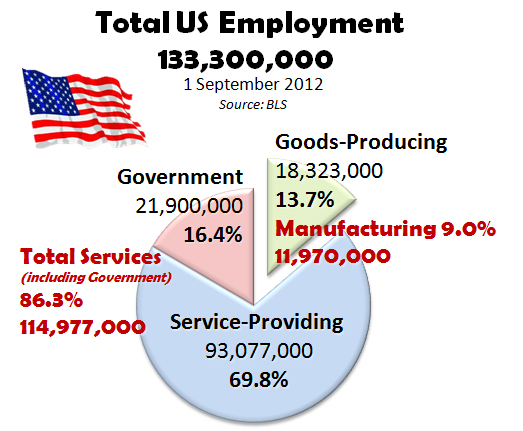
A material manager is responsible for the purchase and delivery of materials. Typically, they come from inventory or raw materials management. It is important that they are knowledgeable about the types of raw material required to produce a product. They must also be resourceful in searching for these materials. They should also have strong relationships with vendors to get the best price and delivery rates. It is also important to consider the salary of a material manager. These are some tips to help get the job.
Job description
Materials managers are responsible for managing stock and purchasing. A materials manager must be able to solve problems and have a good understanding of stock management. A material manager is responsible for the management of inventory, budgets, efficiencies and other tasks. As well as managing inventory, the position must coordinate and supervise subordinates. A master's degree is required for this position. A materials manager must have had experience in a similar role.
A materials manager usually holds a bachelor’s degree in business administration, or another related field. However, if the position requires a supervisor, a master's degree in a related field is advantageous. While an advanced degree is more beneficial than a job experience, education is still a valuable asset. Materials managers should have at minimum three years of experience working in a manufacturing environment before they can apply for a managerial position.
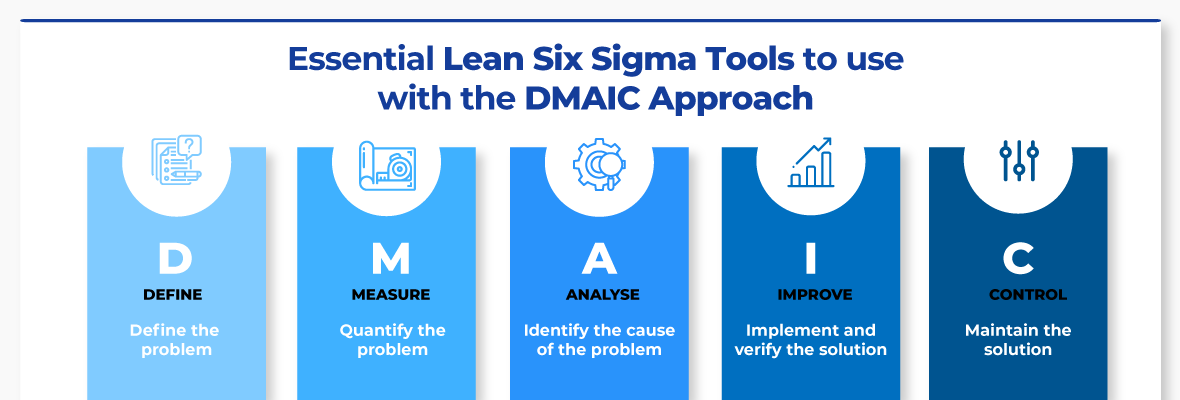
Responsibilities
The role of a materials manager is to evaluate existing projects and determine the material requirements for production. He or she also keeps track of inventory through the company's supply chain management system, and may be responsible for maintaining stock of spare parts for repairing faulty products. He or she may be responsible for training employees in the appropriate use of inventory control systems. These positions are critical in many companies. However not all of them require extensive education.
Job description: A material manger oversees the company's procurement. They also oversee the storage and distribution. This job requires expertise in supply chain management, inventory controls, and logistics. Experience in these areas is an advantage. They will also be working closely with vendors and purchasing departments to establish requirements and plan distribution. These positions require a bachelor's level in business, as well strong analytical abilities.
Education required
If you are considering a career as a material manager, you should be aware of the educational requirements for this position. This position requires excellent management skills as well as a thorough understanding of logistics. As a material manager, you will work with QC personnel and higher-level managers. Plan functions and delegating to subordinates are some of the job duties. As a manager, it is important to be able and able judge the performance of subordinates as well as foster harmonious working relationships.
Materials managers generally have a bachelor's in a related field. For companies to hire material managers with this education, they may require at least two-three years of experience. Higher-ranking roles may require more education. Many material managers hold certifications, such as those offered by the American Purchasing Society (CPSCP) and the APICS (the Association of Purchasing Professionals).
