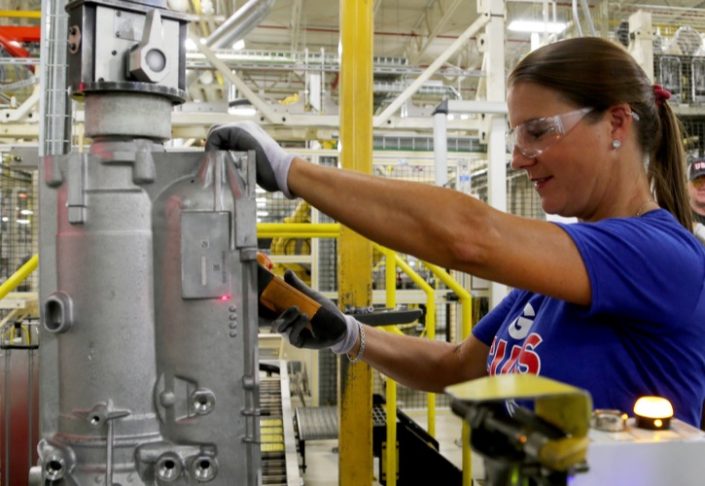
An industrial manager is an engineer who integrates different engineering processes to create an efficient management system. A industrial manager is responsible for integrating these engineering processes into one integrated management system. Here are some important facts about the job. Below are some requirements and benefits for industrial managers. This career is for you if your qualifications are up-to-date and you're looking for a rewarding and challenging job. Continue reading for more information.
Job description
An industrial manager oversees the processes involved in the manufacturing and production of goods and services. This job will cover many aspects of production, but it will also include how to source raw materials or implement equipment. Industrial production managers must be computer literate, as computers increasingly play a key role in the coordination of various departments, suppliers, and clients. Industrial production managers should also be conversant in the most recent production technologies and management procedures. Many managers take part in professional organizations, attend tradeshows and conferences in the industry, and enroll in courses to earn certification.
Industrial managers coordinate the activities in various departments within an organization, and they also oversee manufacturing processes. They make sure that production lines run smoothly and meet customer demands in terms of quality, time and delivery. They may also supervise staffing levels or change production levels as required to minimize inventory. They might also coordinate with other departments and oversee quality control programs. A majority of this role involves managing people, which includes identifying, training, and motivating employees.
Education necessary
Obtaining a bachelor's degree in business administration, management, or engineering is not typically enough to qualify as an industrial manager. However, some employers prefer to hire people with experience in these fields. A computer-literate industrial manager is also required. Computers have become an integral part in manufacturing. They can help coordinate production between departments as well as suppliers and clients. For this job, you will need the necessary education and experience.
Many industrial production manager begin their careers in production and move on to higher-ranking supervisory roles. To advance to an industrial manager position, most professionals must earn a college degree in business management. However, there are some workers who can get this education on the jobs. Or they might choose to go to classes sponsored and paid by their company. Most managers will need to have between two and five years of relevant work experience before they are qualified to become managers.
Your potential to earn
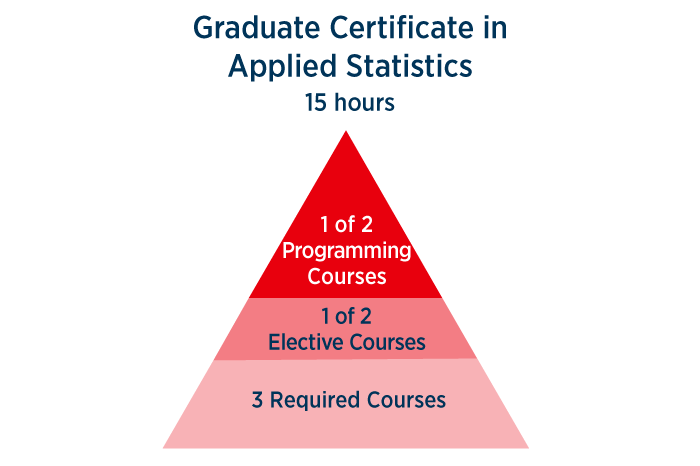
Industrial managers work in manufacturing plants and oversee the smooth operation of the entire process. They determine the best way to use employees and equipment, set production standards and make strategic choices. These people are responsible for evaluating and hiring workers. They also set production schedules and ensure safety. They oversee the day to day activities of a group of workers and analyze the production process continuously to ensure that it runs efficiently and at its peak efficiency.
