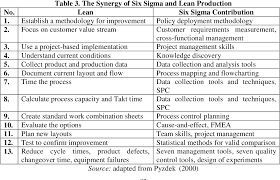
Whether you are a military family looking for affordable housing or a homeowner looking to save money, the HEROES PROGRAM can provide the help you need. This program is a collaboration between radio stations and web networks across the country to recognize acts of bravery from our servicemen, women, and children. It also connects military families to legal professionals who are experts in military law and child support.
Heroes To Heroes (501(c)(3)) is a nonprofit that offers peer support to veterans and helps them prevent suicide. They offer a 12-month program that focuses on emotional strength and a 10-day trip in Israel. In addition, Heroes To Heroes also helps veterans who have suffered Moral Injury. It also provides suicide prevention training and peer support to veterans who have experienced PTSD and combat injuries.
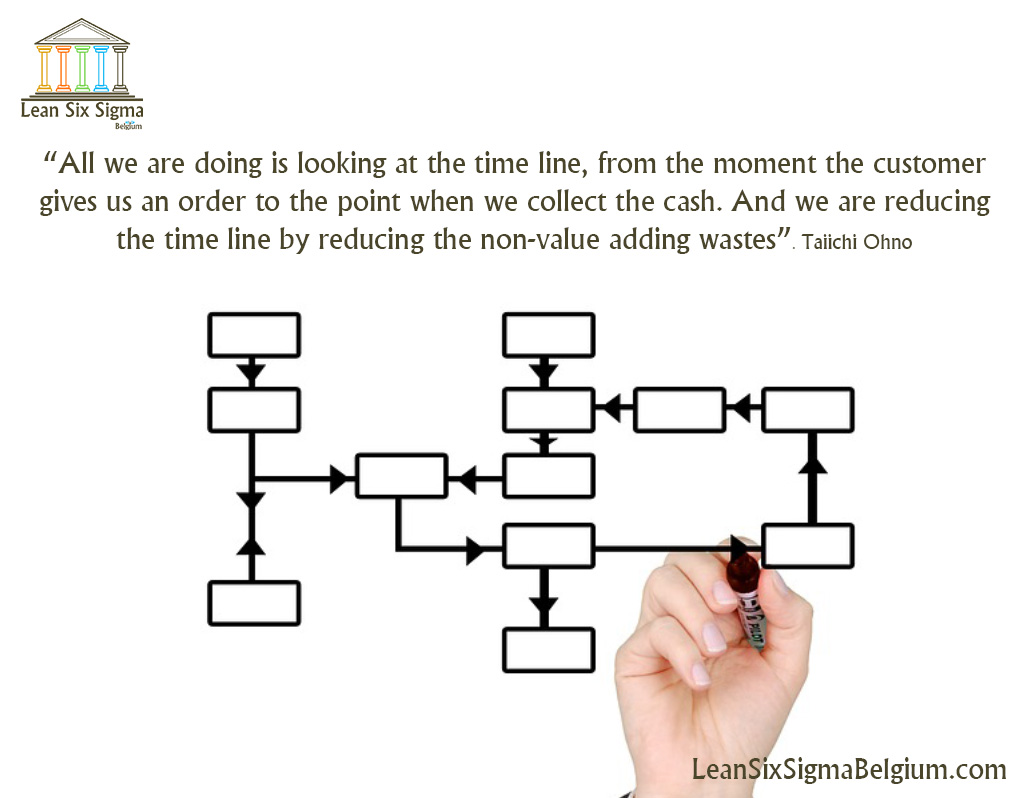
Hiring Our Heroes works to find job opportunities for our nation's veterans. The program helps to identify people from all backgrounds including veterans, active-duty military families, as well as other members the military community. The program also helps veterans find jobs, and offers guidance to military families, particularly those who are raising children. In addition, the organization offers a scholarship for children of veterans, as well as other forms of assistance.
Heroes MAKE America helps veterans identify and place them in jobs. It also offers career readiness training, certification and career readiness preparation. This program has connected 250 companies with its graduates in 42 states. They are working with local technical colleges and organizations to help veterans find careers. The program has expanded since COVID-19, and will soon launch a training site in Georgia. Fort Riley is also home to many of its programs. The program has placed graduates in 136 different military occupation specialties. Veterans looking for employment in the manufacturing sector will find this program a valuable resource.
Fort Riley will continue to develop Heroes MAKE America programs and will add new features in 2021. They will feature virtual reality simulations. This virtual training program will allow transitioning military personnel to take part, even if their computer is not available. They will be able connect with other veterans who participated in the program. The program will grow after COVID-19 and will help veterans find work in the manufacturing industry.
The HEROES leadership project is a group that brings together experience and talent to build a vibrant community for youth. The group creates an environment that youth can feel secure and supported. It is also part in Re-Envisioning Foster Care in America Movement. Members contribute their experiences, talents, and voice to help create a more supportive environment for youth.
