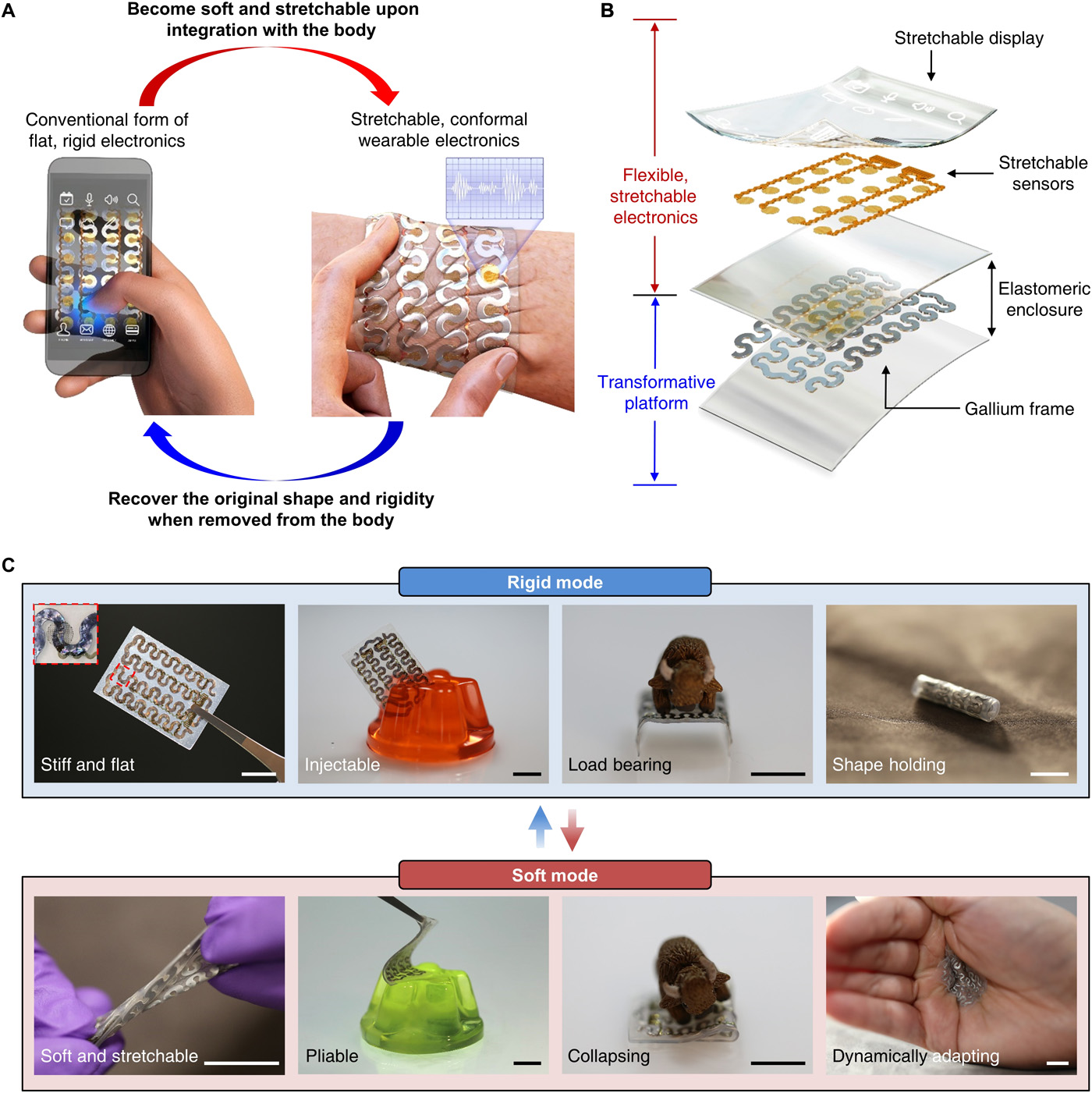
There are many types and styles of manufacturers. Which one is best for you business? Learn more about continuous manufacturing, process manufacturing, job shop manufacturing, and discrete manufacturing. Each type comes with its own set of advantages and disadvantages. This article will explain how these four types of manufacturing differ. Based on your industry, your location and your product type, you can determine which model is best for your company. Once you've decided on the right type, you should consider your sales, manufacturing, and quality control.
Displacement manufacturing
Discrete production is when distinct products are manufactured. These products can include toys, airplanes, and automobiles. Discrete manufacturing allows companies the freedom to concentrate on specific products rather than mass production. It is possible, for instance, to make unique parts of an aeroplane through the integration of several manufacturing processes. High-tech products are made using discrete manufacturing.
Discrete manufacturing produces distinct items. Instead of producing identical products, discrete Manufacturing produces items that can readily be identified by serial numbers or labels. One example is a smartphone that may be made from many parts, each of which are assembled when the product is finished. This is also true for the bag. It could be made up of different parts, including those from the Missouri plant or headquarters.
