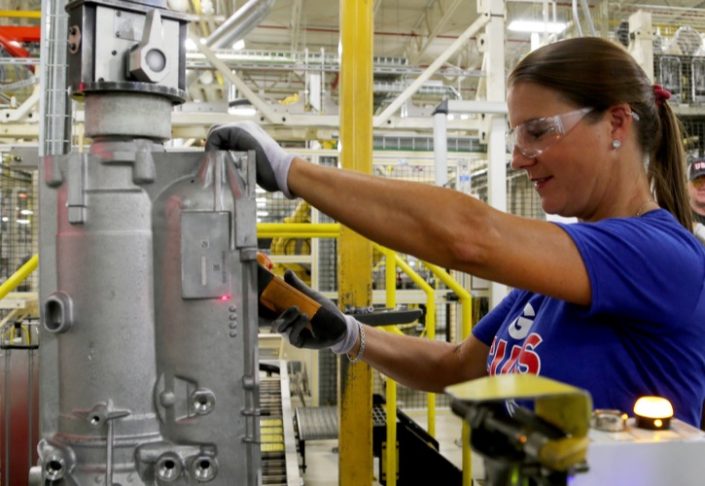
Compared to other professions, structural engineers enjoy one of the highest salaries. The demand for structural engineers affects their salary. A bachelor's degree is usually required for structural engineers. A minimum of a few year's experience in the industry is required. They might work in a construction firm, utility establishment or engineering consulting company. Some structural engineers may even set up their own company.
Structural Engineers design structures that can withstand severe stresses. They should also know the properties different materials. They might also be required to work on bid projects. They must have communication and project management skills. They also need to be well-trained in computer software. They may be required to work overtime in order meet deadlines. They may also be able to travel for clients projects that are not in their immediate area.
Most structural engineers work full time. But they can also work nights and weekends. They will have the option to drive company vehicles and be covered by extended health care benefits. They may also participate in an employee share ownership plan. The salary of a structural engineer can be increased by changing employers and obtaining an advanced degree. The annual salary of structural engineers is between $59,000 and $108,000.
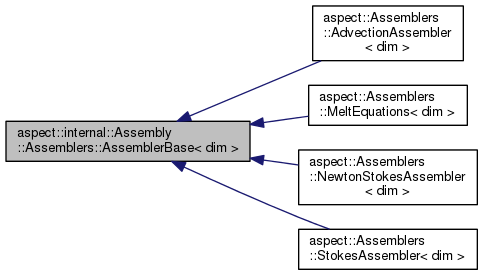
The salaries of structural engineers in the United States vary from one city to another. San Francisco structural engineers earn an average of $147.822 per year. District of Columbia is home to the second highest salary, at $146.683. Deer Park, CA has the third highest average salary at $111,562.
The average salary for a structures engineer in Oslo, Norway is kr 765 026 per year. However, the average salary for structural engineers in Oslo is 8% less than in Norway. The cost of living is also related to the salary of structural engineers.
Structure engineers usually work Monday through Friday between 9:00 am and 5:00 pm. They can work nights, weekends and holidays. They may also visit construction sites to observe the progress. They will need communication skills to communicate the designs to their clients. They also need to be able to use computer-aided design (CAD) software to visualize their finished parts.
As an assistant to an engineer, a structural engineer may also be employed. He or she must complete supervised training before they are able to work alone. Structural engineers can also gain certification through an apprenticeship program. They must have at minimum four years experience in the field. Once they have acquired sufficient experience, they can begin applying directly to employers.
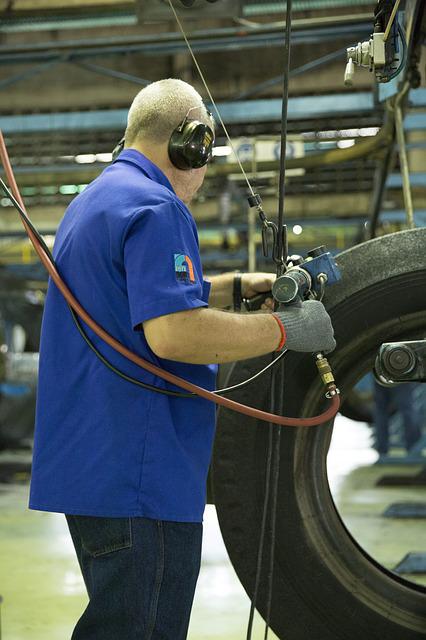
Most structural engineers make $42 an hour. You can earn more if your work is harder and you gain experience as a structural engineering engineer. Senior structural engineers have the highest salaries. The Institution of StructE recognizes excellence in this field and you can become a member.
A structural engineer's total compensation includes salary, bonus and profit sharing. The average bonus is $2,179
FAQ
What are the responsibilities of a manufacturing manager
The manufacturing manager should ensure that every manufacturing process is efficient and effective. They should also be aware and responsive to any company problems.
