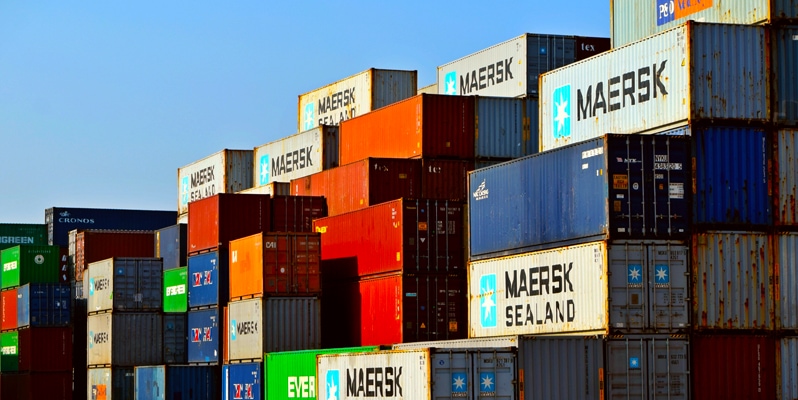
It is vital to have a talent supply chain that works well. This will ensure your company gets the best talent available at the right time and at the right price. It is also key to achieving competitive advantage in the global market.
It takes time to build a strong supply chain of talent. It requires constant monitoring of the talent pool and assessment. It also requires collaboration between several groups including HR, IT, and operations leaders. Ultimately, it requires a common business strategy to ensure that the talent supply chain is in alignment with the organization's goals and objectives.
Today, diversity is one of the greatest challenges HR leaders face. Companies must reevaluate their HR processes in order to attract and keep the best talent. Companies must adapt to new technologies to accomplish this. Modern technology can make it easier to find talent and reduce the time involved in recruitment. Your organization can identify and optimize talent using data. This will also help identify common skills within your supply chain.
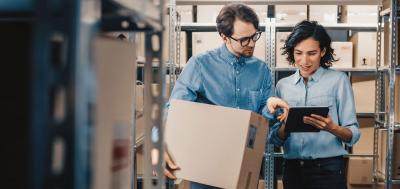
Identifying talent pools will be the first step. Once you have identified the talent pools, you will be able to use the data you have for evaluating your needs. Your talent pools can help you identify the areas where you need to be successful in recruiting. You can also upskill your employees to round out your talent pipeline.
Your organization may be able to track changes in political trends and market forecasts by making use of existing data. These data can also provide insights and help you identify talent strategies that are aligned with your business goals. You can also use existing data to maintain candidate profiles.
Using a talent supply chain can help your organization improve the quality of your workforce and increase its retention rate. The talent supply chain can help you reduce costs and streamline your business. By using the talent supply chains, you can decrease the time required to find talent and also maintain a productive and stable workforce.
A talent supply network can be used to solve short-term problems, such IT projects of major importance, and long-term issues, such as recruiting or retaining employees. A talent supply system can be used to support regions that are not able to find employment. A global talent supply network can offer a greater pool of diverse candidates and cut down on the time required for talent retention and hiring.
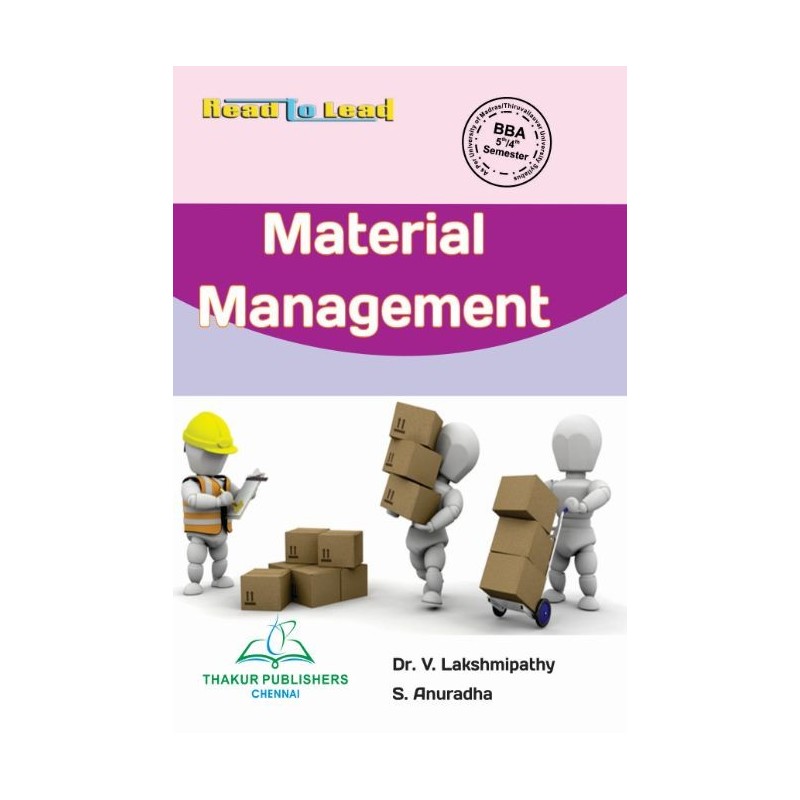
Historically, HR and other functions have worked independently to secure talent. Today's companies must compete on the global market. This means that they must have access to the best and most sought-after talent from all sections of their workforce. It is essential to identify the skills needed by the organization to ensure that the talent supply chains are in line with company goals.
