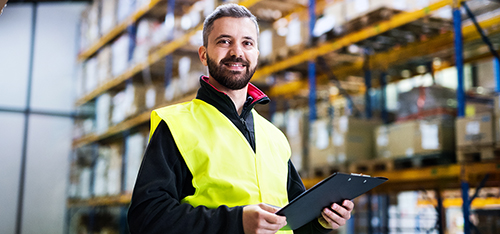
The best lean books provide invaluable guidance for industry leaders by using simple language and clear explanations. The bestselling book discusses a variety concepts, such as improving business processes, reducing expenses, and improving quality. Detailed drawings and step-by-step instructions make implementation easy. Information about lean manufacturing tools is also included in the book.
The book provides a comprehensive overview of Toyota's global success and the Toyota production system. It also discusses Toyota's management style, motivation, and problem-solving skills. It provides information on Toyota's Lean strategy success as well as explains the 14 management concepts that underpin Toyota's business strategies. The book also contains a chapter on Toyota's involvement in the automotive market, which includes a section on Toyota using lean principles within the automotive sector.
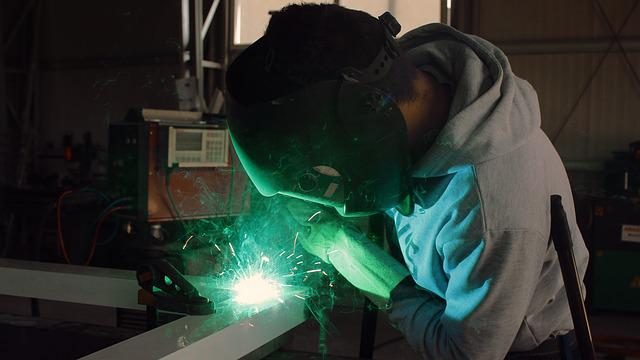
Lean manufacturing is a process of manufacturing that strives to improve the quality and efficiency of the products and services a company produces. It aims to eliminate waste, making the process more efficient and error-free. High-skilled people and machines are key to successful manufacturing processes. These interactions are responsible for the bulk of manufacturing companies' costs.
The Lean Manufacturing Tool Book, The Toyota Way, 14 Management Principles to Improving Quality, Productivity, and The Machine that Changed the World, are the best books about lean manufacturing. These books offer a thorough explanation of Toyota's manufacturing system as well as practical tips, and detailed instructions for how to apply Lean techniques to any type of manufacturing environment. The Lean Manufacturing Tool Book is a complete guide to the tools used in the Lean manufacturing process. It provides expert advice and a list of the various tools available. The book includes information on Lean manufacturing concepts including Six Sigma, and Lean problem solving.
The Toyota Way is the first book to introduce Lean manufacturing. It discusses Toyota's management principles as well as how to implement them in your organization. It includes information on the organization profiles as well as the philosophies that underpin Toyota's success. It also has a new afterword which discusses Lean's effect on the manufacturing industry, since the publication. It also includes updated frameworks for improving production and reducing costs.
The Machine that Changed the World: Why Lean Changed the World was the original book that fully explained the Toyota Production System (and its impact on the manufacturing industry). It was published in 1990. It provides an overview and context of the system. This book contains a new afterword, and a revised foreword. They provide an improved understanding of the Toyota Production System's impact on the global manufacturing sector. It also provides an explanation of the fundamental ideas behind all Lean practices.
