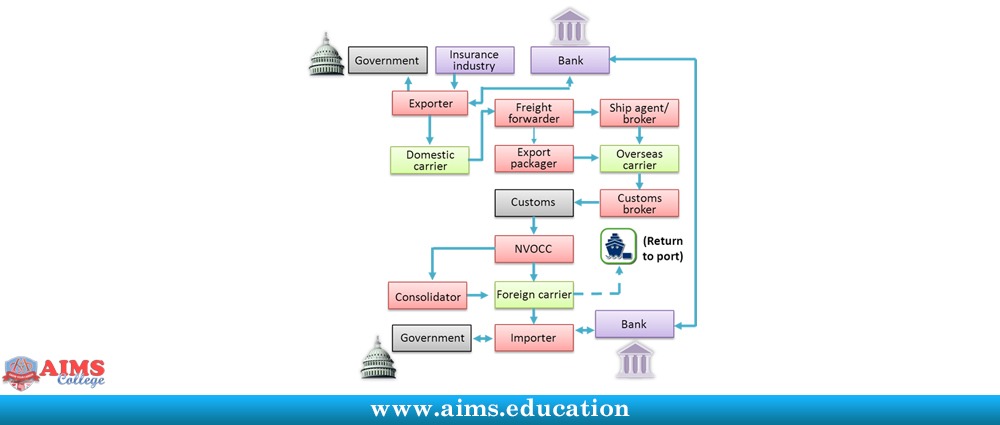
It may be more difficult than you think to introduce kaizen to manufacturing processes. It takes time to obtain inventory and ensure everyone is present. The length of this improvement project depends on the type of company and participation level. To ensure that your manufacturing process improvement initiative will be successful, follow the proper implementation methodologies and get the necessary resources. For this strategy to be successful, it is important to establish a strong company culture encouraging continuous improvement.
Create a company culture that is focused on improvement
Gallup polls indicate that only 32% American workers are engaged in their jobs. 17.2% of those surveyed were disengaged. Kaizen culture encourages employee engagement which in turn will improve processes, reduce turnover and promote innovation. In addition, engaged employees are more likely to contribute ideas and innovate, leading to higher productivity and customer satisfaction. Kaizen culture offers more benefits than reducing waste, increasing productivity, and increasing customer satisfaction.
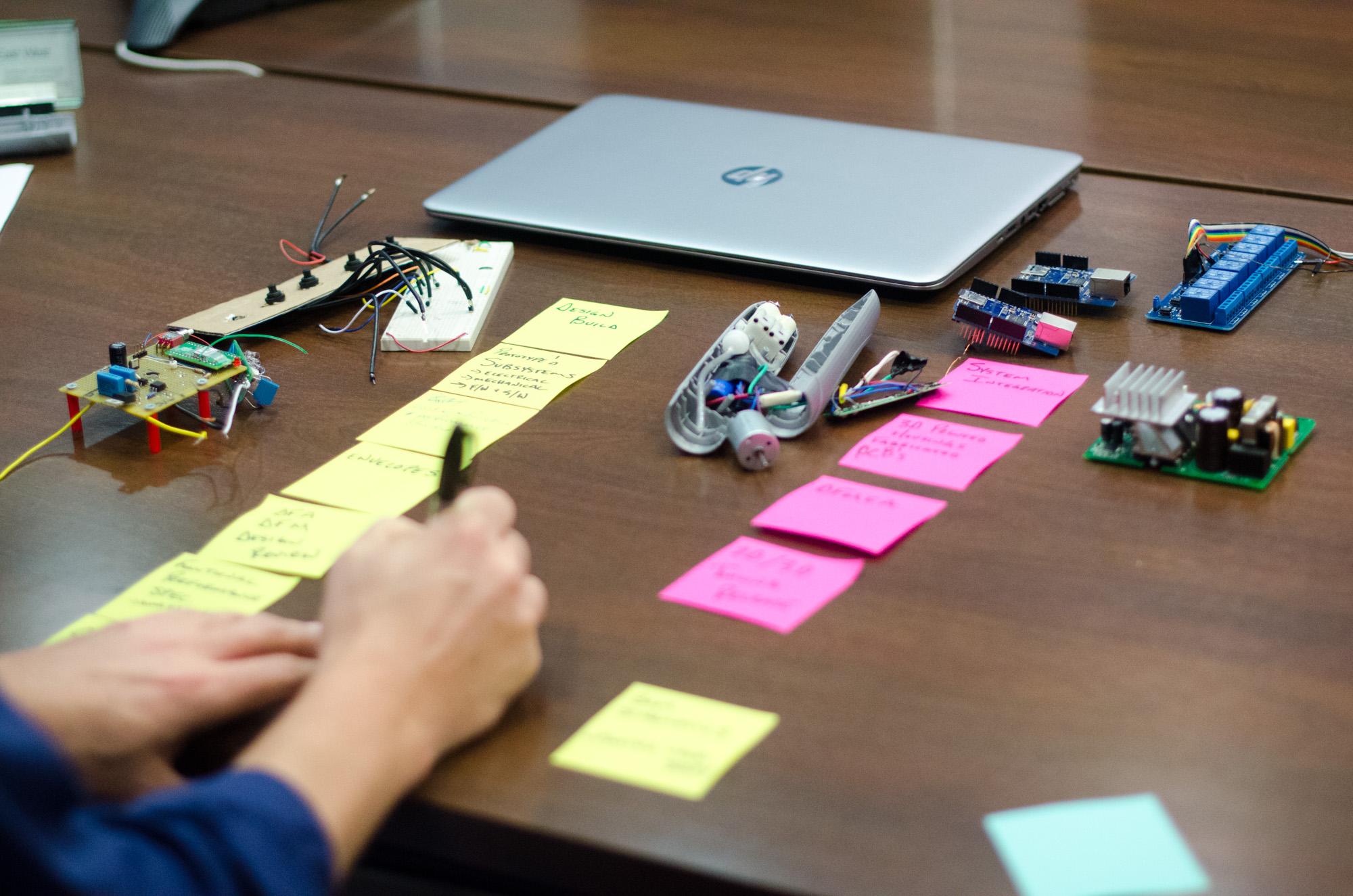
Kaizen is a philosophy that encourages continuous improvement in every area of a business. Rather than making big, sweeping changes that have little to no benefit, Kaizen is a method of incremental improvement. Kaizen is a process that can improve customer satisfaction, productivity, quality, and costs. It is also a great way to increase employee morale.
There are many obstacles to implementing Kaizen in manufacturing
There are some downsides to kaizen implementation. First, implementing Kaizen in a business requires major changes to its management system. Once the changes are in place, it may be difficult to reverse the changes. Second, it is often difficult for businesses to make changes to their work processes, which could be a barrier to kaizen implementation.
Another problem is that many manufacturers work on a "feast-or-famine" basis. When demand drops for their products and they don't have enough people to hire them, the machine shop will be in trouble. In such a case, the machine shop may have to close their doors and lay off employees. Implementing kaizen (continuous improvement) will keep these machine shops from falling into the "feast or feast" cycle. Kaizen will improve the efficiency of a shop and enable it to produce more product.
Kaizen implementation success rate in manufacturing
Statistics show that the success rate of Kaizen implementation in the manufacturing sector is relatively low. Only 10% of manufacturing companies reported positive results following implementation Kaizen. The implementation process does not have to be boring. Implementing kaizen is an essential component of the lean manufacturing process. These are some tips to help increase your manufacturing company's success.
