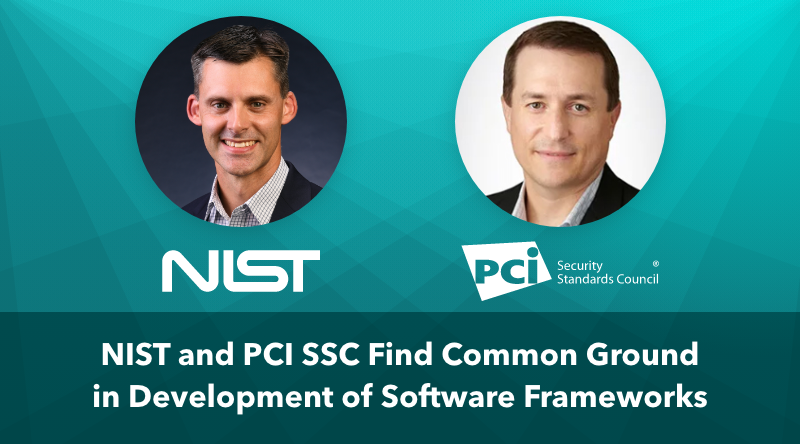
The United States is seeing an increase in manufacturing. The United States is now the third largest country in terms of manufacturing output. The country is now the third-largest manufacturer in the world. Many factors are responsible for this, including automation and productivity growth.
High-Wage America institutes
High-wage, high-paying jobs are part of the High Wage America initiative. Low wages and high levels inequality continue to plague America's economy as it continues to recover slowly from the Great Recession. There are ways to address the low-wage crisis. States and local stakeholders can help improve the working conditions in America by developing an agenda that promotes high-wage work.
The first step is to develop a sustainable manufacturing approach. This will require a plan to address the issues of wage stagnation as well as poor working conditions and a dearth of training. This can only be achieved if the United States fights unfair trade practices. It must also implement policies that help manufacturing communities prosper.
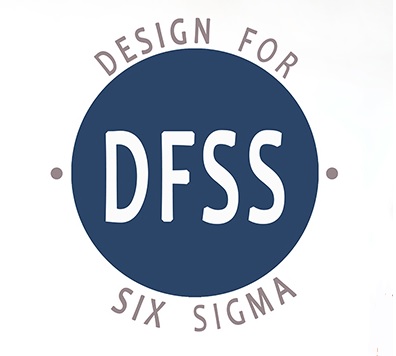
Automation in manufacturing
Automation technologies have transformed the way that we manufacture products, there is no doubt. Automated manufacturing technologies have drastically reduced costs and raised profits for companies and workers. In the US, government policy is making a difference as well, by encouraging the development of new technologies. By encouraging the development new technologies and creating jobs, government policies can actually be beneficial for businesses.
Automated manufacturing started in the US in early 1900s. The Ford Motor Company launched its first auto assembly line. It was the first such line in the world, and significantly improved Ford's production rates. It reduced the time to assemble a car by about one-and-a-half hours from 12 hours.
Productivity growth
Numerous factors are pointing to increased productivity in manufacturing. Many industries have large gaps between the top companies and the rest. This shows that productivity growth is possible. The availability of technology and mobility to move production from one location to another is important, as is increased infrastructure investment. Generally, productivity is measured as output divided by inputs, which are most commonly labor hours. Outputs may be measured in units of production, sales, or both.
Labor productivity is the most common way to measure productivity. This measure measures output and total hours worked. Labor productivity can be broken down according to sector, wage level, technological advancement, or other factors. Productivity growth in the workplace directly impacts corporate profits. Companies that are more efficient in their production processes produce more output per hour of employee labor.
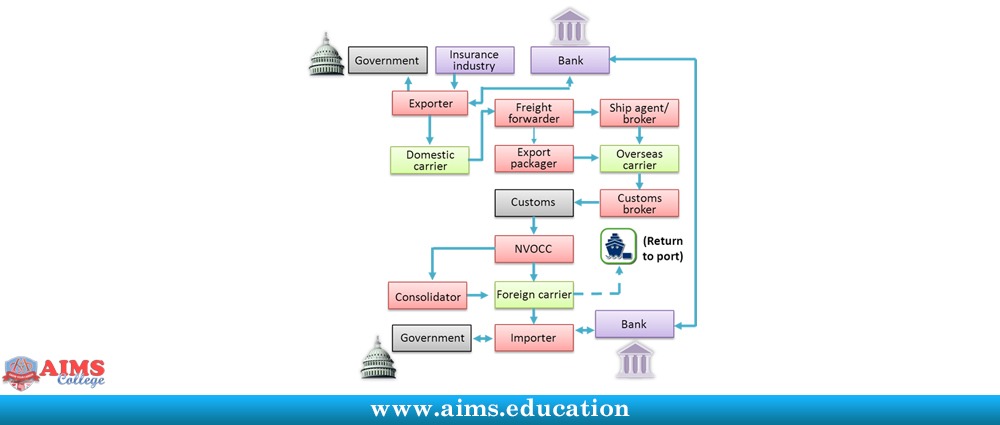
Outsourcing: The Impact
There are multiple ways that outsourcing can impact manufacturing in the United States. It can be a positive thing in some cases. This allows the country to compete against other countries with lower labor costs. In some cases, outsourcing can cause American jobs to be lost. In some cases, it can cause American jobs to be replaced by foreign workers, while in other cases, it can result in lower wages for American workers.
