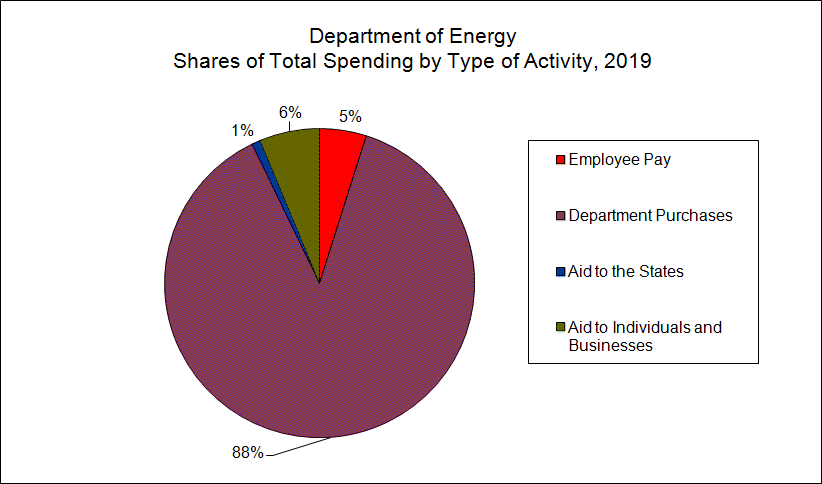
Despite the many benefits of lean manufacturing, there have been some challenges for companies trying to implement this strategy. Companies must develop a plan to overcome these challenges. Companies that have implemented Lean have found that there are three main issues that are responsible for limiting the success of the initiative.
Regardless of the size of a corporation, a commitment to lean manufacturing is critical to its success. It is difficult to say how committed a company will be to lean implementation, but it is critical that managers educate employees about the changes to corporate culture.
Also, it is important to make sure that resources are properly allocated. Many public agencies have discovered that they waste budgets on items not needed. Managers have been reported to buy equipment they don't need in order to save money. This can lead to operational bottlenecks and inefficient implementation of lean manufacturing.
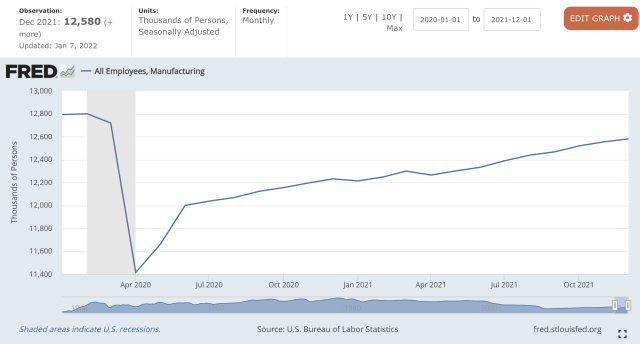
Resistance to cultural changes is one of the biggest obstacles in lean manufacturing. Many employees, especially those who have been with the company a long time, don't like change. Some employees will wait for the majority to speak up and convince them to move in a new direction. In order to break through this resistance, management must communicate the benefits of the program and explain why the change is necessary.
The lack of a plan for strategic transformation is another significant problem. Although companies often manage multiple business operations at once it is essential to develop a long-term strategy. This strategy allows companies identify and mentor future leaders, keep them competitive and improve operations. It can also help identify and resolve operational bottlenecks as well as identify growth opportunities.
This is not all. Training is essential to overcome resistance. Training is essential to help workers understand their roles and expectations. This training helps workers acquire multi skills that can be used to help them work independently. Training also helps workers develop problem solving skills, which helps them sustain Lean through improvements in performance.
To overcome resistance, management needs to engage with workers frequently. Managers may put pressure on workers to follow instructions, but managers need to be open and honest with workers about why the change is needed. Sometimes, managers gave incorrect instructions to workers, leading to ineffective implementation.
