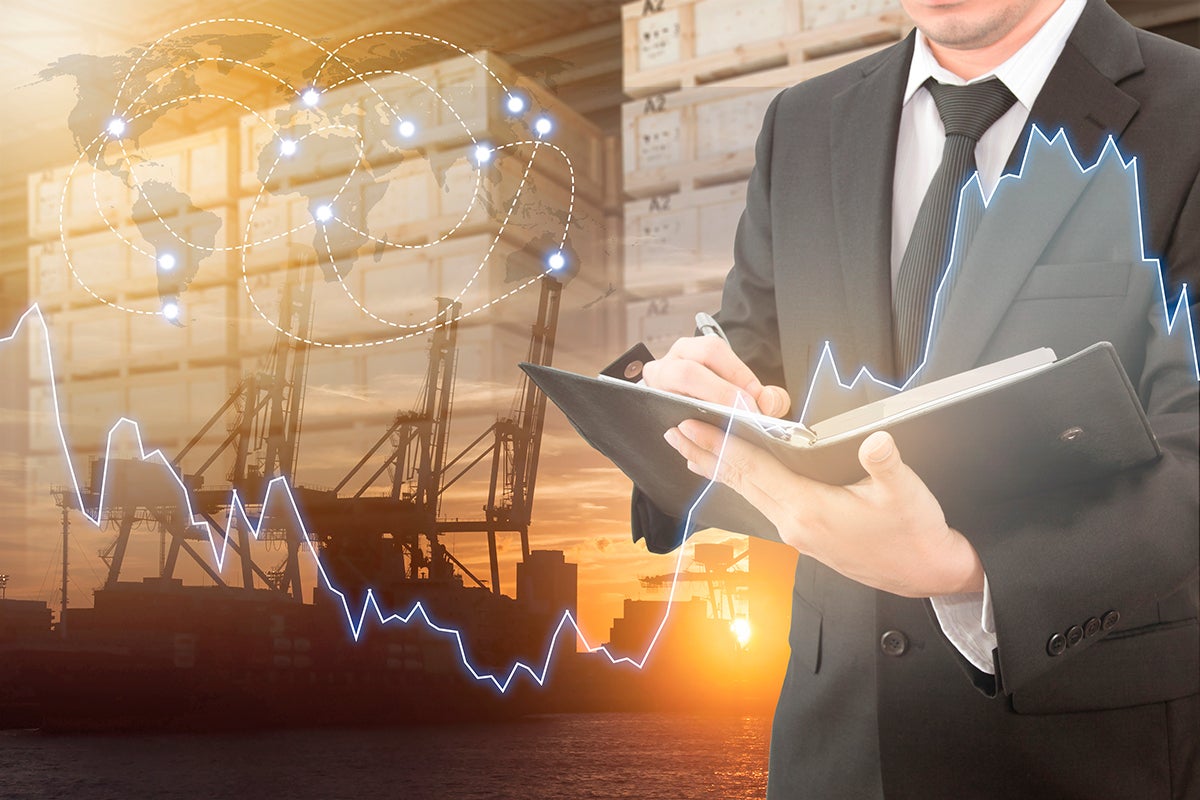
Consider lean manufacturing if you are looking to reduce costs, speed up lead times, minimize setup time, and maximize turnaround time. Lean manufacturing offers many benefits. It reduces costs and leads time, while improving customer satisfaction. These improvements make lean manufacturing a great option to increase your business's profitability. If you're still not convinced, read on for three reasons why it's the best way to make products and cut costs:
Reduces costs
Lean manufacturing can bring significant savings. By reducing defects and rework, manufacturers can reduce their direct labor cost. This makes labor costs less motivating in decision-making. A second benefit is the elimination or hazardous waste. Direct labor costs are below 15% in many industries. It is difficult to justify outsourcing manufacturing to low cost locations. This can lower overall manufacturing costs and improve customer services.
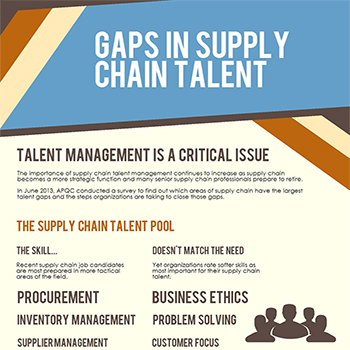
Improves lead times
Lean manufacturing offers many benefits. It can reduce waste and speed up lead times. It is a philosophy that promotes continuous improvement, or "kaizen". It combines the talents of employees and encourages collaboration and accountability. The process can decrease lead times by as high as 20% Lean manufacturing is about making small adjustments frequently to improve product quality.
Shortens set-up times
A significant way to reduce the amount of time required to produce a product is by reducing set-up times. Setup time refers to the amount of time required to switch from the last item on a previous order to the first good item on the next. The setup time includes preparation, replacement, as well as location activities. These activities may be external or internal. External setup activities can be done while the process is still operating.
Reduces time to market
Lean manufacturing, also known as continuous improvement, was first developed in Japan in the period of rebuilding after World War II. It was intended to improve market competitiveness and shorten lead times. Companies can reduce the time required for products to reach the marketplace and meet customer demand. This will increase their profitability. This method of production can not only increase efficiency in the manufacturing process but also make the entire facility more effective.
Improves product quality
Lean manufacturing's success depends on the ability to reduce waste, improve product quality, and minimize costs. It has been used by many companies, large and small. It lowers lead times and costs as well labor. You can learn more about the benefits of lean manufacturing for your business by reading this article. Here are some key areas to concentrate on. Embracing lean principles can reduce lead times by 90%, improve product quality, and reduce your costs.
