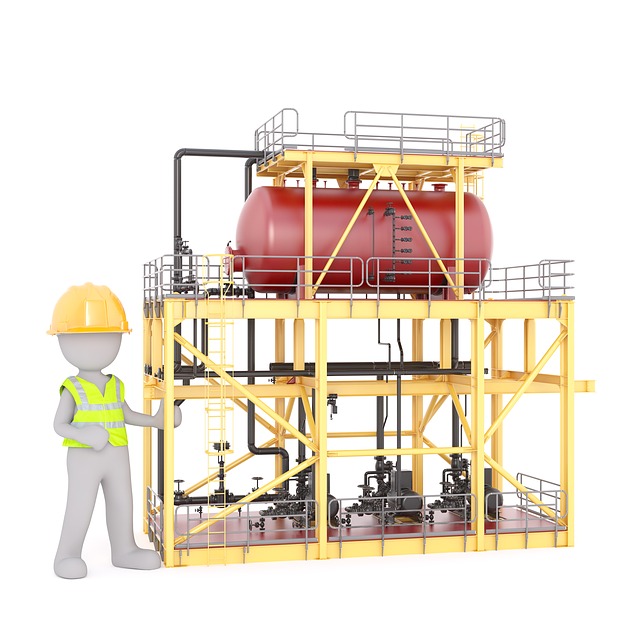
An industrial engineer is a person who uses their knowledge to improve products, processes and engineering. Industrial engineers use shaker tables for product testing under various temperatures, humidity and vibrations. Failure data is collected to improve manufacturing processes. Simple changes such as mold-resistant coatings can make a big difference in the quality and durability of a product. Even the smallest changes such as locking up a place can greatly improve a product’s lifespan.
Job description
If you are considering a career as an industrial engineer, you should write your job description carefully. An effective job description will help attract the best people to your position as an industrial engineer. The most successful engineers combine technical expertise with human intelligence. Monster's engineering job listings can give you some ideas on how to write a job description. Begin with a persuasive introduction that highlights the company's benefits. Your employer must be attractive, regardless of whether you're interested in joining a global brand, an innovative startup, or an open-minded young company that fosters creativity and innovation.
Aside from excellent technical skills, industrial engineers must also have exceptional communication skills. An industrial engineer must understand how to effectively work with different people and departments in order to be successful in industrial processes. He or she must also know how to persuade employees and management that his or her proposed approaches will improve efficiency. A successful relationship management approach leads to greater productivity. It isn't just technical skills that are essential in the job of an industrial engineer.
Education requirements
A degree in industrial engineering is required for a job that requires a lot of math and analysis skills. Industrial engineers are also required to possess excellent communication skills as they are expected to communicate their findings to others. In addition to this, they must be able to design processes and designs that reduce labor and costs. Education in this field will also enable you to succeed in this field. Here are some of the essential educational requirements for this position.
Industrial engineers require excellent communication skills and interpersonal skills in addition to a college education. They work closely with other professionals and act as the link between business and technical aspects of an organization. For industrial engineers to be able to effectively communicate with managers and employees, they must also have excellent communication and analytical skills. This profession requires excellent leadership and problem-solving skills. A high level of technical and mechanical competence is required for industrial engineers.
Options for a career
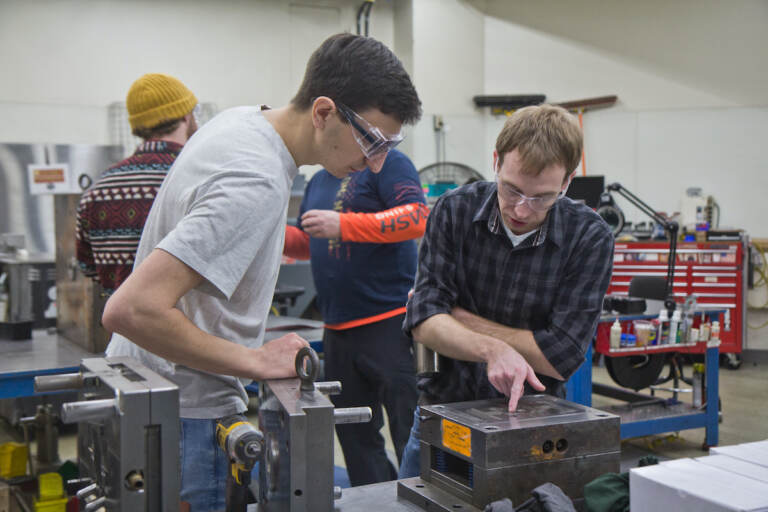
There are many career opportunities for industrial engineers. Many industrial engineers begin their careers in manufacturing. But there are also other options, such as hospitals or government agencies. Other industries that might be available to industrial engineers are the food trade, retail trade and professional trade association, as well as computer service centers. There are many jobs available for industrial engineers. Here are some of the best. Find out if this is the right profession for you.
