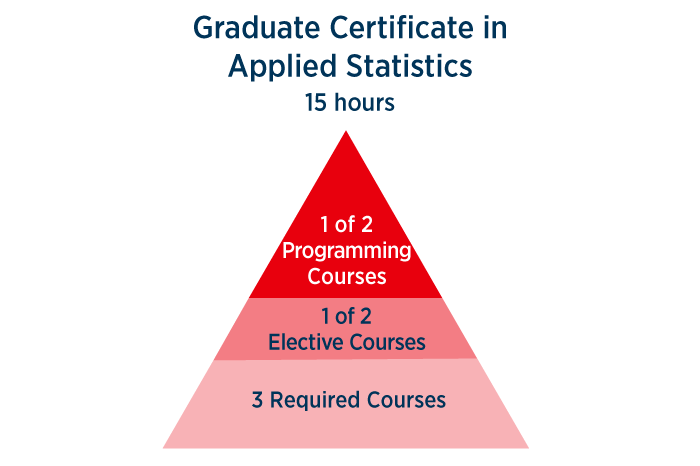
Advanced manufacturing refers the use of innovative technology in order to enhance products or processes. You can categorize the technology used to achieve this as "advanced", innovative, or cutting edge. Advanced manufacturing is becoming more popular as companies use newer and more innovative technologies in their manufacturing processes. Here are some examples for advanced manufacturing. Below are some examples of advanced manufacturing technologies.
Continuous production
The earliest description of continuous manufacturing dates back to the 1700s when it was used to make pig iron in blast furnaces. Since then, the concept has been adopted by many industries, including the automotive and food, oil and refinery, chemicals and pulp and and paper industries. Continuous manufacturing has captured the attention of CMOs from top pharma and other big players in the biopharmaceutical market.
Recent commentary by the FDA and its partner organizations discussed the benefits that continuous manufacturing can bring to the production of therapeutic protein. This legislation would create national centres to promote the field and assist companies in creating standards. The goal is to help the industry improve the process of creating and using medical products. This would encourage companies using continuous manufacturing to improve their products. It is important to make sure that continuous manufacturing is safe.
Automated processes
Automation in advanced manufacturing has many benefits that cannot be overstated. In many cases, automation is the most effective way to make the most of floor space while also maximizing production efficiency. By collecting data and leveraging automation technologies, manufacturers can reduce costs and increase productivity by making better use of equipment. Automation in the process industry also helps to save time and money. While the initial investment can be high, it will eventually increase the bottom line of a manufacturing company.
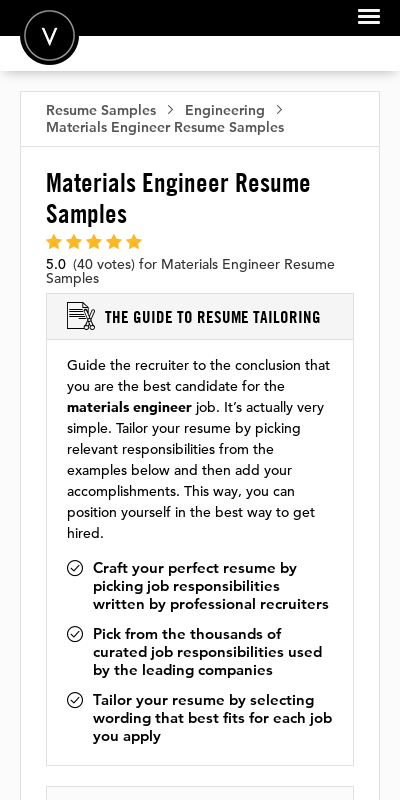
Modern companies combine advanced manufacturing processes and automated processes. Audi is an example of a company that uses automated welding to bond its products. This allows them to cut down on production time and also saves energy and weight. They also utilize advanced manufacturing systems such as regenerative braking in conveyor systems. 3D printing represents the greatest advancement in manufacturing. It has been around for a while, but it is only now that it is mainstream. What is it that makes 3D printing so appealing?
Internet of Things
Manufacturing is being transformed by the IIoT revolution. This revolution uses sensors to monitor machinery and processes. These sensors collect data from all parts of the manufacturing process and send it to a central base station. This data can then be analyzed to help optimize processes and eliminate waste. Advanced manufacturers have already begun to use IIoT sensors in order to optimize production processes. The IIoT industrial version is connected key fobs.