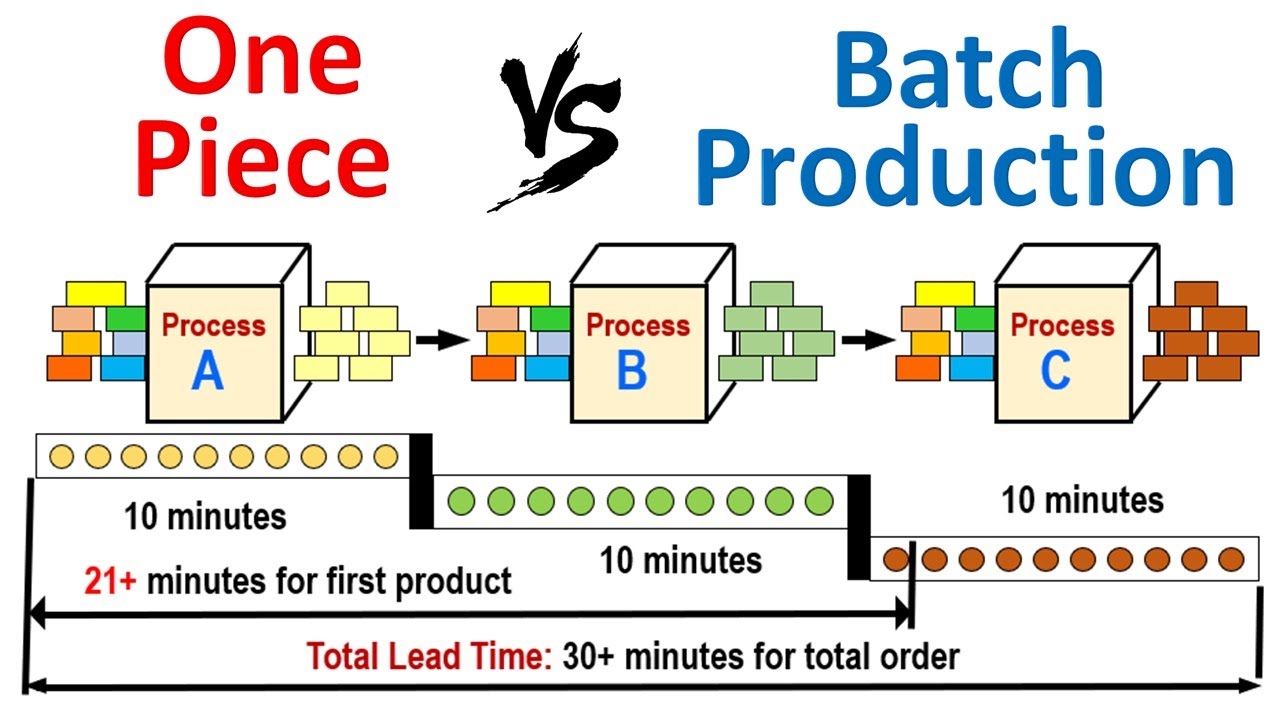
The first step in kaizen is to understand the current state of affairs. In the first step, data are collected and analyzed to identify high priority areas. The next step is to test and verify improvements by performing a comparison of the before-and-after. You can also use benefit-to cost analysis to assess the impact on a particular improvement or the entire kaizen cycle. To assess the program's effectiveness, it is crucial to monitor the results for 60 to 90 days.
FAQ
What are the jobs in logistics?
Logistics can offer many different jobs. Some examples are:
-
Warehouse workers: They load and unload trucks, pallets, and other cargo.
-
Transportation drivers: They drive trucks and trailers and deliver goods and make pick-ups.
-
Freight handlers are people who sort and pack freight into warehouses.
-
Inventory managers – They manage the inventory in warehouses.
-
Sales reps are people who sell products to customers.
-
Logistics coordinators - They organize and plan logistics operations.
-
Purchasing agents – They buy goods or services necessary to run a company.
-
Customer service agents - They answer phone calls and respond to emails.
-
Shipping clerks: They process shipping requests and issue bills.
-
Order fillers: They fill orders based off what has been ordered and shipped.
