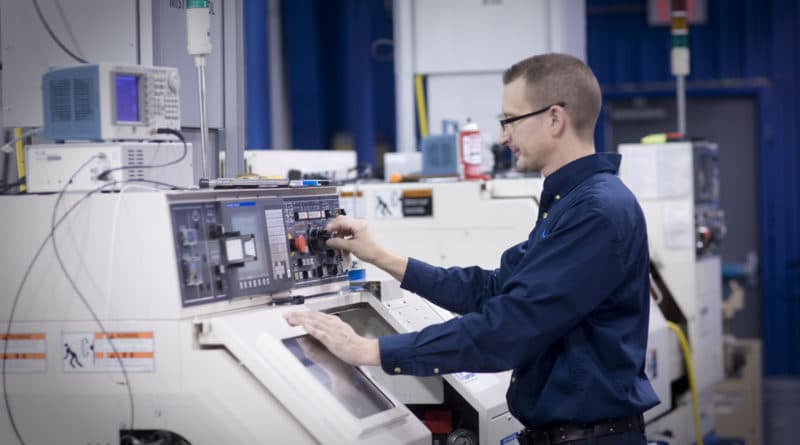
Andon, in the world of lean production, is a visual sign that highlights and draws attention to issues with the intention of solving them permanently. It is an effective tool for empowering plant floor workers and accelerating teamwork.
Andon
The word is of Japanese origin and comes from the paper-covered lanterns of the Edo era, which is the period between the seventeenth and nineteenth centuries. In Japanese, it also refers to a system of tying light signals or sounds to a specific process issue in order to alert operators and management.
Toyota uses the term "build-in" quality as a core principle of its Jidoka. It is a component in their TPS system (Toyota Production System). In the US it is often cited to be the basis of a business concept that allows workers on the production lines to stop the line if a quality or safety problem occurs.
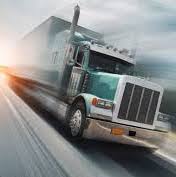
What is andon?
Toyota was the first to introduce Andon, a lean-manufacturing system. The system is simple and consists of an LED board with three colors: green, yellow, and red. Each color represents a different stage of production. The production line runs normally when the green light is on. The yellow light means that the problem has been identified and is being dealt with. If the red light appears, production will stop. Workers may take a short break, prepare spare parts, ask for help or even fill their bins.
The Andon board is easy to use and the supervisors can immediately understand what happened. The system provides immediate feedback to ensure that any problems are dealt with as soon as they arise.
There are several types of andons. The most common one is a light that flashes red with a buzzer or sound to alert the production team. These signal, alert and solve systems are very effective at identifying problems that could lead to downtime or repeat incidents.
An effective andon board can help to keep the production running in case of a malfunction. It's a simple, effective tool to increase productivity, reduce downtime, and improve product quality.
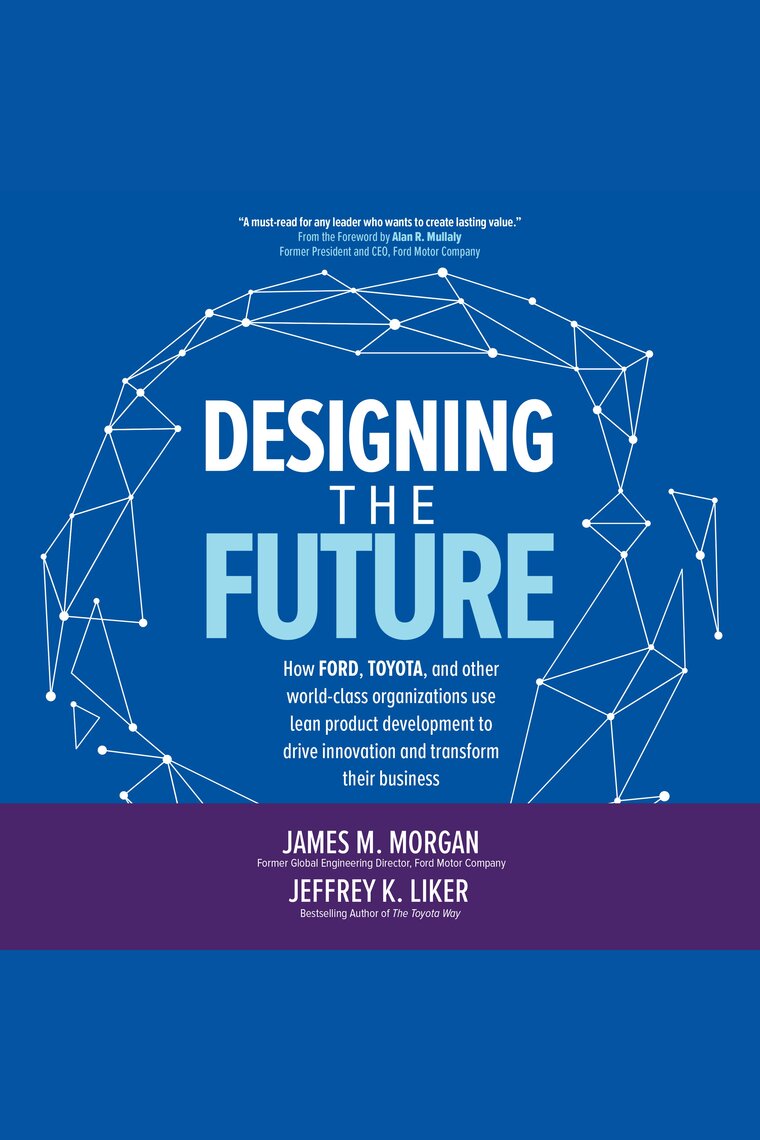
What is anon toyota?
