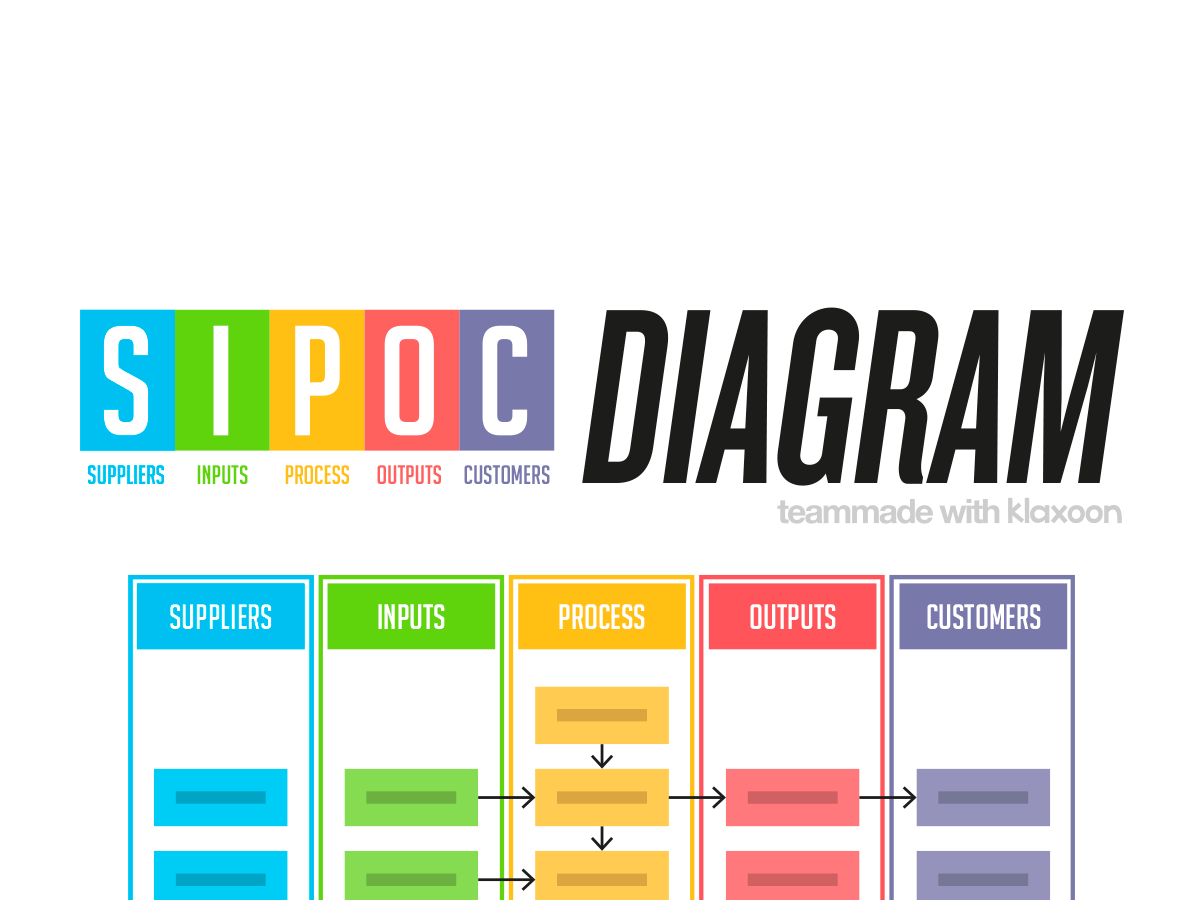
With a projected 5% growth in the number of logistics professionals between 2018-2028, there are many career options. Find out more about the duties and education required to become a logistics professional. These are just the basics to know before you apply for a logistic job. These questions will make it easier for you to get started on your career. These are examples of the jobs and salaries of logistics professionals. Want to become a logistics professional yourself?
Between 2018 and 2028, the number of logistics jobs will increase by 5%
Globalization is increasing in importance, which means that logisticians worldwide are increasingly needed. Companies require the right products at a right price and at the correct time. Logistics professionals can help them achieve that goal. Businesses require specialists, managers and coordinators in this field. The Kangan Institute lists 5 reasons why you might be a good fit for a logistic career. The logistics sector is extremely stable and offers high levels security and certainty.
Logistics professionals oversee the entire product lifecycle and work closely with multiple stakeholders. They use software to plan and coordinate the movement of products from point of purchase to final distribution. According to the Bureau of Labor Statistics (BoLS), the demand for logistics professionals will increase by 5% over ten years. In the meantime, purchasing managers are responsible for more complex procurement tasks. Logistics jobs are highly desired.