-
Quality control inspectors: They inspect outgoing and incoming products for any defects.
-
Other - Logistics has many other job opportunities, including transportation supervisors, logistics specialists, and cargo specialists.
How can overproduction in manufacturing be reduced?
It is essential to find better ways to manage inventory to reduce overproduction. This would decrease the time that is spent on inefficient activities like purchasing, storing, or maintaining excess stock. This will allow us to free up resources for more productive tasks.
One way to do this is to adopt a Kanban system. A Kanban Board is a visual display that tracks work progress. Work items are moved through various states to reach their destination in a Kanban system. Each state is assigned a different priority.
When work is completed, it can be transferred to the next stage. A task that is still in the initial stages of a process will be considered complete until it moves on to the next stage.
This allows for work to continue moving forward, while also ensuring that there is no work left behind. Managers can view the Kanban board to see how much work they have done. This allows them to adjust their workflows based on real-time information.
Another way to control inventory levels is to implement lean manufacturing. Lean manufacturing seeks to eliminate waste from every step of the production cycle. Anything that does not contribute to the product's value is considered waste. Some common types of waste include:
-
Overproduction
-
Inventory
-
Packaging that is not necessary
-
Material surplus
Manufacturers can increase efficiency and decrease costs by implementing these ideas.
What is the role of a manager in manufacturing?
Manufacturing managers must ensure that manufacturing processes are efficient, effective, and cost-effective. They should also be aware of any problems within the company and act accordingly.
They must also be able to communicate with sales and marketing departments.
They should also be aware of the latest trends in their industry and be able to use this information to help improve productivity and efficiency.
Is automation important in manufacturing?
Automation is important not only for manufacturers but also for service providers. It allows them to offer services faster and more efficiently. In addition, it helps them reduce costs by reducing human errors and improving productivity.
What is production management?
Production Planning refers to the development of a plan for every aspect of production. This document is designed to make sure everything is ready for when you're ready to shoot. You should also have information to ensure the best possible results on set. It should include information about shooting locations, casting lists, crew details, equipment requirements, and shooting schedules.
The first step in filming is to define what you want. You may have decided where to shoot or even specific locations you want to use. Once you have identified the scenes and locations, you can start to determine which elements are required for each scene. For example, you might decide that you need a car but don't know exactly what model you want. You could look online for cars to see what options are available, and then narrow down your choices by selecting between different makes or models.
Once you have found the right vehicle, you can think about adding accessories. What about additional seating? You might also need someone to help you get around the back. Maybe you want to change the interior color from black to white? These questions will help you determine the exact look and feel of your car. Also, think about what kind of shots you would like to capture. Are you going to be shooting close-ups? Or wide angles? Maybe you want to show your engine or the steering wheel. All of these things will help you identify the exact style of car you want to film.
Once you have determined all of the above, you can move on to creating a schedule. You can use a schedule to determine when and where you need it to be shot. Each day will include the time when you need to arrive at the location, when you need to leave and when you need to return home. This way, everyone knows what they need to do and when. Hire extra staff by booking them ahead of time. It is not worth hiring someone who won’t show up because you didn’t tell him.
You will need to factor in the days that you have to film when creating your schedule. Some projects take only a few days while others can last several weeks. When you are creating your schedule, you should always keep in mind whether you need more than one shot per day or not. Shooting multiple takes over the same location will increase costs and take longer to complete. It's better to be safe than sorry and shoot less takes if you're not certain whether you need more takes.
Budgeting is another important aspect of production planning. It is important to set a realistic budget so you can work within your budget. It is possible to reduce the budget at any time if you experience unexpected problems. However, you shouldn't overestimate the amount of money you will spend. If you underestimate how much something costs, you'll have less money to pay for other items.
Production planning is a very detailed process, but once you understand how everything works together, it becomes easier to plan future projects.
How can I find out more about manufacturing?
Experience is the best way for you to learn about manufacturing. But if that is not possible you can always read books and watch educational videos.
