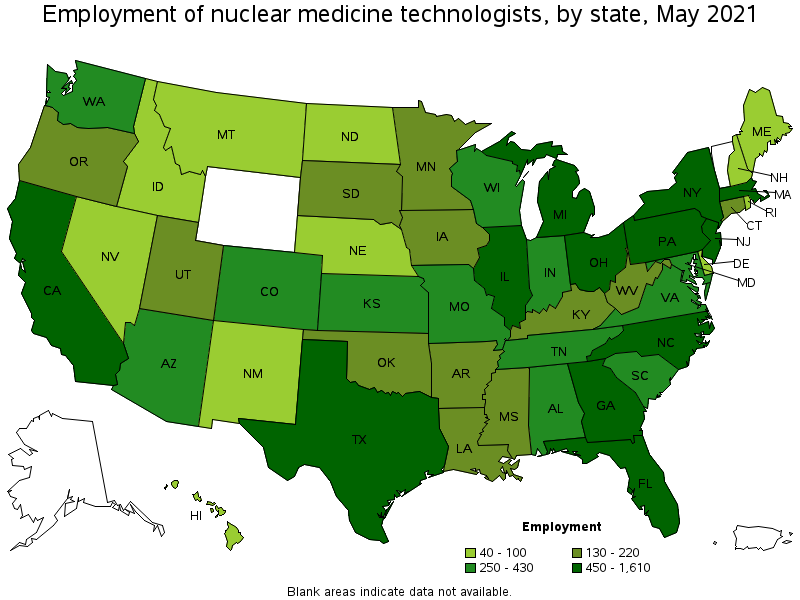
Job shop manufacturing is a small-scale system of production that specializes in custom, batch, and semi-custom manufacturing. Job shop systems can then move on to the next job as each job is finished. This production method is also known as lean manufacturing. A single shift operation is more efficient than other methods. Here are some advantages of job shop production. This manufacturing process is described in detail below. You might consider this for your service or product needs.
First, job shops have to be more efficient. The incorporation of new manufacturing principles is crucial to creating a lean manufacturing environment. These principles are particularly relevant for high-volume operations and emphasize quality control and just in-time production. The job shop can reduce costs and increase productivity by using new manufacturing principles. Additionally, every job should be processed individually, so there should not be a queue.
Continuous manufacturing
One of the biggest benefits of continuous manufacturing is the fact that it allows for much more flexible tracking. This is especially important when it comes to product defect detection. The quantity of raw material and the time stamp can be used to determine if a batch is defective. This increased tracking helps manufacturers reduce waste and decrease the likelihood of product shortages. The pharmaceutical industry is increasingly using continuous manufacturing.
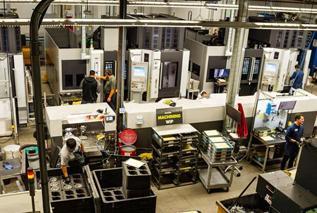
The benefits of continuous production are obvious, but implementation can be slow. The slow pace of implementation can make it difficult to integrate the manufacturing process with the rest. Continuous manufacturing has the potential of being a game changer in the pharmaceutical business, despite the limitations. The process must be seamless and integrate with continuous flow and end to end integration for it to be effective. The pharmaceutical industry has long recognized the benefits of continuous manufacturing, but implementation has been slow.
FAQ
How does a production planner differ from a project manager?
The main difference between a production planner and a project manager is that a project manager is usually the person who plans and organizes the entire project, whereas a production planner is mainly involved in the planning stage of the project.
What is the responsibility of a logistics manager?
Logistics managers ensure that goods arrive on time and are unharmed. This is done using his/her knowledge of the company's products. He/she also needs to ensure adequate stock to meet demand.
What does the term manufacturing industries mean?
Manufacturing Industries refers to businesses that manufacture products. Consumers are the people who purchase these products. To accomplish this goal, these companies employ a range of processes including distribution, sales, management, and production. They create goods from raw materials, using machines and various other equipment. This includes all types and varieties of manufactured goods, such as food items, clothings, building supplies, furnitures, toys, electronics tools, machinery vehicles, pharmaceuticals medical devices, chemicals, among others.
How can manufacturing efficiency improved?
The first step is to determine the key factors that impact production time. Next, we must find ways to improve those factors. If you don’t know how to start, look at which factors have the greatest impact upon production time. Once you've identified them, try to find solutions for each of those factors.
How can we reduce manufacturing overproduction?
The key to reducing overproduction lies in developing better ways to manage inventory. This would reduce the amount of time spent on unnecessary activities such as purchasing, storing, and maintaining excess stock. By doing this, we could free up resources for other productive tasks.
