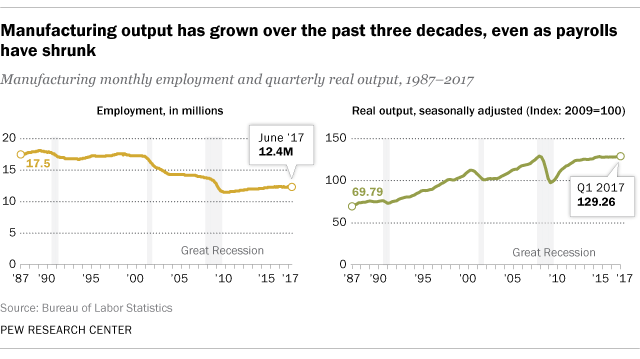
The best lean books provide invaluable guidance for industry leaders by using simple language and clear explanations. The bestselling book covers a range of concepts including how to improve business processes, reduce expenses and improve quality. Implementation is simple thanks to the detailed drawings and step by step instructions. The book also contains information about many tools available to lean manufacturing.
The book also includes a detailed overview of Toyota's global success as well as the Toyota production systems. It also discusses Toyota's management style, motivation, and problem-solving skills. It provides details about Toyota's Lean strategy's success and explains 14 management principles that are the basis of Toyota's business operations. A chapter is also included on the automotive industry. This includes a section about how Toyota used lean principles to improve the automotive sector.
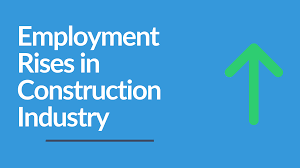
Lean manufacturing refers to a manufacturing process that improves the quality of products and services. It aims to eliminate waste, making the process more efficient and error-free. The most successful manufacturing processes involve the interactions of highly skilled people and machines. These interactions are the main reason for a company's high-quality manufacturing processes.
The Lean Manufacturing Tool Book, The Toyota Way, 14 Management Principles to Improving Quality, Productivity, and The Machine that Changed the World, are the best books about lean manufacturing. These books include a comprehensive explanation about the Toyota production process and practical tips. They also provide step-by-step guidance for applying Lean techniques anywhere there is a manufacturing environment. Lean Manufacturing Tool Book contains all of the necessary tools for Lean manufacturing. It lists the different tools available for use and provides expert advice for selecting the right tool. The book also describes Lean manufacturing concepts and Six Sigma.
The Toyota Way was one of the first books to introduce Lean manufacturing. It covers Toyota's management principles, and how to apply them in your own company. It also contains information about the organizations that make up Toyota's success, and the philosophies they use. It also includes a new afterword that discusses the impact of Lean on the manufacturing industry since the publication of the book. It also includes updated frameworks for improving production and reducing costs.
The Machine that Changed the World: Lean Changed the World is the first book to explain the Toyota Production System in detail and its impact on the manufacturing sector. It was published in 1990. It provides an overview and context of the system. It contains a revised afterword and foreword which provide a deeper understanding of Toyota Production System and its effect on global manufacturing. It also discusses the principles that underlie all Lean practices.
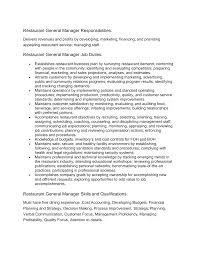
Another important book is The Toyota Kata: Flow Focused Manufacturing Methodology. It explains how Toyota works together with their customers to offer quality products. It explains Toyota's commitment towards quality, problem-solving, speeding up business operations and ensuring customer satisfaction. It also describes how Toyota chooses and hires employees, and how they are motivated and inspired to provide high-quality products and services.
FAQ
How can manufacturing excess production be decreased?
It is essential to find better ways to manage inventory to reduce overproduction. This would reduce the time needed to manage inventory. This could help us free up our time for other productive tasks.
This can be done by using a Kanban system. A Kanban board can be used to monitor work progress. Kanban systems are where work items travel through a series of states until reaching their final destination. Each state has a different priority level.
For instance, when work moves from one stage to another, the current task is complete enough to be moved to the next stage. However, if a task is still at the beginning stages, it will remain so until it reaches the end of the process.
This keeps work moving and ensures no work is lost. With a Kanban board, managers can see exactly how much work is being done at any given moment. This information allows managers to adjust their workflow based off real-time data.
Lean manufacturing can also be used to reduce inventory levels. Lean manufacturing seeks to eliminate waste from every step of the production cycle. Waste includes anything that does not add value to the product. Here are some examples of common types.
-
Overproduction
-
Inventory
-
Packaging not required
-
Material surplus
Manufacturers can reduce their costs and improve their efficiency by using these ideas.
What skills does a production planner need?
Production planners must be flexible, organized, and able handle multiple tasks. Effective communication with clients and colleagues is essential.
