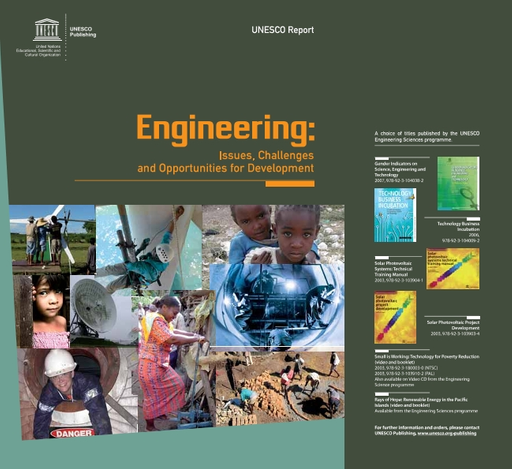
Lean manufacturing is a great way to reduce costs, improve lead times and minimize set-up and turnaround times. The benefits of using lean manufacturing are obvious: they cut costs and increase lead times while improving customer experiences. These are the key benefits of lean manufacturing, which can help you grow your business. If you're still skeptical, let's take a look at three reasons that lean manufacturing is the best method to make products and lower costs.
Reduced costs
Lean manufacturing has the potential to bring about significant efficiency. Manufacturers can save money on direct labor costs by reducing defects or rework. In this way, labor costs are less motivating for decision-making. Eliminating hazardous waste is another advantage. The cost of direct labor in many industries is less than 15%. This makes outsourcing to low-cost areas more difficult. This can help reduce manufacturing costs and improve customer service.
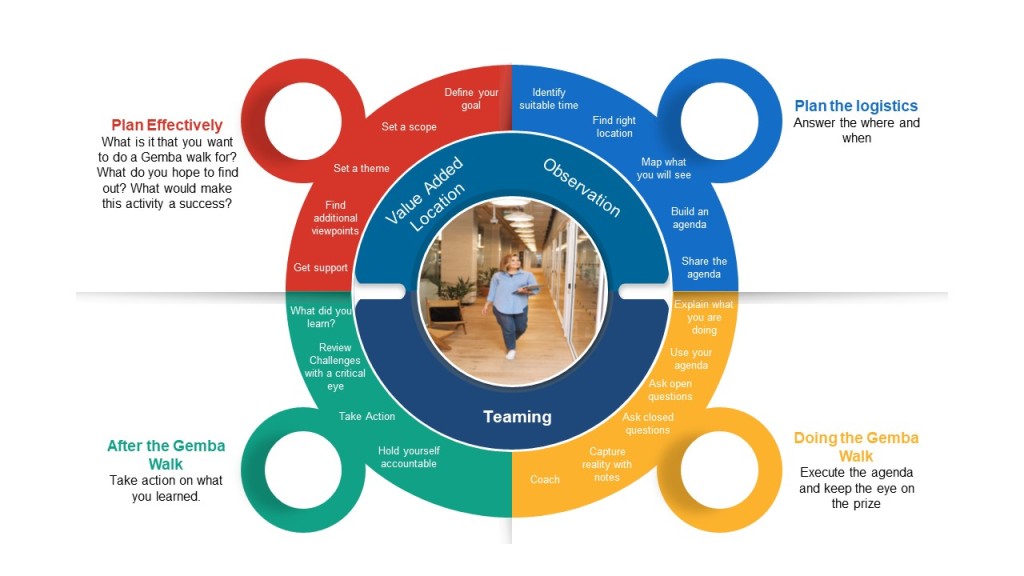
Lead times are improved
Lean manufacturing has many benefits, including the ability reduce waste and increase lead times. It is a philosophy that promotes continuous improvement, or "kaizen". It brings together the talents of employees. It promotes collaboration and employee accountability. The process can decrease lead times by as high as 20% The most important aspect of lean manufacturing is the ability to make small adjustments often to improve the product quality and efficiency.
Shortens set-up times
Reduced set-up time is a great way to cut down on the time it takes to make a product. The time it takes for a product to be switched from its last item to the new one is called setup time. The setup time includes preparation, replacement, as well as location activities. These activities can be internal or external. While internal activities require an inactive process, such as a machine being moved or an item being positioned, external setup activities can be performed while the process is still operational.
Reduces time it takes to get to market
Lean manufacturing (or continuous improvement) was developed in Japan as a way to improve the quality of manufacturing. It sought to improve competitiveness and reduce lead times. By shortening the time it takes for a product to reach the market, companies can meet customer demands and increase profitability. This approach to production will not only increase the efficiency of manufacturing, but also improve the overall efficiency of the facility.
Improves product quality
Lean manufacturing's success depends on the ability to reduce waste, improve product quality, and minimize costs. It's been used by small and large companies as well. It can lower lead times, costs, labor, and other expenses. Learn more about how lean production can help improve your business. These are some of the areas you should be focusing on. Lean principles can lower lead times by as much as 90%, improve product performance, and reduce costs.
