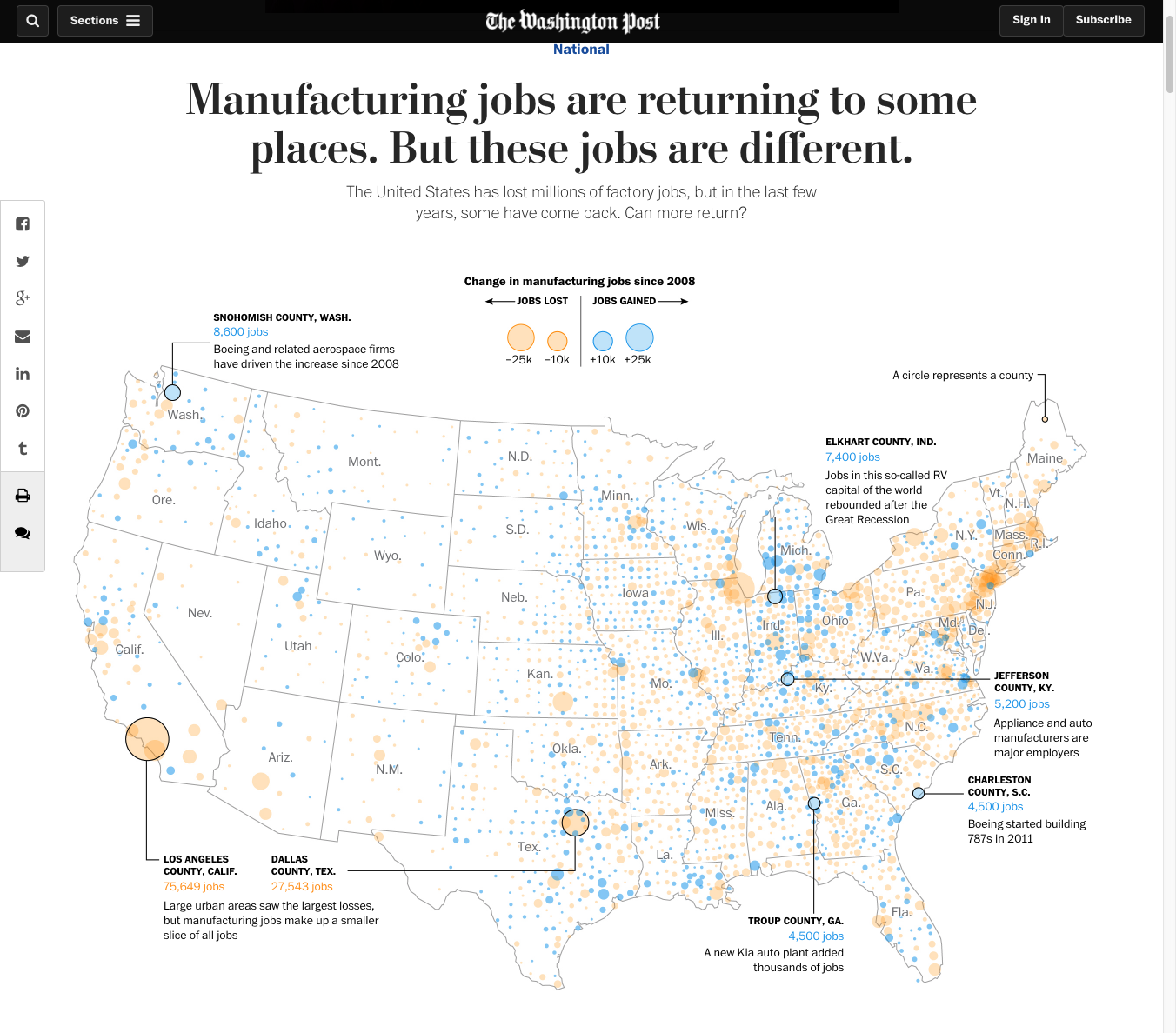
Salary for a validation engineer refers to the compensation an individual receives in exchange for their role as a validator. The amount they receive is usually based on experience, education, and skills. This amount is also influenced by what type of job the employee holds and which company they work for.