The employer's experience and the earnings potential of industrial production managers will affect their earning potential. It's hard to predict future earnings for industrial managers. The average industrial production manager earned $103,380 annually in May 2016. High-skilled industrial production managers may earn more if they have been certified and received additional training. According to U.S. Bureau of Labor Statistics, those who have earned a bachelor’s or higher in industrial production management can earn more.
Work environment
An industrial production manager divides his or her time between the production floor and an office, often in the same building. When they work in a production zone, industrial production managers need to adhere to safety and health guidelines and use appropriate protective equipment. They also spend significant amounts of time in meetings with subordinates and analyzing production data. These managers may also have the ability to write reports. A manager of industrial production often works in a dynamic environment.
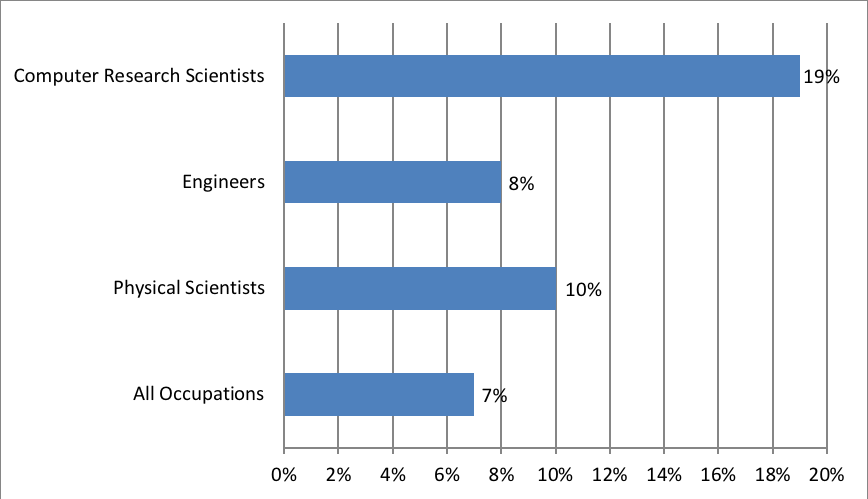
Industrial production managers play an important role in the management of a business. They are responsible for coordinating the activities of workers and increasing productivity. The primary tasks of an industrial producer manager include increasing productivity and maintaining safety. Many levels of management have been eliminated, and support staff has been reduced. This leaves more work for production managers. This can present a serious challenge to any manager and make the job of a producer manager more difficult.
FAQ
What is the job of a manufacturer manager?
A manufacturing manager must ensure that all manufacturing processes are efficient and effective. They should also be aware of any problems within the company and act accordingly.
They should also learn how to communicate effectively with other departments, including sales and marketing.
They should also be knowledgeable about the latest trends in the industry so they can use this information for productivity and efficiency improvements.
What is the role of a logistics manager
A logistics manager makes sure that all goods are delivered on-time and in good condition. This is done through his/her expertise and knowledge about the company's product range. He/she must also ensure sufficient stock to meet the demand.
What skills do production planners need?
To become a successful production planner, you need to be organized, flexible, and able to multitask. Effective communication with clients and colleagues is essential.
What is the role of a production manager?
Production planners ensure that all project aspects are completed on time, within budget and within the scope. They ensure that the product or service is of high quality and meets client requirements.
What is production planning?
Production Planning involves developing a plan for all aspects of the production, including scheduling, budgeting, casting, crew, location, equipment, props, etc. This document ensures that everything is prepared and available when you are ready for shooting. This document should also include information on how to get the best result on set. This includes location information, crew details, equipment specifications, and casting lists.
The first step is to outline what you want to film. You might have an idea of where you want to film, or you may have specific locations or sets in mind. Once you've identified the locations and scenes you want to use, you can begin to plan what elements you need for each scene. If you decide you need a car and don't know what model to choose, this could be an example. You could look online for cars to see what options are available, and then narrow down your choices by selecting between different makes or models.
Once you have found the right car, you can start thinking about extras. Do you have people who need to be seated in the front seat? Or perhaps you need someone walking around the back of the car? You might want to change your interior color from black and white. These questions will help guide you in determining the ideal look and feel for your car. You can also think about the type of shots you want to get. Do you want to film close-ups, or wider angles? Maybe you want the engine or the steering wheels to be shown. These details will help identify the exact car you wish to film.
