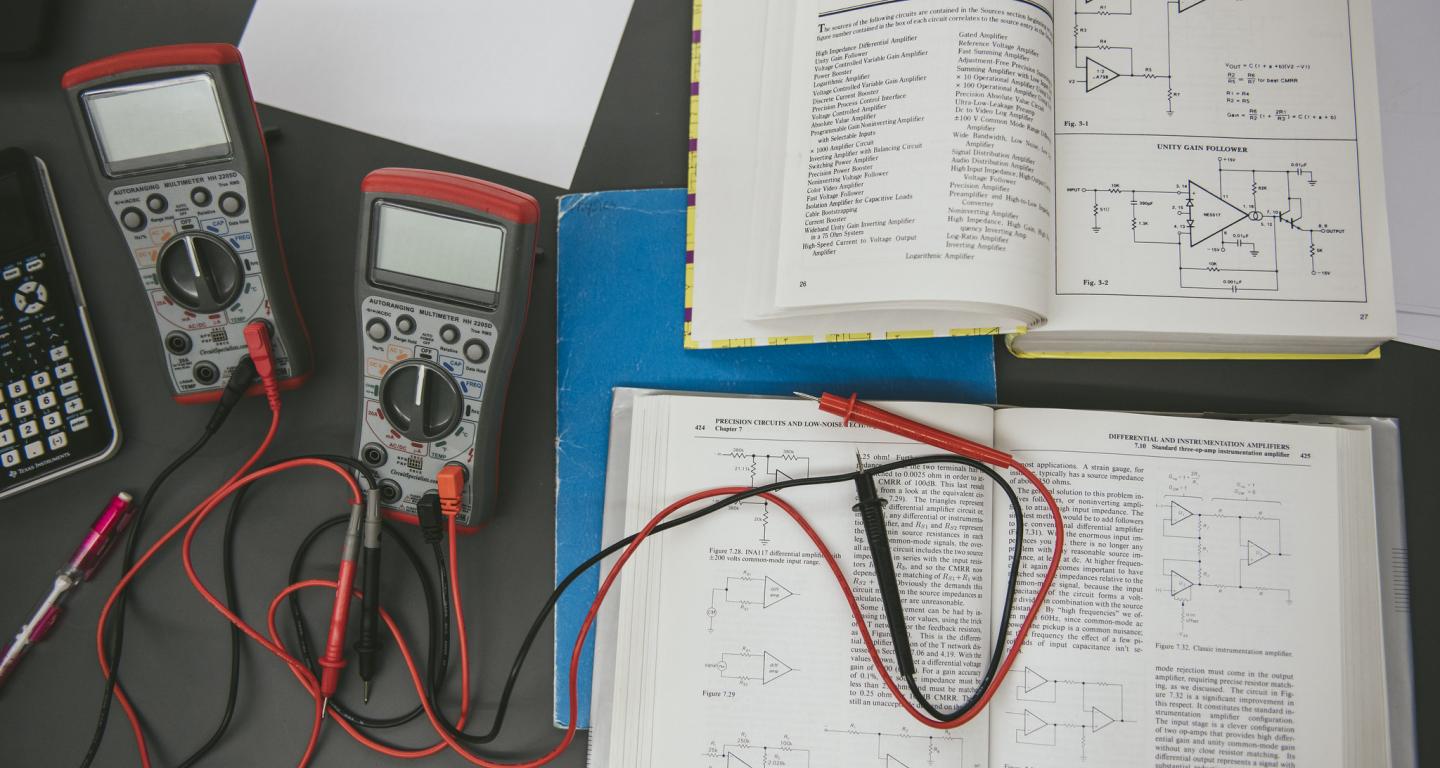
The five principles of Lean Five emphasize eliminating waste. The principles also promote value stream mapping to identify activities that can be done more efficiently. The key to eliminating waste is to differentiate value-added (necessary) waste from non-value-added (unnecessary) waste. The most efficient process uses less energy, time and materials by eliminating redundant steps. This allows customers to be satisfied while still getting the best quality product in the shortest possible time.
