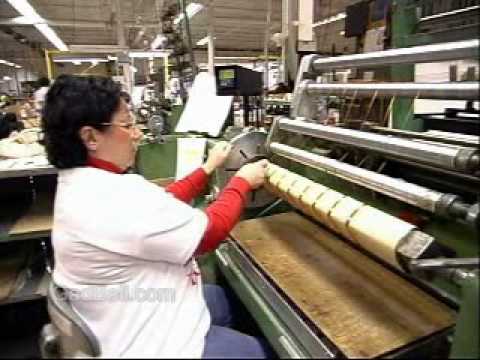
There are many types of manufacturers, but which one is best for your business? Learn about Discrete, Process, Job shop, and Continuous manufacturing. Each type has its pros and cons. This article will discuss the differences between these four types. Based on your industry, your location and your product type, you can determine which model is best for your company. After you have decided which model is right for you, you will need to think about your sales, production, quality control, and customer service.
Discrete Manufacturing
Discrete manufacturing is a process in which distinct products are produced. Toys, cars, and aeroplanes are just a few examples of discrete manufacturing. Discrete manufacturing allows companies to focus on individual products, rather than bulk production of all items. By integrating multiple manufacturing processes, discrete manufacturing allows you to create unique parts for your aircraft. Discrete manufacturing is a popular method for manufacturing high-tech products.
Discrete manufacturing produces distinct items. Instead of producing many identical products discrete manufacturing creates items that are easily identifiable by serial numbers and labels. For example, a smartphone may consist of different parts manufactured in multiple factories in different states, and the individual parts are assembled only once the finished product is ready to be sold. The same is true for the smartphone's case. It could contain parts from different plants, such as the Missouri plant headquarters.
Process manufacturing
The process manufacturing branch is one that deals with formulas or recipes. The term process manufacturing contrasts with discrete manufacturing, which is concerned with individual units, bills of materials, and the assembly of components. These two types of manufacturing have very distinct goals. Each is essential to the manufacturing process. Here are three methods to distinguish between discrete and process manufacturing. Let's look at each one.