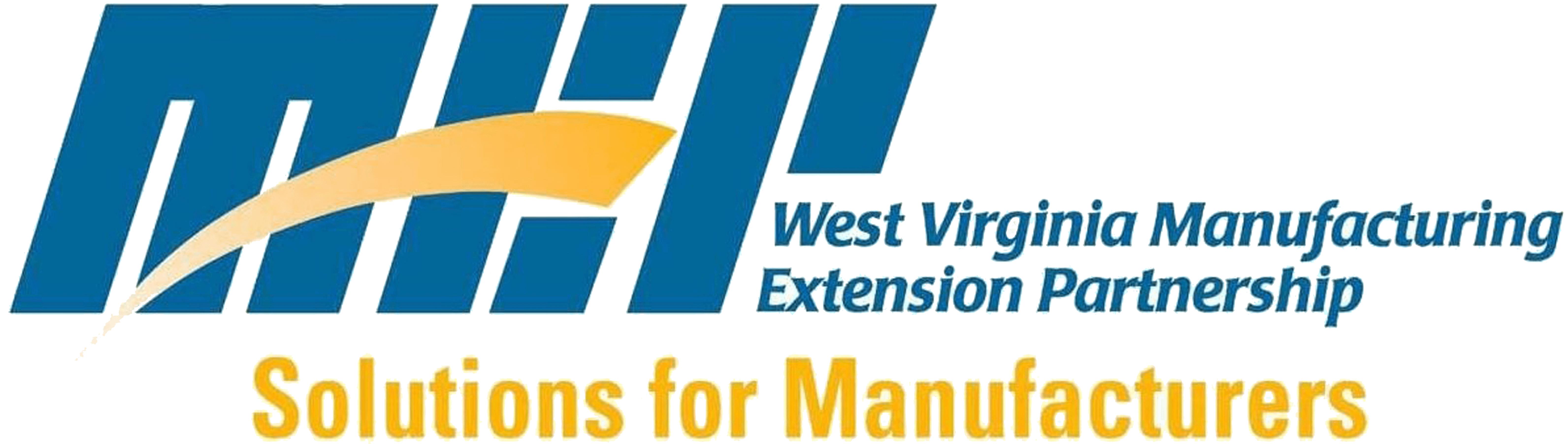
Duties of a logistics professional
You will need a degree and at least two years of experience to be a logistics manger. This position requires a strong understanding of inventory management software as well as analytical skills. The ideal candidate should be organized, have strong communication skills and verbal and/or written communication skills. The logistics manager is responsible for tracking shipments and evaluating metrics. Interacting with employees from other departments is another part of the duties of a logistics professional.
A logistics manager is responsible for managing the entire supply chain in some companies. This includes purchasing, warehousing and transportation as well as distribution and customer service. They are responsible for planning and implementing the logistics system, overseeing the daily operations of distribution centers and ensuring that costs, productivity, and accuracy goals are met. Additionally, they are responsible for establishing supply chain-based performance measurement systems and training shipping department personnel. They might also assist in the selection of carriers and take part in negotiations concerning sustainability or efficiency in supply chain management.
For a logistics professional, the salary is
If you're passionate and interested in helping organizations bring products to the market efficiently, then a career working in logistics would be a good choice. This field entails managing the entire product lifecycle, from design to market, as well as the allocation of materials and transportation plans. According to BLS data, a logistics professional can earn an average annual salary of $76,270. Logistics professionals have a bright future. According to the BLS, there will be an increase in jobs by 30% by the end of this decade.
While your first paycheck as a logistics professional may not be reason for celebration, you will see your earnings increase as you learn more and have better skills. Many logistics managers plan, direct, monitor and manage the distribution of products. Additionally, they oversee financial transactions. According to a recent survey, the salary for logistics managers in the District of Columbia is the highest in the nation. You can find salary information by zip code, state, or even company.
