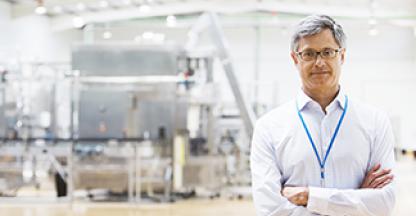
CEVA Logistics is a company that provides logistics services. These logistics companies offer many benefits to employees, whether you are looking for a career change or simply want to find a new job. Here's how you apply for a logistics job with one of these companies. You can search for jobs by region.
Job description
CEVA Logistics offers many jobs to individuals with diverse education and experience. The company's core values include customer service dedication and timely delivery. The company seeks people who are passionate about logistics, and who are willing work hard. When applying for a job, candidates with prior experience in logistics will be preferred. Candidates who are positive and have a positive attitude would also be considered.
CEVA Logistics is searching for a Process/Industrial Engineering to develop and implement new processes, and increase efficiency. The ideal candidate must be self-motivated, energetic, and able work well with others. This includes managing projects, designing and implementing process layouts, and applying analytical and modeling skills. They will need to be skilled in robotics, as well as other manufacturing processes, to improve efficiency and quality.
Education Required
CEVA Logistics offers many opportunities for candidates interested in a career with the company, including sales rep and warehouse manager. You can also choose to be operations supervisors. This involves overseeing all aspects of the company's day, including inventory and scheduling. They may have several employees working under them. These positions require candidates to have a bachelor's degree, supervisory experience, strong management and leadership skills.
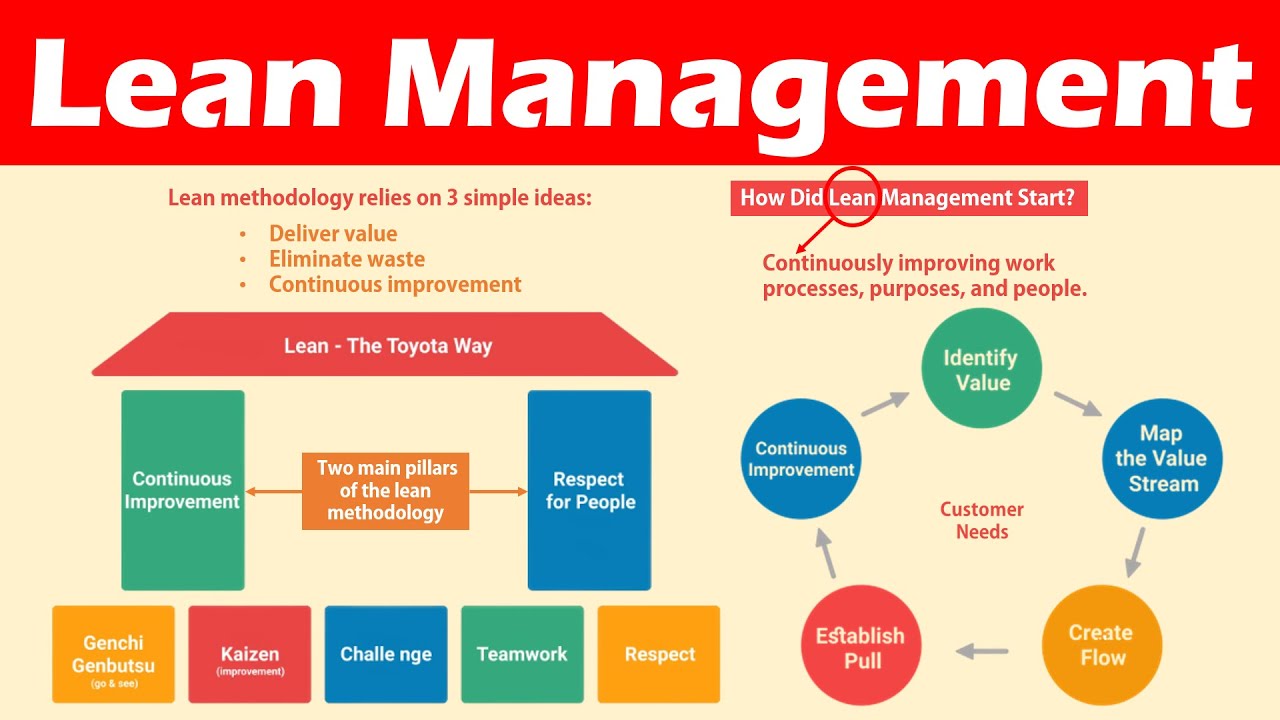
Online applications are accepted from interested applicants. Online applications require candidates to first create a career profile in the company's portal. Their LinkedIn accounts can be used to connect to their profile, upload their resumes and enter relevant information. Once they have completed their profile, they will be able to select the country or region that interests them and then get in touch with a recruiter.