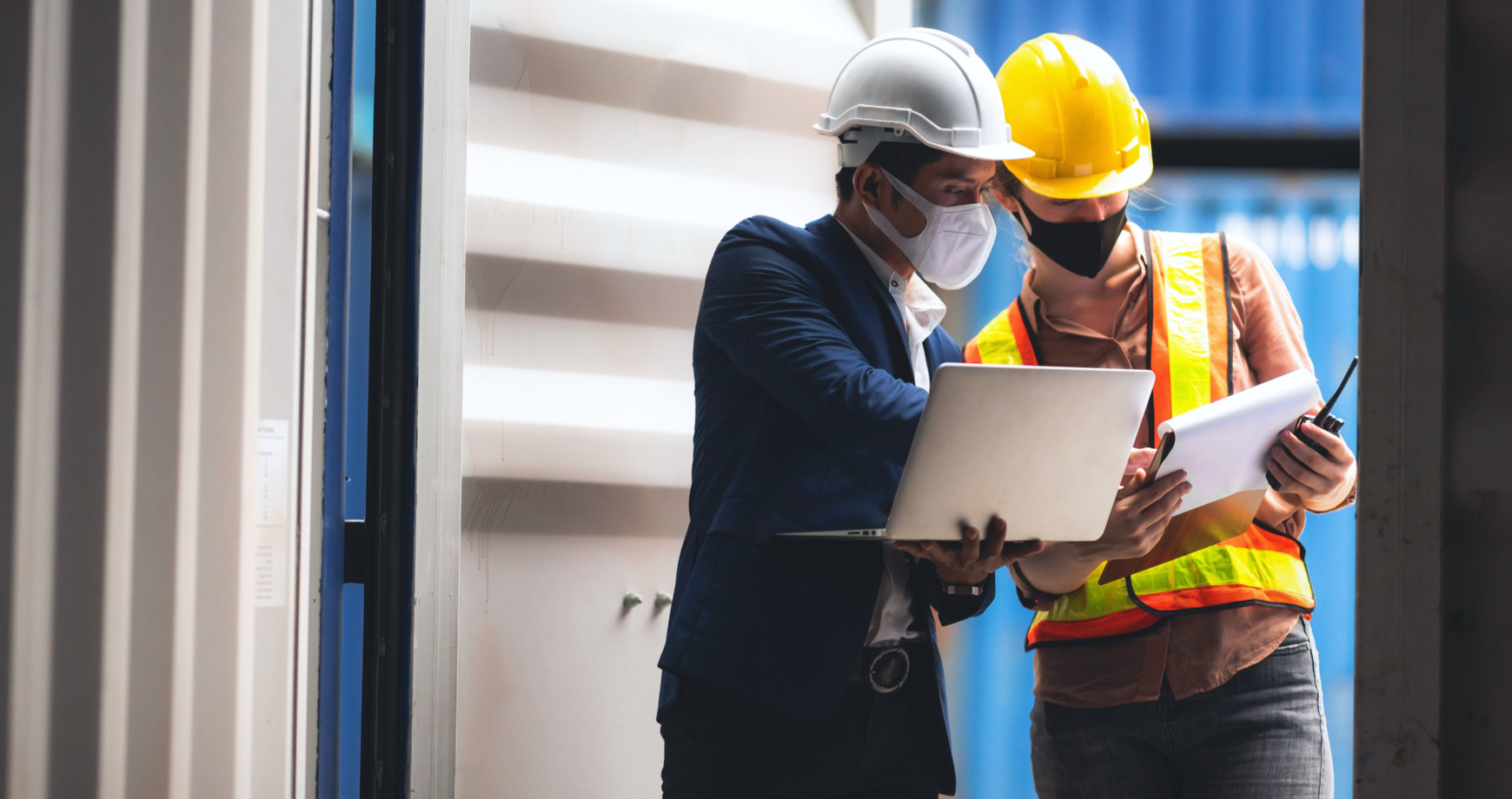
Regardless of the size of he company, managers must be involved on the shop floor, allowing them to identify the areas where changes can be made. They also need to develop structured training modules and acquaint staff with the introduction of new digital work tools. These tools such as 5S improve visual management.
It is crucial to communicate and develop a clear vision of how lean manufacturing will be implemented. This vision should outline the responsibilities of employees and include a schedule to implement lean. It also includes a method for measuring success.
FAQ
How can manufacturing prevent production bottlenecks?
To avoid production bottlenecks, ensure that all processes run smoothly from the moment you receive your order to the time the product ships.
This includes both planning for capacity and quality control.
The best way to do this is to use continuous improvement techniques such as Six Sigma.
Six Sigma management is a system that improves quality and reduces waste within your organization.
It emphasizes consistency and eliminating variance in your work.
Why is logistics important in manufacturing?
Logistics are essential to any business. Logistics can help you achieve amazing results by helping to manage product flow from raw materials to finished products.
Logistics also play a major role in reducing costs and increasing efficiency.
What are the responsibilities of a manufacturing manager
A manufacturing manager has to ensure that all manufacturing processes work efficiently and effectively. They should be alert for any potential problems in the company and react accordingly.
They should also be able communicate with other departments, such as sales or marketing.
They should also be aware of the latest trends in their industry and be able to use this information to help improve productivity and efficiency.
Is it possible to automate certain parts of manufacturing
Yes! Yes! Automation has existed since ancient times. The Egyptians discovered the wheel thousands and years ago. We now use robots to help us with assembly lines.
