
There are thousands upon thousands of jobs available in Connecticut's manufacturing industry. The state has 4,011 manufacturers that employ 159,000 workers. Manufacturing contributes the most to the state's gross state product and pays a better-than-average salary. The Connecticut Business and Industry Association recently released a survey of manufacturing workforce needs. They discovered that 13,000 manufacturing jobs remain unfilled in Connecticut. Many companies are struggling to hire young workers.
Connecticut's manufacturing workforce tends to be older with one-third of its workers over 55. Many manufacturing companies have moved to lower labor costs. Others also started using new machinery, automation, and equipment. Manufacturing used to be dangerous and dirty. But, the reputation has improved. Today, companies offer apprenticeships, internships, and entry level positions. Manufacturing is Connecticut’s third largest employment sector. Its high-tech operations are a key competitive advantage.
Connecticut offers many private and public education programs to help people obtain manufacturing job skills. Manufacturing Innovation Fund is one of these programs. It supports vocational high schools, high schools, and comprehensive high-schools. It also provides support for online training programs, preapprenticeships, as well career activities for K-12 student.
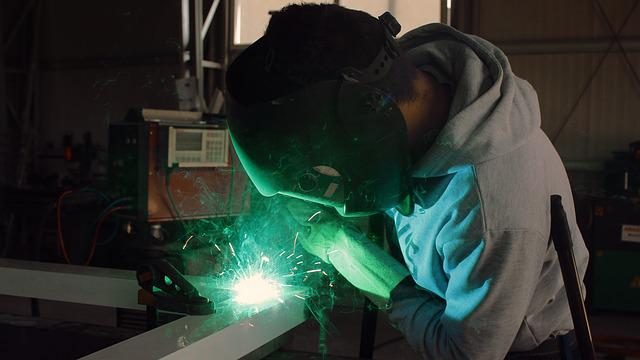
Many backgrounds go into becoming advanced manufacturing workers. Some enter the field straight from high school, while others have spent years in another field before deciding to switch to manufacturing. They may have left school to earn a degree, or they may have entered the workforce after years of service in the military. Many companies will pay tuition for advanced manufacturing programs. Other programs provide wage subsidies for entry-level training.
State Comprehensive High Schools have begun to offer technical education options. One example is the Grasso Tech welding course, which will begin in fall 2019. Employers who recruit through the EB might be interested in students from Connecticut. The Eastern Connecticut Manufacturing Pipeline supports the region's advanced manufacturing businesses. It is modeled after Eastern Connecticut Workforce Investment Board’s Manufacturing Pipeline.
The Manufacturing Careers Program was created to assist job seekers interested in manufacturing careers and demonstrate their readiness for entry-level work. This program helps pre-screened job seekers connect with manufacturers and employers. It includes a CNC Basics course, and provides an industry-infused career path. The Advanced Manufacturing Employer Partnership offers wage subsidies to entry-level training for those who enroll in the program.
Many young people who enter the workforce might not be familiar with the manufacturing industry or not want to go into manufacturing. These people may not be aware of the importance of these programs and might find it difficult to take part in them. These programs receive tens of millions in state funding. These programs are not accessible to young people because they don't know about the existence of these jobs.
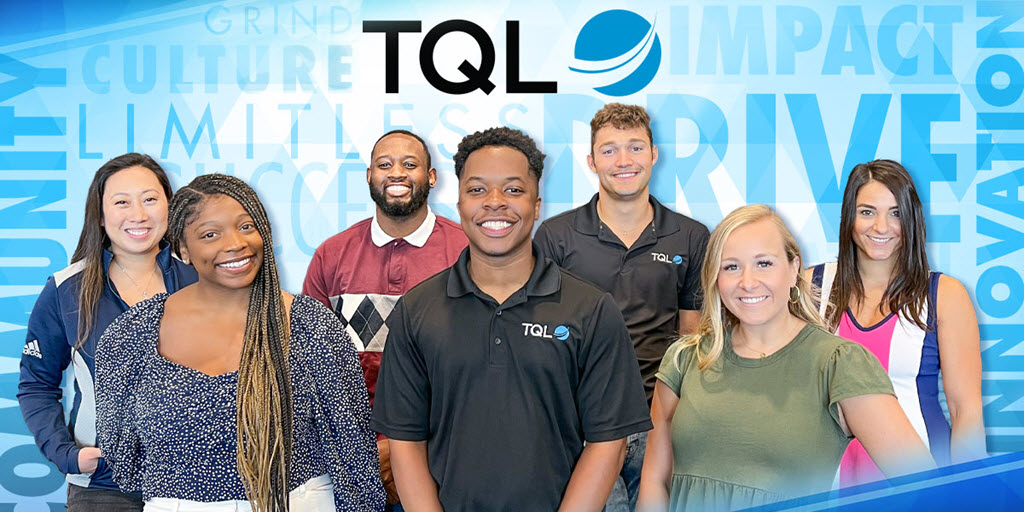
A statewide STEM Town initiative is one innovative way to address Connecticut's shortage of manufacturing jobs. This would involve reallocating resources and improving education programs to meet the needs of manufacturers.
FAQ
What is the difference between Production Planning and Scheduling?
Production Planning (PP), is the process of deciding what production needs to take place at any given time. This is done through forecasting demand and identifying production capacities.
Scheduling refers to the process of allocating specific dates to tasks in order that they can be completed within a specified timeframe.