Batch process manufacturing is similar in many ways to continuous process manufacturing. However, it uses larger quantities and runs continuously. It is commonly used in pharmaceuticals as well as paper production, bookbinding and newspaper printing. This process is not the best for every industry. It can often be too costly and complicated for smaller companies. This is why large-scale companies often use it when they need to make large quantities.
Job shop manufacturing
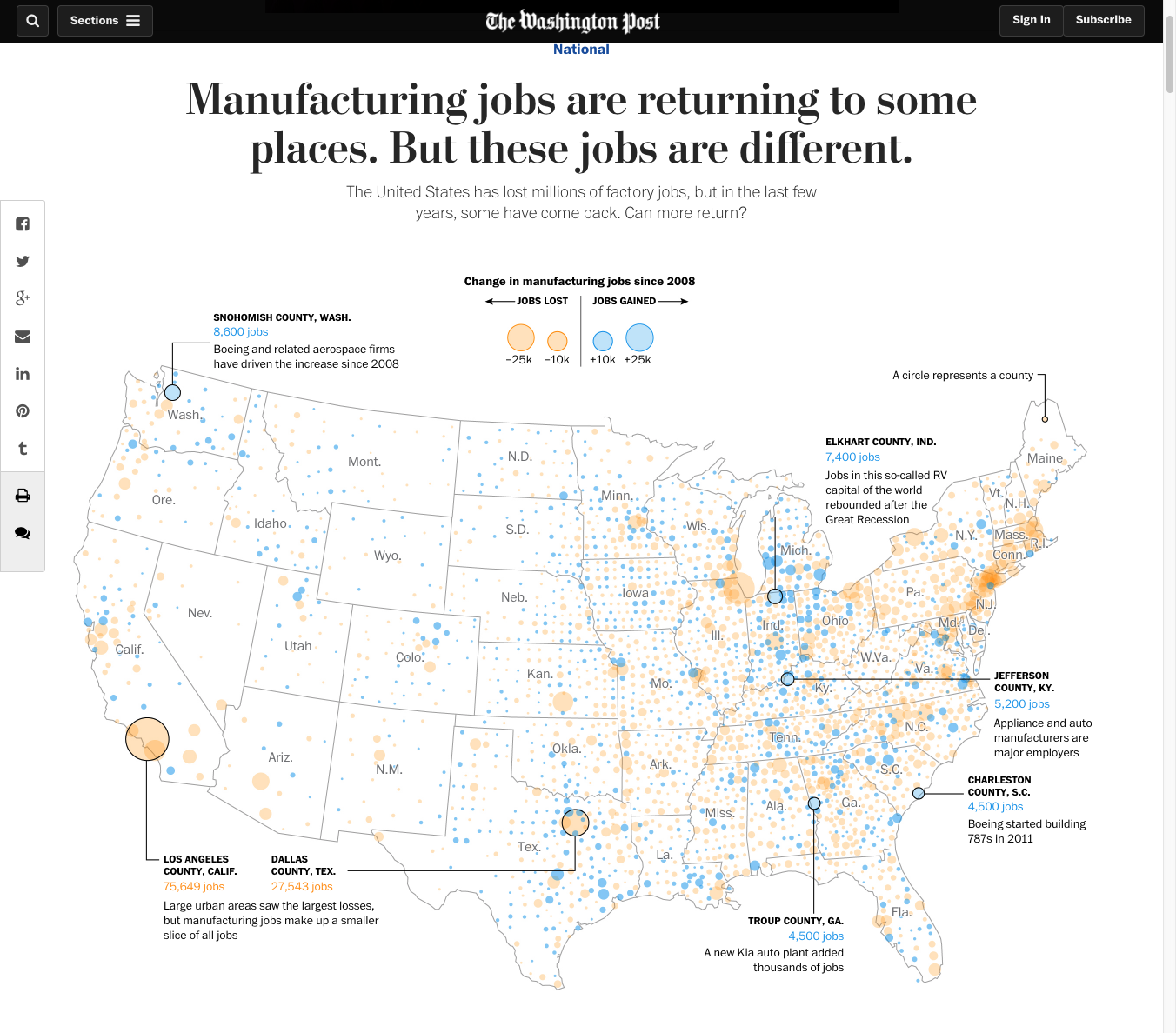
Job shop manufacturing can be described as a small-scale production system that specializes only in custom, batch and semi-custom manufacturing. After each job is complete, job shop systems can move to the next. This type of production is also known lean manufacturing. It is more efficient to use a single shift than many other methods. These are just a few of the many benefits of job-shop manufacturing. Learn more about this manufacturing method. This method of manufacturing might be beneficial for your business.
First, job shops must be more efficient. The incorporation of new manufacturing principles is crucial to creating a lean manufacturing environment. These principles, which emphasize total quality control as well as just-in-time manufacturing, are extremely relevant to high volume operations. By adopting new manufacturing principles, a job shop can increase productivity while lowering costs at the same time. Additionally, every job should be processed individually, so there should not be a queue.
Continuous manufacturing
One of the biggest benefits of continuous manufacturing is the fact that it allows for much more flexible tracking. This is especially beneficial when it concerns product failure. Since the production line's time stamp and the raw material quantity can help identify when a batch has gone wrong, continuous manufacturing allows for more flexible tracking. The increased tracking also helps the manufacturer reduce waste and the chance of a product shortage. Continuous manufacturing is also popular in the pharmaceutical business.