This can be done by using a Kanban system. A Kanban board is a visual display used to track work in progress. A Kanban system allows work items to move through several states before reaching their final destination. Each state has a different priority level.
If work is moving from one stage to the other, then the current task can be completed and moved on to the next. A task that is still in the initial stages of a process will be considered complete until it moves on to the next stage.
This allows you to keep work moving along while making sure that no work gets neglected. Managers can monitor the work being done by Kanban boards to see what is happening at any given time. This data allows them adjust their workflow based upon real-time data.
Lean manufacturing, another method to control inventory levels, is also an option. Lean manufacturing works to eliminate waste throughout every stage of the production chain. Anything that does nothing to add value to a product is waste. The following are examples of common waste types:
-
Overproduction
-
Inventory
-
Packaging that is not necessary
-
Materials in excess
Manufacturers can increase efficiency and decrease costs by implementing these ideas.
Are there any Manufacturing Processes that we should know before we can learn about Logistics?
No. No. Understanding the manufacturing process will allow you to better understand logistics.
Statistics
- Job #1 is delivering the ordered product according to specifications: color, size, brand, and quantity. (netsuite.com)
- You can multiply the result by 100 to get the total percent of monthly overhead. (investopedia.com)
- [54][55] These are the top 50 countries by the total value of manufacturing output in US dollars for its noted year according to World Bank.[56] (en.wikipedia.org)
- (2:04) MTO is a production technique wherein products are customized according to customer specifications, and production only starts after an order is received. (oracle.com)
- According to a Statista study, U.S. businesses spent $1.63 trillion on logistics in 2019, moving goods from origin to end user through various supply chain network segments. (netsuite.com)
External Links
How To
How to use Lean Manufacturing in the production of goods
Lean manufacturing refers to a method of managing that seeks to improve efficiency and decrease waste. It was first developed in Japan in the 1970s/80s by Taiichi Ahno, who was awarded the Toyota Production System (TPS), award from KanjiToyoda, the founder of TPS. The first book published on lean manufacturing was titled "The Machine That Changed the World" written by Michael L. Watkins and published in 1990.
Lean manufacturing is often described as a set if principles that help improve the quality and speed of products and services. It emphasizes eliminating waste and defects throughout the value stream. Lean manufacturing can be described as just-in–time (JIT), total productive maintenance, zero defect (TPM), or even 5S. Lean manufacturing seeks to eliminate non-value added activities, such as inspection, work, waiting, and rework.
Lean manufacturing can help companies improve their product quality and reduce costs. Additionally, it helps them achieve their goals more quickly and reduces employee turnover. Lean manufacturing has been deemed one of the best ways to manage the entire value-chain, including customers, distributors as well retailers and employees. Lean manufacturing is widely used in many industries. Toyota's philosophy is a great example of this. It has helped to create success in automobiles as well electronics, appliances and healthcare.
Five basic principles of Lean Manufacturing are included in lean manufacturing
-
Define Value - Determine the value that your business brings to society. Also, identify what sets you apart from your competitors.
-
Reduce Waste - Eliminate any activity that doesn't add value along the supply chain.
-
Create Flow - Make sure work runs smoothly without interruptions.
-
Standardize & Simplify - Make processes as consistent and repeatable as possible.
-
Build Relationships - Establish personal relationships with both internal and external stakeholders.
Lean manufacturing, although not new, has seen renewed interest in the economic sector since 2008. Many businesses are now using lean manufacturing to improve their competitiveness. According to some economists, lean manufacturing could be a significant factor in the economic recovery.
Lean manufacturing is becoming a popular practice in automotive. It has many advantages. These include higher customer satisfaction levels, reduced inventory levels as well as lower operating costs.
Any aspect of an enterprise can benefit from Lean manufacturing. This is because it ensures efficiency and effectiveness in all stages of the value chain.
There are three main types of lean manufacturing:
-
Just-in-Time Manufacturing: Also known as "pull systems", this type of lean manufacturing uses just-in-time manufacturing (JIT). JIT refers to a system in which components are assembled at the point of use instead of being produced ahead of time. This approach reduces lead time, increases availability and reduces inventory.
-
Zero Defects Manufacturing: ZDM ensures that no defective units leave the manufacturing plant. It is better to repair a part than have it removed from the production line if it needs to be fixed. This is true even for finished products that only require minor repairs prior to shipping.
-
Continuous Improvement (CI: Continuous improvement aims to increase the efficiency of operations by constantly identifying and making improvements to reduce or eliminate waste. It involves continuous improvement of processes, people, and tools.