What Is a Validation Engineer?
A Validation Engineer is an engineering professional who uses equipment, processes and procedures to monitor the quality of products. They work in manufacturing and testing environments, as well as research and development.
What does a Validation Engineer do?
Validation engineers are responsible for monitoring the performance and efficiency of the systems and equipment used in pharmaceutical production. They do this by analyzing, inspecting, testing and calibrating equipment and machinery. They also investigate any malfunctions or anomalies in equipment which could lead to product failure.

What Does a Validation engineer Salary Look Like?
A Validation Engineer salary is usually high, but it depends upon the type of company that you work for. Apple and Google often pay the highest salaries. These engineers can expect an average annual salary of $89130 in the pharmaceutical sector.
What Are the most common skills that are required in this career?
A validation engineer must be able to write, implement and coordinate qualification and commissioning protocols. A validation engineer should have solid technical knowledge in manufacturing, process, and software engineering.
How to Become an Engineer Validation
The path to becoming a validation engineering role is a combination of a bachelor's degree and an apprenticeship. Most employers require that candidates have a bachelor’s degree in an engineering discipline such as electrical, software, mechanical, or any other relevant field.
Then, you can gain experience through an internship or placement in a graduate program for engineers. You can also look for work in newspapers, recruitment agencies, careers services or online.

How to become a Pharmaceutical Validation Engineer
A career as a validation engineer requires the right combination of academic qualifications and practical experience. You must have a relevant engineering or science degree, and you should also be familiar with the pharmaceutical industry. This can be a challenging path, but it is worth persevering to develop your skills and find a job that suits your qualifications and ambitions.
How to Become A Pharma Validation Engineer
For validation engineers, there is a clearly defined career path with positions available in varying levels. Senior engineers can be given management responsibilities, and have the chance to travel abroad. You can also move into roles that allow you to become an expert in a specific field, such as CSV or drug delivery technologies.
Salary of a pharmaceutical validity engineer can be affected by the industry that the person works in, and the types of products with which they are involved. While the average salary of a pharmaceutical validation engineers is $98,150 on a national level, certain cities offer higher salaries. Hayward CA, for instance, has a salary that is higher than the average at $18,034; San Jose CA, on the other hand, comes out tops with a salary of $21,856.
FAQ
What are the 7 Rs of logistics.
The acronym 7Rs of Logistics refers to the seven core principles of logistics management. It was developed by International Association of Business Logisticians (IABL), and published as part of their "Seven Principles of Logistics Management Series" in 2004.
The following letters make up the acronym:
-
Responsible - ensure that all actions taken are within legal requirements and are not harmful to others.
-
Reliable: Have faith in your ability or the ability to honor any promises made.
-
Reasonable - use resources efficiently and don't waste them.
-
Realistic - Take into consideration all aspects of operations including cost-effectiveness, environmental impact, and other factors.
-
Respectful - show respect and treat others fairly and fairly
-
Reliable - Find ways to save money and increase your productivity.
-
Recognizable - Provide value-added services to customers
What is the role of a manager in manufacturing?
A manufacturing manager must ensure that all manufacturing processes are efficient and effective. They should also be aware and responsive to any company problems.
They should also learn how to communicate effectively with other departments, including sales and marketing.
They should also be aware of the latest trends in their industry and be able to use this information to help improve productivity and efficiency.
What is production planning?
Production Planning includes planning for all aspects related to production. It is important to have everything ready and planned before you start shooting. You should also have information to ensure the best possible results on set. This includes information on shooting times, locations, cast lists and crew details.
The first step is to outline what you want to film. You may have decided where to shoot or even specific locations you want to use. Once you have identified your locations and scenes it's time to begin figuring out what elements you will need for each one. If you decide you need a car and don't know what model to choose, this could be an example. To narrow your options, you can search online for available models.