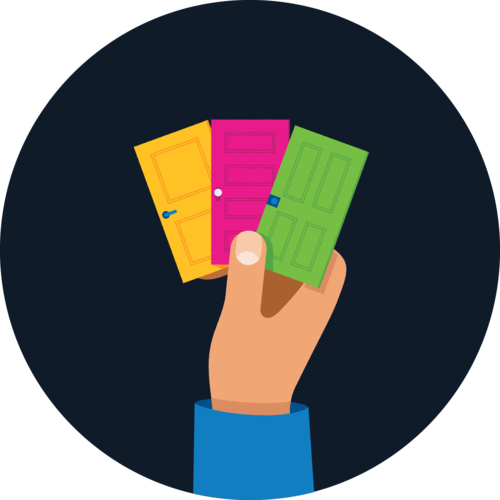
Direct labor costs can be reduced
Low indirect labor costs are the low hanging fruit of lean manufacturing. True lean companies pay scant attention to direct labor efficiency and instead look for ways to cut indirect labor costs. This means eliminating maintenance, inspection, management, and material handling jobs, as well as pushing decisions to the production floor. Toyota and other lean manufacturers use this same approach. This article will examine how lean manufacturing helps lower indirect labor costs.
FAQ
What are the 4 types manufacturing?
Manufacturing is the process that transforms raw materials into useful products. Manufacturing can include many activities such as designing and building, testing, packaging shipping, selling, servicing, and other related activities.
What skills are required to be a production manager?
You must be flexible and organized to become a productive production planner. It is also important to be able communicate with colleagues and clients.
How can manufacturing avoid production bottlenecks
The key to avoiding bottlenecks in production is to keep all processes running smoothly throughout the entire production cycle, from the time you receive an order until the time when the product ships.
This includes both quality control and capacity planning.
Continuous improvement techniques like Six Sigma are the best way to achieve this.
Six Sigma Management System is a method to increase quality and reduce waste throughout your organization.
It seeks to eliminate variation and create consistency in your work.
Statistics
- Many factories witnessed a 30% increase in output due to the shift to electric motors. (en.wikipedia.org)
- [54][55] These are the top 50 countries by the total value of manufacturing output in US dollars for its noted year according to World Bank.[56] (en.wikipedia.org)
- In 2021, an estimated 12.1 million Americans work in the manufacturing sector.6 (investopedia.com)
- According to a Statista study, U.S. businesses spent $1.63 trillion on logistics in 2019, moving goods from origin to end user through various supply chain network segments. (netsuite.com)
- According to the United Nations Industrial Development Organization (UNIDO), China is the top manufacturer worldwide by 2019 output, producing 28.7% of the total global manufacturing output, followed by the United States, Japan, Germany, and India.[52][53] (en.wikipedia.org)
External Links
How To
How to Use the Just-In-Time Method in Production
Just-in time (JIT), is a process that reduces costs and increases efficiency in business operations. It's the process of obtaining the right amount and timing of resources when you need them. This means you only pay what you use. Frederick Taylor was the first to coin this term. He developed it while working as a foreman during the early 1900s. He observed how workers were paid overtime if there were delays in their work. He realized that workers should have enough time to complete their jobs before they begin work. This would help increase productivity.
JIT is a way to plan ahead and make sure you don't waste any money. The entire project should be looked at from start to finish. You need to ensure you have enough resources to tackle any issues that might arise. You can anticipate problems and have enough equipment and people available to fix them. This will ensure that you don't spend more money on things that aren't necessary.
There are many types of JIT methods.
-
Demand-driven JIT: This is a JIT that allows you to regularly order the parts/materials necessary for your project. This will enable you to keep track of how much material is left after you use it. It will also allow you to predict how long it takes to produce more.
-
Inventory-based: This is a type where you stock the materials required for your projects in advance. This allows for you to anticipate how much you can sell.
-
Project-driven : This is a method where you make sure that enough money is set aside to pay the project's cost. You will be able to purchase the right amount of materials if you know what you need.
-
Resource-based JIT: This is the most popular form of JIT. You assign certain resources based off demand. For instance, if you have a lot of orders coming in, you'll assign more people to handle them. If there aren't many orders, you will assign fewer people.
-
Cost-based: This is a similar approach to resource-based but you are not only concerned with how many people you have, but also how much each one costs.
-
Price-based pricing: This is similar in concept to cost-based but instead you look at how much each worker costs, it looks at the overall company's price.
-
Material-based is an alternative to cost-based. Instead of looking at the total cost in the company, this method focuses on the average amount of raw materials that you consume.
-
Time-based JIT: This is another variant of resource-based JIT. Instead of focusing on the cost of each employee, you will focus on the time it takes to complete a project.
-
Quality-based: This is yet another variation of resource-based JIT. Instead of thinking about the cost of each employee or the time it takes to produce something, you focus on how good your product quality.
-
Value-based: This is one of the newest forms of JIT. In this case, you're not concerned with how well the products perform or whether they meet customer expectations. Instead, you are focused on adding value to the marketplace.
-
Stock-based: This stock-based method focuses on the actual quantity of products being made at any given time. It is used when production goals are met while inventory is kept to a minimum.
-
Just-in-time planning (JIT): This is a combination JIT and supply-chain management. It's the process of scheduling delivery of components immediately after they are ordered. It reduces lead times and improves throughput.