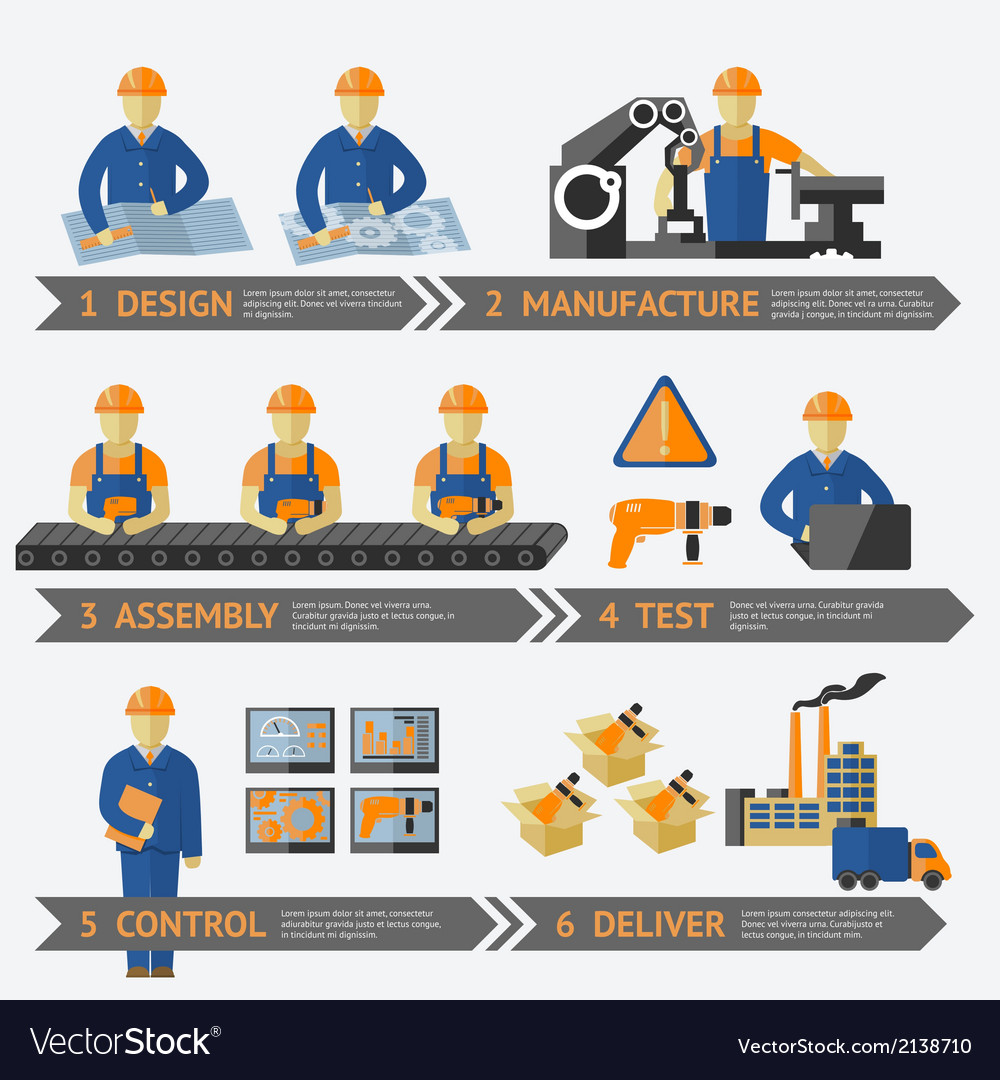
The benefits of continuous production are obvious, but implementation can be slow. The slow pace of implementation can make it difficult to integrate the manufacturing process with the rest. Continuous manufacturing can be a game-changer for the pharmaceutical sector, regardless of its benefits. But to be successful, the process must be integrated with end-to-end integration and continuous flow. The pharmaceutical industry has long recognized the benefits of continuous manufacturing, but implementation has been slow.
FAQ
What is the best way to learn about manufacturing?
Experience is the best way for you to learn about manufacturing. You can also read educational videos or take classes if this isn't possible.
What is it like to manage a logistics company?
You need to have a lot of knowledge and skills to manage a successful logistic business. You must have good communication skills to interact effectively with your clients and suppliers. You need to understand how to analyze data and draw conclusions from it. You need to be able work under pressure and manage stressful situations. In order to innovate and create new ways to improve efficiency, creativity is essential. You will need strong leadership skills to motivate and direct your team members towards achieving their organizational goals.
