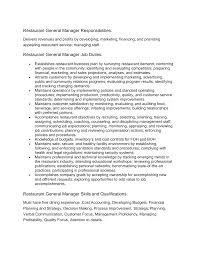
Toyota Motor Manufacturing Indiana Inc., located in Gibson County in Indiana, is the first Toyota plant that is wholly owned by Toyota. It is home to Toyota's full-size pickup trucks (including the Avalon/Corolla) and also the Sienna van. The Toyota RAV4 Hybrid hybrid is also manufactured here. It is the most successful Toyota hybrid ever.
It was originally designed to manufacture Toyota Highlander. The plant has since been moved to Gibson County. Since 2011, the plant has produced Toyota's RAV4 Hybrid compact SUV, and Lexus ES 350. Toyota spent more that $1.33billion at the plant in 2017.
Toyota Safety Sense 2.5+ can also be manufactured here. This feature includes automatic emergency braking. The plant also prepares all of the new 2018 Camry models. New features include a new transmission, greater power and a stylish design. It will be $25,900.
Toyota is the biggest American producer of the Toyota Camry. It is the most popular midsize sedan in America and has been so for 15 years. Toyota has sold 10 million Camry vehicles in Kentucky. The plant is the first in North America to manufacture the hybrid model.
Toyota Production System refers to a set of techniques and practices that improve quality and efficiency. The Toyota Production Engineering and Manufacturing Center is part of this system, and it will house 600 Toyota engineers. The center will also be the first to assemble hydrogen fuel cell modules for heavy duty commercial trucks. This facility can manufacture up to 100,000 vehicles each year.
Toyota has invested $1.5 Billion in the plant over the past five years. Toyota has also employed 700 more workers. This investment will help create 470k jobs in the United States over the next five years. Toyota has made over $147 Million in Kentucky non-profit partners since 1986.
The Toyota Camry is a reliable vehicle that is also highly stylish. It uses the GA-K platform and a new transmission. It is also fun to drive. In July of this year, Consumer Reports highlighted the Toyota Camry as one of the best-selling cars in America.
Toyota's production system includes many elements such as continuous improvement, justin-time parts deliveries, and a sophisticated robotic welder system. Toyota's Kentucky Investments in Kentucky have been well demonstrated by its Toyota Production Engineering and Manufacturing Center.
Toyota has made significant savings on its production hall construction and air conditioning costs by using a new design. The Visitor Center features interactive video displays and exhibits related to hybrid technology. Toyota will be producing up to 2,000,000 vehicles in North America over the next 10 year. This is the largest Toyota plant outside of Japan.
Toyota's New Global Architecture (or New Global Architecture) is a huge step forward in improving Toyota's production process. This strategy includes a revamped engine and organization of production. It also includes a module that unifies all vehicle components. While the new design is a reflection of Toyota's traditional values, it retains its innovative spirit.
FAQ
What is the responsibility of a production planner?
A production planner ensures all aspects of the project are delivered on time, within budget, and within scope. They also ensure that the product/service meets the client’s needs.
What is the responsibility of a logistics manager?
Logistics managers ensure that goods arrive on time and are unharmed. This is achieved by using their knowledge and experience with the products of the company. He/she should also ensure enough stock is available to meet demand.
What's the difference between Production Planning & Scheduling?
Production Planning (PP), or production planning, is the process by which you determine what products are needed at any given time. This is done through forecasting demand and identifying production capacities.
Scheduling refers the process by which tasks are assigned dates so that they can all be completed within the given timeframe.
What are manufacturing and logistic?
Manufacturing refers to the process of making goods using raw materials and machines. Logistics covers all aspects involved in managing supply chains, including procurement and production planning. Sometimes manufacturing and logistics are combined to refer to a wider term that includes both the process of creating products as well as their delivery to customers.
How can manufacturing efficiency improved?
The first step is to identify the most important factors affecting production time. The next step is to identify the most important factors that affect production time. If you don't know where to start, then think about which factor(s) have the biggest impact on production time. Once you have identified the factors, then try to find solutions.
What are the four types of manufacturing?
Manufacturing is the process by which raw materials are transformed into useful products through machines and processes. It includes many different activities like designing, building and testing, packaging, shipping and selling, as well as servicing.
Statistics
- According to the United Nations Industrial Development Organization (UNIDO), China is the top manufacturer worldwide by 2019 output, producing 28.7% of the total global manufacturing output, followed by the United States, Japan, Germany, and India.[52][53] (en.wikipedia.org)
- It's estimated that 10.8% of the U.S. GDP in 2020 was contributed to manufacturing. (investopedia.com)
- Many factories witnessed a 30% increase in output due to the shift to electric motors. (en.wikipedia.org)
- You can multiply the result by 100 to get the total percent of monthly overhead. (investopedia.com)
- In 2021, an estimated 12.1 million Americans work in the manufacturing sector.6 (investopedia.com)
External Links
How To
How to Use the Just In Time Method in Production
Just-in-time is a way to cut costs and increase efficiency in business processes. It's the process of obtaining the right amount and timing of resources when you need them. This means that you only pay the amount you actually use. Frederick Taylor was the first to coin this term. He developed it while working as a foreman during the early 1900s. He noticed that workers were often paid overtime when they had to work late. He realized that workers should have enough time to complete their jobs before they begin work. This would help increase productivity.
JIT is a way to plan ahead and make sure you don't waste any money. Also, you should look at the whole project from start-to-finish and make sure you have the resources necessary to address any issues. You can anticipate problems and have enough equipment and people available to fix them. This will ensure that you don't spend more money on things that aren't necessary.
There are different types of JIT methods:
-
Demand-driven JIT: You order the parts and materials you need for your project every other day. This will enable you to keep track of how much material is left after you use it. You'll also be able to estimate how long it will take to produce more.
-
Inventory-based: This allows you to store the materials necessary for your projects in advance. This allows you predict the amount you can expect to sell.
-
Project-driven: This approach involves setting aside sufficient funds to cover your project's costs. Once you have an idea of how much material you will need, you can purchase the necessary materials.
-
Resource-based JIT: This type of JIT is most commonly used. You allocate resources based on the demand. For example, if there is a lot of work coming in, you will have more people assigned to them. If you don't receive many orders, then you'll assign fewer employees to handle the load.
-
Cost-based: This is similar to resource-based, except that here you're not just concerned about how many people you have but how much each person costs.
-
Price-based: This approach is very similar to the cost-based method except that you don't look at individual workers costs but the total cost of the company.
-
Material-based: This approach is similar to cost-based. However, instead of looking at the total cost for the company, you look at how much you spend on average on raw materials.
-
Time-based: This is another variation of resource-based JIT. Instead of focusing on how much each employee costs, you focus on how long it takes to complete the project.
-
Quality-based JIT: This is another variation of resource based JIT. Instead of worrying about the costs of each employee or how long it takes for something to be made, you should think about how quality your product is.
-
Value-based JIT is the newest form of JIT. In this scenario, you're not concerned about how products perform or whether customers expect them to meet their expectations. Instead, you focus on the added value that you provide to your market.
-
Stock-based: This inventory-based approach focuses on how many items are being produced at any one time. It is used when production goals are met while inventory is kept to a minimum.
-
Just-intime (JIT), planning is a combination JIT management and supply chain management. This refers to the scheduling of the delivery of components as soon after they are ordered. It's important because it reduces lead times and increases throughput.