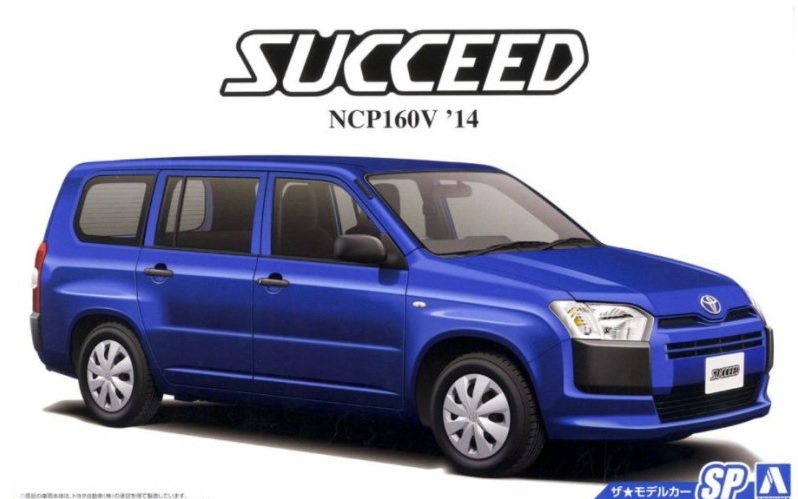
Integrated supply chain management (ISCM) is a process that allows companies to monitor and optimize their supply chain performance. This creates a responsive, streamlined production network. The more efficient your operations are, the simpler and more responsive your supply chains will be. Integrated supply chain management can also improve your profits and minimize waste. This means that your products will be of better quality, more reliable, and less costly to produce.
Integrated supply chain management can increase the reliability and predictability of your orders. Your production schedule will be more responsive, your inventory levels will be more accurate, and your delivery schedule will be more flexible. Integrated supply chains can also help you manage risk. It can also lower greenhouse emissions. This will help you achieve your environmental goals.
The first step in integration is to draft a contract with your preferred vendors. These agreements must be tailored to the needs of your company. The agreement should provide information about your production schedule and materials, as well as the costs. Your preferred suppliers must also be able demonstrate how their services will benefit the organization. You may also find lower prices by purchasing a greater number of goods and services.
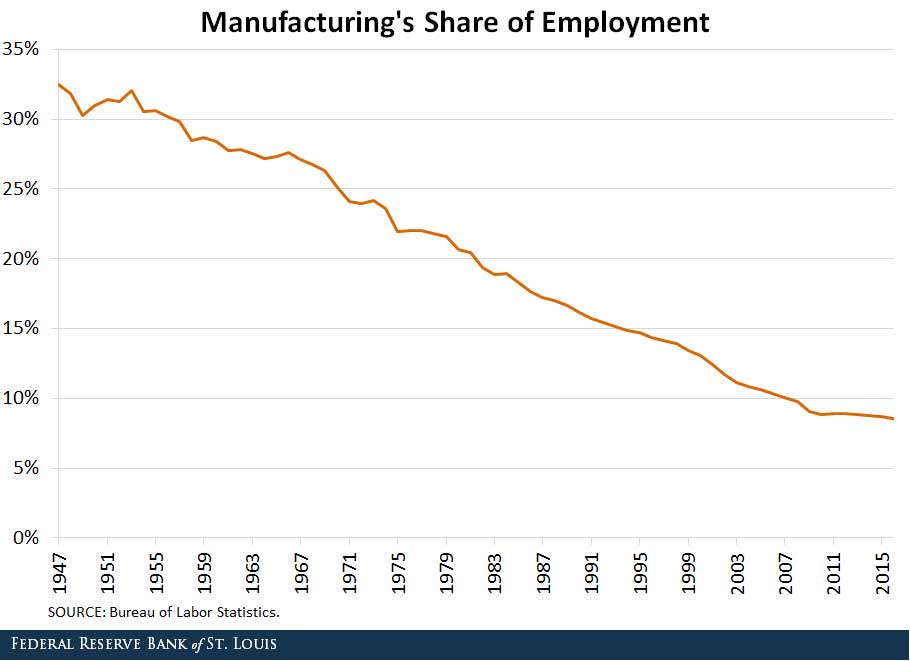
A solid understanding of your relationships and how they impact your business is an essential component of integrated supply chain management. This will allow you to avoid costly mistakes and identify potential opportunities for improving performance. You should also have a comprehensive end-to-end plan to meet your needs. It should be flexible enough that it can accommodate production changes. This will avoid any delays.