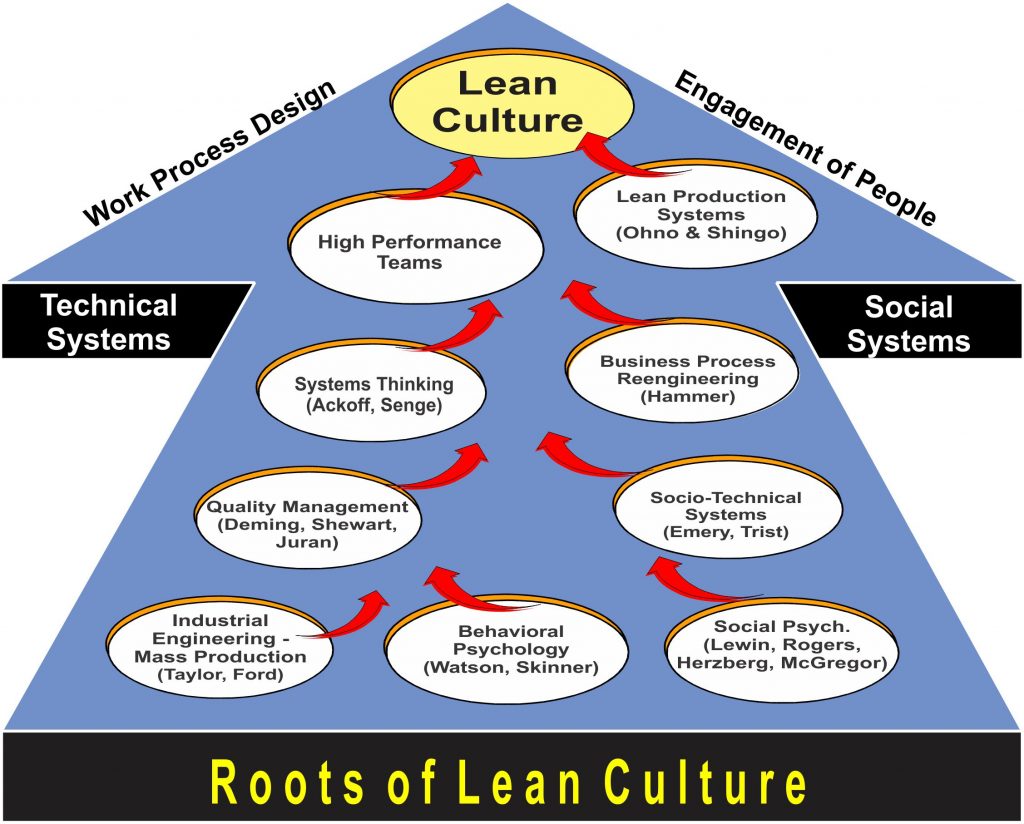
The Toyota Kata Flow-Focused Manufacturing Methodology: Another important book. It explains how Toyota works with their customers to provide quality products and services. It explains Toyota's commitment towards quality, problem-solving, speeding up business operations and ensuring customer satisfaction. It also explains Toyota's selection and hiring process and the motivation of employees to provide high quality products.
FAQ
Can we automate some parts of manufacturing?
Yes! Automation has been around since ancient times. The wheel was invented by the Egyptians thousands of years ago. To help us build assembly lines, we now have robots.
There are many applications for robotics in manufacturing today. These include:
-
Automation line robots
-
Robot welding
-
Robot painting
-
Robotics inspection
-
Robots create products
Manufacturing can also be automated in many other ways. 3D printing is a way to make custom products quickly and without waiting weeks or months for them to be manufactured.
What are the 4 types manufacturing?
Manufacturing refers the process of turning raw materials into useful products with machines and processes. It includes many different activities like designing, building and testing, packaging, shipping and selling, as well as servicing.
How can we increase manufacturing efficiency?
First, we need to identify which factors are most critical in affecting production times. Next, we must find ways to improve those factors. If you aren't sure where to begin, think about the factors that have the greatest impact on production time. Once you have identified them, it is time to identify solutions.
What are the 7 Rs of logistics management?
The 7R's of Logistics is an acronym for the seven basic principles of logistics management. It was published in 2004 by the International Association of Business Logisticians as part of their "Seven Principles of Logistics Management" series.
The following letters make up the acronym:
-
Responsive - ensure all actions are legal and not harmful to others.
-
Reliable - have confidence in the ability to deliver on commitments made.
-
Reasonable - use resources efficiently and don't waste them.
-
Realistic – consider all aspects of operations, from cost-effectiveness to environmental impact.
-
Respectful: Treat others with fairness and equity
-
Resourceful - look for opportunities to save money and increase productivity.
-
Recognizable provides value-added products and services to customers
What is the difference in Production Planning and Scheduling, you ask?