A industrial engineer is able to focus on getting the job done efficiently and effectively. They must balance many factors, including time, workers required, technology available, and the actions that workers need to take. They also need to keep in mind environmental concerns and worker safety. Many industrial engineers also engage in quality assurance activities and supply chain management. This is a vital field because companies are always looking to cut costs and increase productivity. They can also help with product development and work flow optimization.
Salary
In 2004, the median industrial engineer salary was $87.513 USD. This number is expected increase to $114.146 by 2020. The industry one works in will have a significant impact on how much you earn. Salaries in thriving industries are likely to receive larger raises. Industrial Engineers get bonuses that are frequently changing and often moderate. The majority of bonus recipients are part of the revenue generation process. You must hold a degree or equivalent in industrial engineering to be eligible for the highest pay.
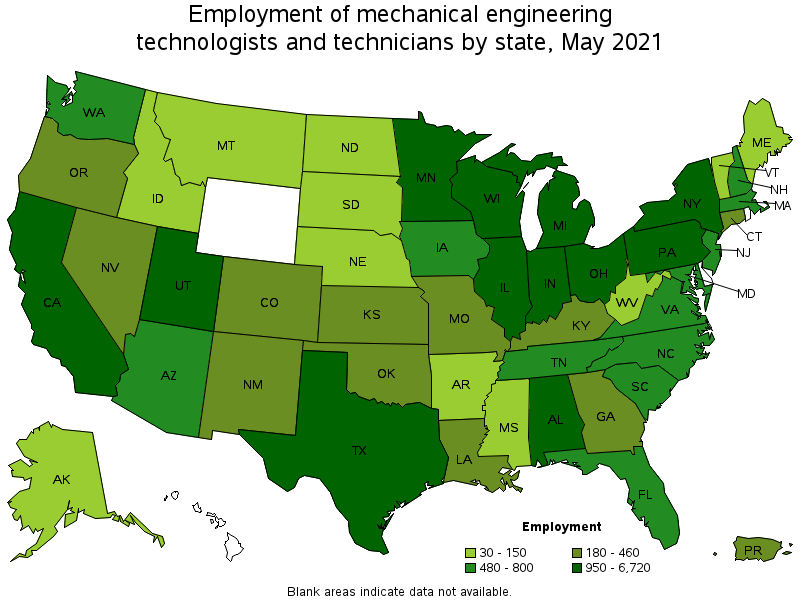
A bachelor's degree is required to be an industrial engineer. Some employers, however, prefer PhDs. A typical industrial engineer salary in the U.S. ranges between $56,000 and $121,000. But this can vary greatly. While an industrial engineer can work in an office setting, many jobs require overtime and protective attire. And as a result, a high degree of flexibility is necessary.
FAQ
What is the responsibility of a logistics manager?
Logistics managers ensure that goods arrive on time and are unharmed. This is done through his/her expertise and knowledge about the company's product range. He/she should also ensure enough stock is available to meet demand.
What is the role of a manager in manufacturing?
Manufacturing managers must ensure that manufacturing processes are efficient, effective, and cost-effective. They should also be aware of any problems within the company and act accordingly.
They should also be able communicate with other departments, such as sales or marketing.
They should also be knowledgeable about the latest trends in the industry so they can use this information for productivity and efficiency improvements.