Process manufacturing
The idea of process manufacturing is a sub-field of manufacturing that includes formulas and recipes. This term contrasts with discrete manufacture, which is concerned only with the production of individual units and bills of materials. The process manufacturing concept also includes the assembly of parts. Both manufacturing methods have different goals. However, each is an essential part of the manufacturing process. Here are three different ways to distinguish process manufacturing and discrete production. Let's look at each one.
Batch manufacturing is similar to continuous manufacturing but uses larger quantities of raw materials and can run around the clock. It is commonly used in pharmaceuticals as well as paper production, bookbinding and newspaper printing. However, this method isn't the best fit for every industry. This method is often too complicated and expensive for small-scale businesses. Therefore, most companies use this method when they need to create large quantities of the same product.
Job shop manufacturing
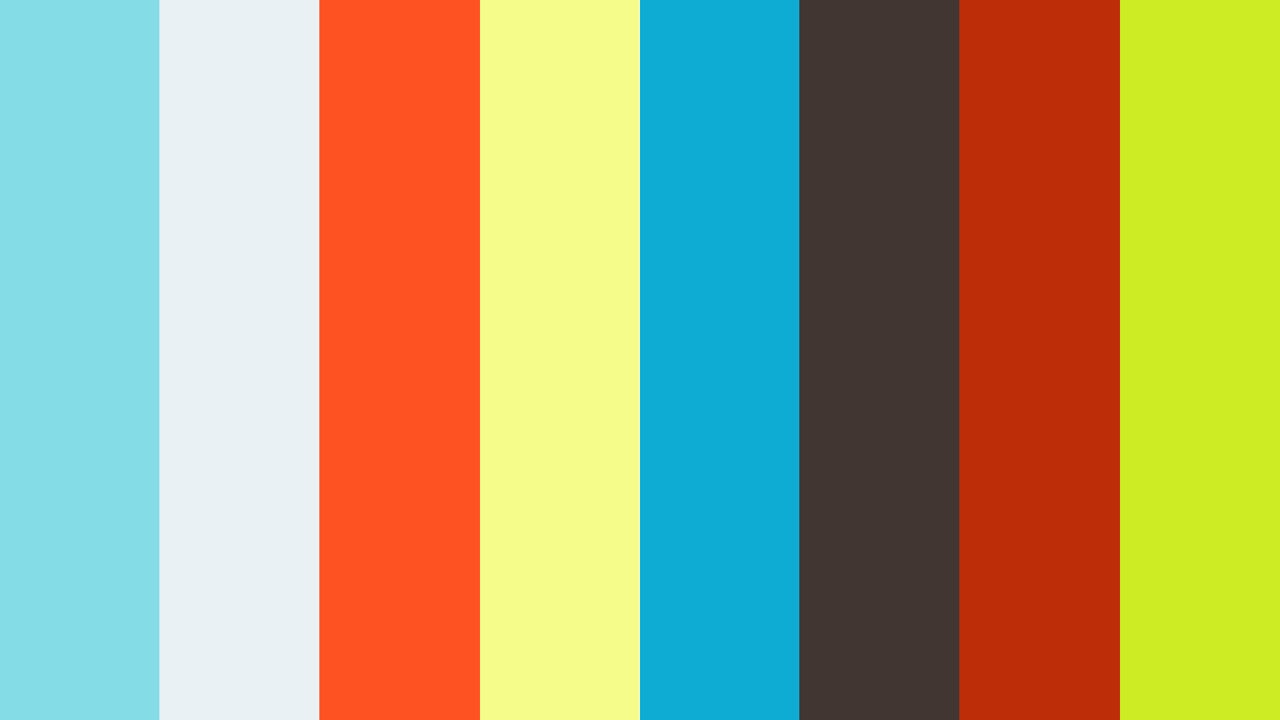
Job shop manufacturing refers to a small-scale, specialized production line that is focused on custom, batch, and semicustom manufacturing. Job shop systems can then move on to the next job as each job is finished. This method of production is also called lean manufacturing, as a single-shift operation is more efficient than many other methods. These are just a few of the many benefits of job-shop manufacturing. Continue reading to learn more about job shop manufacturing. For your business, you might want to consider it for your product or service needs.
First, job shop efficiency must be improved. A critical factor in achieving a lean manufacturing system is incorporating new manufacturing principles. These principles focus on quality control and justin-time production and are especially relevant for high-volume operations. Job shops can increase productivity and decrease costs by adopting new manufacturing methods. Additionally, jobs should proceed through each process one at a time, so there should be no queues.
Continuous manufacturing
Continuous manufacturing offers many benefits, including the flexibility of tracking. This is especially helpful in the event of product failure. Product data such as the amount of raw material used and the time stamp at each production line can be used for identifying defective batches. The manufacturer also has a reduced risk of product shortages due to increased tracking. Continuous manufacturing is also becoming more popular in the pharmaceutical sector.
