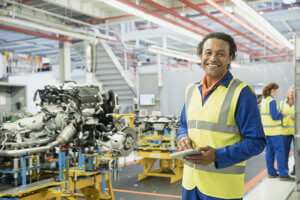
In order to plan demand, you must predict the future demand of a certain product or service. It is a vital part of supply chain management, as it helps businesses meet their customers' needs while also maximizing profits and efficiency.
What is Demand Planning?
Planning demand involves analyzing data, including sales data and inventory information, to forecast future demand for a given product or service. It can be an extremely complex process, involving many different departments.
What is a Demand Planner?
A demand planner works as part of an organization's supply-chain team. This person uses his or her knowledge of the industry to predict market trends. They then create a demand plan that includes ideal inventory levels, shipping timelines, and all the steps a company needs to take to meet demand.
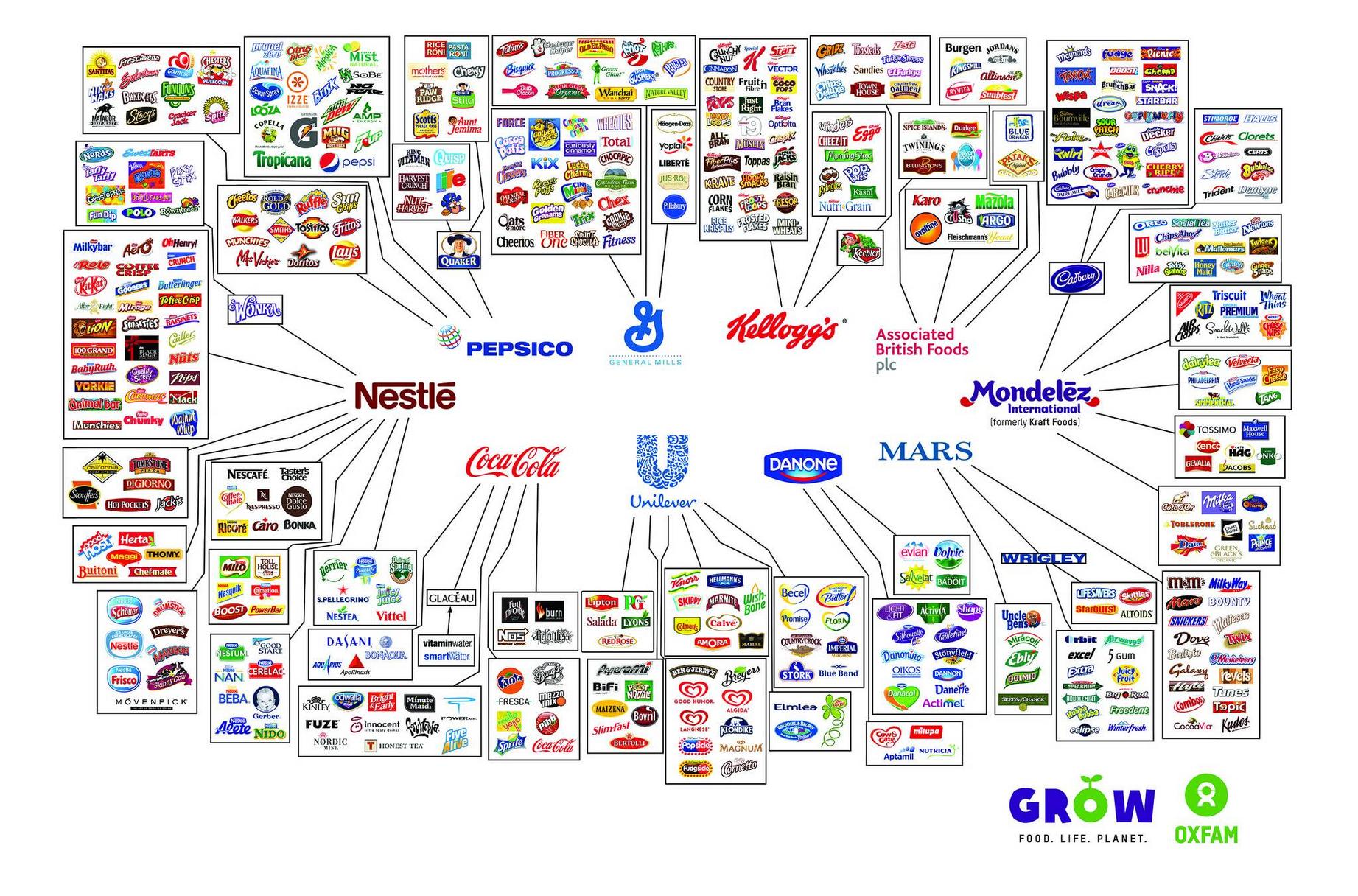
What Are the Best Tools to Plan Demand?
The most effective demand planning tools are those that provide end-to-end visibility across a company's entire supply chain. The demand planners are then able to track the demand and analyze it in real-time.
What is a good way to predict the demand for a product?
The sales data provided by a business's team is an excellent way to forecast demand. This data could help you pinpoint issues that your company's sales team might have with its customers. It may also lead to changes made in your demand plans.
A statistical analysis can be used to establish the relationship between sales and inventories. The accuracy of demand plans can be improved by using analytics to discover these relationships.
What are the most common mistakes in demand planning?