What is the role and responsibility of a Production Planner?
A production planner makes sure all project elements are delivered on schedule, within budget, as well as within the agreed scope. They ensure that the product or service is of high quality and meets client requirements.
Statistics
- In 2021, an estimated 12.1 million Americans work in the manufacturing sector.6 (investopedia.com)
- You can multiply the result by 100 to get the total percent of monthly overhead. (investopedia.com)
- Many factories witnessed a 30% increase in output due to the shift to electric motors. (en.wikipedia.org)
- According to a Statista study, U.S. businesses spent $1.63 trillion on logistics in 2019, moving goods from origin to end user through various supply chain network segments. (netsuite.com)
- [54][55] These are the top 50 countries by the total value of manufacturing output in US dollars for its noted year according to World Bank.[56] (en.wikipedia.org)
External Links
How To
How to use lean manufacturing in the production of goods
Lean manufacturing (or lean manufacturing) is a style of management that aims to increase efficiency, reduce waste and improve performance through continuous improvement. It was created in Japan by Taiichi Ohno during the 1970s and 80s. He received the Toyota Production System award (TPS), from Kanji Toyoda, founder of TPS. The first book published on lean manufacturing was titled "The Machine That Changed the World" written by Michael L. Watkins and published in 1990.
Lean manufacturing, often described as a set and practice of principles, is aimed at improving the quality, speed, cost, and efficiency of products, services, and other activities. It emphasizes reducing defects and eliminating waste throughout the value chain. Just-in-time (JIT), zero defect (TPM), and 5S are all examples of lean manufacturing. Lean manufacturing seeks to eliminate non-value added activities, such as inspection, work, waiting, and rework.
Lean manufacturing not only improves product quality but also reduces costs. Companies can also achieve their goals faster by reducing employee turnover. Lean manufacturing is a great way to manage the entire value chain including customers, suppliers, distributors and retailers as well as employees. Lean manufacturing practices are widespread in many industries. Toyota's philosophy, for example, is what has enabled it to be successful in electronics, automobiles, medical devices, healthcare and chemical engineering as well as paper and food.
Lean manufacturing is based on five principles:
-
Define Value - Determine the value that your business brings to society. Also, identify what sets you apart from your competitors.
-
Reduce Waste - Eliminate any activity that doesn't add value along the supply chain.
-
Create Flow – Ensure that work flows smoothly throughout the process.
-
Standardize and Simplify – Make processes as consistent, repeatable, and as simple as possible.
-
Building Relationships – Establish personal relationships with both external and internal stakeholders.
Lean manufacturing is not a new concept, but it has been gaining popularity over the last few years due to a renewed interest in the economy following the global financial crisis of 2008. Many businesses have adopted lean manufacturing techniques to help them become more competitive. Many economists believe lean manufacturing will play a major role in economic recovery.
Lean manufacturing is becoming a popular practice in automotive. It has many advantages. These include better customer satisfaction and lower inventory levels. They also result in lower operating costs.
Lean manufacturing can be applied to almost every aspect of an organization. This is because it ensures efficiency and effectiveness in all stages of the value chain.
There are three main types in lean manufacturing
-
Just-in Time Manufacturing, (JIT): This kind of lean manufacturing is also commonly known as "pull-systems." JIT refers to a system in which components are assembled at the point of use instead of being produced ahead of time. This approach aims to reduce lead times, increase the availability of parts, and reduce inventory.
-
Zero Defects Manufacturing (ZDM): ZDM focuses on ensuring that no defective units leave the manufacturing facility. It is better to repair a part than have it removed from the production line if it needs to be fixed. This is also true for finished products that require minor repairs before shipping.
-
Continuous Improvement (CI): CI aims to improve the efficiency of operations by continuously identifying problems and making changes in order to eliminate or minimize waste. Continuous improvement involves continuous improvement of processes and people as well as tools.