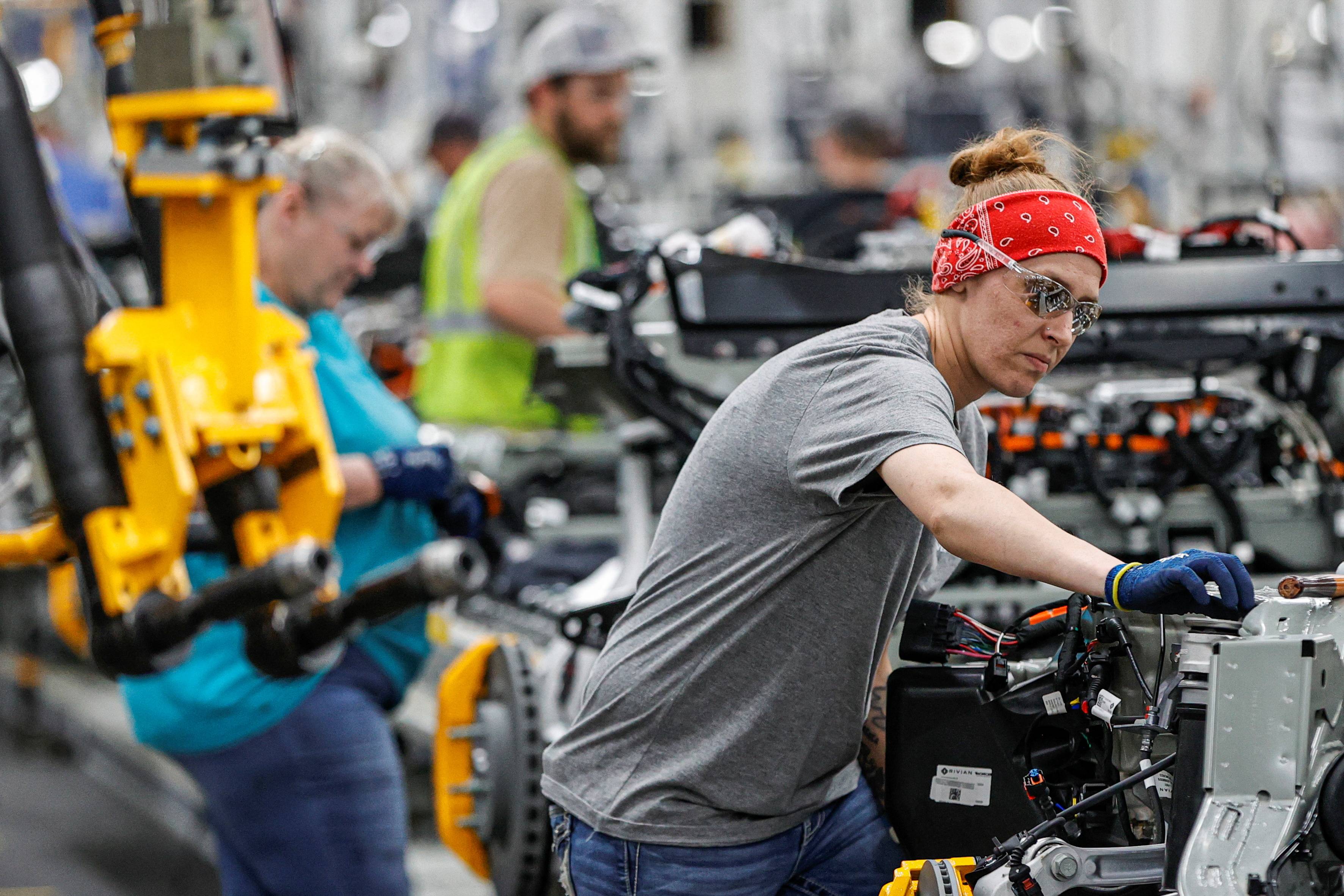
The Production Development Engineer is responsible to optimize production processes within the manufacturing environment. The responsibilities include creating a team working environment to ensure quality and on-time delivery of products. It is crucial that you are adaptable and innovative as well as a skilled communicator. Strong analytical and development skills are also essential.
The Production Development Engineer is part of the Advanced Manufacturing Engineering Team. He or she works in cross-functional team. He/she will look for problems in current product and development processes and then use process tech to increase productivity and quality, decrease costs, and reduce cost. Additionally, the Production Development Engineer works with external vendors in order to solve technical problems.
This position requires an engineering bachelor's degree and the candidate should have at least 3 years of experience working in a manufacturing environment. It is desirable to have a strong understanding of Lean Manufacturing. A good understanding of technical communication is a must. If you have a passion for innovation and cost-effective solutions, you can be a great asset to the Production Development Team.