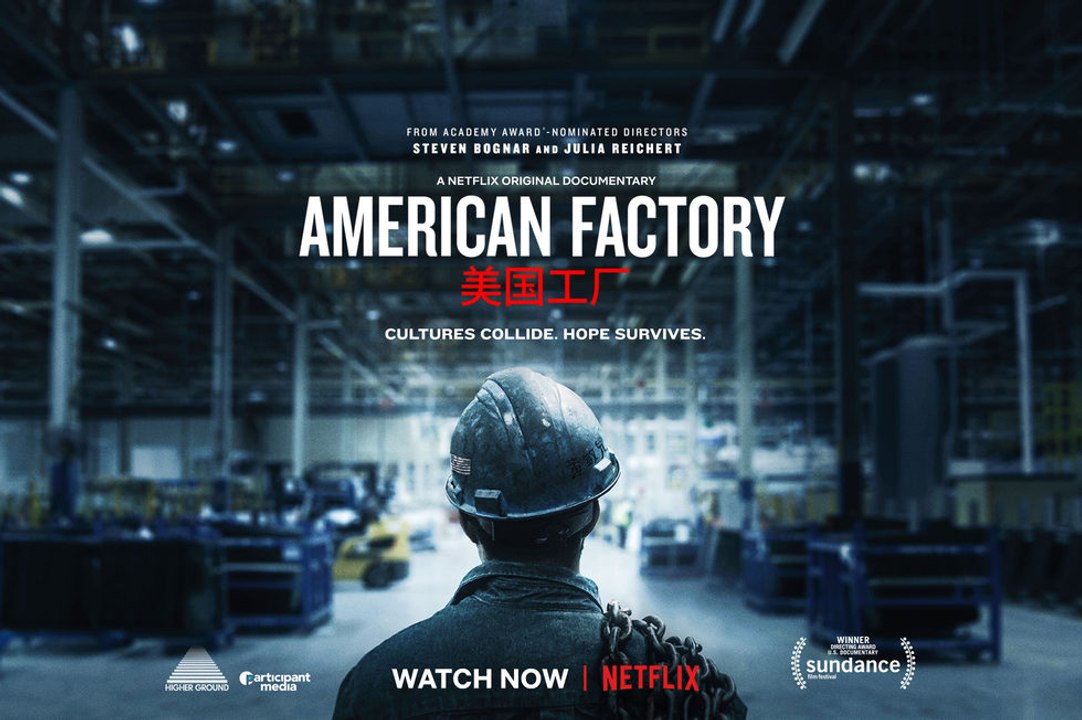
Salary
The average salary for Materials Managers is approximately $78,500. This figure is based off 106 TurboTax user salaries. It includes taxable wages, tips, and bonuses. The exact salary will vary depending on education and experience. Salary data is adjusted to reflect inflation each year. You can read the following to learn about the average salary for a Materials Manager job.
A background in management is required to become a materials manager. A good knowledge of logistics, receiving and shipping is essential. You should have a good understanding of the industry that you want to work in if you are in manufacturing. This will help you negotiate the most favorable prices with suppliers. The type of training and experience a materials manager has will determine the salary they earn.
FAQ
What is production planning?
Production Planning involves developing a plan for all aspects of the production, including scheduling, budgeting, casting, crew, location, equipment, props, etc. This document is designed to make sure everything is ready for when you're ready to shoot. This document should include information about how to achieve the best results on-set. This includes shooting schedules, locations, cast lists, crew details, and equipment requirements.
First, you need to plan what you want to film. You may already know where you want the film to be shot, or perhaps you have specific locations and sets you wish to use. Once you have determined your scenes and locations, it is time to start figuring out the elements that you will need for each scene. For example, you might decide that you need a car but don't know exactly what model you want. You could look online for cars to see what options are available, and then narrow down your choices by selecting between different makes or models.
Once you have found the right vehicle, you can think about adding accessories. You might need to have people in the front seats. You might also need someone to help you get around the back. Maybe you'd like to change the interior from black to a white color. These questions will help guide you in determining the ideal look and feel for your car. Also, think about what kind of shots you would like to capture. You will be filming close-ups and wide angles. Maybe you want the engine or the steering wheels to be shown. All of these things will help you identify the exact style of car you want to film.
Once you have all the information, you are ready to create a plan. A schedule will tell you when you need to start shooting and when you need to finish. The schedule will show you when to get there, what time to leave, and when to return home. This way, everyone knows what they need to do and when. You can also make sure to book extra staff in advance if you have to hire them. There is no point in hiring someone who won't turn up because you didn't let him know.
You will need to factor in the days that you have to film when creating your schedule. Some projects only take one or two days, while others may last weeks. When creating your schedule, be aware of whether you need more shots per day. Multiple takes at the same place will result in higher costs and longer completion times. It's better to be safe than sorry and shoot less takes if you're not certain whether you need more takes.
Budgeting is another important aspect of production planning. As it will allow you and your team to work within your financial means, setting a realistic budget is crucial. It is possible to reduce the budget at any time if you experience unexpected problems. But, don't underestimate how much money you'll spend. You will end up spending less money if you underestimate the cost of something.
Production planning can be a complex process. However, once you know how everything works together it will become easier to plan future projects.