Value
The Value of lean 5 principles will help you improve manufacturing flow by eliminating waste. The key to smooth production-to-shipping flow is identifying and eliminating those steps that don't add any value. This process helps reduce inventory, saves time and eliminates work in progress.
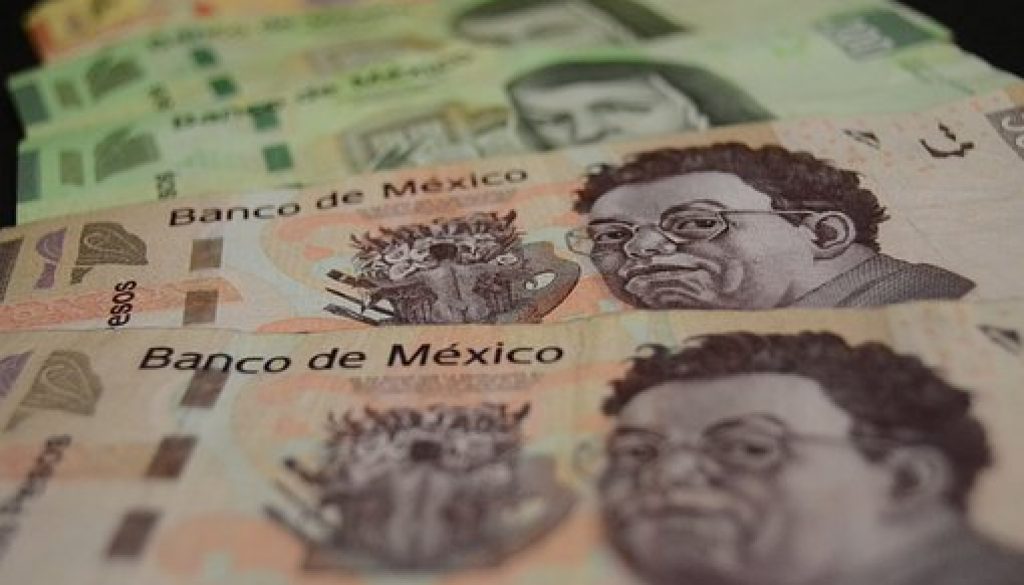
Value stream
The value stream of Lean Manufacturing is a way to eliminate waste from manufacturing processes. This method maps each step of a manufacturing process to identify those elements that are essential and eliminate those that don't. The entire value stream is the product's entire life cycle, including its creation and use. Understanding the value stream is key to eliminating waste. A value stream can contain three types of waste.
Flow
The first principle of lean 5, Flow, is to identify and evaluate the customer's actual needs. This is essential for designing new products and services as customers may not always be able to express their needs clearly. The second step in the process is to determine the value stream. It's the sequence of activities required to complete the project. This process requires close collaboration with all project participants and is a key part of lean project management.
Pull
In a pull-system, a process starts only when there's a customer order. A pizza restaurant wouldn't make extra pizzas unless they received a order from a customer. A restaurant would not waste their time, resources, or ingredients if they did.
Perfection
One of the lean 5 principles is the pursuit of perfection. This concept defines perfection as a state that is perfect, precise, consistent, and complete. But perfection is not possible. The idea behind this concept is to promote continuous improvement. The result is a better performance for organizations.