They should also be able and comfortable communicating with other departments like sales and marketing.
They must also keep up-to-date with the latest trends in their field and be able use this information to improve productivity and efficiency.
What are the main products of logistics?
Logistics is the process of moving goods from one point to another.
They encompass all aspects transport, including packaging and loading, transporting, storage, unloading.
Logisticians ensure that the product is delivered to the correct place, at the right time, and under safe conditions. Logisticians assist companies in managing their supply chains by providing information such as demand forecasts, stock levels and production schedules.
They also keep track of shipments in transit, monitor quality standards, perform inventories and order replenishment, coordinate with suppliers and vendors, and provide support services for sales and marketing.
Is it possible to automate certain parts of manufacturing
Yes! Since ancient times, automation has been in existence. The Egyptians invent the wheel thousands of year ago. Nowadays, we use robots for assembly lines.
There are many applications for robotics in manufacturing today. These include:
-
Line robots
-
Robot welding
-
Robot painting
-
Robotics inspection
-
Robots that create products
Manufacturing can also be automated in many other ways. For example, 3D printing allows us to make custom products without having to wait for weeks or months to get them manufactured.
Is automation necessary in manufacturing?
Automation is important not only for manufacturers but also for service providers. It allows them provide faster and more efficient services. It also helps to reduce costs and improve productivity.
How can manufacturing efficiency improved?
The first step is to identify the most important factors affecting production time. We then need to figure out how to improve these variables. If you don’t know where to begin, consider which factors have the largest impact on production times. Once you identify them, look for solutions.
What are the 4 types of manufacturing?
Manufacturing is the process that transforms raw materials into useful products. It can involve many activities like designing, manufacturing, testing packaging, shipping, selling and servicing.
Statistics
- According to a Statista study, U.S. businesses spent $1.63 trillion on logistics in 2019, moving goods from origin to end user through various supply chain network segments. (netsuite.com)
- [54][55] These are the top 50 countries by the total value of manufacturing output in US dollars for its noted year according to World Bank.[56] (en.wikipedia.org)
- In the United States, for example, manufacturing makes up 15% of the economic output. (twi-global.com)
- You can multiply the result by 100 to get the total percent of monthly overhead. (investopedia.com)
- Job #1 is delivering the ordered product according to specifications: color, size, brand, and quantity. (netsuite.com)
External Links
How To
How to Use Just-In-Time Production
Just-in-time is a way to cut costs and increase efficiency in business processes. It is a process where you get the right amount of resources at the right moment when they are needed. This means that you only pay for what you actually use. Frederick Taylor was the first to coin this term. He developed it while working as a foreman during the early 1900s. He noticed that workers were often paid overtime when they had to work late. He concluded that if workers were given enough time before they start work, productivity would increase.
JIT is about planning ahead. You should have all the necessary resources ready to go so that you don’t waste money. Look at your entire project, from start to end. Make sure you have enough resources in place to deal with any unexpected problems. You can anticipate problems and have enough equipment and people available to fix them. This will prevent you from spending extra money on unnecessary things.
There are different types of JIT methods:
-
Demand-driven: This type of JIT allows you to order the parts/materials required for your project on a regular basis. This will let you track the amount of material left over after you've used it. You'll also be able to estimate how long it will take to produce more.
-
Inventory-based: This allows you to store the materials necessary for your projects in advance. This allows one to predict how much they will sell.
-
Project-driven: This method allows you to set aside enough funds for your project. You will be able to purchase the right amount of materials if you know what you need.
-
Resource-based JIT: This type of JIT is most commonly used. Here you can allocate certain resources based purely on demand. You might assign more people to help with orders if there are many. You'll have fewer orders if you have fewer.
-
Cost-based: This approach is very similar to resource-based. However, you don't just care about the number of people you have; you also need to consider how much each person will cost.
-
Price-based: This approach is very similar to the cost-based method except that you don't look at individual workers costs but the total cost of the company.
-
Material-based - This is a variant of cost-based. But instead of looking at the total company cost, you focus on how much raw material you spend per year.
-
Time-based: Another variation of resource-based JIT. Instead of focusing on the cost of each employee, you will focus on the time it takes to complete a project.
-
Quality-based JIT is another variant of resource-based JIT. Instead of thinking about the cost of each employee or the time it takes to produce something, you focus on how good your product quality.
-
Value-based JIT : This is the newest type of JIT. This is where you don't care about how the products perform or whether they meet customers' expectations. Instead, you focus on the added value that you provide to your market.
-
Stock-based: This inventory-based approach focuses on how many items are being produced at any one time. This method is useful when you want to increase production while decreasing inventory.
-
Just-in time (JIT), planning: This is a combination JIT/supply chain management. It is the process of scheduling components' delivery as soon as they have been ordered. It's important because it reduces lead times and increases throughput.