What are the products of logistics?
Logistics involves the transportation of goods from point A and point B.
These include all aspects related to transport such as packaging, loading and transporting, storing, transporting, unloading and warehousing inventory management, customer service. Distribution, returns, recycling are some of the options.
Logisticians ensure that products reach the right destination at the right moment and under safe conditions. Logisticians assist companies in managing their supply chains by providing information such as demand forecasts, stock levels and production schedules.
They monitor shipments in transit, ensure quality standards, manage inventories, replenish orders, coordinate with suppliers and other vendors, and offer support services for sales, marketing, and customer service.
Why is logistics important in manufacturing
Logistics are essential to any business. They are essential to any business's success.
Logistics play a key role in reducing expenses and increasing efficiency.
How can excess manufacturing production be reduced?
Better inventory management is key to reducing excess production. This would reduce the time spent on unproductive activities like purchasing, storing and maintaining excess stock. This could help us free up our time for other productive tasks.
Kanban systems are one way to achieve this. A Kanban Board is a visual display that tracks work progress. In a Kanban system, work items move through a sequence of states until they reach their final destination. Each state represents a different priority.
For instance, when work moves from one stage to another, the current task is complete enough to be moved to the next stage. But if a task remains in the beginning stages it will stay that way until it reaches its end.
This allows you to keep work moving along while making sure that no work gets neglected. A Kanban board allows managers to monitor how much work is being completed at any given moment. This information allows them to adjust their workflow based on real-time data.
Lean manufacturing can also be used to reduce inventory levels. Lean manufacturing focuses on eliminating waste throughout the entire production chain. Anything that does not contribute to the product's value is considered waste. There are several types of waste that you might encounter:
-
Overproduction
-
Inventory
-
Unnecessary packaging
-
Materials in excess
These ideas will help manufacturers increase efficiency and lower costs.
What do we need to know about Manufacturing Processes in order to learn more about Logistics?
No. It doesn't matter if you don't know anything about manufacturing before you learn about logistics. Understanding the manufacturing process will allow you to better understand logistics.
Statistics
- In 2021, an estimated 12.1 million Americans work in the manufacturing sector.6 (investopedia.com)
- [54][55] These are the top 50 countries by the total value of manufacturing output in US dollars for its noted year according to World Bank.[56] (en.wikipedia.org)
- According to the United Nations Industrial Development Organization (UNIDO), China is the top manufacturer worldwide by 2019 output, producing 28.7% of the total global manufacturing output, followed by the United States, Japan, Germany, and India.[52][53] (en.wikipedia.org)
- According to a Statista study, U.S. businesses spent $1.63 trillion on logistics in 2019, moving goods from origin to end user through various supply chain network segments. (netsuite.com)
- In the United States, for example, manufacturing makes up 15% of the economic output. (twi-global.com)
External Links
How To
Six Sigma: How to Use it in Manufacturing
Six Sigma is defined by "the application SPC (statistical process control) techniques to achieve continuous improvements." Motorola's Quality Improvement Department, Tokyo, Japan, developed it in 1986. Six Sigma is a method to improve quality through standardization and elimination of defects. Many companies have adopted Six Sigma in recent years because they believe that there are no perfect products and services. The main goal of Six Sigma is to reduce variation from the mean value of production. This means that if you take a sample of your product, then measure its performance against the average, you can find out what percentage of the time the process deviates from the norm. If this deviation is too big, you know something needs fixing.
Understanding how your business' variability is a key step towards Six Sigma implementation is the first. Once you have a good understanding of the basics, you can identify potential sources of variation. You'll also want to determine whether these variations are random or systematic. Random variations are caused when people make mistakes. While systematic variations are caused outside of the process, they can occur. If you make widgets and some of them end up on the assembly line, then those are considered random variations. But if you notice that every widget you make falls apart at the exact same place each time, this would indicate that there is a problem.
Once you've identified where the problems lie, you'll want to design solutions to eliminate those problems. That solution might involve changing the way you do things or redesigning the process altogether. Test them again once you've implemented the changes. If they fail, you can go back to the drawing board to come up with a different plan.