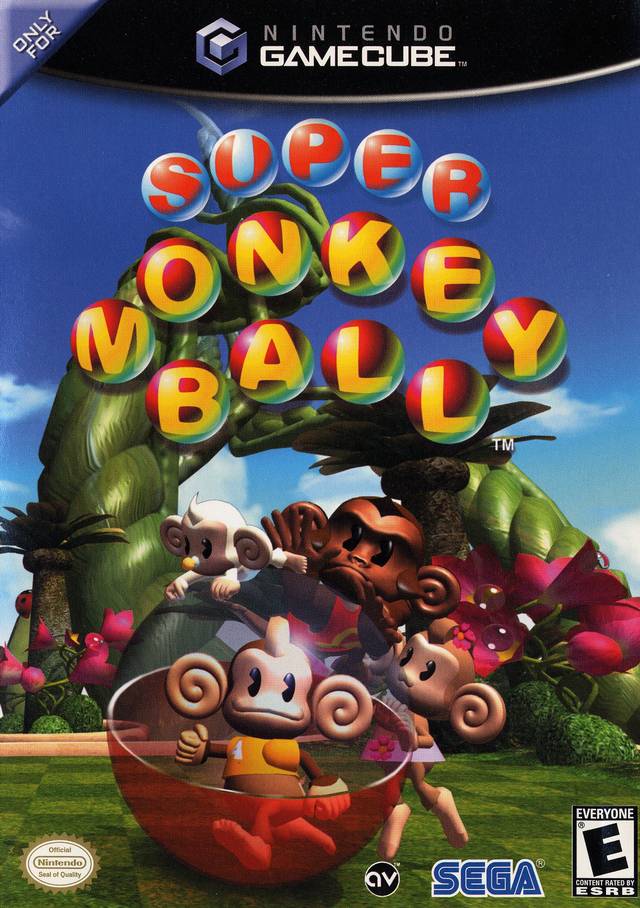
The product engineers are those who create new products. Their duties include identifying consumer needs and preferences, analyzing data, and developing product prototypes. They also manage quality control and prepare specifications for production. At the same time, they analyze and test the proposed product to determine any problems or design tolerances. These tasks require good mathematical and analytical abilities.
A production development engineer who is successful will be creative and efficient. Not only must he/she be skilled in the design of new products, but he/she also needs to be able to satisfy budgetary expectations as well as stakeholder requirements. You will need to have extensive product knowledge and be familiar with manufacturing processes.
Product engineers are typically skilled in areas such as software, electrical, and materials. Other areas of expertise include optics, mechanics or testing. The production development engineer will participate in every stage during a project. He or she will be responsible for ensuring that production methods and equipment are used in order to achieve the product's quality goals, as well as cost and time.
During the product development phase, the Product Development Engineer will review and test the product for potential issues or design tolerances. Next, the Product Development Engineer will design a new prototype using built-in control elements that help to save money during manufacturing.
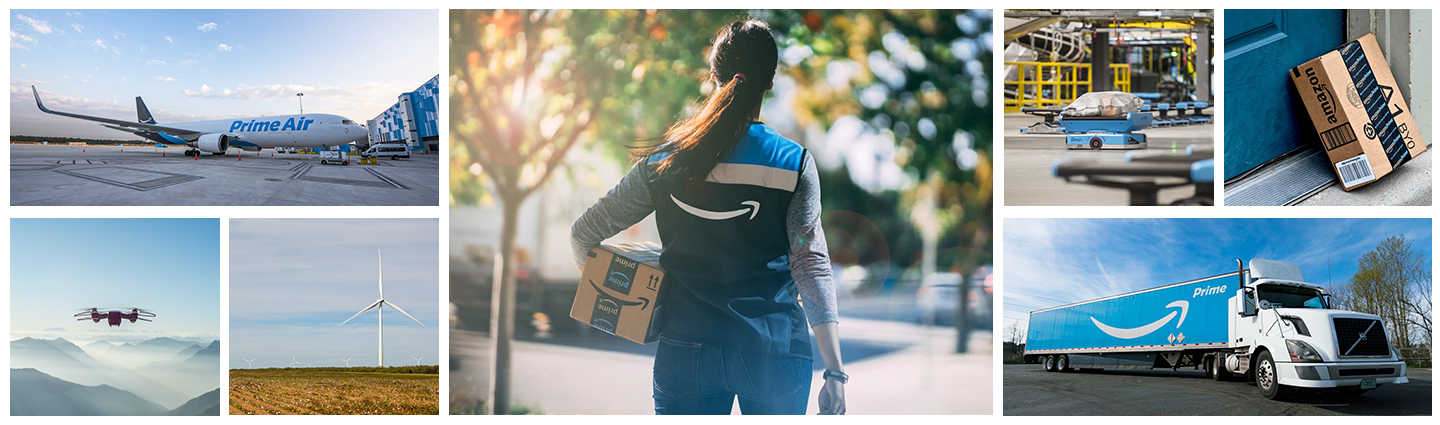
After the design has been completed, the Product Development Engineer will coordinate all activities with other departments and develop a quality control plan to ensure that the product meets its requirements. This includes all safety and environmental issues. Finally, the engineer will submit approved product plans for production to the team.
