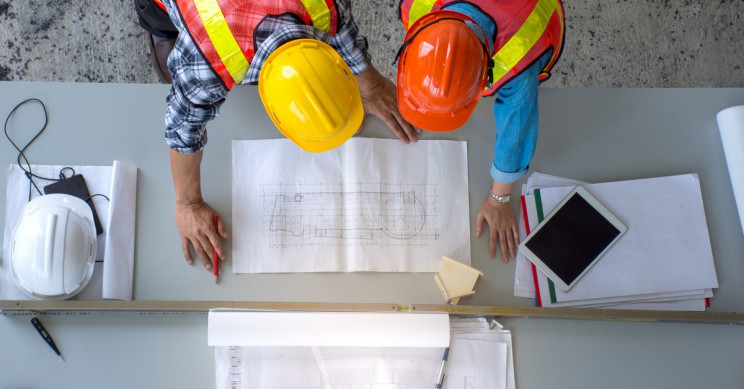
Companies can use lean product development methods to ensure products that are best suited for their customers' needs. Lean product development methods can be used to speed up product development, reduce waste, and ensure products meet customer requirements. Lean manufacturing practices can help companies remain competitive.
Lean product development is a method that combines engineering and manufacturing work. Its goal is to create a product that works with minimal effort, stock, and time. It includes rapid learning cycles and uses visual planning techniques such as visual boards. It also integrates set based concurrent engineering.
Understanding the customer is the foundation of lean product development. This involves understanding the customer and identifying the risks involved in the business plan. It is important that you understand the product's functionality and features. If the customer doesn't use them, they can make the product more expensive and unnecessary. It includes the creation and implementation of a validation and verification plan.
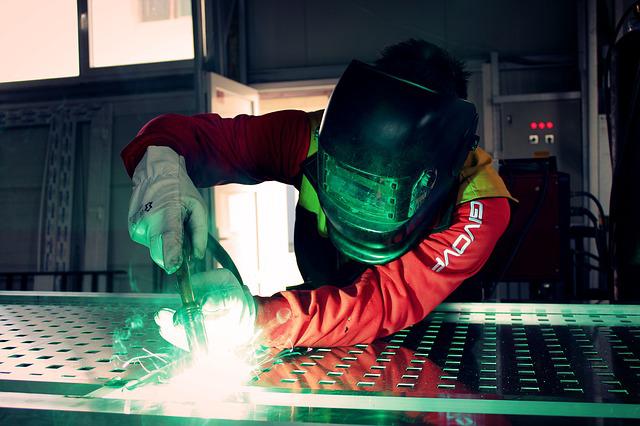
Next is to create an activity community. This allows teams to determine their own work and plan their own work. The network creates a framework that allows for the creation of value. It helps reduce waste and allows teams to find ways to improve their processes.
The ideal PD procedure focuses on a steady flow of value from conception until production. It shouldn't contain any bureaucratic loopbacks or stops to correct mistakes. It should also reflect the value stream as an entire system. The system should not become unstable and lead to vision loss. This should be a one-piece flow in manufacturing.
First, you need to establish the value. This can be done by analyzing the business case and reviewing all relevant literature. It is essential that all stakeholders agree on the expectations regarding value. It is important to define the product scope. This includes customer value as well as the features and functions. These are the elements that determine the technology and process used.
The next step is to design the value stream. This involves eliminating non-value adding steps from the value stream. Unused designs and untested code should be removed. It is also important to reduce the number of tasks performed at once. This is often done by frequent changes to priorities.
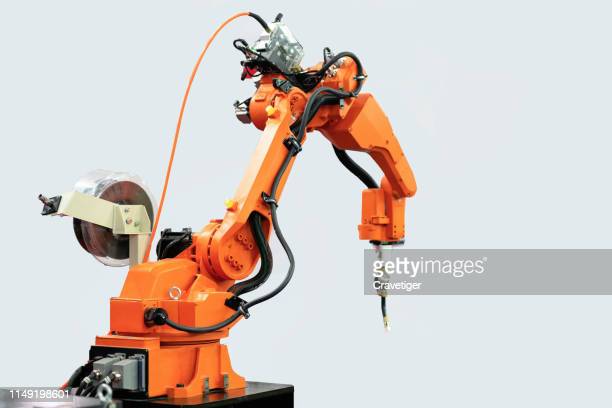
Lean product development is a very valuable tool that can help businesses reduce costs, find inefficiencies in processes and remain competitive. It helps companies create value streams that can be sustained over time, which will make them more profitable. It has helped businesses from all industries including healthcare, high tech, and manufacturing.