There are many uses of robotics today in manufacturing. These include:
-
Line robots
-
Robot welding
-
Robot painting
-
Robotics inspection
-
Robots create products
Manufacturing can also be automated in many other ways. 3D printing is a way to make custom products quickly and without waiting weeks or months for them to be manufactured.
What kind of jobs are there in logistics?
There are different kinds of jobs available in logistics. Some of them are:
-
Warehouse workers - They load trucks and pallets.
-
Transportation drivers - They drive trucks and trailers to deliver goods and carry out pick-ups.
-
Freight handlers - They sort and pack freight in warehouses.
-
Inventory managers – These people oversee inventory at warehouses.
-
Sales reps - They sell products and services to customers.
-
Logistics coordinators - They plan and organize logistics operations.
-
Purchasing agents are those who purchase goods and services for the company.
-
Customer service representatives are available to answer customer calls and emails.
-
Ship clerks - They issue bills and process shipping orders.
-
Order fillers - These people fill orders based on what has been ordered.
-
Quality control inspectors: They inspect outgoing and incoming products for any defects.
-
Others - There is a variety of other jobs in logistics. These include transportation supervisors and cargo specialists.
What skills should a production planner have?
Being a production planner is not easy. You need to be organized and flexible. Also, you must be able and willing to communicate with clients and coworkers.
How can we improve manufacturing efficiency?
The first step is to identify the most important factors affecting production time. Next, we must find ways to improve those factors. If you don't know where to start, then think about which factor(s) have the biggest impact on production time. Once you have identified them, it is time to identify solutions.
Statistics
- It's estimated that 10.8% of the U.S. GDP in 2020 was contributed to manufacturing. (investopedia.com)
- According to a Statista study, U.S. businesses spent $1.63 trillion on logistics in 2019, moving goods from origin to end user through various supply chain network segments. (netsuite.com)
- (2:04) MTO is a production technique wherein products are customized according to customer specifications, and production only starts after an order is received. (oracle.com)
- Job #1 is delivering the ordered product according to specifications: color, size, brand, and quantity. (netsuite.com)
- You can multiply the result by 100 to get the total percent of monthly overhead. (investopedia.com)
External Links
How To
How to use the Just In-Time Production Method
Just-in-time is a way to cut costs and increase efficiency in business processes. It allows you to get the right amount resources at the right time. This means that your only pay for the resources you actually use. Frederick Taylor was the first to coin this term. He developed it while working as a foreman during the early 1900s. Taylor observed that overtime was paid to workers if they were late in working. He decided that workers would be more productive if they had enough time to complete their work before they started to work.
The idea behind JIT is that you should plan ahead and have everything ready so you don't waste money. Look at your entire project, from start to end. Make sure you have enough resources in place to deal with any unexpected problems. You will have the resources and people to solve any problems you anticipate. This way, you won't end up paying extra money for things that weren't really necessary.
There are many JIT methods.
-
Demand-driven: This type of JIT allows you to order the parts/materials required for your project on a regular basis. This will allow to track how much material has been used up. You'll also be able to estimate how long it will take to produce more.
-
Inventory-based: You stock materials in advance to make your projects easier. This allows you to predict how much you can expect to sell.
-
Project-driven: This is an approach where you set aside enough funds to cover the cost of your project. Knowing how much money you have available will help you purchase the correct amount of materials.
-
Resource-based JIT is the most widespread form. Here, you allocate certain resources based on demand. You might assign more people to help with orders if there are many. If there aren't many orders, you will assign fewer people.
-
Cost-based : This is similar in concept to resource-based. But here, you aren't concerned about how many people your company has but how much each individual costs.
-
Price-based pricing: This is similar in concept to cost-based but instead you look at how much each worker costs, it looks at the overall company's price.
-
Material-based: This is quite similar to cost-based, but instead of looking at the total cost of the company, you're concerned with how much raw materials you spend on average.
-
Time-based JIT: This is another variant of resource-based JIT. Instead of focusing solely on the amount each employee costs, focus on how long it takes for the project to be completed.
-
Quality-based: This is yet another variation of resource-based JIT. Instead of thinking about how much each employee costs or how long it takes to manufacture something, you think about how good the quality of your product is.
-
Value-based JIT: This is the latest form of JIT. This is where you don't care about how the products perform or whether they meet customers' expectations. Instead, you're focused on how much value you add to the market.
-
Stock-based is an inventory-based system that measures the number of items produced at any given moment. This method is useful when you want to increase production while decreasing inventory.
-
Just-in-time planning (JIT): This is a combination JIT and supply-chain management. It's the process of scheduling delivery of components immediately after they are ordered. It's important because it reduces lead times and increases throughput.