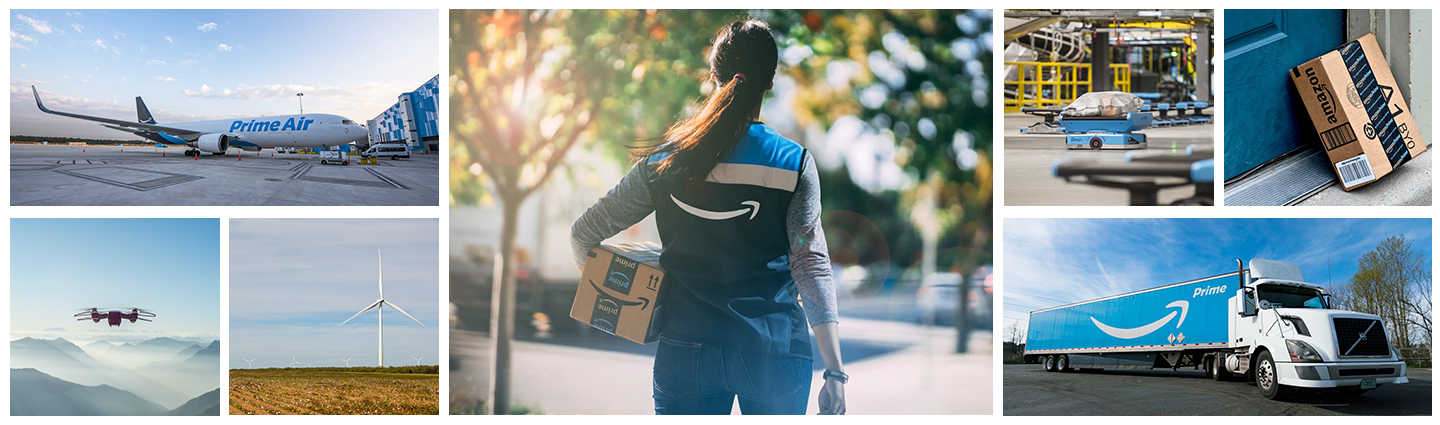
You need to be educated in order to become a logistics professional
There are many reasons you might want to be a logistician. They ensure smooth operations of companies and organizations. Unfortunately, the logistics field is losing its spotlight as the Baby Boomers begin to enter retirement. This lack of exposure could actually be in the favor of this field. After all, most people are aware of opportunities in fields like accounting, law, and nursing, but not many are aware of the logistics field.
A bachelor's degree in logistics requires 60 credits. The program is completed in two years. This course covers concepts such as supply chain management and logistics. After graduation, you may work in a logistics company.
FAQ
What is the responsibility of a production planner?
Production planners make sure that every aspect of the project is delivered on-time, within budget, and within schedule. They also ensure the quality of the product and service meets the client's requirements.
How can we reduce manufacturing overproduction?
Improved inventory management is the key to reducing overproduction. This would reduce the amount of time spent on unnecessary activities such as purchasing, storing, and maintaining excess stock. This would allow us to use our resources for more productive tasks.
One way to do this is to adopt a Kanban system. A Kanban board, a visual display to show the progress of work, is called a Kanban board. Work items are moved through various states to reach their destination in a Kanban system. Each state has a different priority level.
When work is completed, it can be transferred to the next stage. But if a task remains in the beginning stages it will stay that way until it reaches its end.
This allows work to move forward and ensures that no work is missed. Managers can view the Kanban board to see how much work they have done. This information allows managers to adjust their workflow based off real-time data.
Another way to control inventory levels is to implement lean manufacturing. Lean manufacturing works to eliminate waste throughout every stage of the production chain. Anything that doesn't add value to the product is considered waste. The following are examples of common waste types:
-
Overproduction
-
Inventory
-
Unnecessary packaging
-
Excess materials
Manufacturers can increase efficiency and decrease costs by implementing these ideas.
What does manufacturing mean?
Manufacturing Industries refers to businesses that manufacture products. Consumers are the people who purchase these products. These companies use various processes such as production, distribution, retailing, management, etc., to fulfill this purpose. They manufacture goods from raw materials using machines and other equipment. This includes all types if manufactured goods.
Statistics
- You can multiply the result by 100 to get the total percent of monthly overhead. (investopedia.com)
- [54][55] These are the top 50 countries by the total value of manufacturing output in US dollars for its noted year according to World Bank.[56] (en.wikipedia.org)
- Job #1 is delivering the ordered product according to specifications: color, size, brand, and quantity. (netsuite.com)
- In the United States, for example, manufacturing makes up 15% of the economic output. (twi-global.com)
- According to a Statista study, U.S. businesses spent $1.63 trillion on logistics in 2019, moving goods from origin to end user through various supply chain network segments. (netsuite.com)
External Links
How To
How to Use 5S for Increasing Productivity in Manufacturing
5S stands for "Sort", 'Set In Order", 'Standardize', & Separate>. Toyota Motor Corporation invented the 5S strategy in 1954. This methodology helps companies improve their work environment to increase efficiency.
This method has the basic goal of standardizing production processes to make them repeatable. This means that tasks such as cleaning, sorting, storing, packing, and labeling are performed daily. This knowledge allows workers to be more efficient in their work because they are aware of what to expect.
There are five steps to implementing 5S, including Sort, Set In Order, Standardize, Separate and Store. Each step is a different action that leads to greater efficiency. By sorting, for example, you make it easy to find the items later. Once you have placed items in an ordered fashion, you will put them together. You then organize your inventory in groups. Finally, when you label your containers, you ensure everything is labeled correctly.
This requires employees to critically evaluate how they work. Employees need to understand the reasons they do certain jobs and determine if there is a better way. They will need to develop new skills and techniques in order for the 5S system to be implemented.
The 5S method increases efficiency and morale among employees. They feel more motivated to work towards achieving greater efficiency as they see the results.