
Three basic sectors are the basis of classical economics. These categories include manufacturing, services, as well as financial activities. The characteristics and risk factors that go into a business' classification are important. Here are some details about each of the sectors. Here is a quick overview of the different types of businesses within each sector. If you are interested, this information is available to further explore. Keep in mind, however, that these categories don't have to be mutually exclusive.
Economic activity
The factors that affect production, inputs and outputs have a significant impact on the country's economic activities. A region's ability to produce a particular product or service determines its economic activity. There are two types of economic activity: primary and secondary. Primary economic activities produce goods and services that satisfy human needs. While secondary economic activities add value by combining raw materials into a better product, they are not as valuable. Manufacturing and processing industries are examples of secondary economic activity.
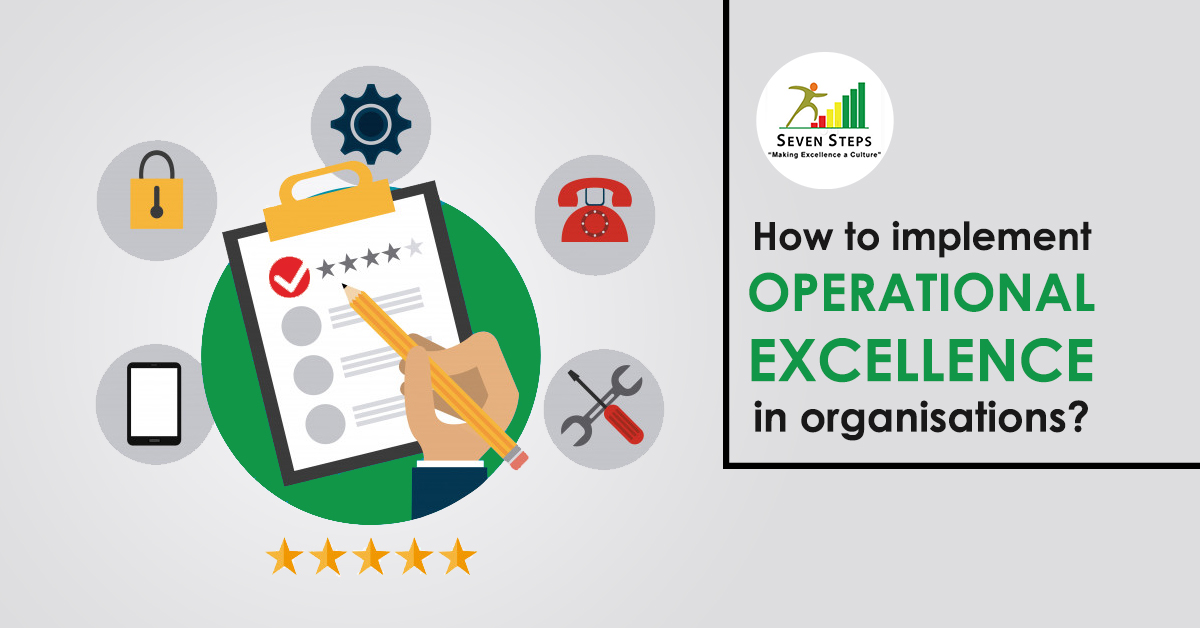
Classification of businesses
Business classification refers to the process of grouping businesses based on their activities. There are two types of businesses: primary and secondary. Primary businesses are those who extract and exchange natural resource. The second type of businesses process and convert raw materials into consumer-ready products. There are numerous differences between these two types of businesses. Listed below are some of the major differences between the two types. This article can be used to help you decide which business type is best for your company.
Characteristics
The following discussion explains the differences between the primary, secondary, and tertiary sectors and focuses on how each type of sector affects the economy. First, let's define sectors. Each sector is an economic entity that responds differently to different factors. These conditions can be repeated (e.g. business cycles) or one-off events (e.g. technological improvements). These characteristics can be helpful for identifying the most viable sectors, and for determining their relative importance in an economy.
Risques
Industry risk is the variation of performance across industries and among companies. It can be measured by assessing the variance in return on equity (ROE) and profitability. This may be influenced by the performance of stock market stocks, depending on the industry. An example of this is a steel company, which is considered to be at high risk because there are potential earthquakes in the region. These risks could help investors to determine which industries are more volatile.