Outsourcing began with American companies. It then spread to other countries. In order to cut costs, some companies decided to eliminate all of their "core" activities. Sodexo which provides food services, IBM, and UPS were just a few examples. Companies like Foxconn, which manufactures computers, also started outsourcing. Apple is just one of many companies that outsource their entire manufacturing.
FAQ
What's the difference between Production Planning & Scheduling?
Production Planning (PP), is the process of deciding what production needs to take place at any given time. Forecasting demand is one way to do this.
Scheduling refers the process by which tasks are assigned dates so that they can all be completed within the given timeframe.
How can manufacturing overproduction be reduced?
It is essential to find better ways to manage inventory to reduce overproduction. This would decrease the time that is spent on inefficient activities like purchasing, storing, or maintaining excess stock. By doing this, we could free up resources for other productive tasks.
One way to do this is to adopt a Kanban system. A Kanban Board is a visual display that tracks work progress. Kanban systems allow work items to move through different states until they reach their final destination. Each state has a different priority level.
If work is moving from one stage to the other, then the current task can be completed and moved on to the next. However, if a task is still at the beginning stages, it will remain so until it reaches the end of the process.
This allows work to move forward and ensures that no work is missed. Managers can see how much work has been done and the status of each task at any time with a Kanban Board. This information allows managers to adjust their workflow based off real-time data.
Another way to control inventory levels is to implement lean manufacturing. Lean manufacturing seeks to eliminate waste from every step of the production cycle. Anything that doesn't add value to the product is considered waste. Here are some examples of common types.
-
Overproduction
-
Inventory
-
Packaging not required
-
Material surplus
These ideas can help manufacturers improve efficiency and reduce costs.
What types of jobs can you find in logistics
There are many jobs available in logistics. Some examples are:
-
Warehouse workers – They load and unload pallets and trucks.
-
Transportation drivers: They drive trucks and trailers and deliver goods and make pick-ups.
-
Freight handlers – They sort and package freight at warehouses.
-
Inventory managers: They are responsible for the inventory and management of warehouses.
-
Sales representatives - They sell products.
-
Logistics coordinators are responsible for organizing and planning logistics operations.
-
Purchasing agents – They buy goods or services necessary to run a company.
-
Customer service representatives - They answer calls and emails from customers.
-
Ship clerks - They issue bills and process shipping orders.
-
Order fillers - These people fill orders based on what has been ordered.
-
Quality control inspectors - They check incoming and outgoing products for defects.
-
Others - There are many types of jobs in logistics such as transport supervisors and cargo specialists.
What are the logistics products?
Logistics involves the transportation of goods from point A and point B.
These include all aspects related to transport such as packaging, loading and transporting, storing, transporting, unloading and warehousing inventory management, customer service. Distribution, returns, recycling are some of the options.
Logisticians ensure that the right product reaches the right place at the right time and under safe conditions. Logisticians help companies improve their supply chain efficiency by providing information about demand forecasts and stock levels, production schedules, as well as availability of raw materials.
They monitor shipments in transit, ensure quality standards, manage inventories, replenish orders, coordinate with suppliers and other vendors, and offer support services for sales, marketing, and customer service.
Statistics
- According to the United Nations Industrial Development Organization (UNIDO), China is the top manufacturer worldwide by 2019 output, producing 28.7% of the total global manufacturing output, followed by the United States, Japan, Germany, and India.[52][53] (en.wikipedia.org)
- In the United States, for example, manufacturing makes up 15% of the economic output. (twi-global.com)
- [54][55] These are the top 50 countries by the total value of manufacturing output in US dollars for its noted year according to World Bank.[56] (en.wikipedia.org)
- (2:04) MTO is a production technique wherein products are customized according to customer specifications, and production only starts after an order is received. (oracle.com)
- In 2021, an estimated 12.1 million Americans work in the manufacturing sector.6 (investopedia.com)
External Links
How To
Six Sigma in Manufacturing
Six Sigma can be described as "the use of statistical process control (SPC), techniques to achieve continuous improvement." It was developed by Motorola's Quality Improvement Department at their plant in Tokyo, Japan, in 1986. Six Sigma's basic concept is to improve quality and eliminate defects through standardization. Since there are no perfect products, or services, this approach has been adopted by many companies over the years. Six Sigma's primary goal is to reduce variation from the average value of production. It is possible to measure the performance of your product against an average and find the percentage of time that it differs from the norm. If it is too large, it means that there are problems.
The first step toward implementing Six Sigma is understanding how variability works in your business. Once you have a good understanding of the basics, you can identify potential sources of variation. These variations can also be classified as random or systematic. Random variations occur when people make mistakes; systematic ones are caused by factors outside the process itself. Random variations would include, for example, the failure of some widgets to fall from the assembly line. But if you notice that every widget you make falls apart at the exact same place each time, this would indicate that there is a problem.
Once you have identified the problem, you can design solutions. You might need to change the way you work or completely redesign the process. To verify that the changes have worked, you need to test them again. If they don’t work, you’ll need to go back and rework the plan.