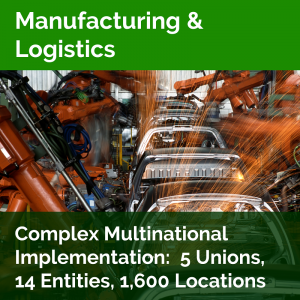
Until recently "Made in Japan", meant low quality consumer goods. But now, Japanese products have gained a reputation for durability, precision, and reliability. Japanese manufacturers are also setting higher standards. This has caused increased cost pressure and increased competition. Japanese companies are also being asked how fast they can adapt to changing market conditions.
Japanese factories are characterized by a high degree of process control. They manage the work content, labor, as well as working relationships. They can do this by training employees to produce high quality products. They also encourage feedback from customers, quality inspectors, vendors, and other stakeholders.
Japan's manufacturing culture is rooted in its cultural commitment to discipline. Modern technology has also had an influence on it. Many Japanese companies use artificial intelligence to augment non-manufacturing workers. The next generation of technology promises further enhancements to non-manufacturing labor. This includes robots that will work in factories, nursing homes, hospitals, temples, and even schools.
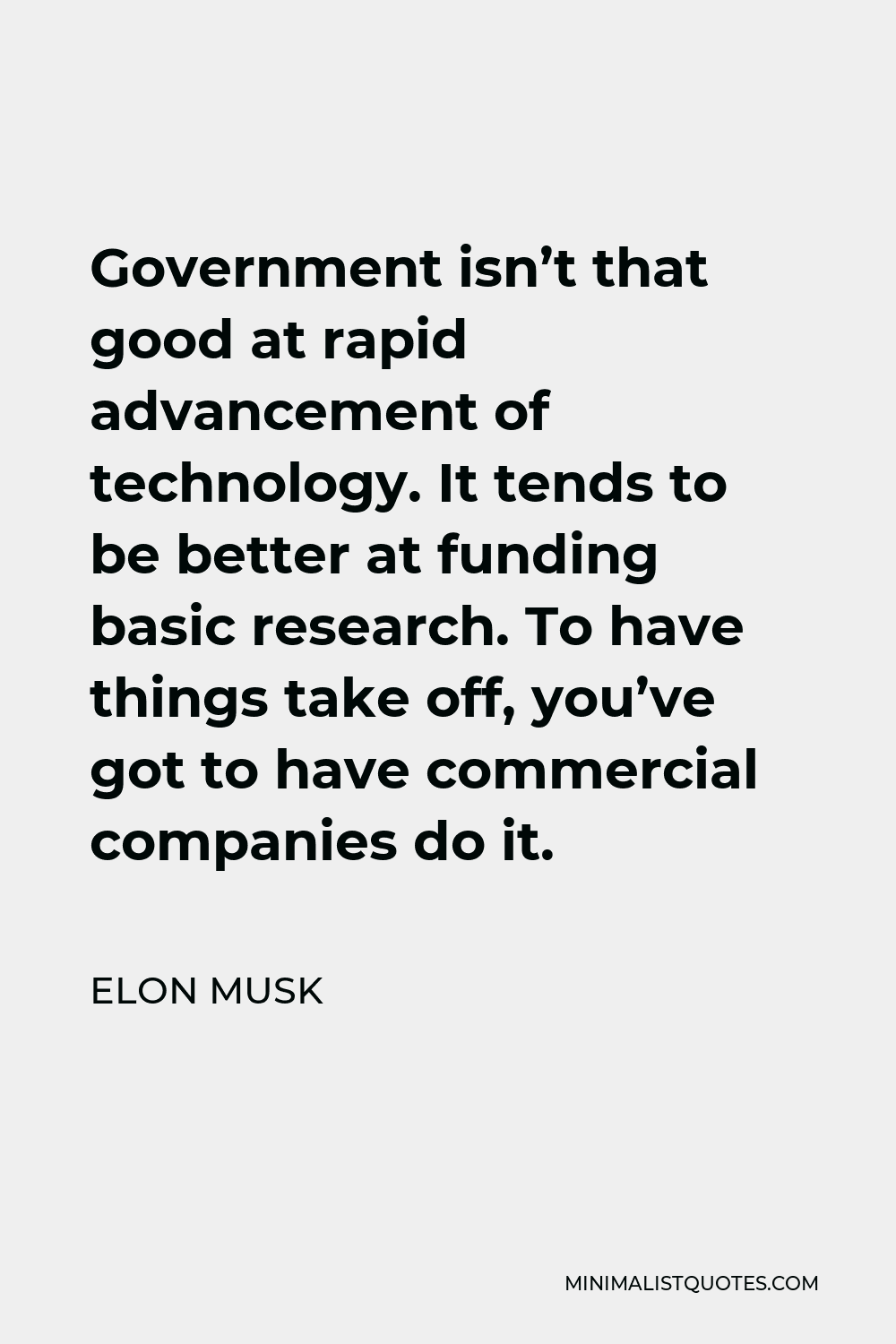
There have been many safety scandals. One case involved a girl aged 13 who died in her factory after contracting a severe illness. Another involved a company that admitted to improper vehicle inspection procedures. These scandals have brought the Japanese factory floor under close scrutiny. Numerous strikes by workers have also altered the work environment. To address these problems, government officials have enacted new regulations like closed loop management. This allows workers to be isolated to prevent the spread of viruses.