Salary range
If you are interested in applying for a CEVA Logistics career, the first thing to do is create a profile at the company's online job portal. This allows to link with your LinkedIn profile, upload your resume, and allow you to create a job application. You can also input details about your work experience, skills, or other pertinent information. Next, select the country or region in which you would like to work. After this step, you will be provided with contact information by a recruiter from that region.
Salaries at CEVA Logistics vary based on job title, experience, and location. An Air Break Bulk Specialist earns 24,000, while the Vice President at CEVA Logistics earns $166,000 each year. However, salaries can be different in each location, depending on the economic conditions in that area.
Localities
CEVA Logistics has a fantastic career opportunity for those looking to work in logistics. There are many positions available at different locations. Each position has different responsibilities and requirements. To apply for a position, type the job title into the search box. Also, enter your location. If you search for Edison, NJ jobs, you will see the listings. You must have driving experience and the ability to communicate well with clients and employees.
CEVA Logistics offers many career options, including supervisory and managerial positions. Supervisors manage the company's day-to-day operations. They are responsible for managing inventory, scheduling, and supervising employees. Operations supervisors typically have a team of employees reporting to them, and typically require a bachelor's degree or other related experience. Leadership and management skills are essential.
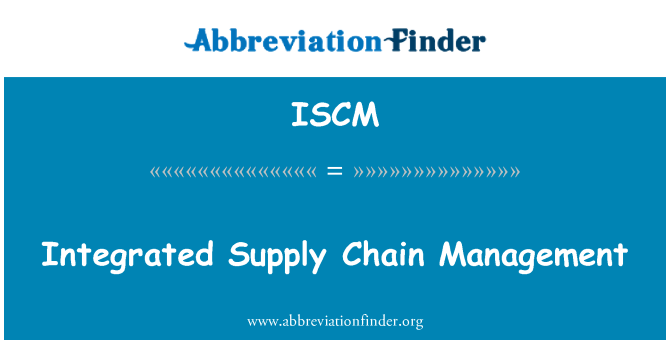
Apply online
If you're in the market for a job in the logistics industry, you can apply online for a position with CEVA Logistics. Ceva Logistics, an international logistics company, was established in 2006 as a result the merger of two Australian and Texan contracts logistics companies. The company's operations today span more than 950 locations across 170 countries. You have the option to apply for part or full-time employment.
Although some positions at CEVA may require some experience in order to be successful, many are entry-level. Others require minimal to moderate experience. You can find entry-level positions such as customer service representative, administrative clerk, or dispatcher.
FAQ
What does manufacturing mean?
Manufacturing Industries refers to businesses that manufacture products. These products are sold to consumers. This is accomplished by using a variety of processes, including production, distribution and retailing. They create goods from raw materials, using machines and various other equipment. This includes all types manufactured goods such as clothing, building materials, furniture, electronics, tools and machinery.
What are the four types in manufacturing?
Manufacturing is the process of transforming raw materials into useful products using machines and processes. It includes many different activities like designing, building and testing, packaging, shipping and selling, as well as servicing.
How can overproduction in manufacturing be reduced?
The key to reducing overproduction lies in developing better ways to manage inventory. This would reduce the time needed to manage inventory. This will allow us to free up resources for more productive tasks.
This can be done by using a Kanban system. A Kanban board is a visual display used to track work in progress. Work items are moved through various states to reach their destination in a Kanban system. Each state represents a different priority level.
To illustrate, work can move from one stage or another when it is complete enough for it to be moved to a new stage. It is possible to keep a task in the beginning stages until it gets to the end.
This allows for work to continue moving forward, while also ensuring that there is no work left behind. With a Kanban board, managers can see exactly how much work is being done at any given moment. This information allows managers to adjust their workflow based off real-time data.
Lean manufacturing can also be used to reduce inventory levels. Lean manufacturing emphasizes eliminating waste in all phases of production. Anything that does nothing to add value to a product is waste. Here are some examples of common types.
-
Overproduction
-
Inventory
-
Unnecessary packaging
-
Exceed materials
Manufacturers can reduce their costs and improve their efficiency by using these ideas.
What is the difference between Production Planning and Scheduling?