IIoT deployment needs a detailed roadmap and development capabilities in order to deploy use cases efficiently and scale effectively. The following road map from an automaker shows three waves of deployment:
Cost-effectiveness
Costs of advanced manufacturing may not be directly comparable to traditional production systems. It is more likely that the traditional cost-benefit model is insufficient to assess economic benefits. However, a holistic model that considers both costs and benefits of technology can help to identify new benefits and accelerate decision-making processes. Munker and Schroer present a cost-benefit analysis that addresses the most important issues related to AMS implementation.
Information technology advances are changing rapidly the face of manufacturing, as well as their costs. As production systems become more networked and smart, they are also becoming more efficient. The cost pressure is increasing, putting more emphasis on productivity and company's ability respond to customer demands. The adoption of modern manufacturing technologies will accelerate the development of new technologies and increase their cost-effectiveness. As the industry digitizes, this will likely lead to a rapid adoption of such technologies.
Human error reduction
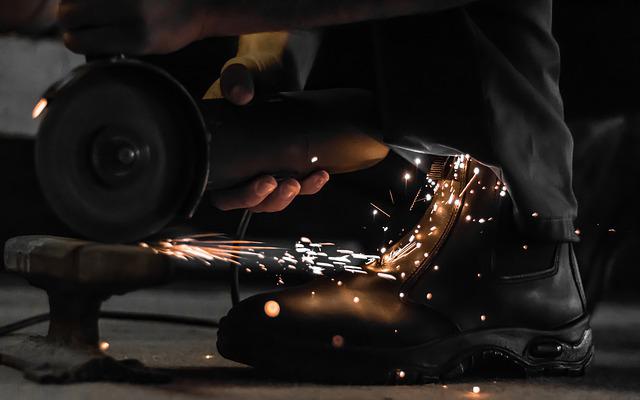
While humans make mistakes, the process they use to produce a product is usually designed to protect it. Human error can happen when employees don't read or understand instructions. For example, pharmaceutical laboratories must follow specific procedures when making drugs. In some cases, an employee may think they have mastered a process and understand the exact amounts of ingredients to use, so they proceed to make the mixture without consulting the written procedure.
A way to reduce human errors is to communicate effectively between junior and senior employees. Employees who are treated unfairly are more likely to make mistakes. Managers should not punish employees for asking questions. Employees should feel comfortable asking for questions. If they do not feel comfortable, they may not take corrective steps. Maintain a healthy dialog between junior and senior employees and resolve communication problems in a professional and courteous manner.
FAQ
What is the difference between a production planner and a project manager?
The major difference between a Production Planner and a Project Manager is that a Project Manager is often the person responsible for organizing and planning the entire project. While a Production Planner is involved mainly in the planning stage,
What kind of jobs are there in logistics?
There are many jobs available in logistics. Here are some examples:
-
Warehouse workers - They load and unload trucks and pallets.
-
Transportation drivers: They drive trucks and trailers and deliver goods and make pick-ups.
-
Freight handlers are people who sort and pack freight into warehouses.
-
Inventory managers - They oversee the inventory of goods in warehouses.
-
Sales reps - They sell products and services to customers.
-
Logistics coordinators – They plan and coordinate logistics operations.
-
Purchasing agents: They are responsible for purchasing goods and services to support company operations.
-
Customer service representatives – They answer emails and phone calls from customers.
-
Shipping clerks: They process shipping requests and issue bills.
-
Order fillers: They fill orders based off what has been ordered and shipped.
-
Quality control inspectors are responsible for inspecting incoming and outgoing products looking for defects.
-
Others - There are many types of jobs in logistics such as transport supervisors and cargo specialists.
What is the role and responsibility of a Production Planner?
A production planner makes sure all project elements are delivered on schedule, within budget, as well as within the agreed scope. They also ensure the quality of the product and service meets the client's requirements.
How can we reduce manufacturing overproduction?
Improved inventory management is the key to reducing overproduction. This would reduce the time spent on unproductive activities like purchasing, storing and maintaining excess stock. This will allow us to free up resources for more productive tasks.
A Kanban system is one way to achieve this. A Kanbanboard is a visual tool that allows you to keep track of the work being done. A Kanban system allows work items to move through several states before reaching their final destination. Each state has a different priority level.
When work is completed, it can be transferred to the next stage. If a task is still in its beginning stages, it will continue to be so until it reaches the end.
This helps to keep work moving forward while ensuring that no work is left behind. Managers can see how much work has been done and the status of each task at any time with a Kanban Board. This allows them to adjust their workflows based on real-time information.
Lean manufacturing is another way to manage inventory levels. Lean manufacturing emphasizes eliminating waste in all phases of production. Waste includes anything that does not add value to the product. These are some of the most common types.