What is the best way to learn about manufacturing?
Hands-on experience is the best way to learn more about manufacturing. However, if that's not possible, you can always read books or watch educational videos.
What is the difference between manufacturing and logistics
Manufacturing refers to the process of making goods using raw materials and machines. Logistics covers all aspects involved in managing supply chains, including procurement and production planning. Sometimes manufacturing and logistics are combined to refer to a wider term that includes both the process of creating products as well as their delivery to customers.
Why should you automate your warehouse?
Modern warehouses are increasingly dependent on automation. E-commerce has brought increased demand for more efficient and quicker delivery times.
Warehouses must be able to quickly adapt to changing demands. In order to do this, they need to invest in technology. Automating warehouses has many benefits. These are some of the benefits that automation can bring to warehouses:
-
Increases throughput/productivity
-
Reduces errors
-
Improves accuracy
-
Safety increases
-
Eliminates bottlenecks
-
Companies can scale more easily
-
It makes workers more efficient
-
The warehouse can be viewed from all angles.
-
Enhances customer experience
-
Improves employee satisfaction
-
Minimizes downtime and increases uptime
-
Ensures quality products are delivered on time
-
Removes human error
-
It helps ensure compliance with regulations
Statistics
- Many factories witnessed a 30% increase in output due to the shift to electric motors. (en.wikipedia.org)
- According to the United Nations Industrial Development Organization (UNIDO), China is the top manufacturer worldwide by 2019 output, producing 28.7% of the total global manufacturing output, followed by the United States, Japan, Germany, and India.[52][53] (en.wikipedia.org)
- You can multiply the result by 100 to get the total percent of monthly overhead. (investopedia.com)
- Job #1 is delivering the ordered product according to specifications: color, size, brand, and quantity. (netsuite.com)
- (2:04) MTO is a production technique wherein products are customized according to customer specifications, and production only starts after an order is received. (oracle.com)
External Links
How To
How to use Lean Manufacturing in the production of goods
Lean manufacturing refers to a method of managing that seeks to improve efficiency and decrease waste. It was first developed in Japan in the 1970s/80s by Taiichi Ahno, who was awarded the Toyota Production System (TPS), award from KanjiToyoda, the founder of TPS. Michael L. Watkins published the "The Machine That Changed the World", the first book about lean manufacturing. It was published in 1990.
Lean manufacturing is often described as a set if principles that help improve the quality and speed of products and services. It emphasizes the elimination and minimization of waste in the value stream. The five-steps of Lean Manufacturing are just-in time (JIT), zero defect and total productive maintenance (TPM), as well as 5S. Lean manufacturing seeks to eliminate non-value added activities, such as inspection, work, waiting, and rework.
Lean manufacturing improves product quality and costs. It also helps companies reach their goals quicker and decreases employee turnover. Lean manufacturing is a great way to manage the entire value chain including customers, suppliers, distributors and retailers as well as employees. Many industries worldwide use lean manufacturing. Toyota's philosophy is a great example of this. It has helped to create success in automobiles as well electronics, appliances and healthcare.
Five principles are the basis of lean manufacturing:
-
Define value - Find out what your business contributes to society, and what makes it different from other competitors.
-
Reduce waste - Stop any activity that isn't adding value to the supply chains.
-
Create Flow: Ensure that the work process flows without interruptions.
-
Standardize and simplify – Make processes as repeatable and consistent as possible.
-
Building Relationships – Establish personal relationships with both external and internal stakeholders.
Although lean manufacturing has always been around, it is gaining popularity in recent years because of a renewed interest for the economy after 2008's global financial crisis. Many businesses are now using lean manufacturing to improve their competitiveness. Economists think that lean manufacturing is a crucial factor in economic recovery.
Lean manufacturing is becoming a popular practice in automotive. It has many advantages. These include improved customer satisfaction, reduced inventory levels, lower operating costs, increased productivity, and better overall safety.
The principles of lean manufacturing can be applied in almost any area of an organization. It is especially useful for the production aspect of an organization, as it ensures that every step in the value chain is efficient and effective.
There are three main types:
-
Just-in Time Manufacturing: This lean manufacturing method is commonly called "pull systems." JIT refers to a system in which components are assembled at the point of use instead of being produced ahead of time. This strategy aims to decrease lead times, increase availability of parts and reduce inventory.
-
Zero Defects Manufacturing (ZDM): ZDM focuses on ensuring that no defective units leave the manufacturing facility. It is better to repair a part than have it removed from the production line if it needs to be fixed. This also applies to finished products that need minor repairs before being shipped.
-
Continuous Improvement (CI),: Continuous improvement aims improve the efficiency and effectiveness of operations by continuously identifying issues and making changes to reduce waste. Continuous Improvement involves continuous improvement of processes.