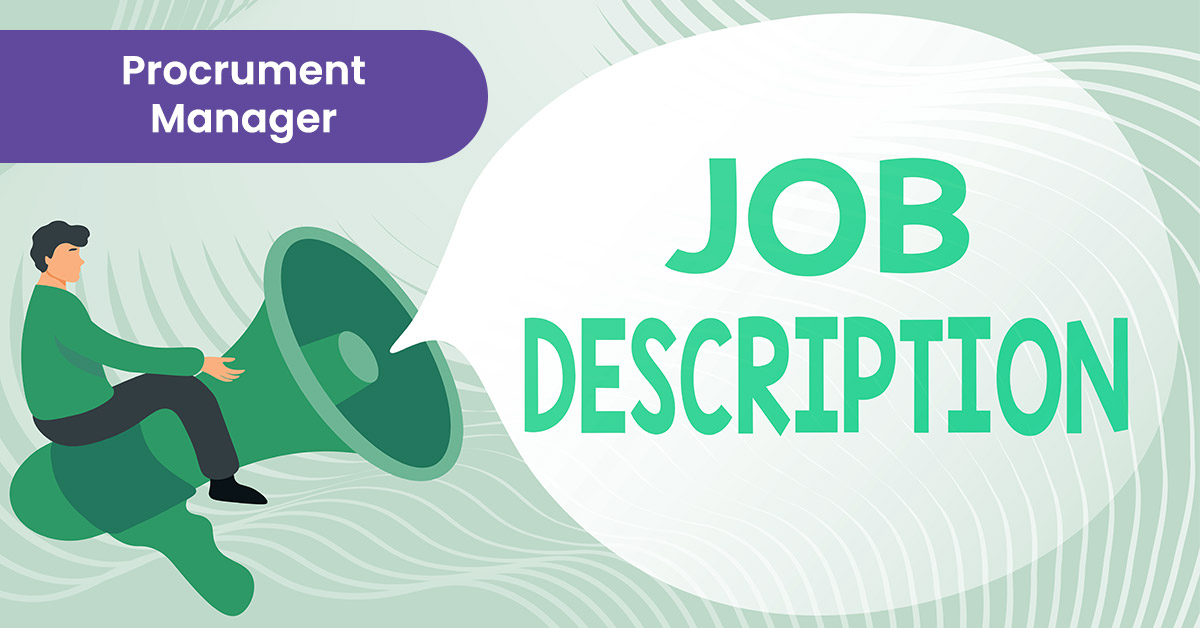
You've found the right place if you are looking for news on manufacturing. Fusion 360 community members review the week's events, and share news about innovation in manufacturing. Fusion 360 covers all aspects of the industry, including Alexandria Industries and Festo's expansion plans. Fusion 360 covers everything from the latest product launches, to news about additive production. Here are some recent articles regarding manufacturing innovation. Continue reading for more information.
Alexandria Industries
Alexandria Industries recently announced that they are expanding their operations in Douglas County. While they currently employ 480 people, the company is investing several million dollars in the new facility to grow even more. Although Alexandria Industries has long outpaced employment and revenue levels prior to the recession, they still struggle to find qualified applicants for 50 new jobs. These positions have a starting salary of $15- $30 per hour and include benefits. Alexandria Industries offers a great career opportunity for those who are interested in a change.
Alexandria Industries recently appointed new management to aid their growth. Jonathan D. Olson will be the CFO of Alexandria Industries. He is determined to make investments in the company, and the people who work there. He was also appointed the company's CFO. He is looking to improve the working environment of employees and invest heavily in training programs. Alexandria Plastics, Inc., a manufacturer and distributor of foam-molded and plastic injection parts, will be integrated into this acquisition, which will enhance the company’s capabilities.
Festo U.S. expansion plans
Festo Corp. recently announced expansion plans for its North American manufacturing operations. The company will increase its presence in Mason by three times and create 350 additional jobs. This expansion will bring in $90 million and create new jobs over five more years. In addition to manufacturing, Festo will provide industrial training solutions and support services. The expansion will also include a new Didactic Education Center to provide support services for manufacturing businesses and colleges throughout the Tristate.
The expansion will see the construction of a new Mason, Ohio plant that manufactures automation components. This new facility will house both the Research and Development Center and Global Production Center. The new facility will house a Research and Development Center as well as a Global Production Center. In addition to creating new jobs, the company plans to establish a new research and development center to enhance automation systems. This expansion is part the company's larger plan to target the U.S. market.
Additive Manufacturing
With the advancement of technology, manufacturers have begun to see the benefits of additive manufacturing in the manufacturing process. A number of companies have recently announced partnerships to reach the global markets. Voxeljet, a glass- and ceramic company, is one example of such partnerships. Voxeljet & AGC Ceramic plan to launch Brightorb, a high performance ceramic material, as well as optimize the VX1000 for 3D-printing ceramic powder. Stratasys has partnered up with Tata Technologies in order to promote additive manufacturing technology in India.
New technologies are being developed to aid in the additive manufacturing process. Optimus 3D recently acquired a fourth Renishaw Metal additive manufacturing system. Moreover, the company has also expanded its 3D printing machine portfolio to include metal powder. With these developments additive manufacturing will soon be an integral part in advanced PLM. This will allow for a more IoT-oriented and integrated approach to additive manufacturing. These innovations will facilitate the rapid growth and diversification of many industries.
Collaborative Manufacturing
What is collaborative production? Collaborative production involves direct input from the plant floors. This information is crucial for the management process. It involves both the design and manufacturing teams working together. Collaboration can help increase productivity and quality while reducing the need for workers in each stage of production. What are the advantages of collaborative manufacturing? Let's take a look at some examples. How can collaborative production improve plant performance? Learn more.