-
Overproduction
-
Inventory
-
Unnecessary packaging
-
Material surplus
These ideas will help manufacturers increase efficiency and lower costs.
What are the 7 R's of logistics?
The acronym 7Rs of Logistics refers to the seven core principles of logistics management. It was developed by International Association of Business Logisticians (IABL), and published as part of their "Seven Principles of Logistics Management Series" in 2004.
The acronym is composed of the following letters.
-
Responsible - ensure that actions are in compliance with legal requirements and do not cause harm to others.
-
Reliable – have faith in your ability and capability to keep promises.
-
Reasonable - make sure you use your resources well and don't waste them.
-
Realistic - Consider all aspects of operations, including environmental impact and cost effectiveness.
-
Respectful - treat people fairly and equitably.
-
You are resourceful and look for ways to save money while increasing productivity.
-
Recognizable provides value-added products and services to customers
How can manufacturing reduce production bottlenecks?
To avoid production bottlenecks, ensure that all processes run smoothly from the moment you receive your order to the time the product ships.
This includes both quality control and capacity planning.
Continuous improvement techniques such Six Sigma are the best method to accomplish this.
Six Sigma is a management system used to improve quality and reduce waste in every aspect of your organization.
It's all about eliminating variation and creating consistency in work.
What is the importance of logistics in manufacturing?
Logistics are an essential component of any business. They can help you achieve great success by helping you manage product flow from raw material to finished goods.
Logistics plays a significant role in reducing cost and increasing efficiency.
Statistics
- You can multiply the result by 100 to get the total percent of monthly overhead. (investopedia.com)
- It's estimated that 10.8% of the U.S. GDP in 2020 was contributed to manufacturing. (investopedia.com)
- [54][55] These are the top 50 countries by the total value of manufacturing output in US dollars for its noted year according to World Bank.[56] (en.wikipedia.org)
- Many factories witnessed a 30% increase in output due to the shift to electric motors. (en.wikipedia.org)
- According to a Statista study, U.S. businesses spent $1.63 trillion on logistics in 2019, moving goods from origin to end user through various supply chain network segments. (netsuite.com)
External Links
How To
How to use the Just In-Time Production Method
Just-in-time is a way to cut costs and increase efficiency in business processes. It is a process where you get the right amount of resources at the right moment when they are needed. This means you only pay what you use. Frederick Taylor, a 1900s foreman, first coined the term. Taylor observed that overtime was paid to workers if they were late in working. He decided that workers would be more productive if they had enough time to complete their work before they started to work.
JIT is a way to plan ahead and make sure you don't waste any money. It is important to look at your entire project from beginning to end and ensure that you have enough resources to handle any issues that may arise. You will have the resources and people to solve any problems you anticipate. This way you won't be spending more on things that aren’t really needed.
There are many types of JIT methods.
-
Demand-driven: This type of JIT allows you to order the parts/materials required for your project on a regular basis. This will allow for you to track the material that you have left after using it. This will allow you to calculate how long it will take to make more.
-
Inventory-based: This allows you to store the materials necessary for your projects in advance. This allows one to predict how much they will sell.
-
Project-driven: This is an approach where you set aside enough funds to cover the cost of your project. Knowing how much money you have available will help you purchase the correct amount of materials.
-
Resource-based JIT is the most widespread form. Here, you allocate certain resources based on demand. For instance, if you have a lot of orders coming in, you'll assign more people to handle them. If there aren't many orders, you will assign fewer people.
-
Cost-based : This is similar in concept to resource-based. But here, you aren't concerned about how many people your company has but how much each individual costs.
-
Price-based: This is very similar to cost-based, except that instead of looking at how much each individual worker costs, you look at the overall price of the company.
-
Material-based: This approach is similar to cost-based. However, instead of looking at the total cost for the company, you look at how much you spend on average on raw materials.
-
Time-based JIT is another form of resource-based JIT. Instead of focusing on the cost of each employee, you will focus on the time it takes to complete a project.
-
Quality-based: This is yet another variation of resource-based JIT. Instead of thinking about how much each employee costs or how long it takes to manufacture something, you think about how good the quality of your product is.
-
Value-based: This is one of the newest forms of JIT. In this instance, you are not concerned about the product's performance or meeting customer expectations. Instead, your focus is on the value you bring to the market.
-
Stock-based is an inventory-based system that measures the number of items produced at any given moment. It's used when you want to maximize production while minimizing inventory.
-
Just-in-time (JIT) planning: This is a combination of JIT and supply chain management. It's the process of scheduling delivery of components immediately after they are ordered. It's important as it reduces leadtimes and increases throughput.