Once you've determined the above, it is time to start creating a calendar. You can use a schedule to determine when and where you need it to be shot. The schedule will show you when to get there, what time to leave, and when to return home. So everyone is clear about what they need to do. Book extra staff ahead of time if you need them. You should not hire anyone who doesn't show up because of your inaction.
Also, consider how many days you will be filming your schedule. Some projects may only take a couple of days, while others could last for weeks. You should consider whether you will need more than one shot per week when creating your schedule. Multiple shots at the same location can increase costs and make it more difficult to complete. It is better to be cautious and take fewer shots than you risk losing money if you are not sure if multiple takes are necessary.
Budget setting is another important aspect in production planning. As it will allow you and your team to work within your financial means, setting a realistic budget is crucial. Remember that you can always reduce the budget later on if you run into unforeseen problems. You shouldn't underestimate the amount you'll spend. Underestimating the cost will result in less money after you have paid for other items.
Production planning is a complicated process. But once you understand how everything works together, it becomes much easier to plan future project.
Statistics
- Many factories witnessed a 30% increase in output due to the shift to electric motors. (en.wikipedia.org)
- According to the United Nations Industrial Development Organization (UNIDO), China is the top manufacturer worldwide by 2019 output, producing 28.7% of the total global manufacturing output, followed by the United States, Japan, Germany, and India.[52][53] (en.wikipedia.org)
- In 2021, an estimated 12.1 million Americans work in the manufacturing sector.6 (investopedia.com)
- In the United States, for example, manufacturing makes up 15% of the economic output. (twi-global.com)
- [54][55] These are the top 50 countries by the total value of manufacturing output in US dollars for its noted year according to World Bank.[56] (en.wikipedia.org)
External Links
How To
How to use Lean Manufacturing in the production of goods
Lean manufacturing is a management system that aims at increasing efficiency and reducing waste. It was first developed in Japan in the 1970s/80s by Taiichi Ahno, who was awarded the Toyota Production System (TPS), award from KanjiToyoda, the founder of TPS. Michael L. Watkins published the original book on lean manufacturing, "The Machine That Changed the World," in 1990.
Lean manufacturing refers to a set of principles that improve the quality, speed and costs of products and services. It emphasizes eliminating waste and defects throughout the value stream. The five-steps of Lean Manufacturing are just-in time (JIT), zero defect and total productive maintenance (TPM), as well as 5S. Lean manufacturing eliminates non-value-added tasks like inspection, rework, waiting.
Lean manufacturing improves product quality and costs. It also helps companies reach their goals quicker and decreases employee turnover. Lean manufacturing is a great way to manage the entire value chain including customers, suppliers, distributors and retailers as well as employees. Lean manufacturing can be found in many industries. Toyota's philosophy, for example, is what has enabled it to be successful in electronics, automobiles, medical devices, healthcare and chemical engineering as well as paper and food.
Lean manufacturing is based on five principles:
-
Define Value- Identify the added value your company brings to society. What makes you stand out from your competitors?
-
Reduce Waste - Remove any activity which doesn't add value to your supply chain.
-
Create Flow: Ensure that the work process flows without interruptions.
-
Standardize & simplify - Make processes consistent and repeatable.
-
Build relationships - Develop and maintain personal relationships with both your internal and external stakeholders.
Lean manufacturing, although not new, has seen renewed interest in the economic sector since 2008. To increase their competitiveness, many businesses have turned to lean manufacturing. Many economists believe lean manufacturing will play a major role in economic recovery.
Lean manufacturing is becoming a popular practice in automotive. It has many advantages. These benefits include increased customer satisfaction, reduced inventory levels and lower operating costs.
Any aspect of an enterprise can benefit from Lean manufacturing. Lean manufacturing is most useful in the production sector of an organisation because it ensures that each step in the value-chain is efficient and productive.
There are three main types of lean manufacturing:
-
Just-in Time Manufacturing (JIT), also known as "pull system": This form of lean manufacturing is often referred to simply as "pull". JIT is a method in which components are assembled right at the moment of use, rather than being manufactured ahead of time. This strategy aims to decrease lead times, increase availability of parts and reduce inventory.
-
Zero Defects Manufacturing, (ZDM): ZDM is focused on ensuring that no defective products leave the manufacturing facility. If a part needs to be fixed during the assembly line, it should be repaired rather than scrapped. This applies to finished products, which may need minor repairs before they are shipped.
-
Continuous Improvement: Continuous Improvement aims to improve efficiency by continually identifying problems and making adjustments to eliminate or minimize waste. It involves continuous improvement of processes, people, and tools.