Several industries are embracing collaborative manufacturing. It's used to increase product design, streamline logistics, and help with product development. In addition, collaborative manufacturing helps reduce time-to-market and volume, and can cut manufacturing cycle time among designated suppliers. It is important for companies to realize that collaborative manufacturing offers significant benefits for everyone. This isn't for every company. Before adopting collaborative manufacturing, consider the benefits.
FAQ
What are the 7 Rs of logistics?
The acronym 7R's for Logistics stands to represent the seven basic principles in logistics management. It was developed and published by the International Association of Business Logisticians in 2004 as part of the "Seven Principles of Logistics Management".
The acronym is made up of the following letters:
-
Responsible - to ensure that all actions are within the legal requirements and are not detrimental to others.
-
Reliable – have faith in your ability and capability to keep promises.
-
Use resources effectively and sparingly.
-
Realistic - consider all aspects of operations, including cost-effectiveness and environmental impact.
-
Respectful: Treat others with fairness and equity
-
You are resourceful and look for ways to save money while increasing productivity.
-
Recognizable is a company that provides customers with value-added solutions.
How can we increase manufacturing efficiency?
First, identify the factors that affect production time. The next step is to identify the most important factors that affect production time. If you don't know where to start, then think about which factor(s) have the biggest impact on production time. Once you have identified the factors, then try to find solutions.
What is the job of a logistics manger?
Logistics managers are responsible for ensuring that all goods arrive in perfect condition and on time. This is done by using his/her experience and knowledge of the company's products. He/she should make sure that enough stock is on hand to meet the demands.
How can manufacturing reduce production bottlenecks?
Avoiding production bottlenecks is as simple as keeping all processes running smoothly, from the time an order is received until the product ships.
This includes planning to meet capacity requirements and quality control.
Continuous improvement techniques such Six Sigma can help you achieve this.
Six Sigma is a management method that helps to improve quality and reduce waste.
It emphasizes consistency and eliminating variance in your work.
What is the importance of automation in manufacturing?
Not only is automation important for manufacturers, but it's also vital for service providers. They can provide services more quickly and efficiently thanks to automation. It also helps to reduce costs and improve productivity.
Statistics
- (2:04) MTO is a production technique wherein products are customized according to customer specifications, and production only starts after an order is received. (oracle.com)
- You can multiply the result by 100 to get the total percent of monthly overhead. (investopedia.com)
- According to a Statista study, U.S. businesses spent $1.63 trillion on logistics in 2019, moving goods from origin to end user through various supply chain network segments. (netsuite.com)
- According to the United Nations Industrial Development Organization (UNIDO), China is the top manufacturer worldwide by 2019 output, producing 28.7% of the total global manufacturing output, followed by the United States, Japan, Germany, and India.[52][53] (en.wikipedia.org)
- [54][55] These are the top 50 countries by the total value of manufacturing output in US dollars for its noted year according to World Bank.[56] (en.wikipedia.org)
External Links
How To
How to Use the Just-In-Time Method in Production
Just-intime (JIT), which is a method to minimize costs and maximize efficiency in business process, is one way. It is a process where you get the right amount of resources at the right moment when they are needed. This means that your only pay for the resources you actually use. Frederick Taylor, a 1900s foreman, first coined the term. He observed how workers were paid overtime if there were delays in their work. He concluded that if workers were given enough time before they start work, productivity would increase.
JIT is a way to plan ahead and make sure you don't waste any money. The entire project should be looked at from start to finish. You need to ensure you have enough resources to tackle any issues that might arise. If you anticipate that there might be problems, you'll have enough people and equipment to fix them. This will prevent you from spending extra money on unnecessary things.
There are several types of JIT techniques:
-
Demand-driven JIT: This is a JIT that allows you to regularly order the parts/materials necessary for your project. This will allow you to track how much material you have left over after using it. This will let you know how long it will be to produce more.
-
Inventory-based: This type allows you to stock the materials needed for your projects ahead of time. This allows you to forecast how much you will sell.
-
Project-driven: This approach involves setting aside sufficient funds to cover your project's costs. You will be able to purchase the right amount of materials if you know what you need.
-
Resource-based JIT: This is the most popular form of JIT. You allocate resources based on the demand. For example, if there is a lot of work coming in, you will have more people assigned to them. If you don't receive many orders, then you'll assign fewer employees to handle the load.
-
Cost-based : This is similar in concept to resource-based. But here, you aren't concerned about how many people your company has but how much each individual costs.
-
Price-based: This approach is very similar to the cost-based method except that you don't look at individual workers costs but the total cost of the company.
-
Material-based: This is quite similar to cost-based, but instead of looking at the total cost of the company, you're concerned with how much raw materials you spend on average.
-
Time-based: Another variation of resource-based JIT. Instead of focusing on how much each employee costs, you focus on how long it takes to complete the project.
-
Quality-based JIT - This is another form of resource-based JIT. Instead of worrying about the costs of each employee or how long it takes for something to be made, you should think about how quality your product is.
-
Value-based JIT : This is the newest type of JIT. In this scenario, you're not concerned about how products perform or whether customers expect them to meet their expectations. Instead, you're focused on how much value you add to the market.
-
Stock-based is an inventory-based system that measures the number of items produced at any given moment. It is used when production goals are met while inventory is kept to a minimum.
-
Just-in-time planning (JIT): This is a combination JIT and supply-chain management. This refers to the scheduling of the delivery of components as soon after they are ordered. It's important as it reduces leadtimes and increases throughput.