To meet tight deadlines, you must also be efficient and organized.
What are the four types in manufacturing?
Manufacturing refers the process of turning raw materials into useful products with machines and processes. It involves many different activities such as designing, building, testing, packaging, shipping, selling, servicing, etc.
What are the 7 R's of logistics?
The acronym 7R's for Logistics stands to represent the seven basic principles in logistics management. It was developed by International Association of Business Logisticians (IABL), and published as part of their "Seven Principles of Logistics Management Series" in 2004.
The following letters form the acronym:
-
Responsive - ensure all actions are legal and not harmful to others.
-
Reliable – have faith in your ability and capability to keep promises.
-
Use resources effectively and sparingly.
-
Realistic - Consider all aspects of operations, including environmental impact and cost effectiveness.
-
Respectful – Treat others fairly and equitably.
-
Be resourceful: Look for opportunities to save money or increase productivity.
-
Recognizable - provide customers with value-added services.
Statistics
- In the United States, for example, manufacturing makes up 15% of the economic output. (twi-global.com)
- According to a Statista study, U.S. businesses spent $1.63 trillion on logistics in 2019, moving goods from origin to end user through various supply chain network segments. (netsuite.com)
- Job #1 is delivering the ordered product according to specifications: color, size, brand, and quantity. (netsuite.com)
- Many factories witnessed a 30% increase in output due to the shift to electric motors. (en.wikipedia.org)
- It's estimated that 10.8% of the U.S. GDP in 2020 was contributed to manufacturing. (investopedia.com)
External Links
How To
How to Use the Just In Time Method in Production
Just-in time (JIT), is a process that reduces costs and increases efficiency in business operations. It allows you to get the right amount resources at the right time. This means that your only pay for the resources you actually use. Frederick Taylor was the first to coin this term. He developed it while working as a foreman during the early 1900s. He noticed that workers were often paid overtime when they had to work late. He decided to ensure workers have enough time to do their jobs before starting work to improve productivity.
JIT teaches you to plan ahead and prepare everything so you don’t waste time. You should also look at the entire project from start to finish and make sure that you have sufficient resources available to deal with any problems that arise during the course of your project. You'll be prepared to handle any potential problems if you know in advance. This will ensure that you don't spend more money on things that aren't necessary.
There are many types of JIT methods.
-
Demand-driven: This type of JIT allows you to order the parts/materials required for your project on a regular basis. This will allow for you to track the material that you have left after using it. This will allow to you estimate the time it will take for more to be produced.
-
Inventory-based : You can stock the materials you need in advance. This allows you to forecast how much you will sell.
-
Project-driven: This method allows you to set aside enough funds for your project. You will be able to purchase the right amount of materials if you know what you need.
-
Resource-based JIT is the most widespread form. You allocate resources based on the demand. You will, for example, assign more staff to deal with large orders. If you don't have many orders, you'll assign fewer people to handle the workload.
-
Cost-based: This approach is very similar to resource-based. However, you don't just care about the number of people you have; you also need to consider how much each person will cost.
-
Price-based: This is very similar to cost-based, except that instead of looking at how much each individual worker costs, you look at the overall price of the company.
-
Material-based: This approach is similar to cost-based. However, instead of looking at the total cost for the company, you look at how much you spend on average on raw materials.
-
Time-based JIT: This is another variant of resource-based JIT. Instead of focusing on how much each employee costs, you focus on how long it takes to complete the project.
-
Quality-based JIT: This is another variation of resource based JIT. Instead of focusing on the cost of each worker or how long it takes, think about how high quality your product is.
-
Value-based JIT: This is the latest form of JIT. In this instance, you are not concerned about the product's performance or meeting customer expectations. Instead, your focus is on the value you bring to the market.
-
Stock-based: This stock-based method focuses on the actual quantity of products being made at any given time. It's used when you want to maximize production while minimizing inventory.
-
Just-in-time planning (JIT): This is a combination JIT and supply-chain management. It's the process of scheduling delivery of components immediately after they are ordered. It reduces lead times and improves throughput.