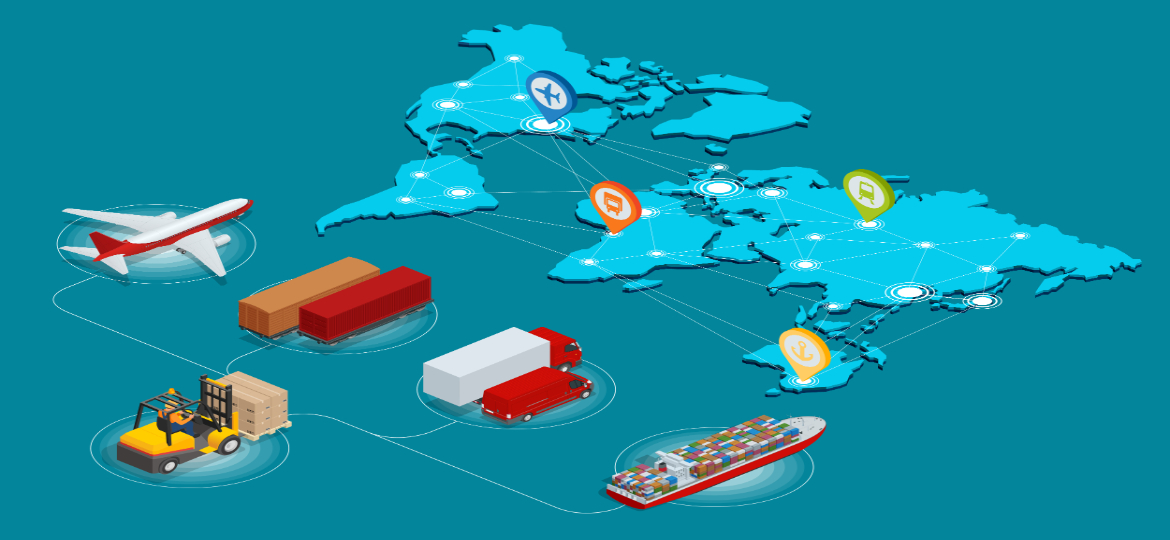
Manufacturing of wind turbines is a job opportunity
Wind turbine manufacturing jobs include a variety of tasks that require specialized knowledge and skills. These jobs include tower assembly, blade epoxies and gears. Third-party suppliers are also used by some wind turbine manufacturing companies to make various components. Wind turbine components are large and need to be transported quickly and efficiently. For this purpose, companies require teams of logisticians and rail freight driver drivers.
Jobs in wind turbine manufacturing typically require a bachelor's degree, though some require master's degrees. Engineering and environmental engineering concentrations are required for jobs in wind turbine manufacturing. In addition to a degree, entry-level engineers must have advanced computer skills and experience. They work closely with more experienced staff to ensure quality control. They may also be assigned more complex projects.
Processes involved in wind turbine manufacturing
The main component in a wind turbine are its blades. Each blade has two faces connected by integral shear Webs. The blades have a box spar and shell fairings to support them. These structures can withstand edgewise as well as flapwise loads. The spar resists edgewise bending from wind pressure and gravitational forces. These forces are met by the blades.

Blades can be made from many different materials. For commercial wind turbine blades, fiberglass is the most widely used material. However, aluminum and lightweight woodens can also be used. The blades then get covered with foil and are connected to tubes that pump resin.
Competitors within the wind turbine manufacturing sector
While Chinese manufacturers are growing in the global industry of wind, they are not yet the predominant player. Chinese turbine makers have had difficulty dethroning established manufacturers in developed market markets. They may be able to grow their overseas activities if it is possible to invest in local manufacturing.
Many are opting to build their components themselves, even though large turbine companies are outsourcing increasingly many parts. This has both its advantages and disadvantages. Vestas in Pueblo (Colorado) has adopted this strategy and now manufactures wind turbine towers to support third-party US projects. The agreement gives the tower plant access to up to 25 per cent of its production capabilities and supports 100 local workers. However, the downside of this approach is weak quality control. In the past, outsourced components have experienced failures such as blade cracking and gearbox failures. Some offshore foundations even use low-quality steel.
Manufacturing wind turbines poses health and safety risks
In wind turbine manufacturing, safety and health is an important concern. Many hazards are present that can cause long-term injury or even death for workers. There are several ways to reduce the risk. These include proper training and routine inspections. Here are some tips that will keep employees safe in a wind turbine manufacturing plant.
