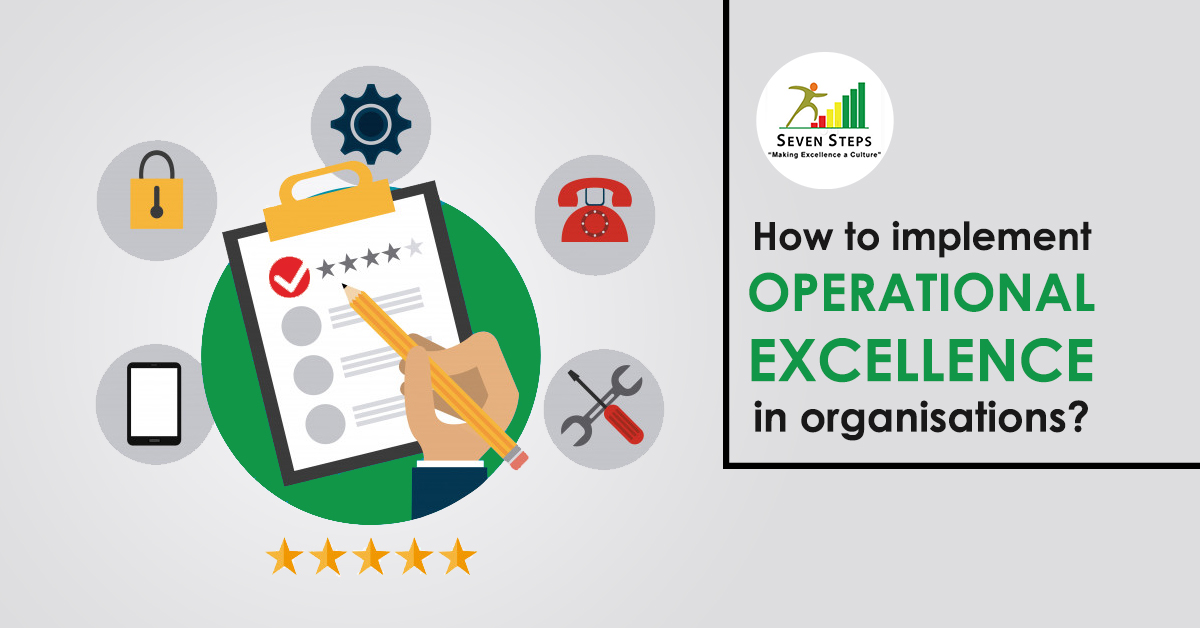
The manufacturing industry is in rapid change. This requires new skillsets and cutting-edge experience. The factory of tomorrow will be digital and flexible, efficient, responsible, and accountable. Manufacturing processes and energy consumption must be optimized, robots and cobotics developed, and traceability must be maintained. A manufacturing engineer will be at the forefront of this change. Here are three areas where you need to excel. This article will discuss these skills and how they can impact the future direction of your industry.
Analyst perspectives
Analyst perspectives are crucial for understanding industry trends and assessing industry's competitive dynamics. These insights are a great way to understand the changing consumer landscape. This includes attitudes and intentions as much as buying behavior. NPD's annual survey provides a comprehensive view of the industry’s outlook. Each country has its own forecasted categories. This chapter examines the role played by industry analysts in validating and generating market-based knowledge.
Consumer survey data
Prosper's consumer survey data is based upon responses from more than seven thousand adults in the United States each month. It is trended and correlated, and includes questions about consumers' emotional state, future plans, and purchasing habits. It also contains monthly data from hundreds of major brands and retailers over the last 18 years. It provides the most accurate way to determine the attitudes and spending habits of consumers within a market. For marketers and business owners, the data from consumer surveys is invaluable.
Patterns of industry growth
This chapter focuses on the growth patterns of industries and firms. The development of financial markets in developed countries affects the speed of industry growth. Finance-hungry areas grow faster in countries where there are financial markets. Conversely, sectors that depend on external financing grow faster after periods with high stock market performance. These trends are consistent with theories of trade and development, which suggests that a country’s product mix is a reflection of its economic stage. We discuss the major trends that influence industry growth.
Automation
According to Gartner, automation will affect nearly every occupation within the next decade. While only five percent of occupations can be fully automated by currently demonstrated technologies, many more have constituent activities that could be automated. Ultimately, most occupations will be affected in some way, and the nature of these jobs will likely change. Whether they remain human or change will depend on the individual workplace. Here are five possible ways automation could impact the manufacturing industry.
Hybrid work environment
Employers need to listen to employees' feedback and offer many options for sharing it. This will help them create a hybrid workplace. This valuable information can be collected through surveys, focus groups, or one-on-1 conversations. Employees can be given performance incentives, such as financial rewards, food delivery, or tokens expressing appreciation. Companies can create positive employee experiences by listening to their employees.
Streaming media
The streaming media industry is a relatively new business model and its future looks uncertain. Many media conglomerates are now selling short-term streaming rights to three services. Although streaming was a small market at first, it is now a booming industry that is poised to surpass linear television as the leading viewing option in the next few years. In 2025, almost every production of the four media conglomerates should only be available through their streaming services.
Automotive industry
What are the prospects for the Automotive Industry's future? Many experts believe that it will slowly start to recover in the next decade. Automakers face many challenges right now. But, connected vehicles and other technologies could offer new income streams. Governments can help by changing emission laws and automotive companies can create more resilient supply chains and intensify R&D programs. There are many reasons why Automotive could begin to recover slowly over coming decades.
