
In the world of lean manufacturing, andon means a visual indication that points out and calls attention to problems for the express purpose of resolving them with long-term fixes. It is a tool that empowers plant floor operators and accelerates teamwork in production.
Andon
( ) – a Japanese term, it is derived from the paper-enclosed fixed lanterns that were used during the Edo period between the 17th Century and the 19th Century. It is also used to describe a Japanese system that ties light signals or sound to a particular process issue to alert the operators and management.
Toyota uses the term "build-in" quality as a core principle of its Jidoka. It is a component in their TPS system (Toyota Production System). In the US it is often cited to be the basis of a business concept that allows workers on the production lines to stop the line if a quality or safety problem occurs.
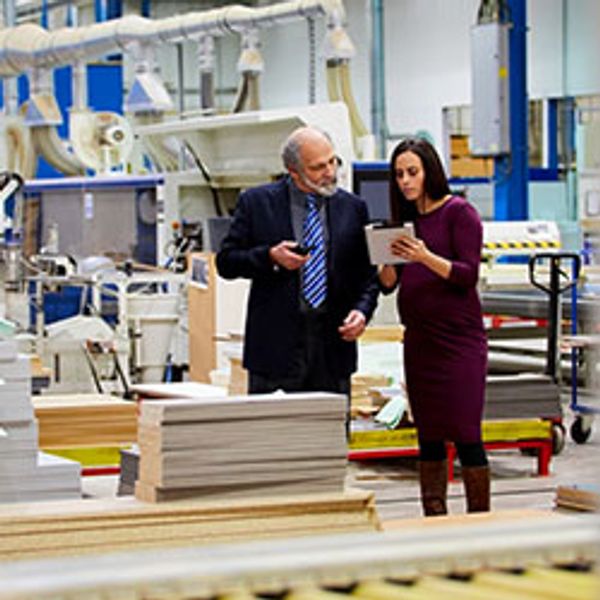
What is anon?
Toyota is the pioneer of Andon. It's a lean system for manufacturing. It's a simple system, consisting of three lights: yellow, green and red. Each color indicates the different status of production. The production line runs normally when the green light is on. The yellow light means that the problem has been identified and is being dealt with. When the red light is lit, all production stops. The workers can take a pause, prepare parts, get help, or simply fill their bins.
Andon's board is simple to operate and supervisors understand exactly what has occurred. The system is designed to provide immediate feedback and ensure all problems are resolved as soon as possible.
There are many types of andons, but most common is a red light with a sound or buzzer to alert production teams. These systems, which include alerts and signals, are useful in identifying potential problems that can lead to repeat or prolonged downtime.
An effective andon board can help to keep the production running in case of a malfunction. It is an easy-to-use tool that improves productivity, reduces downtimes, and increases product quality and safety.
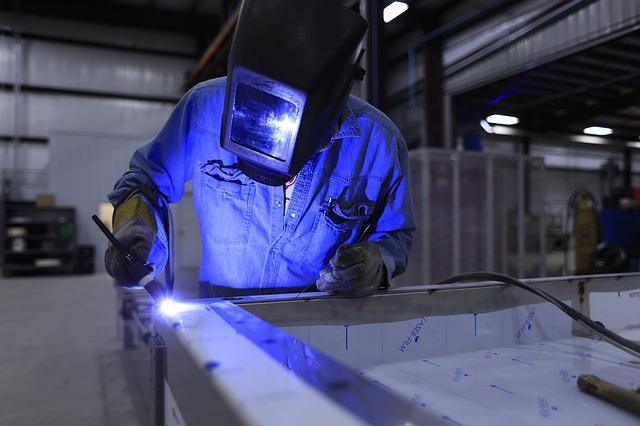
What is anon toyota?
Toyota used a special cord that any employee on the manufacturing floor could pull if they saw a potential issue with one of their cars. If a worker felt the car was compromised, they could instantly stop the production line by pulling this cord.
