
The right qualifications are essential if you want to work as a maintenance engineer. Here are some of these certifications and the expected earnings. Maintenance engineers are a job that is perfect for those who have a keen eye for detail. These professionals are responsible in maintaining and optimizing a building’s infrastructure.
Qualifications for a career as a maintenance engineer
A few key things to consider when considering a career in maintenance engineering. You can get a high school diploma, but you should also consider enrolling in college courses in engineering. As well as work experience, courses in chemistry or math are beneficial. A technical school might be an option, depending on your company's needs.
Maintenance engineers are responsible for maintaining machinery and equipment as well as infrastructures, systems, and systems. They are responsible for maintaining industrial machinery as efficient as possible. They also oversee the provision of spare parts. Some jobs in this field require shift work, particularly those involved in manufacturing. Maintenance engineers can work in management roles or other related fields depending on the nature of their job. After they have gained experience, they may be able to start their own business.
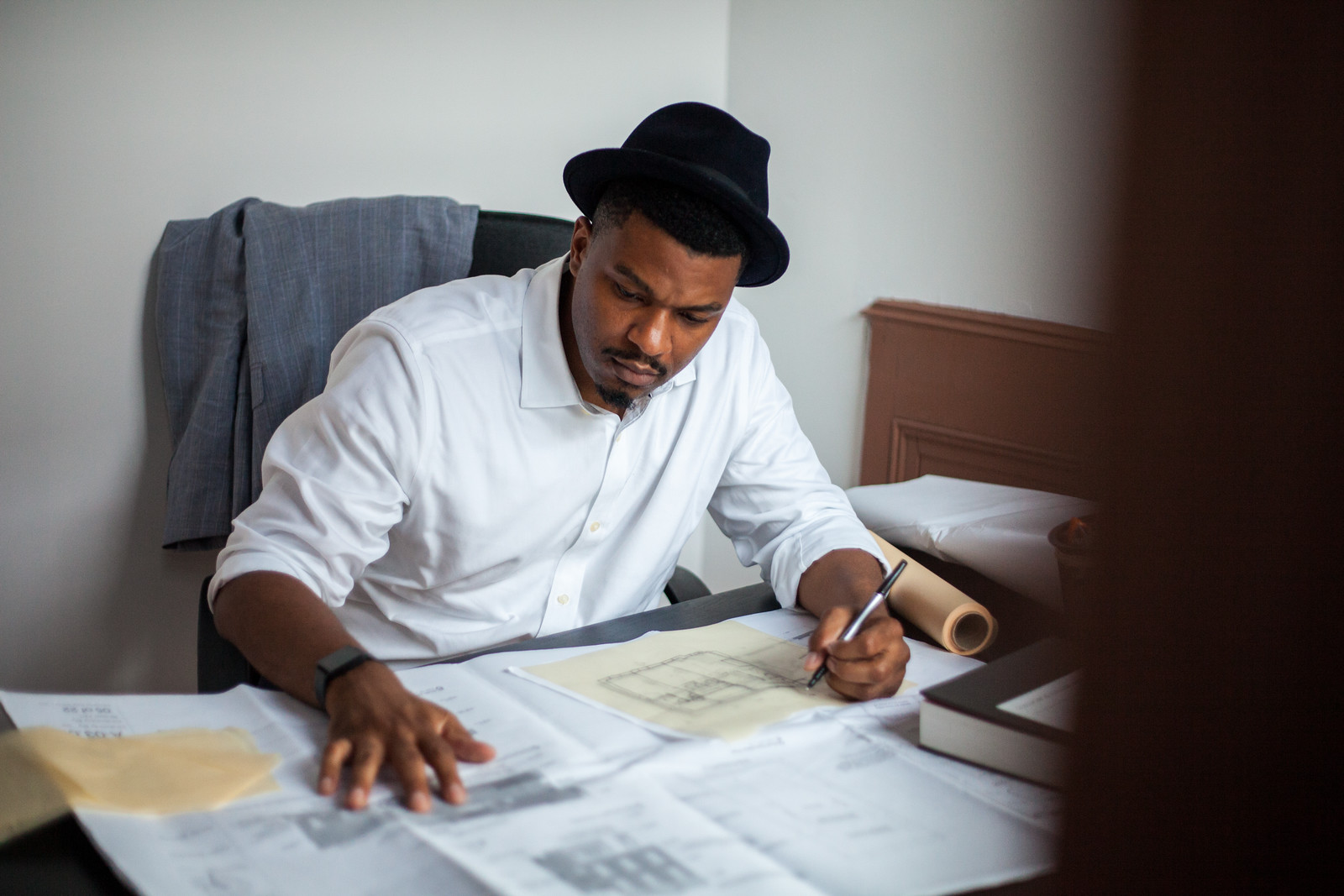
Maintenance engineers typically earn between PS20,000-PS25,000. Salary ranges can vary depending on industry, size, and location. An engineer who is skilled in maintenance can be promoted to management positions. You may also be able to achieve Chartered status, which can help you move up in your career.
Certifications required
As a maintenance engineer, you may be required to hold several certifications. These certifications can be specific to one system or may relate to hazardous material handling. The International Maintenance Institute offers several levels of professional certification. These include lower-level certifications for Certified Maintenance Technicians, as well as higher-level certifications for Certified Maintenance Professionals and Maintenance Managers.
