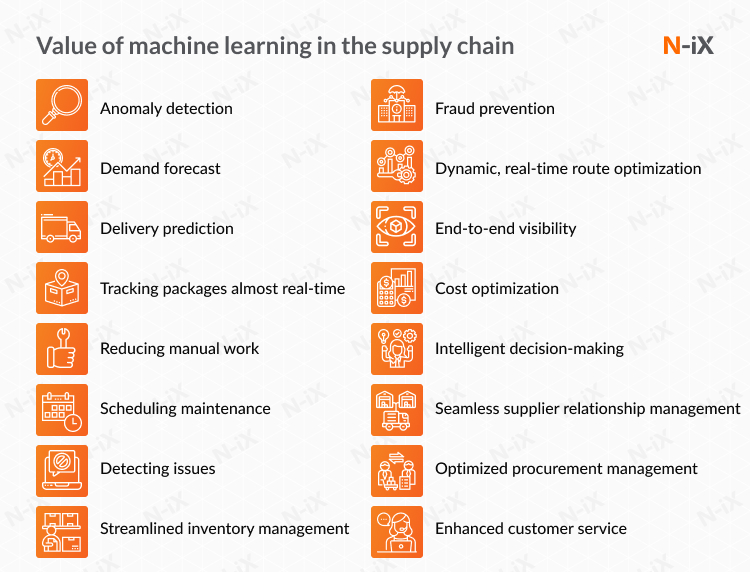
It is important that you include all the duties in the job description to attract the best people for transport and logistic jobs. These duties can include filling company paperwork and ordering raw materials. This can make the job description more appealing but it could also lead to the hiring of the wrong person. This can lead to problems for customers and businesses. It means you'll have to spend time, money, and effort training the new employee.
Job description
The logistics and transport professions work in many different industries, moving people and goods from A to B. Some work in the field of shipping, while others may be involved in road maintenance. The job includes monitoring traffic congestion and safety. This field requires that workers adapt to changing business requirements and work in multiple locations.
A job description that is effective focuses on the skills and training required for the job. It also reflects the company's culture, values, and culture. It should state whether the job is permanent or temporary.
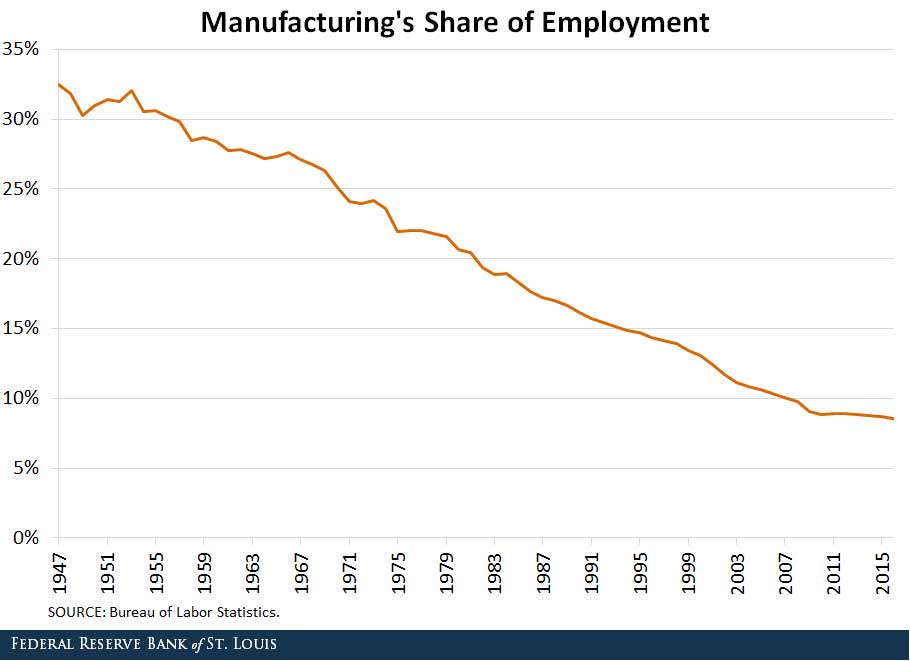
Salary
Many opportunities exist in transport and logistics jobs. These range from entry-level roles to more senior positions. The industry you work in and your experience will determine the salary level. Entry-level jobs typically start at $40,000 per annum. There are opportunities for advancement and salaries can go up.
You have many options when it comes to salary for logistics or transportation jobs. Some are more lucrative than some. Although entry-level salary may be lower than for other professions, it is possible to earn much more if your experience level is high. Some companies offer in-house training or even pay for graduate-level education.
Requirements
The high demand for logistics and transportation jobs in many industries is reflected in their ability to be highly skilled. The primary goal of these jobs is to ensure that goods are delivered on time and at the lowest cost. Employers must hire the right personnel with the correct skills. Although junior staff might not require prior training, those who wish to move up should possess relevant qualifications, such a Supply Chain Practitioner Advanced Apprenticeship and Chartered Institute of Logistics and Transport accreditations.
A degree in transportation and logistics is an important step to take if you want to pursue a career in this field. There are plenty of courses available that will help you to develop your knowledge and skills. The Chartered Institute of Logistics and Transport UK has a Level 2 Certificate for Transport and Logistics. This course is great for those just starting out in this field. You can also gain valuable work experience by undertaking a graduate recruitment scheme, which is offered by many large logistics companies.