Just-intime distribution is one example of an integrated supply chain. This strategy reduces operational costs and increases warehouse space. This strategy can also be used to forecast accurately. Using an integrated supply chain is also important for reducing greenhouse gas emissions. You can achieve this by reducing the amount of large fixed assets.
Vertical integration refers to when all the elements are in place for a product. This could include a manufacturer, vendor, or supplier. This could give the manufacturer a larger share of profits. You may also consider buying a manufacturer of widgets or a business that makes widgets. This can give you the ability to manage your competitors and guarantee that you are offering a fair price for widgets.
Another example is a container management plan. This allows you to see your inventory levels and adjust your container pull strategies as necessary. You can also make changes to the production schedule right away.
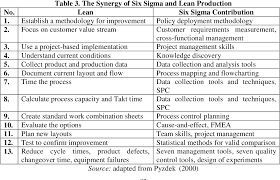
A supply chain management plan is more effective if you have a clear vision of your goals. Integrated supply chains aim to improve performance and provide customers with the best possible products. An integrated supply chain can reduce the amount waste plastic is created during manufacturing. This will help you increase your profit margins while reducing your greenhouse gas emissions.
FAQ
How can overproduction in manufacturing be reduced?
Better inventory management is key to reducing excess production. This would reduce the time spent on unproductive activities like purchasing, storing and maintaining excess stock. By doing this, we could free up resources for other productive tasks.
Kanban systems are one way to achieve this. A Kanban Board is a visual display that tracks work progress. Work items are moved through various states to reach their destination in a Kanban system. Each state represents a different priority.
To illustrate, work can move from one stage or another when it is complete enough for it to be moved to a new stage. A task that is still in the initial stages of a process will be considered complete until it moves on to the next stage.
This allows you to keep work moving along while making sure that no work gets neglected. A Kanban board allows managers to monitor how much work is being completed at any given moment. This data allows them adjust their workflow based upon real-time data.
Lean manufacturing is another way to manage inventory levels. Lean manufacturing seeks to eliminate waste from every step of the production cycle. Anything that does nothing to add value to a product is waste. The following are examples of common waste types:
-
Overproduction
-
Inventory
-
Unnecessary packaging
-
Exceed materials
Manufacturers can increase efficiency and decrease costs by implementing these ideas.
What is the responsibility of a production planner?
A production planner ensures all aspects of the project are delivered on time, within budget, and within scope. They also ensure the quality of the product and service meets the client's requirements.
What is the responsibility of a manufacturing manager?
The manufacturing manager should ensure that every manufacturing process is efficient and effective. They should also be aware of any problems within the company and act accordingly.
They should also be able and comfortable communicating with other departments like sales and marketing.
They must also keep up-to-date with the latest trends in their field and be able use this information to improve productivity and efficiency.
Statistics
- Many factories witnessed a 30% increase in output due to the shift to electric motors. (en.wikipedia.org)
- Job #1 is delivering the ordered product according to specifications: color, size, brand, and quantity. (netsuite.com)
- You can multiply the result by 100 to get the total percent of monthly overhead. (investopedia.com)
- [54][55] These are the top 50 countries by the total value of manufacturing output in US dollars for its noted year according to World Bank.[56] (en.wikipedia.org)
- According to a Statista study, U.S. businesses spent $1.63 trillion on logistics in 2019, moving goods from origin to end user through various supply chain network segments. (netsuite.com)
External Links
How To
How to Use the 5S to Increase Productivity In Manufacturing
5S stands to stand for "Sort", “Set In Order", “Standardize", and "Store". Toyota Motor Corporation was the first to develop the 5S approach in 1954. This methodology helps companies improve their work environment to increase efficiency.
This approach aims to standardize production procedures, making them predictable, repeatable, and easily measurable. This means that tasks such as cleaning, sorting, storing, packing, and labeling are performed daily. Because workers know what they can expect, this helps them perform their jobs more efficiently.
Implementing 5S requires five steps. These are Sort, Set In Order, Standardize. Separate. And Store. Each step requires a different action, which increases efficiency. You can make it easy for people to find things later by sorting them. Once you have placed items in an ordered fashion, you will put them together. Next, organize your inventory into categories and store them in containers that are easily accessible. Finally, label all containers correctly.
Employees must be able to critically examine their work practices. Employees need to understand the reasons they do certain jobs and determine if there is a better way. In order to use the 5S system effectively, they must be able to learn new skills.
In addition to improving efficiency, the 5S system also increases morale and teamwork among employees. They will feel motivated to strive for higher levels of efficiency once they start to see results.