It is important to consider your education background if you are interested in becoming a maintenance engineer. Most certification companies don't require a specific education, but some recommend having a high-school diploma or GED. Employers and recruiters generally require this minimum requirement. However, you can also obtain a certification without a degree if you've had previous work experience in a similar industry.
While a bachelor's degree isn't required to become a maintenance engineer, having a degree in an appropriate field will help you stand out from the competition. It may be beneficial to have a degree in facilities management, mechanical engineering, or electrical engineering. Even if you don’t have an engineering degree you might still be able to work as a maintenance technie or progress to the position of maintenance engineer through training and experience.
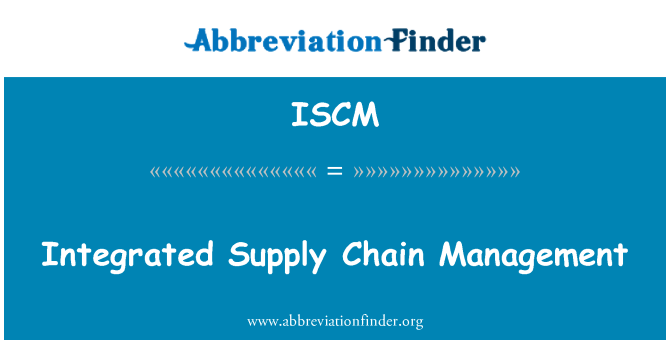
Salary
Although the Bureau of Labor Statistics doesn't monitor the salaries of maintenance engineers, it projects job growth in related areas. In general maintenance, engineers and mechanical technicians are expected to see eight percent growth, while construction management managers might see an 11 percent increase in their employment. If you are interested in a career as maintenance engineer, then you should look for entry-level jobs within industries that have high job growth.
Salary for maintenance engineer: In 2008, the median salary for maintenance engineers was $88,570. The lowest 25 % earned $48,270, and the highest 10 % earned more that $110,310.
FAQ
How can I learn about manufacturing?
Experience is the best way for you to learn about manufacturing. If that is not possible, you could always read books or view educational videos.
Why automate your warehouse?
Modern warehousing is becoming more automated. E-commerce has increased the demand for quicker delivery times and more efficient processes.
Warehouses must be able to quickly adapt to changing demands. To do so, they must invest heavily in technology. Automation warehouses can bring many benefits. Here are some benefits of investing in automation
-
Increases throughput/productivity
-
Reduces errors
-
Increases accuracy
-
Safety enhancements
-
Eliminates bottlenecks
-
Allows companies scale more easily
-
Workers are more productive
-
The warehouse can be viewed from all angles.
-
Enhances customer experience
-
Improves employee satisfaction
-
Minimizes downtime and increases uptime
-
This ensures that quality products are delivered promptly
-
Removing human error
-
It ensures compliance with regulations
Is automation important in manufacturing?
Automation is important not only for manufacturers but also for service providers. It enables them to provide services faster and more efficiently. It also helps to reduce costs and improve productivity.
What are the 7 Rs of logistics?
The acronym 7Rs of Logistics refers to the seven core principles of logistics management. It was developed by International Association of Business Logisticians (IABL), and published as part of their "Seven Principles of Logistics Management Series" in 2004.
The acronym is composed of the following letters.
-
Responsible – ensure that all actions are legal and don't cause harm to anyone else.
-
Reliable - Have confidence in your ability to fulfill all of your commitments.
-
It is reasonable to use resources efficiently and not waste them.
-
Realistic - Consider all aspects of operations, including environmental impact and cost effectiveness.
-
Respectful – Treat others fairly and equitably.
-
Resourceful - look for opportunities to save money and increase productivity.
-
Recognizable - provide customers with value-added services.
Statistics
- Many factories witnessed a 30% increase in output due to the shift to electric motors. (en.wikipedia.org)
- According to a Statista study, U.S. businesses spent $1.63 trillion on logistics in 2019, moving goods from origin to end user through various supply chain network segments. (netsuite.com)
- It's estimated that 10.8% of the U.S. GDP in 2020 was contributed to manufacturing. (investopedia.com)
- In the United States, for example, manufacturing makes up 15% of the economic output. (twi-global.com)
- According to the United Nations Industrial Development Organization (UNIDO), China is the top manufacturer worldwide by 2019 output, producing 28.7% of the total global manufacturing output, followed by the United States, Japan, Germany, and India.[52][53] (en.wikipedia.org)
External Links
How To
How to use 5S to increase Productivity in Manufacturing
5S stands as "Sort", Set In Order", Standardize", Separate" and "Store". Toyota Motor Corporation developed the 5S method in 1954. It helps companies achieve higher levels of efficiency by improving their work environment.
This method aims to standardize production processes so that they are repeatable, measurable and predictable. This means that daily tasks such as cleaning and sorting, storage, packing, labeling, and packaging are possible. Workers can be more productive by knowing what to expect.
There are five steps to implementing 5S, including Sort, Set In Order, Standardize, Separate and Store. Each step requires a different action, which increases efficiency. By sorting, for example, you make it easy to find the items later. Once you have placed items in an ordered fashion, you will put them together. After you have divided your inventory into groups you can store them in easy-to-reach containers. Finally, label all containers correctly.
Employees will need to be more critical about their work. Employees need to be able understand their motivations and discover alternative ways to do them. They must learn new skills and techniques in order to implement the 5S system.
In addition to improving efficiency, the 5S system also increases morale and teamwork among employees. As they begin to see improvements, they feel motivated to continue working towards the goal of achieving higher levels of efficiency.