Production Planning (PP), is the process of deciding what production needs to take place at any given time. Forecasting and identifying production capacity are two key elements to this process.
Scheduling involves the assignment of dates and times to tasks in order to complete them within the timeframe.
What do we need to know about Manufacturing Processes in order to learn more about Logistics?
No. It doesn't matter if you don't know anything about manufacturing before you learn about logistics. Knowing about manufacturing processes will help you understand how logistics works.
What is production planning?
Production Planning refers to the development of a plan for every aspect of production. This document aims to ensure that everything is planned and ready when you are ready to shoot. This document should also include information on how to get the best result on set. It should include information about shooting locations, casting lists, crew details, equipment requirements, and shooting schedules.
The first step is to decide what you want. You may have already chosen the location you want, or there are locations or sets you prefer. Once you have identified the scenes and locations, you can start to determine which elements are required for each scene. For example, you might decide that you need a car but don't know exactly what model you want. If this is the case, you might start searching online for car models and then narrow your options by selecting from different makes.
After you've found the perfect car, it's time to start thinking about adding extras. Do you need people sitting in the front seats? You might also need someone to help you get around the back. Perhaps you would like to change the interior colour from black to white. These questions will help to determine the style and feel of your car. Another thing you can do is think about what type of shots are desired. Will you be filming close-ups or wide angles? Maybe you want to show the engine and the steering wheel. These factors will help you determine which car style you want to film.
Once you have established all the details, you can create a schedule. You can create a schedule that will outline when you must start and finish your shoots. You will need to know when you have to be there, what time you have to leave and when your return home. Everyone knows exactly what they should do and when. If you need to hire extra staff, you can make sure you book them in advance. It is not worth hiring someone who won’t show up because you didn’t tell him.
Your schedule will also have to be adjusted to reflect the number of days required to film. Some projects may only take a couple of days, while others could last for weeks. While creating your schedule, it is important to remember whether you will require more than one shot per day. Multiple shots at the same location can increase costs and make it more difficult to complete. It is better to be cautious and take fewer shots than you risk losing money if you are not sure if multiple takes are necessary.
Budget setting is an important part of production planning. Setting a realistic budget is essential as it will allow you to work within your means. You can always lower the budget if you encounter unexpected problems. However, it is important not to overestimate the amount that you will spend. You'll end up with less money after paying for other things if the cost is underestimated.
Production planning can be a complex process. However, once you know how everything works together it will become easier to plan future projects.
How does a Production Planner differ from a Project Manager?
A production planner is more involved in the planning phase of the project than a project manger.
Statistics
- You can multiply the result by 100 to get the total percent of monthly overhead. (investopedia.com)
- In the United States, for example, manufacturing makes up 15% of the economic output. (twi-global.com)
- [54][55] These are the top 50 countries by the total value of manufacturing output in US dollars for its noted year according to World Bank.[56] (en.wikipedia.org)
- (2:04) MTO is a production technique wherein products are customized according to customer specifications, and production only starts after an order is received. (oracle.com)
- According to the United Nations Industrial Development Organization (UNIDO), China is the top manufacturer worldwide by 2019 output, producing 28.7% of the total global manufacturing output, followed by the United States, Japan, Germany, and India.[52][53] (en.wikipedia.org)
External Links
How To
How to Use Six Sigma in Manufacturing
Six Sigma is defined by "the application SPC (statistical process control) techniques to achieve continuous improvements." Motorola's Quality Improvement Department in Tokyo, Japan developed Six Sigma in 1986. The basic idea behind Six Sigma is to improve quality by improving processes through standardization and eliminating defects. Many companies have adopted Six Sigma in recent years because they believe that there are no perfect products and services. Six Sigma's primary goal is to reduce variation from the average value of production. If you take a sample and compare it with the average, you will be able to determine how much of the production process is different from the norm. If you notice a large deviation, then it is time to fix it.
Understanding the nature of variability in your business is the first step to Six Sigma. Once you've understood that, you'll want to identify sources of variation. It is important to identify whether the variations are random or systemic. Random variations happen when people make errors; systematic variations are caused externally. If you make widgets and some of them end up on the assembly line, then those are considered random variations. It would be considered a systematic problem if every widget that you build falls apart at the same location each time.
Once you've identified the problem areas you need to find solutions. You might need to change the way you work or completely redesign the process. After implementing the new changes, you should test them again to see if they worked. If they didn't work, then you'll need to go back to the drawing board and come up with another plan.