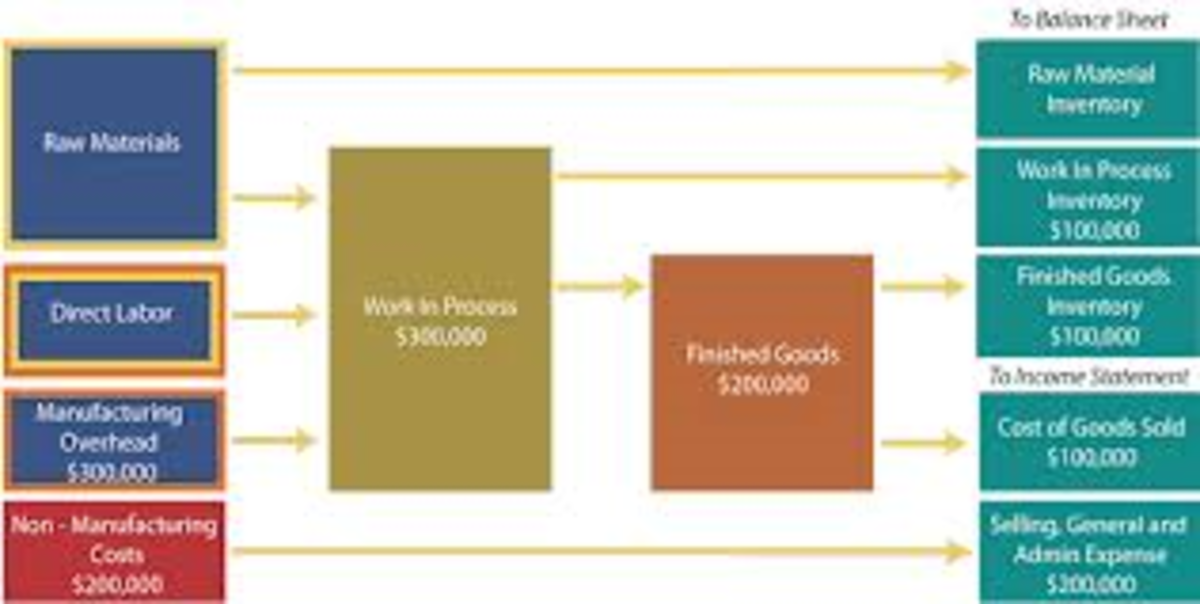
Collaboration among stakeholders
Collaboration with stakeholders is key to lean project management. It involves collaboration between project team members in order to solve problems and increase the value of the project. Teams should identify areas for improvement and problems in the planning stage. The doing phase involves gathering data to help them find solutions. Execution is not the main focus. The team should also consider the organizational structure for collaboration.
FAQ
What are the products and services of logistics?
Logistics involves the transportation of goods from point A and point B.
They encompass all aspects transport, including packaging and loading, transporting, storage, unloading.
Logisticians ensure that the right product reaches the right place at the right time and under safe conditions. Logisticians assist companies in managing their supply chains by providing information such as demand forecasts, stock levels and production schedules.
They also keep track of shipments in transit, monitor quality standards, perform inventories and order replenishment, coordinate with suppliers and vendors, and provide support services for sales and marketing.
Is automation necessary in manufacturing?
Automation is essential for both manufacturers and service providers. It allows them to offer services faster and more efficiently. In addition, it helps them reduce costs by reducing human errors and improving productivity.
What kind of jobs are there in logistics?
Logistics can offer many different jobs. Here are some:
-
Warehouse workers – They load and unload pallets and trucks.
-
Transportation drivers – These drivers drive trucks and wagons to transport goods and pick up the goods.
-
Freight handlers: They sort and package freight in warehouses.
-
Inventory managers - These are responsible for overseeing the stock of goods in warehouses.
-
Sales representatives: They sell products to customers.
-
Logistics coordinators - They organize and plan logistics operations.
-
Purchasing agents are those who purchase goods and services for the company.
-
Customer service agents - They answer phone calls and respond to emails.
-
Shipping clerks – They process shipping orders, and issue bills.
-
Order fillers – They fill orders based upon what was ordered and shipped.
-
Quality control inspectors: They inspect outgoing and incoming products for any defects.
-
Other - Logistics has many other job opportunities, including transportation supervisors, logistics specialists, and cargo specialists.
What does manufacturing mean?
Manufacturing Industries are those businesses that make products for sale. These products are sold to consumers. To accomplish this goal, these companies employ a range of processes including distribution, sales, management, and production. They create goods from raw materials, using machines and various other equipment. This includes all types and varieties of manufactured goods, such as food items, clothings, building supplies, furnitures, toys, electronics tools, machinery vehicles, pharmaceuticals medical devices, chemicals, among others.
Why is logistics so important in manufacturing?
Logistics are an essential part of any business. They help you achieve great results by helping you manage all aspects of product flow, from raw materials to finished goods.