FAQ
What is the difference in Production Planning and Scheduling, you ask?
Production Planning (PP), is the process of deciding what production needs to take place at any given time. Forecasting demand is one way to do this.
Scheduling refers to the process of allocating specific dates to tasks in order that they can be completed within a specified timeframe.
How can I find out more about manufacturing?
You can learn the most about manufacturing by getting involved in it. But if that is not possible you can always read books and watch educational videos.
What are the responsibilities of a logistic manager?
Logistics managers ensure that goods arrive on time and are unharmed. This is accomplished by using the experience and knowledge gained from working with company products. He/she should make sure that enough stock is on hand to meet the demands.
Why is logistics important in manufacturing
Logistics are an essential part of any business. They help you achieve great results by helping you manage all aspects of product flow, from raw materials to finished goods.
Logistics plays a significant role in reducing cost and increasing efficiency.
What kind of jobs are there in logistics?
There are many types of jobs in logistics. Some examples are:
-
Warehouse workers – They load, unload and transport pallets and trucks.
-
Transportation drivers - They drive trucks and trailers to deliver goods and carry out pick-ups.
-
Freight handlers - They sort and pack freight in warehouses.
-
Inventory managers – They manage the inventory in warehouses.
-
Sales reps - They sell products and services to customers.
-
Logistics coordinators - They plan and organize logistics operations.
-
Purchasing agents - They purchase goods and services needed for company operations.
-
Customer service representatives – They answer emails and phone calls from customers.
-
Shippers clerks - They process shipping order and issue bills.
-
Order fillers – They fill orders based upon what was ordered and shipped.
-
Quality control inspectors are responsible for inspecting incoming and outgoing products looking for defects.
-
Others - There are many types of jobs in logistics such as transport supervisors and cargo specialists.
Is automation necessary in manufacturing?
Automating is not just important for manufacturers, but also for service providers. It allows them provide faster and more efficient services. It helps them to lower costs by reducing human errors, and improving productivity.
Statistics
- [54][55] These are the top 50 countries by the total value of manufacturing output in US dollars for its noted year according to World Bank.[56] (en.wikipedia.org)
- Many factories witnessed a 30% increase in output due to the shift to electric motors. (en.wikipedia.org)
- It's estimated that 10.8% of the U.S. GDP in 2020 was contributed to manufacturing. (investopedia.com)
- (2:04) MTO is a production technique wherein products are customized according to customer specifications, and production only starts after an order is received. (oracle.com)
- Job #1 is delivering the ordered product according to specifications: color, size, brand, and quantity. (netsuite.com)
External Links
How To
How to Use Lean Manufacturing in the Production of Goods
Lean manufacturing is an approach to management that aims for efficiency and waste reduction. It was created in Japan by Taiichi Ohno during the 1970s and 80s. He received the Toyota Production System award (TPS), from Kanji Toyoda, founder of TPS. Michael L. Watkins published the first book on lean manufacturing in 1990.
Lean manufacturing is often defined as a set of principles used to improve the quality, speed, and cost of products and services. It emphasizes the elimination and minimization of waste in the value stream. The five-steps of Lean Manufacturing are just-in time (JIT), zero defect and total productive maintenance (TPM), as well as 5S. Lean manufacturing is about eliminating activities that do not add value, such as inspection, rework, and waiting.
In addition to improving product quality and reducing costs, lean manufacturing helps companies achieve their goals faster and reduces employee turnover. Lean Manufacturing is one of the most efficient ways to manage the entire value chains, including suppliers and customers as well distributors and retailers. Lean manufacturing can be found in many industries. For example, Toyota's philosophy underpins its success in automobiles, electronics, appliances, healthcare, chemical engineering, aerospace, paper, food, etc.
Lean manufacturing is based on five principles:
-
Define Value- Identify the added value your company brings to society. What makes you stand out from your competitors?
-
Reduce Waste – Eliminate all activities that don't add value throughout the supply chain.
-
Create Flow – Ensure that work flows smoothly throughout the process.
-
Standardize & simplify - Make processes consistent and repeatable.
-
Build relationships - Develop and maintain personal relationships with both your internal and external stakeholders.
Lean manufacturing is not a new concept, but it has been gaining popularity over the last few years due to a renewed interest in the economy following the global financial crisis of 2008. Many businesses have adopted lean manufacturing techniques to help them become more competitive. In fact, some economists believe that lean manufacturing will be an important factor in economic recovery.
Lean manufacturing is becoming a popular practice in automotive. It has many advantages. These include improved customer satisfaction, reduced inventory levels, lower operating costs, increased productivity, and better overall safety.
Any aspect of an enterprise can benefit from Lean manufacturing. This is because it ensures efficiency and effectiveness in all stages of the value chain.
There are three main types:
-
Just-in Time Manufacturing (JIT), also known as "pull system": This form of lean manufacturing is often referred to simply as "pull". JIT refers to a system in which components are assembled at the point of use instead of being produced ahead of time. This strategy aims to decrease lead times, increase availability of parts and reduce inventory.
-
Zero Defects Manufacturing: ZDM ensures that no defective units leave the manufacturing plant. If a part is required to be repaired on the assembly line, it should not be scrapped. This is also true for finished products that require minor repairs before shipping.
-
Continuous Improvement (CI), also known as Continuous Improvement, aims at improving the efficiency of operations through continuous identification and improvement to minimize or eliminate waste. Continuous improvement involves continuous improvement of processes and people as well as tools.