Once you have found the right car, you can start thinking about extras. What about additional seating? You might also need someone to help you get around the back. Maybe you'd like to change the interior from black to a white color. These questions can help you decide the right look for your car. It is also worth considering the types of shots that you wish to take. Will you be filming close-ups or wide angles? Maybe you want the engine or the steering wheels to be shown. All of these things will help you identify the exact style of car you want to film.
Once you've determined the above, it is time to start creating a calendar. You can use a schedule to determine when and where you need it to be shot. The schedule will show you when to get there, what time to leave, and when to return home. This way, everyone knows what they need to do and when. You can also make sure to book extra staff in advance if you have to hire them. You should not hire anyone who doesn't show up because of your inaction.
It is important to calculate the amount of filming days when you are creating your schedule. Some projects can be completed in a matter of days or weeks. Others may take several days. It is important to consider whether you require more than one photo per day when you create your schedule. Multiple shots at the same location can increase costs and make it more difficult to complete. You can't be certain if you will need multiple takes so it is better not to shoot too many.
Budget setting is another important aspect in production planning. As it will allow you and your team to work within your financial means, setting a realistic budget is crucial. If you have to reduce your budget due to unexpected circumstances, you can always lower it later. But, don't underestimate how much money you'll spend. Underestimating the cost will result in less money after you have paid for other items.
Production planning is a complicated process. But once you understand how everything works together, it becomes much easier to plan future project.
Is automation important in manufacturing?
Automation is important not only for manufacturers but also for service providers. Automation allows them to deliver services quicker and more efficiently. It helps them to lower costs by reducing human errors, and improving productivity.
How does a production planner differ from a project manager?
The primary difference between a producer planner and a manager of a project is that the manager usually plans and organizes the whole project, while a production planner is only involved in the planning stage.
Why is logistics important in manufacturing
Logistics are an essential part of any business. They enable you to achieve outstanding results by helping manage product flow from raw materials through to finished goods.
Logistics plays a significant role in reducing cost and increasing efficiency.
What does manufacturing mean?
Manufacturing Industries are those businesses that make products for sale. These products are sold to consumers. These companies employ many processes to achieve this purpose, such as production and distribution, retailing, management and so on. They produce goods from raw materials by using machines and other machinery. This includes all types manufactured goods such as clothing, building materials, furniture, electronics, tools and machinery.
Statistics
- You can multiply the result by 100 to get the total percent of monthly overhead. (investopedia.com)
- According to the United Nations Industrial Development Organization (UNIDO), China is the top manufacturer worldwide by 2019 output, producing 28.7% of the total global manufacturing output, followed by the United States, Japan, Germany, and India.[52][53] (en.wikipedia.org)
- In 2021, an estimated 12.1 million Americans work in the manufacturing sector.6 (investopedia.com)
- In the United States, for example, manufacturing makes up 15% of the economic output. (twi-global.com)
- Many factories witnessed a 30% increase in output due to the shift to electric motors. (en.wikipedia.org)
External Links
How To
Six Sigma and Manufacturing
Six Sigma is defined by "the application SPC (statistical process control) techniques to achieve continuous improvements." Motorola's Quality Improvement Department created Six Sigma at their Tokyo plant, Japan in 1986. Six Sigma's main goal is to improve process quality by standardizing processes and eliminating defects. In recent years, many companies have adopted this method because they believe there is no such thing as perfect products or services. Six Sigma's primary goal is to reduce variation from the average value of production. This means that if you take a sample of your product, then measure its performance against the average, you can find out what percentage of the time the process deviates from the norm. If this deviation is too big, you know something needs fixing.
Understanding the dynamics of variability within your business is the first step in Six Sigma. Once you understand this, you can then identify the causes of variation. These variations can also be classified as random or systematic. Random variations are caused by human errors. Systematic variations can be caused by outside factors. If you make widgets and some of them end up on the assembly line, then those are considered random variations. If however, you notice that each time you assemble a widget it falls apart in exactly the same spot, that is a problem.
Once you've identified where the problems lie, you'll want to design solutions to eliminate those problems. This could mean changing your approach or redesigning the entire process. To verify that the changes have worked, you need to test them again. If they didn't work, then you'll need to go back to the drawing board and come up with another plan.