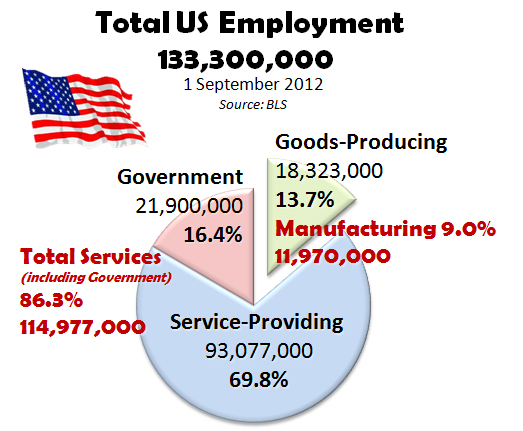
Demand management is a technique that helps companies meet their customers' needs. In essence, it involves bridging the gap between marketing and supply, by enabling organizations to predict demand. This process can increase speed and quality of delivery and reduce invoice disputes. It also lowers the cost of running a business.
Companies that have a developed demand management process are more responsive to market shifts. Because they have a system to identify the ideal customers, this can result in effective marketing.
Demand management can help businesses plan for future demand, and improve customer satisfaction. Correctly done, demand management can help businesses reduce invoice disputes as well as improve asset utilization. A good demand management strategy will also increase operational flexibility and operational resilience.
Project management software programs can enhance demand management. Such software allows teams to collaborate and prevent silos. Companies can also use change management plans to quickly address supply chain issues.
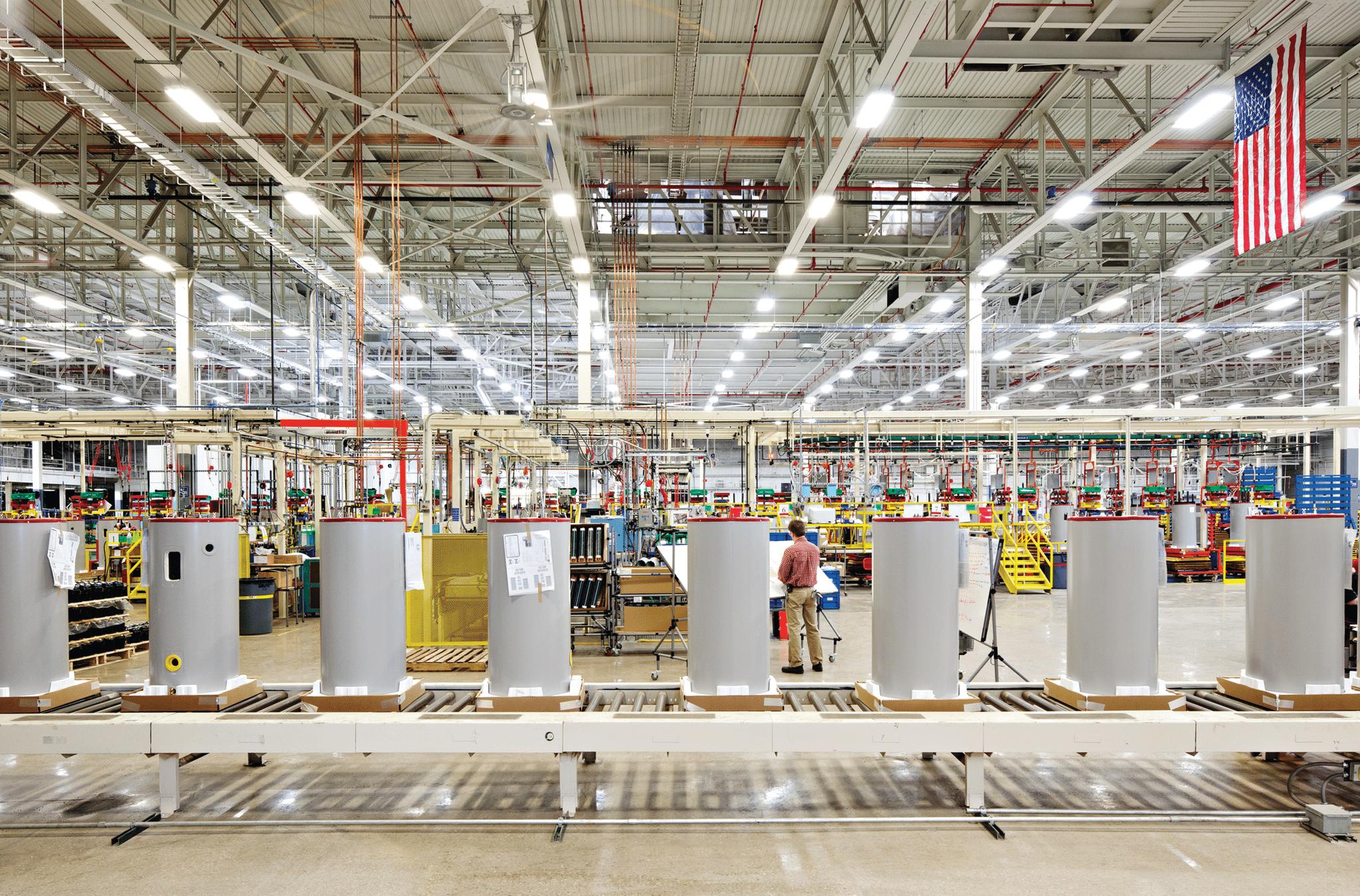
For example, ILOG's PowerOps Suite integrates manufacturing scheduling functions. Dynasys and QAD offer similar applications that enable organizations to create a supply and demand plan. These applications help companies visualize the impact of supply chain changes. Optiant offers ERP solutions for organizations that help them develop efficient, consistent order management and supply chain processes.