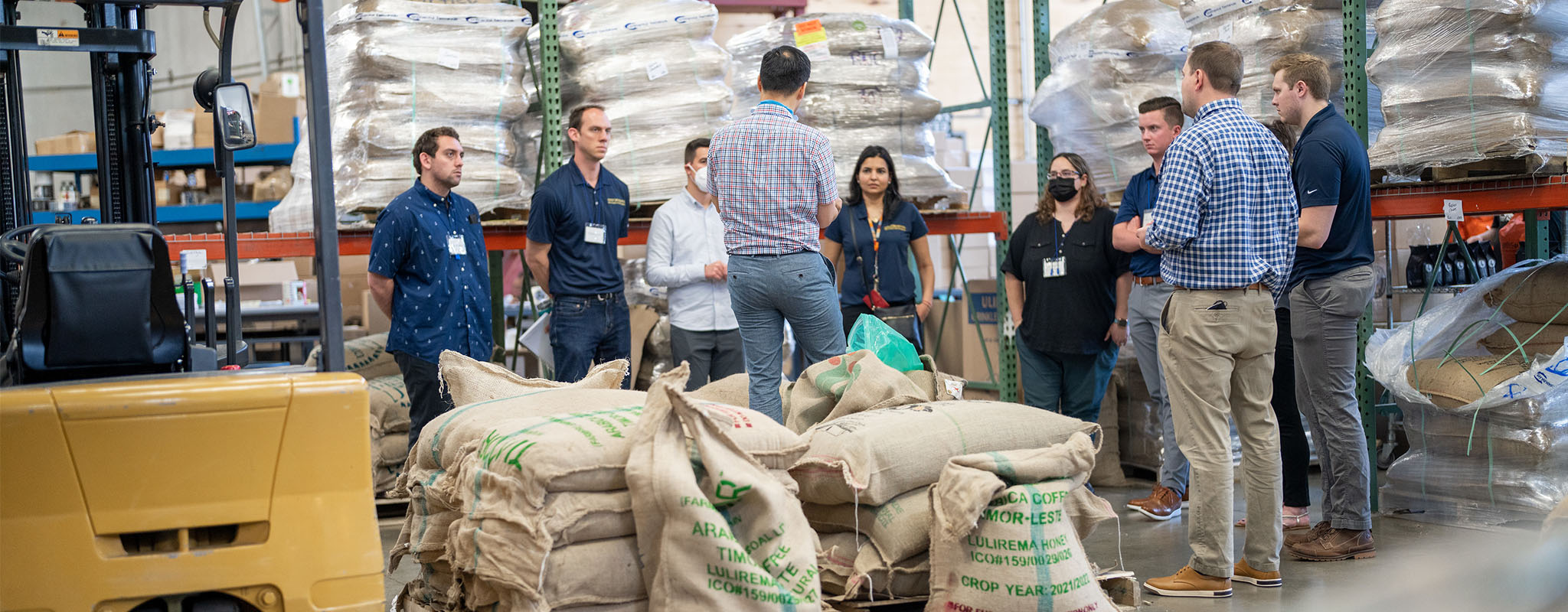
The Homes for Heroes program also offers discounts on real estate agent commissions and home inspection fees. The program is a huge success and has spread nationally. The program offers discounts to teachers, active and retired military personnel, and health-care professionals. On average, a Hero saves about $2400.
FAQ
What does warehouse refer to?
A warehouse is an area where goods are stored before being sold. It can be an outdoor or indoor area. In some cases it could be both indoors and outdoors.
What are the responsibilities of a logistic manager?
Logistics managers make sure all goods are delivered on schedule and without damage. This is accomplished by using the experience and knowledge gained from working with company products. He/she should make sure that enough stock is on hand to meet the demands.
What is the role of a production manager?
A production planner ensures all aspects of the project are delivered on time, within budget, and within scope. They also ensure the quality of the product and service meets the client's requirements.
Can some manufacturing processes be automated?
Yes! Automation has been around since ancient times. The Egyptians invented the wheel thousands of years ago. We now use robots to help us with assembly lines.
Robotics is used in many manufacturing processes today. They include:
-
Robots for assembly line
-
Robot welding
-
Robot painting
-
Robotics inspection
-
Robots that make products
Manufacturing can also be automated in many other ways. 3D printing is a way to make custom products quickly and without waiting weeks or months for them to be manufactured.
Statistics
- (2:04) MTO is a production technique wherein products are customized according to customer specifications, and production only starts after an order is received. (oracle.com)
- Many factories witnessed a 30% increase in output due to the shift to electric motors. (en.wikipedia.org)
- It's estimated that 10.8% of the U.S. GDP in 2020 was contributed to manufacturing. (investopedia.com)
- According to a Statista study, U.S. businesses spent $1.63 trillion on logistics in 2019, moving goods from origin to end user through various supply chain network segments. (netsuite.com)
- In 2021, an estimated 12.1 million Americans work in the manufacturing sector.6 (investopedia.com)
External Links
How To
How to Use the 5S to Increase Productivity In Manufacturing
5S stands to stand for "Sort", “Set In Order", “Standardize", and "Store". Toyota Motor Corporation invented the 5S strategy in 1954. This methodology helps companies improve their work environment to increase efficiency.
The idea behind standardizing production processes is to make them repeatable and measurable. Cleaning, sorting and packing are all done daily. These actions allow workers to perform their job more efficiently, knowing what to expect.
Implementing 5S involves five steps: Sort, Set in Order, Standardize Separate, Store, and Each step has a different action and leads to higher efficiency. For example, when you sort things, you make them easy to find later. When you set items in an order, you put items together. Then, after you separate your inventory into groups, you store those groups in containers that are easy to access. Finally, when you label your containers, you ensure everything is labeled correctly.
Employees must be able to critically examine their work practices. Employees need to understand the reasons they do certain jobs and determine if there is a better way. To be successful in the 5S system, employees will need to acquire new skills and techniques.
The 5S method not only increases efficiency but also boosts morale and teamwork. As they begin to see improvements, they feel motivated to continue working towards the goal of achieving higher levels of efficiency.