Similarly, the modern andon system uses technology to present curated content that makes it easy to identify emerging problems. It also pushes notifications in real-time to stakeholders and identifies the root cause. However, human touch is still essential in interpreting and acting upon this information.
How to make andon work?
It is important to start by creating a culture in which workers and managers are not afraid to address and identify problems. The more hesitant people are, the greater their tendency to hide issues and miss opportunities to resolve them. Line stops can help improve this by encouraging workers to press the button and pull out the cord when they detect a problem.
FAQ
What is the role of a production manager?
A production planner ensures all aspects of the project are delivered on time, within budget, and within scope. They ensure that the product or service is of high quality and meets client requirements.
What do we need to know about Manufacturing Processes in order to learn more about Logistics?
No. You don't have to know about manufacturing processes before learning about logistics. Understanding the manufacturing process will allow you to better understand logistics.
What are the 4 types manufacturing?
Manufacturing is the process that transforms raw materials into useful products. Manufacturing can include many activities such as designing and building, testing, packaging shipping, selling, servicing, and other related activities.
Statistics
- In the United States, for example, manufacturing makes up 15% of the economic output. (twi-global.com)
- Job #1 is delivering the ordered product according to specifications: color, size, brand, and quantity. (netsuite.com)
- In 2021, an estimated 12.1 million Americans work in the manufacturing sector.6 (investopedia.com)
- Many factories witnessed a 30% increase in output due to the shift to electric motors. (en.wikipedia.org)
- [54][55] These are the top 50 countries by the total value of manufacturing output in US dollars for its noted year according to World Bank.[56] (en.wikipedia.org)
External Links
How To
How to use the Just In-Time Production Method
Just-in-time (JIT) is a method that is used to reduce costs and maximize efficiency in business processes. It's the process of obtaining the right amount and timing of resources when you need them. This means that only what you use is charged to your account. Frederick Taylor first coined this term while working in the early 1900s as a foreman. Taylor observed that overtime was paid to workers if they were late in working. He realized that workers should have enough time to complete their jobs before they begin work. This would help increase productivity.
The idea behind JIT is that you should plan ahead and have everything ready so you don't waste money. Look at your entire project, from start to end. Make sure you have enough resources in place to deal with any unexpected problems. You will have the resources and people to solve any problems you anticipate. This will ensure that you don't spend more money on things that aren't necessary.
There are different types of JIT methods:
-
Demand-driven JIT: You order the parts and materials you need for your project every other day. This will allow to track how much material has been used up. This will allow you to calculate how long it will take to make more.
-
Inventory-based: This type allows you to stock the materials needed for your projects ahead of time. This allows you to predict how much you can expect to sell.
-
Project-driven: This is an approach where you set aside enough funds to cover the cost of your project. When you know how much you need, you'll purchase the appropriate amount of materials.
-
Resource-based JIT: This is the most popular form of JIT. You allocate resources based on the demand. You might assign more people to help with orders if there are many. If there aren't many orders, you will assign fewer people.
-
Cost-based : This is similar in concept to resource-based. But here, you aren't concerned about how many people your company has but how much each individual costs.
-
Price-based pricing: This is similar in concept to cost-based but instead you look at how much each worker costs, it looks at the overall company's price.
-
Material-based - This is a variant of cost-based. But instead of looking at the total company cost, you focus on how much raw material you spend per year.
-
Time-based JIT is another form of resource-based JIT. Instead of focusing on the cost of each employee, you will focus on the time it takes to complete a project.
-
Quality-based JIT: This is another variation of resource based JIT. Instead of looking at the labor costs and time it takes to make a product, think about its quality.
-
Value-based JIT: One of the most recent forms of JIT. You don't worry about whether the products work or if they meet customer expectations. Instead, your goal is to add value to the market.
-
Stock-based: This stock-based method focuses on the actual quantity of products being made at any given time. It's useful when you want maximum production and minimal inventory.
-
Just-intime (JIT), planning is a combination JIT management and supply chain management. It is the process that schedules the delivery of components within a short time of their order. This is important as it reduces lead time and increases throughput.