Toyota used a special cord that any employee on the manufacturing floor could pull if they saw a potential issue with one of their cars. This cord could be pulled by a worker if they felt that the car had been compromised.
In a similar way, modern andon system use technology in order to present curated data that helps to identify emerging issues, push notifications to stakeholder in real time and identify the underlying cause that requires a longer-term solution. Nevertheless, a human touch is required to interpret and act on this information.
How to make the andon system work?
It is important to start by creating a culture in which workers and managers are not afraid to address and identify problems. The more reluctant they are, they are more likely not to address problems or hide them. This can be improved by tying line stops to the resolution of problems, so workers are more likely pull the cable and hit the button when there is a problem.
FAQ
What do we need to know about Manufacturing Processes in order to learn more about Logistics?
No. No. Knowing about manufacturing processes will help you understand how logistics works.
Is automation important for manufacturing?
Automating is not just important for manufacturers, but also for service providers. They can provide services more quickly and efficiently thanks to automation. It reduces human errors and improves productivity, which in turn helps them lower their costs.
Why is logistics important in manufacturing
Logistics is an integral part of every business. They can help you achieve great success by helping you manage product flow from raw material to finished goods.
Logistics are also important in reducing costs and improving efficiency.
Statistics
- (2:04) MTO is a production technique wherein products are customized according to customer specifications, and production only starts after an order is received. (oracle.com)
- According to a Statista study, U.S. businesses spent $1.63 trillion on logistics in 2019, moving goods from origin to end user through various supply chain network segments. (netsuite.com)
- According to the United Nations Industrial Development Organization (UNIDO), China is the top manufacturer worldwide by 2019 output, producing 28.7% of the total global manufacturing output, followed by the United States, Japan, Germany, and India.[52][53] (en.wikipedia.org)
- In 2021, an estimated 12.1 million Americans work in the manufacturing sector.6 (investopedia.com)
- Many factories witnessed a 30% increase in output due to the shift to electric motors. (en.wikipedia.org)
External Links
How To
How to use lean manufacturing in the production of goods
Lean manufacturing is a management style that aims to increase efficiency and reduce waste through continuous improvement. It was developed in Japan during the 1970s and 1980s by Taiichi Ohno, who received the Toyota Production System (TPS) award from TPS founder Kanji Toyoda. Michael L. Watkins published the book "The Machine That Changed the World", which was the first to be published about lean manufacturing.
Lean manufacturing, often described as a set and practice of principles, is aimed at improving the quality, speed, cost, and efficiency of products, services, and other activities. It emphasizes the elimination of defects and waste throughout the value stream. Lean manufacturing can be described as just-in–time (JIT), total productive maintenance, zero defect (TPM), or even 5S. Lean manufacturing is about eliminating activities that do not add value, such as inspection, rework, and waiting.
Lean manufacturing improves product quality and costs. It also helps companies reach their goals quicker and decreases employee turnover. Lean manufacturing has been deemed one of the best ways to manage the entire value-chain, including customers, distributors as well retailers and employees. Lean manufacturing practices are widespread in many industries. Toyota's philosophy has been a key driver of success in many industries, including automobiles and electronics.
Five fundamental principles underlie lean manufacturing.
-
Define Value - Identify the value your business adds to society and what makes you different from competitors.
-
Reduce waste - Stop any activity that isn't adding value to the supply chains.
-
Create Flow – Ensure that work flows smoothly throughout the process.
-
Standardize and Simplify – Make processes as consistent, repeatable, and as simple as possible.
-
Build relationships - Develop and maintain personal relationships with both your internal and external stakeholders.
Although lean manufacturing has always been around, it is gaining popularity in recent years because of a renewed interest for the economy after 2008's global financial crisis. Many businesses have adopted lean production techniques to make them more competitive. In fact, some economists believe that lean manufacturing will be an important factor in economic recovery.
With many benefits, lean manufacturing is becoming more common in the automotive industry. These include better customer satisfaction and lower inventory levels. They also result in lower operating costs.
You can apply Lean Manufacturing to virtually any aspect of your organization. However, it is particularly useful when applied to the production side of an organization because it ensures that all steps in the value chain are efficient and effective.
There are three types of lean manufacturing.
-
Just-in Time Manufacturing: This lean manufacturing method is commonly called "pull systems." JIT refers to a system in which components are assembled at the point of use instead of being produced ahead of time. This approach aims to reduce lead times, increase the availability of parts, and reduce inventory.
-
Zero Defects Manufacturing (ZDM): ZDM focuses on ensuring that no defective units leave the manufacturing facility. Repairing a part that is damaged during assembly should be done, not scrapping. This also applies to finished products that need minor repairs before being shipped.
-
Continuous Improvement (CI: Continuous improvement aims to increase the efficiency of operations by constantly identifying and making improvements to reduce or eliminate waste. Continuous Improvement involves continuous improvement of processes.