Demand planning can seem like a daunting task. It takes time and energy to do it right. There are a number of things that can go wrong if your demand plan isn't accurate, including excess inventory that locks up working capital or increases inventory carrying costs, which can cost the company money and negatively impact customers.
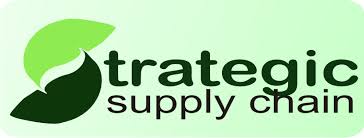
What are the most common skills that a demand planner requires?
A demand planner needs to have strong analytical and management skills. They must be able analyze large data sets, and then make informed decisions. They should also have the ability to reach a consensus and work well with others.
What Are Some of The Most Valuable Qualities in Demand Forecasting?
A great demand planner should be skilled with both people and technology. This is because they will be working with various teams to develop a forecasting model, and they need to be able to communicate effectively with these teams.
In addition to analyzing a wide range of statistical data, a demand planner should be skilled with the Delphi method, which allows them to solicit feedback from outside experts or facilitators who are not inside the company. This method is particularly useful when limited data are available and you want to hear more opinions on a certain issue.
FAQ
What do you mean by warehouse?
A warehouse or storage facility is where goods are stored before they are sold. It can be either an indoor or outdoor space. Sometimes, it can be both an indoor and outdoor space.
What skills is required for a production planner?
A production planner must be organized, flexible, and able multitask to succeed. It is also important to be able communicate with colleagues and clients.
How does manufacturing avoid bottlenecks in production?
To avoid production bottlenecks, ensure that all processes run smoothly from the moment you receive your order to the time the product ships.
This includes both quality control and capacity planning.
Continuous improvement techniques like Six Sigma are the best way to achieve this.
Six Sigma is a management system used to improve quality and reduce waste in every aspect of your organization.
It emphasizes consistency and eliminating variance in your work.
How can overproduction in manufacturing be reduced?
The key to reducing overproduction lies in developing better ways to manage inventory. This would reduce the time needed to manage inventory. This could help us free up our time for other productive tasks.
This can be done by using a Kanban system. A Kanban board, a visual display to show the progress of work, is called a Kanban board. Kanban systems allow work items to move through different states until they reach their final destination. Each state represents a different priority.
If work is moving from one stage to the other, then the current task can be completed and moved on to the next. If a task is still in its beginning stages, it will continue to be so until it reaches the end.
This allows work to move forward and ensures that no work is missed. Managers can see how much work has been done and the status of each task at any time with a Kanban Board. This allows them to adjust their workflows based on real-time information.
Lean manufacturing is another way to manage inventory levels. Lean manufacturing seeks to eliminate waste from every step of the production cycle. Anything that does nothing to add value to a product is waste. There are several types of waste that you might encounter:
-
Overproduction
-
Inventory
-
Unnecessary packaging
-
Overstock materials
Manufacturers can increase efficiency and decrease costs by implementing these ideas.
Are there ways to automate parts of manufacturing?
Yes! Yes! Automation has existed since ancient times. The Egyptians created the wheel thousands years ago. We now use robots to help us with assembly lines.
Actually, robotics can be used in manufacturing for many purposes. These include:
-
Automated assembly line robots
-
Robot welding
-
Robot painting
-
Robotics inspection
-
Robots create products
There are many other examples of how manufacturing could benefit from automation. For instance, 3D printing allows us make custom products and not have to wait for months or even weeks to get them made.
What is the importance of logistics in manufacturing?
Logistics are essential to any business. Logistics can help you achieve amazing results by helping to manage product flow from raw materials to finished products.
Logistics play a key role in reducing expenses and increasing efficiency.
Statistics
- In 2021, an estimated 12.1 million Americans work in the manufacturing sector.6 (investopedia.com)
- According to a Statista study, U.S. businesses spent $1.63 trillion on logistics in 2019, moving goods from origin to end user through various supply chain network segments. (netsuite.com)
- According to the United Nations Industrial Development Organization (UNIDO), China is the top manufacturer worldwide by 2019 output, producing 28.7% of the total global manufacturing output, followed by the United States, Japan, Germany, and India.[52][53] (en.wikipedia.org)
- In the United States, for example, manufacturing makes up 15% of the economic output. (twi-global.com)
- [54][55] These are the top 50 countries by the total value of manufacturing output in US dollars for its noted year according to World Bank.[56] (en.wikipedia.org)
External Links
How To
How to Use 5S for Increasing Productivity in Manufacturing
5S stands for "Sort", "Set In Order", "Standardize", "Separate" and "Store". Toyota Motor Corporation invented the 5S strategy in 1954. It assists companies in improving their work environments and achieving higher efficiency.
This method has the basic goal of standardizing production processes to make them repeatable. This means that every day tasks such cleaning, sorting/storing, packing, and labeling can be performed. Because workers know what they can expect, this helps them perform their jobs more efficiently.
There are five steps that you need to follow in order to implement 5S. Each step is a different action that leads to greater efficiency. By sorting, for example, you make it easy to find the items later. You arrange items by placing them in an order. You then organize your inventory in groups. Make sure everything is correctly labeled when you label your containers.
Employees need to reflect on how they do their jobs. Employees must understand why they do certain tasks and decide if there's another way to accomplish them without relying on the old ways of doing things. They must learn new skills and techniques in order to implement the 5S system.
The 5S method not only increases efficiency but also boosts morale and teamwork. They will feel motivated to strive for higher levels of efficiency once they start to see results.