Real-Time Inventory and Terra Technology offer real-time supply chain forecasting solutions. Collaboration management strategies allow companies to share information, and help each other. It involves planning and executing joint actions, knowledge sharing, performance indicators, and planning.
A few key factors should be considered before you decide to implement a strategy for demand management. These factors can be helpful for professionals to better understand the process and help them focus on the most crucial aspects.
One of the most critical factors in a demand management process is leadership buy-in. Demand management is a collaborative process that requires input from all levels of management. Top executives and managers are responsible for making sure that everyone is on the same page. Those at lower levels are also important to the success of the initiative.
There are many applications available that can assist organizations in implementing a demand/supply planning. However, these key points should be kept in mind.
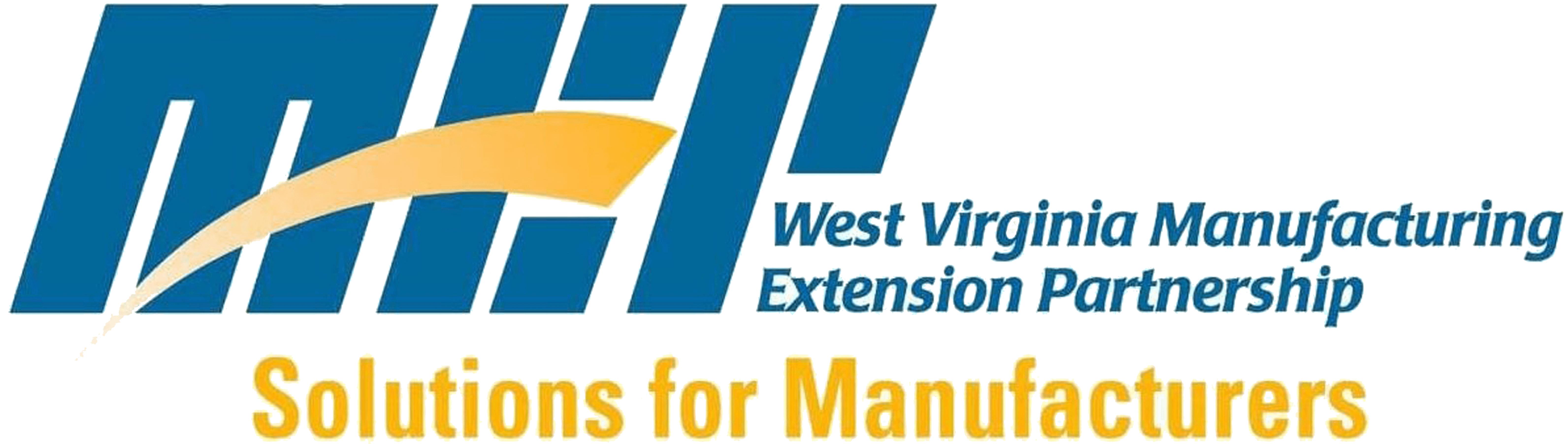
Understanding the market and identifying the ideal customer is key to demand management. In addition to knowing who to target, the organization should be able to effectively measure and analyze the results of its efforts.
Businesses must devise a demand management strategy that is flexible enough to adjust to changes in order to remain agile. An effective plan will help to reduce tactical forecast errors as well as supply chain disruptions. Last but not least, demand management is an important tool for helping to create and implement portfolios and strategic plans.
FAQ
What does it mean to be a manufacturer?
Manufacturing Industries refers to businesses that manufacture products. These products are sold to consumers. These companies use a variety processes such as distribution, retailing and management to accomplish their purpose. They create goods from raw materials, using machines and various other equipment. This includes all types if manufactured goods.
What are the 7 Rs of logistics?
The acronym 7R's of Logistic is an acronym that stands for seven fundamental principles of logistics management. It was developed by the International Association of Business Logisticians (IABL) and published in 2004 as part of its "Seven Principles of Logistics Management" series.
The acronym consists of the following letters:
-
Responsible – ensure that all actions are legal and don't cause harm to anyone else.
-
Reliable - have confidence in the ability to deliver on commitments made.
-
Reasonable - use resources efficiently and don't waste them.
-
Realistic – Consider all aspects, including cost-effectiveness as well as environmental impact.
-
Respectful – Treat others fairly and equitably.
-
Be resourceful: Look for opportunities to save money or increase productivity.