Production Planning (PP) refers to the process of determining how much production is needed at any given moment. This is accomplished by forecasting the demand and identifying production resources.
Scheduling refers to the process of allocating specific dates to tasks in order that they can be completed within a specified timeframe.
What is the responsibility of a manufacturing manager?
Manufacturing managers must ensure that manufacturing processes are efficient, effective, and cost-effective. They should also be aware of any problems within the company and act accordingly.
They should also be able communicate with other departments, such as sales or marketing.
They should be informed about industry trends and be able make use of this information to improve their productivity and efficiency.
Statistics
- In the United States, for example, manufacturing makes up 15% of the economic output. (twi-global.com)
- You can multiply the result by 100 to get the total percent of monthly overhead. (investopedia.com)
- (2:04) MTO is a production technique wherein products are customized according to customer specifications, and production only starts after an order is received. (oracle.com)
- According to a Statista study, U.S. businesses spent $1.63 trillion on logistics in 2019, moving goods from origin to end user through various supply chain network segments. (netsuite.com)
- Job #1 is delivering the ordered product according to specifications: color, size, brand, and quantity. (netsuite.com)
External Links
How To
How to Use Lean Manufacturing for the Production of Goods
Lean manufacturing is a management style that aims to increase efficiency and reduce waste through continuous improvement. It was first developed in Japan in the 1970s/80s by Taiichi Ahno, who was awarded the Toyota Production System (TPS), award from KanjiToyoda, the founder of TPS. Michael L. Watkins published the book "The Machine That Changed the World", which was the first to be published about lean manufacturing.
Lean manufacturing refers to a set of principles that improve the quality, speed and costs of products and services. It emphasizes the elimination and minimization of waste in the value stream. Lean manufacturing can be described as just-in–time (JIT), total productive maintenance, zero defect (TPM), or even 5S. Lean manufacturing focuses on eliminating non-value-added activities such as rework, inspection, and waiting.
In addition to improving product quality and reducing costs, lean manufacturing helps companies achieve their goals faster and reduces employee turnover. Lean manufacturing can be used to manage all aspects of the value chain. Customers, suppliers, distributors, retailers and employees are all included. Many industries worldwide use lean manufacturing. For example, Toyota's philosophy underpins its success in automobiles, electronics, appliances, healthcare, chemical engineering, aerospace, paper, food, etc.
Five principles are the basis of lean manufacturing:
-
Define Value- Identify the added value your company brings to society. What makes you stand out from your competitors?
-
Reduce Waste - Remove any activity which doesn't add value to your supply chain.
-
Create Flow - Ensure work moves smoothly through the process without interruption.
-
Standardize & simplify - Make processes consistent and repeatable.
-
Build Relationships - Establish personal relationships with both internal and external stakeholders.
Although lean manufacturing has always been around, it is gaining popularity in recent years because of a renewed interest for the economy after 2008's global financial crisis. Many businesses are now using lean manufacturing to improve their competitiveness. Some economists even believe that lean manufacturing can be a key factor in economic recovery.
Lean manufacturing is now becoming a common practice in the automotive industry, with many benefits. These include higher customer satisfaction levels, reduced inventory levels as well as lower operating costs.
Lean manufacturing can be applied to almost every aspect of an organization. Lean manufacturing is most useful in the production sector of an organisation because it ensures that each step in the value-chain is efficient and productive.
There are three types of lean manufacturing.
-
Just-in-Time Manufacturing: Also known as "pull systems", this type of lean manufacturing uses just-in-time manufacturing (JIT). JIT means that components are assembled at the time of use and not manufactured in advance. This strategy aims to decrease lead times, increase availability of parts and reduce inventory.
-
Zero Defects Manufacturing: ZDM ensures that no defective units leave the manufacturing plant. Repairing a part that is damaged during assembly should be done, not scrapping. This also applies to finished products that need minor repairs before being shipped.
-
Continuous Improvement: Continuous Improvement aims to improve efficiency by continually identifying problems and making adjustments to eliminate or minimize waste. Continuous improvement involves continuous improvement of processes and people as well as tools.