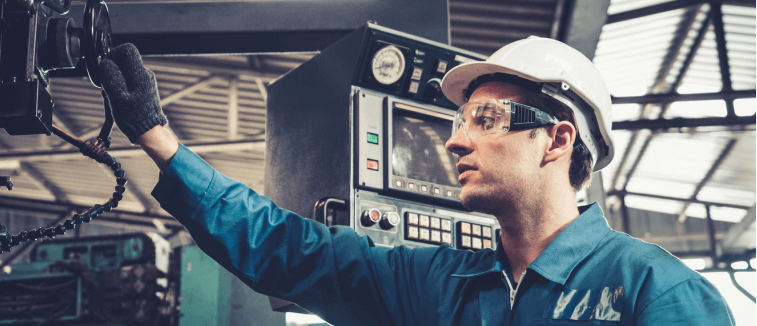
Localities
There are many career options in logistics and transport. They involve planning and evaluating different distribution methods. These jobs require an excellent level of analytical thinking and the ability manage complex data. Communication skills are essential. Some jobs require you travel to remote places. Graduate training in logistics, transport and logistics is available. These programs will provide you the skills to succeed. Many of these programs will offer paid internships.
Transport and logistics occupations are in great demand. They are expected to increase by 3% from 2019-2029, the same as the national median. However, certain jobs are expected to see higher growth than the average, such as commercial and airline pilots. Other jobs in this sector include driver/sales workers and delivery truck drivers.
FAQ
How can manufacturing efficiency improved?
First, identify the factors that affect production time. We must then find ways that we can improve these factors. If you don’t know how to start, look at which factors have the greatest impact upon production time. Once you identify them, look for solutions.
What is the job of a logistics manger?
A logistics manager makes sure that all goods are delivered on-time and in good condition. This is achieved by using their knowledge and experience with the products of the company. He/she should ensure that sufficient stock is available in order to meet customer demand.
What is the role and responsibility of a Production Planner?
Production planners ensure all aspects of the project are delivered within time and budget. They make sure that the product and services meet client expectations.
How is a production manager different from a producer planner?
The main difference between a production planner and a project manager is that a project manager is usually the person who plans and organizes the entire project, whereas a production planner is mainly involved in the planning stage of the project.
What types of jobs can you find in logistics
There are many types of jobs in logistics. Some of them are:
-
Warehouse workers - They load and unload trucks and pallets.
-
Transportation drivers: They drive trucks and trailers and deliver goods and make pick-ups.
-
Freight handlers - They sort and pack freight in warehouses.
-
Inventory managers - These are responsible for overseeing the stock of goods in warehouses.
-
Sales representatives - They sell products to customers.
-
Logistics coordinators are responsible for organizing and planning logistics operations.
-
Purchasing agents - They purchase goods and services needed for company operations.
-
Customer service representatives are available to answer customer calls and emails.
-
Shippers clerks - They process shipping order and issue bills.
-
Order fillers – They fill orders based upon what was ordered and shipped.
-
Quality control inspectors (QCI) - They inspect all incoming and departing products for potential defects.
-
Others – There are many other types available in logistics. They include transport supervisors, cargo specialists and others.
Statistics
- Many factories witnessed a 30% increase in output due to the shift to electric motors. (en.wikipedia.org)
- According to the United Nations Industrial Development Organization (UNIDO), China is the top manufacturer worldwide by 2019 output, producing 28.7% of the total global manufacturing output, followed by the United States, Japan, Germany, and India.[52][53] (en.wikipedia.org)
- (2:04) MTO is a production technique wherein products are customized according to customer specifications, and production only starts after an order is received. (oracle.com)
- [54][55] These are the top 50 countries by the total value of manufacturing output in US dollars for its noted year according to World Bank.[56] (en.wikipedia.org)
- Job #1 is delivering the ordered product according to specifications: color, size, brand, and quantity. (netsuite.com)
External Links
How To
Six Sigma: How to Use it in Manufacturing
Six Sigma is "the application statistical process control (SPC), techniques for continuous improvement." Motorola's Quality Improvement Department developed it at their Tokyo plant in Japan in 1986. Six Sigma's main goal is to improve process quality by standardizing processes and eliminating defects. This method has been adopted by many companies in recent years as they believe there are no perfect products or services. The main goal of Six Sigma is to reduce variation from the mean value of production. If you take a sample and compare it with the average, you will be able to determine how much of the production process is different from the norm. If the deviation is excessive, it's likely that something needs to be fixed.
Understanding the dynamics of variability within your business is the first step in Six Sigma. Once you've understood that, you'll want to identify sources of variation. This will allow you to decide if these variations are random and systematic. Random variations occur when people make mistakes; systematic ones are caused by factors outside the process itself. Random variations would include, for example, the failure of some widgets to fall from the assembly line. But if you notice that every widget you make falls apart at the exact same place each time, this would indicate that there is a problem.
Once you identify the problem areas, it is time to create solutions. It might mean changing the way you do business or redesigning it entirely. Test them again once you've implemented the changes. If they don't work, you will need to go back to the drawing boards and create a new plan.