What types of jobs can you find in logistics
There are many types of jobs in logistics. Some of them are:
-
Warehouse workers – They load and unload pallets and trucks.
-
Transportation drivers – These drivers drive trucks and wagons to transport goods and pick up the goods.
-
Freight handlers, - They sort out and pack freight in warehouses.
-
Inventory managers - These are responsible for overseeing the stock of goods in warehouses.
-
Sales representatives - They sell products.
-
Logistics coordinators – They plan and coordinate logistics operations.
-
Purchasing agents - They purchase goods and services needed for company operations.
-
Customer service representatives - They answer calls and emails from customers.
-
Shipping clerks - They process shipping orders and issue bills.
-
Order fillers: They fill orders based off what has been ordered and shipped.
-
Quality control inspectors are responsible for inspecting incoming and outgoing products looking for defects.
-
Others - There is a variety of other jobs in logistics. These include transportation supervisors and cargo specialists.
What are the goods of logistics?
Logistics are the activities involved in moving goods from point A to point B.
They cover all aspects of transportation, such as packing, loading, transporting and unloading.
Logisticians make sure that the right product arrives at the right place at the correct time and in safe conditions. Logisticians assist companies in managing their supply chains by providing information such as demand forecasts, stock levels and production schedules.
They can also track shipments in transit and monitor quality standards.
What are the responsibilities of a logistic manager?
Logistics managers make sure all goods are delivered on schedule and without damage. This is achieved by using their knowledge and experience with the products of the company. He/she should ensure that sufficient stock is available in order to meet customer demand.
What does the term manufacturing industries mean?
Manufacturing Industries are businesses that produce products for sale. The people who buy these products are called consumers. This is accomplished by using a variety of processes, including production, distribution and retailing. They manufacture goods from raw materials using machines and other equipment. This includes all types and varieties of manufactured goods, such as food items, clothings, building supplies, furnitures, toys, electronics tools, machinery vehicles, pharmaceuticals medical devices, chemicals, among others.
How can I learn about manufacturing?
You can learn the most about manufacturing by getting involved in it. You can also read educational videos or take classes if this isn't possible.
How can manufacturing efficiency be improved?
First, we need to identify which factors are most critical in affecting production times. Then we need to find ways to improve these factors. You can start by identifying the most important factors that impact production time. Once you have identified them, it is time to identify solutions.
Statistics
- You can multiply the result by 100 to get the total percent of monthly overhead. (investopedia.com)
- Many factories witnessed a 30% increase in output due to the shift to electric motors. (en.wikipedia.org)
- According to a Statista study, U.S. businesses spent $1.63 trillion on logistics in 2019, moving goods from origin to end user through various supply chain network segments. (netsuite.com)
- (2:04) MTO is a production technique wherein products are customized according to customer specifications, and production only starts after an order is received. (oracle.com)
- It's estimated that 10.8% of the U.S. GDP in 2020 was contributed to manufacturing. (investopedia.com)
External Links
How To
How to Use Just-In-Time Production
Just-in-time is a way to cut costs and increase efficiency in business processes. This is where you have the right resources at the right time. This means you only pay what you use. Frederick Taylor, a 1900s foreman, first coined the term. After observing how workers were paid overtime for late work, he realized that overtime was a common practice. He realized that workers should have enough time to complete their jobs before they begin work. This would help increase productivity.
JIT is a way to plan ahead and make sure you don't waste any money. Also, you should look at the whole project from start-to-finish and make sure you have the resources necessary to address any issues. If you expect problems to arise, you will be able to provide the necessary equipment and personnel to address them. You won't have to pay more for unnecessary items.
There are many JIT methods.
-
Demand-driven: This JIT is where you place regular orders for the parts/materials that are needed for your project. This will allow for you to track the material that you have left after using it. This will let you know how long it will be to produce more.
-
Inventory-based: This is a type where you stock the materials required for your projects in advance. This allows you predict the amount you can expect to sell.
-
Project-driven: This means that you have enough money to pay for your project. When you know how much you need, you'll purchase the appropriate amount of materials.
-
Resource-based: This is the most common form of JIT. Here, you allocate certain resources based on demand. If you have many orders, you will assign more people to manage them. If you don't receive many orders, then you'll assign fewer employees to handle the load.
-
Cost-based: This approach is very similar to resource-based. However, you don't just care about the number of people you have; you also need to consider how much each person will cost.
-
Price-based: This is very similar to cost-based, except that instead of looking at how much each individual worker costs, you look at the overall price of the company.
-
Material-based - This is a variant of cost-based. But instead of looking at the total company cost, you focus on how much raw material you spend per year.
-
Time-based JIT: A variation on resource-based JIT. Instead of focusing only on how much each employee is costing, you should focus on how long it takes to complete your project.
-
Quality-based JIT is another variant of resource-based JIT. Instead of looking at the labor costs and time it takes to make a product, think about its quality.
-
Value-based JIT is the newest form of JIT. This is where you don't care about how the products perform or whether they meet customers' expectations. Instead, you are focused on adding value to the marketplace.
-
Stock-based: This inventory-based approach focuses on how many items are being produced at any one time. It's useful when you want maximum production and minimal inventory.
-
Just-intime planning (JIT), is a combination JIT/sales chain management. This refers to the scheduling of the delivery of components as soon after they are ordered. This is important as it reduces lead time and increases throughput.