The Production Development Engineer must have a good working knowledge of 3D modeling and surface modelling software. A background in the assembly industry is a plus.
FAQ
What are the responsibilities of a manufacturing manager
The manufacturing manager should ensure that every manufacturing process is efficient and effective. They should also be aware and responsive to any company problems.
They should also be able communicate with other departments, such as sales or marketing.
They must also keep up-to-date with the latest trends in their field and be able use this information to improve productivity and efficiency.
What is manufacturing and logistics?
Manufacturing is the process of creating goods from raw materials by using machines and processes. Logistics manages all aspects of the supply chain, including procurement, production planning and distribution, inventory control, transportation, customer service, and transport. Logistics and manufacturing are often referred to as one thing. It encompasses both the creation of products and their delivery to customers.
What is the best way to learn about manufacturing?
Hands-on experience is the best way to learn more about manufacturing. If that is not possible, you could always read books or view educational videos.
Statistics
- In 2021, an estimated 12.1 million Americans work in the manufacturing sector.6 (investopedia.com)
- According to a Statista study, U.S. businesses spent $1.63 trillion on logistics in 2019, moving goods from origin to end user through various supply chain network segments. (netsuite.com)
- In the United States, for example, manufacturing makes up 15% of the economic output. (twi-global.com)
- Job #1 is delivering the ordered product according to specifications: color, size, brand, and quantity. (netsuite.com)
- (2:04) MTO is a production technique wherein products are customized according to customer specifications, and production only starts after an order is received. (oracle.com)
External Links
How To
How to Use lean manufacturing in the Production of Goods
Lean manufacturing (or lean manufacturing) is a style of management that aims to increase efficiency, reduce waste and improve performance through continuous improvement. It was created in Japan by Taiichi Ohno during the 1970s and 80s. He received the Toyota Production System award (TPS), from Kanji Toyoda, founder of TPS. Michael L. Watkins published the original book on lean manufacturing, "The Machine That Changed the World," in 1990.
Lean manufacturing refers to a set of principles that improve the quality, speed and costs of products and services. It emphasizes eliminating waste and defects throughout the value stream. Just-in-time (JIT), zero defect (TPM), and 5S are all examples of lean manufacturing. Lean manufacturing focuses on eliminating non-value-added activities such as rework, inspection, and waiting.
Lean manufacturing improves product quality and costs. It also helps companies reach their goals quicker and decreases employee turnover. Lean manufacturing has been deemed one of the best ways to manage the entire value-chain, including customers, distributors as well retailers and employees. Many industries worldwide use lean manufacturing. Toyota's philosophy has been a key driver of success in many industries, including automobiles and electronics.
Five basic principles of Lean Manufacturing are included in lean manufacturing
-
Define Value - Identify the value your business adds to society and what makes you different from competitors.
-
Reduce waste - Stop any activity that isn't adding value to the supply chains.
-
Create Flow: Ensure that the work process flows without interruptions.
-
Standardize and Simplify – Make processes as consistent, repeatable, and as simple as possible.
-
Build Relationships- Develop personal relationships with both internal as well as external stakeholders.
Lean manufacturing isn’t new, but it has seen a renewed interest since 2008 due to the global financial crisis. Many businesses have adopted lean production techniques to make them more competitive. Some economists even believe that lean manufacturing can be a key factor in economic recovery.
Lean manufacturing is becoming a popular practice in automotive. It has many advantages. These include improved customer satisfaction, reduced inventory levels, lower operating costs, increased productivity, and better overall safety.
Any aspect of an enterprise can benefit from Lean manufacturing. Because it makes sure that all value chains are efficient and effectively managed, Lean Manufacturing is particularly helpful for organizations.
There are three types principally of lean manufacturing:
-
Just-in Time Manufacturing, (JIT): This kind of lean manufacturing is also commonly known as "pull-systems." JIT stands for a system where components are assembled on the spot rather than being made in advance. This strategy aims to decrease lead times, increase availability of parts and reduce inventory.
-
Zero Defects Manufacturing (ZDM),: ZDM is a system that ensures no defective units are left the manufacturing facility. If a part needs to be fixed during the assembly line, it should be repaired rather than scrapped. This applies to finished goods that may require minor repairs before shipment.
-
Continuous Improvement: Continuous Improvement aims to improve efficiency by continually identifying problems and making adjustments to eliminate or minimize waste. Continuous improvement refers to continuous improvement of processes as well people and tools.