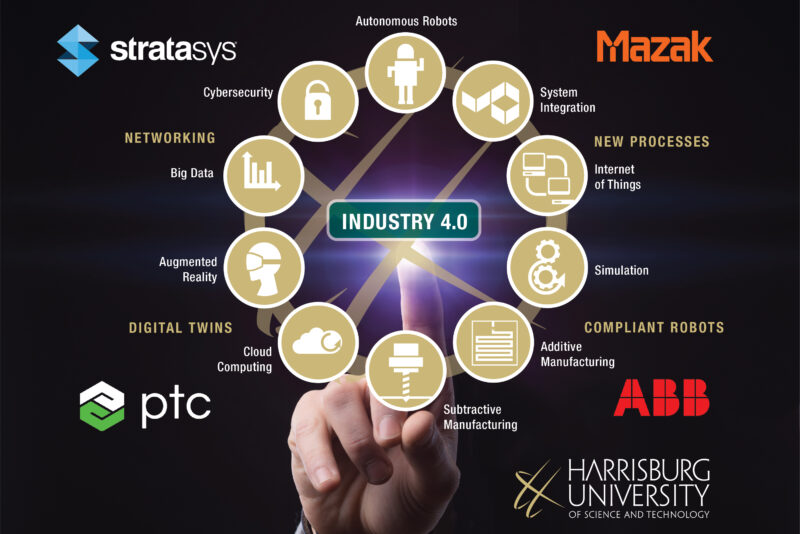
Although continuous manufacturing has many benefits, implementation can be difficult. The lack of integration with other departments can often make implementation difficult. Regardless of the benefits, continuous manufacturing has the potential to be a game changer for the pharmaceutical industry. To be successful, however, the entire process must be integrated with continuous flow as well as end-to–end integration. The benefits of continuous manufacture have long been recognized by the pharmaceutical industries, but implementation has been slow.
FAQ
What does "warehouse" mean?
A warehouse is an area where goods are stored before being sold. You can have it indoors or outdoors. In some cases it could be both indoors and outdoors.
What is the responsibility of a manufacturing manager?
The manufacturing manager should ensure that every manufacturing process is efficient and effective. They must also be alert to any potential problems and take appropriate action.
They should also learn how to communicate effectively with other departments, including sales and marketing.
They should also be aware of the latest trends in their industry and be able to use this information to help improve productivity and efficiency.
What are manufacturing & logistics?
Manufacturing is the process of creating goods from raw materials by using machines and processes. Logistics manages all aspects of the supply chain, including procurement, production planning and distribution, inventory control, transportation, customer service, and transport. As a broad term, manufacturing and logistics often refer to both the creation and delivery of products.
What are the 7 Rs of logistics management?
The acronym 7R's of Logistic is an acronym that stands for seven fundamental principles of logistics management. It was created by the International Association of Business Logisticians and published in 2004 under its "Seven Principles of Logistics Management".
The acronym is composed of the following letters.
-
Responsible – ensure that all actions are legal and don't cause harm to anyone else.
-
Reliable – have faith in your ability and capability to keep promises.
-
Reasonable - make sure you use your resources well and don't waste them.
-
Realistic - Consider all aspects of operations, including environmental impact and cost effectiveness.
-
Respectful - show respect and treat others fairly and fairly
-
Be resourceful: Look for opportunities to save money or increase productivity.
-
Recognizable - Provide value-added services to customers
How can I find out more about manufacturing?
Experience is the best way for you to learn about manufacturing. But if that is not possible you can always read books and watch educational videos.
Statistics
- [54][55] These are the top 50 countries by the total value of manufacturing output in US dollars for its noted year according to World Bank.[56] (en.wikipedia.org)
- It's estimated that 10.8% of the U.S. GDP in 2020 was contributed to manufacturing. (investopedia.com)
- In the United States, for example, manufacturing makes up 15% of the economic output. (twi-global.com)
- According to a Statista study, U.S. businesses spent $1.63 trillion on logistics in 2019, moving goods from origin to end user through various supply chain network segments. (netsuite.com)
- (2:04) MTO is a production technique wherein products are customized according to customer specifications, and production only starts after an order is received. (oracle.com)
External Links
How To
Six Sigma: How to Use it in Manufacturing
Six Sigma refers to "the application and control of statistical processes (SPC) techniques in order to achieve continuous improvement." Motorola's Quality Improvement Department in Tokyo, Japan developed Six Sigma in 1986. Six Sigma's main goal is to improve process quality by standardizing processes and eliminating defects. Many companies have adopted Six Sigma in recent years because they believe that there are no perfect products and services. Six Sigma's main objective is to reduce variations from the production average. This means that if you take a sample of your product, then measure its performance against the average, you can find out what percentage of the time the process deviates from the norm. If there is a significant deviation from the norm, you will know that something needs to change.
The first step toward implementing Six Sigma is understanding how variability works in your business. Once you understand that, it is time to identify the sources of variation. These variations can also be classified as random or systematic. Random variations occur when people make mistakes; systematic ones are caused by factors outside the process itself. Random variations would include, for example, the failure of some widgets to fall from the assembly line. However, if you notice that every time you assemble a widget, it always falls apart at exactly the same place, then that would be a systematic problem.
Once you identify the problem areas, it is time to create solutions. That solution might involve changing the way you do things or redesigning the process altogether. To verify that the changes have worked, you need to test them again. If they don’t work, you’ll need to go back and rework the plan.