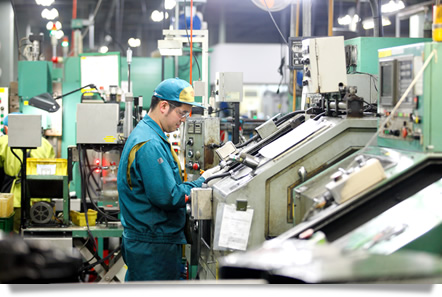
Direct labor costs can be reduced
Low indirect labor costs are the low hanging fruit of lean manufacturing. Lean companies focus less on direct labor efficiency and look instead for ways to lower indirect labor costs. This includes eliminating management, material handling, inspection and management jobs as well as pushing production decisions to the floor. It's the same approach used by Toyota and other lean manufacturing companies. In this article, we'll examine how lean production can lower indirect labor expenses.
FAQ
What are the four types in manufacturing?
Manufacturing refers the process of turning raw materials into useful products with machines and processes. It involves many different activities such as designing, building, testing, packaging, shipping, selling, servicing, etc.
Is automation important in manufacturing?
Not only is automation important for manufacturers, but it's also vital for service providers. They can provide services more quickly and efficiently thanks to automation. It helps them to lower costs by reducing human errors, and improving productivity.
Are there any Manufacturing Processes that we should know before we can learn about Logistics?
No. No. But, being familiar with manufacturing processes will give you a better understanding about how logistics works.
What is the role of a production manager?
A production planner ensures all aspects of the project are delivered on time, within budget, and within scope. They make sure that the product and services meet client expectations.
Statistics
- In the United States, for example, manufacturing makes up 15% of the economic output. (twi-global.com)
- According to a Statista study, U.S. businesses spent $1.63 trillion on logistics in 2019, moving goods from origin to end user through various supply chain network segments. (netsuite.com)
- It's estimated that 10.8% of the U.S. GDP in 2020 was contributed to manufacturing. (investopedia.com)
- (2:04) MTO is a production technique wherein products are customized according to customer specifications, and production only starts after an order is received. (oracle.com)
- Job #1 is delivering the ordered product according to specifications: color, size, brand, and quantity. (netsuite.com)
External Links
How To
How to Use Lean Manufacturing for the Production of Goods
Lean manufacturing is a management style that aims to increase efficiency and reduce waste through continuous improvement. It was developed by Taiichi Okono in Japan, during the 1970s & 1980s. TPS founder Kanji Takoda awarded him the Toyota Production System Award (TPS). Michael L. Watkins published the original book on lean manufacturing, "The Machine That Changed the World," in 1990.
Lean manufacturing is often defined as a set of principles used to improve the quality, speed, and cost of products and services. It emphasizes the elimination of defects and waste throughout the value stream. Lean manufacturing is called just-in-time (JIT), zero defect, total productive maintenance (TPM), or 5S. Lean manufacturing eliminates non-value-added tasks like inspection, rework, waiting.
Lean manufacturing is a way for companies to achieve their goals faster, improve product quality, and lower costs. Lean manufacturing is a great way to manage the entire value chain including customers, suppliers, distributors and retailers as well as employees. Lean manufacturing practices are widespread in many industries. Toyota's philosophy has been a key driver of success in many industries, including automobiles and electronics.
Five basic principles of Lean Manufacturing are included in lean manufacturing
-
Define Value - Determine the value that your business brings to society. Also, identify what sets you apart from your competitors.
-
Reduce waste - Stop any activity that isn't adding value to the supply chains.
-
Create Flow - Ensure work moves smoothly through the process without interruption.
-
Standardize and simplify - Make your processes as consistent as possible.
-
Building Relationships – Establish personal relationships with both external and internal stakeholders.
Lean manufacturing is not a new concept, but it has been gaining popularity over the last few years due to a renewed interest in the economy following the global financial crisis of 2008. To increase their competitiveness, many businesses have turned to lean manufacturing. According to some economists, lean manufacturing could be a significant factor in the economic recovery.
Lean manufacturing is now becoming a common practice in the automotive industry, with many benefits. These include higher customer satisfaction levels, reduced inventory levels as well as lower operating costs.
It can be applied to any aspect of an organisation. Lean manufacturing is most useful in the production sector of an organisation because it ensures that each step in the value-chain is efficient and productive.
There are three main types in lean manufacturing
-
Just-in-Time Manufacturing: Also known as "pull systems", this type of lean manufacturing uses just-in-time manufacturing (JIT). JIT stands for a system where components are assembled on the spot rather than being made in advance. This approach is designed to reduce lead times and increase the availability of components. It also reduces inventory.
-
Zero Defects Manufacturing (ZDM): ZDM focuses on ensuring that no defective units leave the manufacturing facility. It is better to repair a part than have it removed from the production line if it needs to be fixed. This applies to finished products, which may need minor repairs before they are shipped.
-
Continuous Improvement (CI): CI aims to improve the efficiency of operations by continuously identifying problems and making changes in order to eliminate or minimize waste. Continuous Improvement (CI) involves continuous improvement in processes, people, tools, and infrastructure.