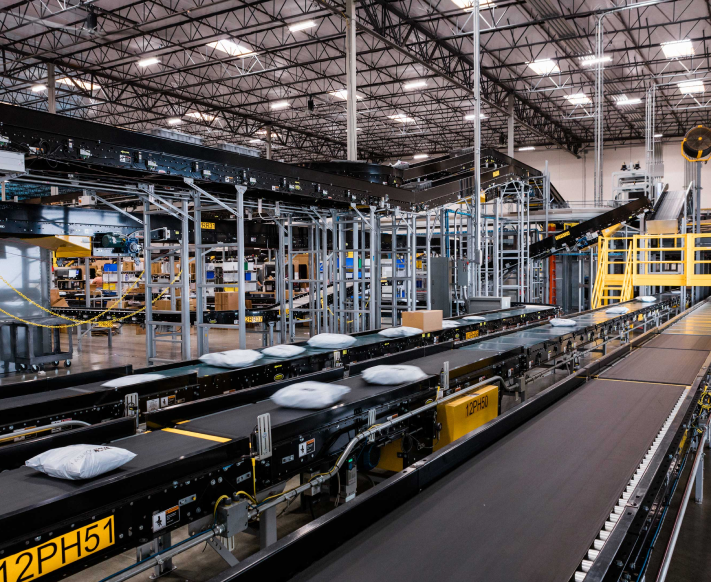
Wind turbine blade manufacturing poses a number of hazards, including the possibility of exposure to harmful gases and vapors. To reduce this exposure, workers must wear respirators and be trained to use the correct type. Good training is key to ensuring that workers are protected from the elements.
FAQ
What are the responsibilities of a manufacturing manager
A manufacturing manager has to ensure that all manufacturing processes work efficiently and effectively. They should be aware of any issues within the company and respond accordingly.
They must also be able to communicate with sales and marketing departments.
They must also keep up-to-date with the latest trends in their field and be able use this information to improve productivity and efficiency.
What is the job of a logistics manger?
Logistics managers make sure all goods are delivered on schedule and without damage. This is done using his/her knowledge of the company's products. He/she also needs to ensure adequate stock to meet demand.
What are the 7 Rs of logistics.
The acronym 7R's for Logistics stands to represent the seven basic principles in logistics management. It was developed by the International Association of Business Logisticians (IABL) and published in 2004 as part of its "Seven Principles of Logistics Management" series.
The acronym consists of the following letters:
-
Responsible – ensure that all actions are legal and don't cause harm to anyone else.
-
Reliable – have faith in your ability and capability to keep promises.
-
It is reasonable to use resources efficiently and not waste them.
-
Realistic - Consider all aspects of operations, including environmental impact and cost effectiveness.
-
Respectful: Treat others with fairness and equity
-
You are resourceful and look for ways to save money while increasing productivity.
-
Recognizable - Provide value-added services to customers
Statistics
- It's estimated that 10.8% of the U.S. GDP in 2020 was contributed to manufacturing. (investopedia.com)
- (2:04) MTO is a production technique wherein products are customized according to customer specifications, and production only starts after an order is received. (oracle.com)
- In the United States, for example, manufacturing makes up 15% of the economic output. (twi-global.com)
- Job #1 is delivering the ordered product according to specifications: color, size, brand, and quantity. (netsuite.com)
- [54][55] These are the top 50 countries by the total value of manufacturing output in US dollars for its noted year according to World Bank.[56] (en.wikipedia.org)
External Links
How To
How to use 5S to increase Productivity in Manufacturing
5S stands to stand for "Sort", “Set In Order", “Standardize", and "Store". Toyota Motor Corporation developed the 5S method in 1954. This methodology helps companies improve their work environment to increase efficiency.
The idea behind standardizing production processes is to make them repeatable and measurable. This means that every day tasks such cleaning, sorting/storing, packing, and labeling can be performed. Through these actions, workers can perform their jobs more efficiently because they know what to expect from them.
There are five steps to implementing 5S, including Sort, Set In Order, Standardize, Separate and Store. Each step has a different action and leads to higher efficiency. You can make it easy for people to find things later by sorting them. When items are ordered, they are put together. You then organize your inventory in groups. Make sure everything is correctly labeled when you label your containers.
Employees need to reflect on how they do their jobs. Employees must understand why they do certain tasks and decide if there's another way to accomplish them without relying on the old ways of doing things. In order to use the 5S system effectively, they must be able to learn new skills.
In addition to improving efficiency, the 5S system also increases morale and teamwork among employees. They feel more motivated to work towards achieving greater efficiency as they see the results.