What is the difference between a production planner and a project manager?
A production planner is more involved in the planning phase of the project than a project manger.
Is automation important in manufacturing?
Automation is important not only for manufacturers but also for service providers. It enables them to provide services faster and more efficiently. It also helps to reduce costs and improve productivity.
Why automate your factory?
Modern warehouses are increasingly dependent on automation. Increased demand for efficient and faster delivery has resulted in a rise in e-commerce.
Warehouses must adapt quickly to meet changing customer needs. In order to do this, they need to invest in technology. Automation warehouses can bring many benefits. Here are some benefits of investing in automation
-
Increases throughput/productivity
-
Reduces errors
-
Improves accuracy
-
Safety increases
-
Eliminates bottlenecks
-
Companies can scale more easily
-
Increases efficiency of workers
-
It gives visibility to everything that happens inside the warehouse
-
Enhances customer experience
-
Improves employee satisfaction
-
Reduces downtime and improves uptime
-
Ensures quality products are delivered on time
-
Removes human error
-
Helps ensure compliance with regulations
What is the difference between Production Planning, Scheduling and Production Planning?
Production Planning (PP), is the process of deciding what production needs to take place at any given time. This is accomplished by forecasting the demand and identifying production resources.
Scheduling refers the process by which tasks are assigned dates so that they can all be completed within the given timeframe.
What skills does a production planner need?
To become a successful production planner, you need to be organized, flexible, and able to multitask. You must also be able to communicate effectively with clients and colleagues.
What does the term manufacturing industries mean?
Manufacturing Industries are those businesses that make products for sale. Consumers are the people who purchase these products. To accomplish this goal, these companies employ a range of processes including distribution, sales, management, and production. They manufacture goods from raw materials using machines and other equipment. This covers all types of manufactured goods including clothing, food, building supplies and furniture, as well as electronics, tools, machinery, vehicles and pharmaceuticals.
Statistics
- (2:04) MTO is a production technique wherein products are customized according to customer specifications, and production only starts after an order is received. (oracle.com)
- According to a Statista study, U.S. businesses spent $1.63 trillion on logistics in 2019, moving goods from origin to end user through various supply chain network segments. (netsuite.com)
- It's estimated that 10.8% of the U.S. GDP in 2020 was contributed to manufacturing. (investopedia.com)
- In 2021, an estimated 12.1 million Americans work in the manufacturing sector.6 (investopedia.com)
- You can multiply the result by 100 to get the total percent of monthly overhead. (investopedia.com)
External Links
How To
How to Use the Just In Time Method in Production
Just-intime (JIT), which is a method to minimize costs and maximize efficiency in business process, is one way. This is where you have the right resources at the right time. This means that only what you use is charged to your account. Frederick Taylor developed the concept while working as foreman in early 1900s. He observed how workers were paid overtime if there were delays in their work. He then concluded that if he could ensure that workers had enough time to do their job before starting to work, this would improve productivity.
JIT is a way to plan ahead and make sure you don't waste any money. It is important to look at your entire project from beginning to end and ensure that you have enough resources to handle any issues that may arise. If you anticipate that there might be problems, you'll have enough people and equipment to fix them. This will ensure that you don't spend more money on things that aren't necessary.
There are many JIT methods.
-
Demand-driven: This is a type of JIT where you order the parts/materials needed for your project regularly. This will enable you to keep track of how much material is left after you use it. You'll also be able to estimate how long it will take to produce more.
-
Inventory-based: This is a type where you stock the materials required for your projects in advance. This allows you to forecast how much you will sell.
-
Project-driven : This is a method where you make sure that enough money is set aside to pay the project's cost. You will be able to purchase the right amount of materials if you know what you need.
-
Resource-based JIT: This type of JIT is most commonly used. Here you can allocate certain resources based purely on demand. You might assign more people to help with orders if there are many. If you don’t have many orders you will assign less people to the work.
-
Cost-based: This is a similar approach to resource-based but you are not only concerned with how many people you have, but also how much each one costs.
-
Price-based: This is similar to cost-based but instead of looking at individual workers' salaries, you look at the total company price.
-
Material-based is an alternative to cost-based. Instead of looking at the total cost in the company, this method focuses on the average amount of raw materials that you consume.
-
Time-based: This is another variation of resource-based JIT. Instead of worrying about how much each worker costs, you can focus on how long the project takes.
-
Quality-based JIT: Another variation on resource-based JIT. Instead of looking at the labor costs and time it takes to make a product, think about its quality.
-
Value-based JIT: One of the most recent forms of JIT. In this instance, you are not concerned about the product's performance or meeting customer expectations. Instead, you are focused on adding value to the marketplace.
-
Stock-based: This stock-based method focuses on the actual quantity of products being made at any given time. This is used to increase production and minimize inventory.
-
Just-in-time planning (JIT): This is a combination JIT and supply-chain management. It is the process that schedules the delivery of components within a short time of their order. It's important because it reduces lead times and increases throughput.