Logistics play a key role in reducing expenses and increasing efficiency.
What is production planning?
Production Planning refers to the development of a plan for every aspect of production. This document will ensure everything is in order and ready to go when you need it. This document should include information about how to achieve the best results on-set. It should include information about shooting locations, casting lists, crew details, equipment requirements, and shooting schedules.
The first step is to outline what you want to film. You may already know where you want the film to be shot, or perhaps you have specific locations and sets you wish to use. Once you have determined your scenes and locations, it is time to start figuring out the elements that you will need for each scene. For example, you might decide that you need a car but don't know exactly what model you want. You could look online for cars to see what options are available, and then narrow down your choices by selecting between different makes or models.
After you have chosen the right car, you will be able to begin thinking about accessories. What about additional seating? Maybe you need someone to move around in the back. Maybe you want to change the interior color from black to white? These questions will help you determine the exact look and feel of your car. It is also worth considering the types of shots that you wish to take. You will be filming close-ups and wide angles. Maybe the engine or steering wheel is what you are looking to film. These things will help you to identify the car that you are looking for.
Once you have all the information, you are ready to create a plan. A schedule will tell you when you need to start shooting and when you need to finish. Every day will have a time for you to arrive at the location, leave when you are leaving and return home when you are done. Everyone will know what they need and when. You can also make sure to book extra staff in advance if you have to hire them. It's not worth paying someone to show up if you haven't told him.
When creating your schedule, you will also need to consider the number of days you need to film. Some projects can be completed in a matter of days or weeks. Others may take several days. It is important to consider whether you require more than one photo per day when you create your schedule. Multiple shots at the same location can increase costs and make it more difficult to complete. You can't be certain if you will need multiple takes so it is better not to shoot too many.
Budgeting is another crucial aspect of production plan. It is important to set a realistic budget so you can work within your budget. Keep in mind that you can always reduce your budget if you face unexpected difficulties. But, don't underestimate how much money you'll spend. Underestimating the cost will result in less money after you have paid for other items.
Production planning is a detailed process. But, once you understand the workings of everything, it becomes easier for future projects to be planned.
What is the difference in Production Planning and Scheduling, you ask?
Production Planning (PP), is the process of deciding what production needs to take place at any given time. Forecasting and identifying production capacity are two key elements to this process.
Scheduling refers to the process of allocating specific dates to tasks in order that they can be completed within a specified timeframe.
Statistics
- In 2021, an estimated 12.1 million Americans work in the manufacturing sector.6 (investopedia.com)
- According to a Statista study, U.S. businesses spent $1.63 trillion on logistics in 2019, moving goods from origin to end user through various supply chain network segments. (netsuite.com)
- You can multiply the result by 100 to get the total percent of monthly overhead. (investopedia.com)
- (2:04) MTO is a production technique wherein products are customized according to customer specifications, and production only starts after an order is received. (oracle.com)
- Many factories witnessed a 30% increase in output due to the shift to electric motors. (en.wikipedia.org)
External Links
How To
How to use 5S to increase Productivity in Manufacturing
5S stands for "Sort", "Set In Order", "Standardize", "Separate" and "Store". The 5S methodology was developed at Toyota Motor Corporation in 1954. It assists companies in improving their work environments and achieving higher efficiency.
This method aims to standardize production processes so that they are repeatable, measurable and predictable. It means tasks like cleaning, sorting or packing, labeling, and storing are done every day. This knowledge allows workers to be more efficient in their work because they are aware of what to expect.
There are five steps that you need to follow in order to implement 5S. Each step has a different action and leads to higher efficiency. By sorting, for example, you make it easy to find the items later. You arrange items by placing them in an order. Next, organize your inventory into categories and store them in containers that are easily accessible. Finally, label all containers correctly.
Employees must be able to critically examine their work practices. Employees must be able to see why they do what they do and find a way to achieve them without having to rely on their old methods. In order to use the 5S system effectively, they must be able to learn new skills.
The 5S method not only increases efficiency but also boosts morale and teamwork. Once they start to notice improvements, they are motivated to keep working towards their goal of increasing efficiency.