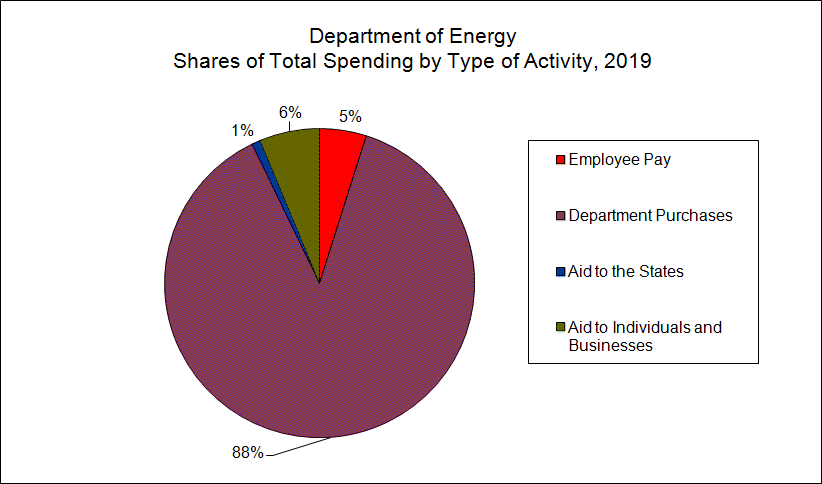
Investments
Although many investors prefer to invest in companies, it is possible to invest in sectors. Sectors can be found both in mutual funds as well as exchange-traded funds. They are safer and have lower risks. Sector investing is a popular strategy for investors today. This article will discuss how sector investing can help you find the right investments. Continue reading to find out more. You can also visit our free resource section for additional information.
FAQ
How does a production planner differ from a project manager?
The major difference between a Production Planner and a Project Manager is that a Project Manager is often the person responsible for organizing and planning the entire project. While a Production Planner is involved mainly in the planning stage,
What are manufacturing and logistics?
Manufacturing is the process of creating goods from raw materials by using machines and processes. Logistics is the management of all aspects of supply chain activities, including procurement, production planning, distribution, warehousing, inventory control, transportation, and customer service. Sometimes manufacturing and logistics are combined to refer to a wider term that includes both the process of creating products as well as their delivery to customers.
Is it necessary to be familiar with Manufacturing Processes before we learn about Logistics.
No. No. However, knowing about manufacturing processes will definitely give you a better understanding of how logistics works.
Is automation necessary in manufacturing?
Not only are service providers and manufacturers important, but so is automation. It enables them to provide services faster and more efficiently. In addition, it helps them reduce costs by reducing human errors and improving productivity.
Statistics
- [54][55] These are the top 50 countries by the total value of manufacturing output in US dollars for its noted year according to World Bank.[56] (en.wikipedia.org)
- According to a Statista study, U.S. businesses spent $1.63 trillion on logistics in 2019, moving goods from origin to end user through various supply chain network segments. (netsuite.com)
- In the United States, for example, manufacturing makes up 15% of the economic output. (twi-global.com)
- In 2021, an estimated 12.1 million Americans work in the manufacturing sector.6 (investopedia.com)
- Job #1 is delivering the ordered product according to specifications: color, size, brand, and quantity. (netsuite.com)
External Links
How To
How to Use 5S for Increasing Productivity in Manufacturing
5S stands as "Sort", Set In Order", Standardize", Separate" and "Store". The 5S methodology was developed at Toyota Motor Corporation in 1954. It helps companies achieve higher levels of efficiency by improving their work environment.
The basic idea behind this method is to standardize production processes, so they become repeatable, measurable, and predictable. This means that daily tasks such as cleaning and sorting, storage, packing, labeling, and packaging are possible. Because workers know what they can expect, this helps them perform their jobs more efficiently.
There are five steps that you need to follow in order to implement 5S. Each step involves a different action which leads to increased efficiency. By sorting, for example, you make it easy to find the items later. When you arrange items, you place them together. Once you have separated your inventory into groups and organized them, you will store these groups in easily accessible containers. You can also label your containers to ensure everything is properly labeled.
Employees need to reflect on how they do their jobs. Employees need to be able understand their motivations and discover alternative ways to do them. In order to use the 5S system effectively, they must be able to learn new skills.
The 5S method increases efficiency and morale among employees. Once they start to notice improvements, they are motivated to keep working towards their goal of increasing efficiency.