Lean product development uses a set-based concurrent engineering approach that allows teams to develop products faster and with less resources. In the past, big companies took longer to develop new products than start-ups, primarily due to the complex codebases they used. This can make it hard to build on and maintain.
FAQ
What are the 7 Rs of logistics?
The 7R's of Logistics is an acronym for the seven basic principles of logistics management. It was developed and published by the International Association of Business Logisticians in 2004 as part of the "Seven Principles of Logistics Management".
The acronym is composed of the following letters.
-
Responsible - ensure that actions are in compliance with legal requirements and do not cause harm to others.
-
Reliable: Have faith in your ability or the ability to honor any promises made.
-
Be responsible - Use resources efficiently and avoid wasting them.
-
Realistic - Take into consideration all aspects of operations including cost-effectiveness, environmental impact, and other factors.
-
Respectful - Treat people fairly and equitably
-
Reliable - Find ways to save money and increase your productivity.
-
Recognizable provides value-added products and services to customers
What are the responsibilities for a manufacturing manager
A manufacturing manager has to ensure that all manufacturing processes work efficiently and effectively. They should be aware of any issues within the company and respond accordingly.
They should also be able communicate with other departments, such as sales or marketing.
They should also be aware of the latest trends in their industry and be able to use this information to help improve productivity and efficiency.
Is there anything we should know about Manufacturing Processes prior to learning about Logistics.
No. No. Knowing about manufacturing processes will help you understand how logistics works.
What are the responsibilities of a logistic manager?
Logistics managers are responsible for ensuring that all goods arrive in perfect condition and on time. This is done by using his/her experience and knowledge of the company's products. He/she should make sure that enough stock is on hand to meet the demands.
What are the products of logistics?
Logistics involves the transportation of goods from point A and point B.
They include all aspects associated with transport including packaging, loading transporting, unloading storage, warehousing inventory management customer service, distribution returns and recycling.
Logisticians ensure the product reaches its destination in the most efficient manner. They provide information on demand forecasts as well stock levels, production schedules and availability of raw material.
They can also track shipments in transit and monitor quality standards.
Statistics
- Many factories witnessed a 30% increase in output due to the shift to electric motors. (en.wikipedia.org)
- In 2021, an estimated 12.1 million Americans work in the manufacturing sector.6 (investopedia.com)
- (2:04) MTO is a production technique wherein products are customized according to customer specifications, and production only starts after an order is received. (oracle.com)
- According to a Statista study, U.S. businesses spent $1.63 trillion on logistics in 2019, moving goods from origin to end user through various supply chain network segments. (netsuite.com)
- You can multiply the result by 100 to get the total percent of monthly overhead. (investopedia.com)
External Links
How To
How to Use the 5S to Increase Productivity In Manufacturing
5S stands to stand for "Sort", “Set In Order", “Standardize", and "Store". Toyota Motor Corporation created the 5S methodology in 1954. It helps companies achieve higher levels of efficiency by improving their work environment.
This method aims to standardize production processes so that they are repeatable, measurable and predictable. It means tasks like cleaning, sorting or packing, labeling, and storing are done every day. Workers can be more productive by knowing what to expect.
Five steps are required to implement 5S: Sort, Set In Order, Standardize. Separate. Each step has a different action and leads to higher efficiency. By sorting, for example, you make it easy to find the items later. When you arrange items, you place them together. Once you have separated your inventory into groups and organized them, you will store these groups in easily accessible containers. Finally, label all containers correctly.
Employees will need to be more critical about their work. Employees need to understand the reasons they do certain jobs and determine if there is a better way. To be successful in the 5S system, employees will need to acquire new skills and techniques.
The 5S method increases efficiency and morale among employees. As they begin to see improvements, they feel motivated to continue working towards the goal of achieving higher levels of efficiency.