-
Recognizable is a company that provides customers with value-added solutions.
How can manufacturing efficiency be improved?
First, determine which factors have the greatest impact on production time. Then we need to find ways to improve these factors. If you aren't sure where to begin, think about the factors that have the greatest impact on production time. Once you've identified them, try to find solutions for each of those factors.
What is the best way to learn about manufacturing?
The best way to learn about manufacturing is through hands-on experience. If that is not possible, you could always read books or view educational videos.
Why should you automate your warehouse?
Modern warehousing is becoming more automated. E-commerce has brought increased demand for more efficient and quicker delivery times.
Warehouses must adapt quickly to meet changing customer needs. To do so, they must invest heavily in technology. Automating warehouses is a great way to save money. These are some of the benefits that automation can bring to warehouses:
-
Increases throughput/productivity
-
Reduces errors
-
Accuracy is improved
-
Safety enhancements
-
Eliminates bottlenecks
-
Companies can scale more easily
-
This makes workers more productive
-
This gives you visibility into what happens in the warehouse
-
Enhances customer experience
-
Improves employee satisfaction
-
This reduces downtime while increasing uptime
-
This ensures that quality products are delivered promptly
-
Human error can be eliminated
-
Assure compliance with regulations
What skills does a production planner need?
Being a production planner is not easy. You need to be organized and flexible. Effective communication with clients and colleagues is essential.
Statistics
- According to a Statista study, U.S. businesses spent $1.63 trillion on logistics in 2019, moving goods from origin to end user through various supply chain network segments. (netsuite.com)
- According to the United Nations Industrial Development Organization (UNIDO), China is the top manufacturer worldwide by 2019 output, producing 28.7% of the total global manufacturing output, followed by the United States, Japan, Germany, and India.[52][53] (en.wikipedia.org)
- In the United States, for example, manufacturing makes up 15% of the economic output. (twi-global.com)
- In 2021, an estimated 12.1 million Americans work in the manufacturing sector.6 (investopedia.com)
- [54][55] These are the top 50 countries by the total value of manufacturing output in US dollars for its noted year according to World Bank.[56] (en.wikipedia.org)
External Links
How To
How to Use Lean Manufacturing for the Production of Goods
Lean manufacturing is a management system that aims at increasing efficiency and reducing waste. It was developed in Japan between 1970 and 1980 by Taiichi Ohno. TPS founder Kanji Tyoda gave him the Toyota Production System, or TPS award. Michael L. Watkins published the "The Machine That Changed the World", the first book about lean manufacturing. It was published in 1990.
Lean manufacturing can be described as a set or principles that are used to improve quality, speed and cost of products or services. It emphasizes the elimination of defects and waste throughout the value stream. The five-steps of Lean Manufacturing are just-in time (JIT), zero defect and total productive maintenance (TPM), as well as 5S. Lean manufacturing eliminates non-value-added tasks like inspection, rework, waiting.
Lean manufacturing improves product quality and costs. It also helps companies reach their goals quicker and decreases employee turnover. Lean manufacturing can be used to manage all aspects of the value chain. Customers, suppliers, distributors, retailers and employees are all included. Lean manufacturing is widely used in many industries. For example, Toyota's philosophy underpins its success in automobiles, electronics, appliances, healthcare, chemical engineering, aerospace, paper, food, etc.
Five principles are the basis of lean manufacturing:
-
Define value - Find out what your business contributes to society, and what makes it different from other competitors.
-
Reduce Waste - Eliminate any activity that doesn't add value along the supply chain.
-
Create Flow - Ensure work moves smoothly through the process without interruption.
-
Standardize & Simplify - Make processes as consistent and repeatable as possible.
-
Build relationships - Develop and maintain personal relationships with both your internal and external stakeholders.
Although lean manufacturing isn't a new concept in business, it has gained popularity due to renewed interest in the economy after the 2008 global financial crisis. Many businesses are now using lean manufacturing to improve their competitiveness. Many economists believe lean manufacturing will play a major role in economic recovery.
Lean manufacturing has many benefits in the automotive sector. These include higher customer satisfaction, lower inventory levels, lower operating expenses, greater productivity, and improved overall safety.
The principles of lean manufacturing can be applied in almost any area of an organization. This is because it ensures efficiency and effectiveness in all stages of the value chain.
There are three types principally of lean manufacturing:
-
Just-in Time Manufacturing, (JIT): This kind of lean manufacturing is also commonly known as "pull-systems." JIT stands for a system where components are assembled on the spot rather than being made in advance. This method reduces lead times, increases availability, and decreases inventory.
-
Zero Defects Manufacturing, (ZDM): ZDM is focused on ensuring that no defective products leave the manufacturing facility. Repairing a part that is damaged during assembly should be done, not scrapping. This is also true for finished products that require minor repairs before shipping.
-
Continuous Improvement (CI): CI aims to improve the efficiency of operations by continuously identifying problems and making changes in order to eliminate or minimize waste. Continuous improvement involves continuous improvement of processes and people as well as tools.