Companies are now challenged to adapt their business models with the help of technology. These changes have forced companies to reevaluate and adapt their workforce, acquire new skills, and improve their agility. This new talent acquisition strategy is an important part of the future of many companies.
FAQ
What are the 7 R's of logistics?
The acronym "7R's" of Logistics stands for seven principles that underpin logistics management. It was created by the International Association of Business Logisticians and published in 2004 under its "Seven Principles of Logistics Management".
The following letters make up the acronym:
-
Responsive - ensure all actions are legal and not harmful to others.
-
Reliable - You can have confidence that you will fulfill your promises.
-
Be responsible - Use resources efficiently and avoid wasting them.
-
Realistic - Take into consideration all aspects of operations including cost-effectiveness, environmental impact, and other factors.
-
Respectful – Treat others fairly and equitably.
-
Reliable - Find ways to save money and increase your productivity.
-
Recognizable is a company that provides customers with value-added solutions.
What does it mean to be a manufacturer?
Manufacturing Industries are businesses that produce products for sale. Consumers are those who purchase these products. This is accomplished by using a variety of processes, including production, distribution and retailing. They manufacture goods from raw materials using machines and other equipment. This covers all types of manufactured goods including clothing, food, building supplies and furniture, as well as electronics, tools, machinery, vehicles and pharmaceuticals.
How can I learn about manufacturing?
Hands-on experience is the best way to learn more about manufacturing. You can read books, or watch instructional videos if you don't have the opportunity to do so.
How can manufacturing reduce production bottlenecks?
You can avoid bottlenecks in production by making sure that everything runs smoothly throughout the production cycle, from the moment you receive an order to the moment the product is shipped.
This includes planning for both capacity requirements and quality control measures.
Continuous improvement techniques such Six Sigma can help you achieve this.
Six Sigma management is a system that improves quality and reduces waste within your organization.
It's all about eliminating variation and creating consistency in work.
Statistics
- Many factories witnessed a 30% increase in output due to the shift to electric motors. (en.wikipedia.org)
- In the United States, for example, manufacturing makes up 15% of the economic output. (twi-global.com)
- Job #1 is delivering the ordered product according to specifications: color, size, brand, and quantity. (netsuite.com)
- According to a Statista study, U.S. businesses spent $1.63 trillion on logistics in 2019, moving goods from origin to end user through various supply chain network segments. (netsuite.com)
- According to the United Nations Industrial Development Organization (UNIDO), China is the top manufacturer worldwide by 2019 output, producing 28.7% of the total global manufacturing output, followed by the United States, Japan, Germany, and India.[52][53] (en.wikipedia.org)
External Links
How To
How to use 5S in Manufacturing to Increase Productivity
5S stands for "Sort", 'Set In Order", 'Standardize', & Separate>. Toyota Motor Corporation developed the 5S method in 1954. It improves the work environment and helps companies to achieve greater efficiency.
The basic idea behind this method is to standardize production processes, so they become repeatable, measurable, and predictable. It means tasks like cleaning, sorting or packing, labeling, and storing are done every day. Because workers know what they can expect, this helps them perform their jobs more efficiently.
Implementing 5S involves five steps: Sort, Set in Order, Standardize Separate, Store, and Each step requires a different action, which increases efficiency. Sorting things makes it easier to find them later. When items are ordered, they are put together. Once you have separated your inventory into groups and organized them, you will store these groups in easily accessible containers. Labeling your containers will ensure that everything is correctly labeled.
This requires employees to critically evaluate how they work. Employees need to understand the reasons they do certain jobs and determine if there is a better way. They must learn new skills and techniques in order to implement the 5S system.
In addition to increasing efficiency, the 5S method also improves morale and teamwork among employees. As they begin to see improvements, they feel motivated to continue working towards the goal of achieving higher levels of efficiency.