A second important factor that is affecting Japan's industrial sector is the aging population. Japanese birth rates are declining which means that there is a shortage labor. This demand is not being met by enough labor in Japan. Japanese manufacturing is dependent on foreign workers. Many factories have difficulty sourcing supplies. This is causing problems in their supply chain.
Japanese manufacturers have a reputation for working closely with suppliers to resolve problems. Japanese companies may even organize seminars for their suppliers in order to help them meet customer expectations. To make sure they meet specifications, they screen all incoming parts. They use advanced technology like automatic checkers to spot defects before they occur.
Their products show the best of Japanese production. Japanese automobiles are well-known for their fuel efficiency, durability, quality, and reliability. The Japanese automobile industry is also a major one in the world. Japan is home to six of the top 10 automakers, including Toyota and Honda. They also produce cars with more features for a less expensive price.
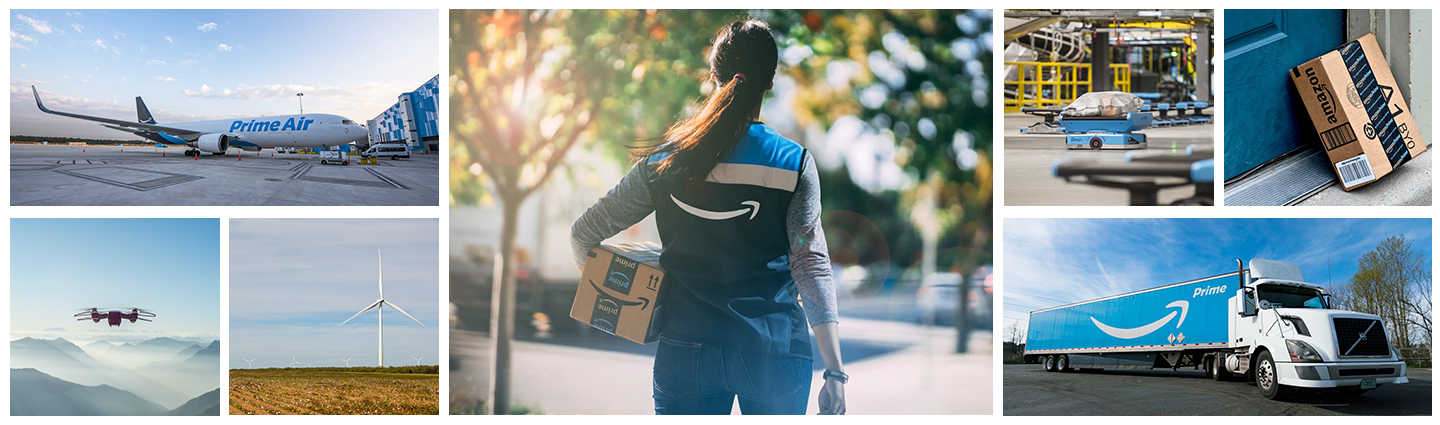
The next wave of technology will also have a big impact on the industry, especially in terms of wages. Robots are already replacing human workers in field service organizations. These workers report directly into sales and manufacturing managers. Automation will not be limited to Japanese factories. Robots will even work in hospitals and train stations.
Japan faces many problems with its supply chains. This has affected exports, slowing them down and creating congestion in the port. Another problem is the increase in non-regular labor, which has led to lower standards and reduced costs.
FAQ
What is the difference in Production Planning and Scheduling, you ask?
Production Planning (PP), is the process of deciding what production needs to take place at any given time. Forecasting demand is one way to do this.
Scheduling involves the assignment of dates and times to tasks in order to complete them within the timeframe.
Do we need to know about Manufacturing Processes before learning about Logistics?
No. No. However, knowing about manufacturing processes will definitely give you a better understanding of how logistics works.
What are the 7 Rs of logistics.
The acronym 7R's for Logistics stands to represent the seven basic principles in logistics management. It was developed and published by the International Association of Business Logisticians in 2004 as part of the "Seven Principles of Logistics Management".
The following letters make up the acronym:
-
Responsive - ensure all actions are legal and not harmful to others.
-
Reliable – have faith in your ability and capability to keep promises.
-
Reasonable - make sure you use your resources well and don't waste them.
-
Realistic – Consider all aspects, including cost-effectiveness as well as environmental impact.
-
Respectful: Treat others with fairness and equity
-
You are resourceful and look for ways to save money while increasing productivity.
-
Recognizable: Provide customers with value-added service
How can manufacturing avoid production bottlenecks
The key to avoiding bottlenecks in production is to keep all processes running smoothly throughout the entire production cycle, from the time you receive an order until the time when the product ships.
This includes both planning for capacity and quality control.
Continuous improvement techniques such Six Sigma are the best method to accomplish this.
Six Sigma is a management method that helps to improve quality and reduce waste.
It's all about eliminating variation and creating consistency in work.
Why automate your warehouse?
Modern warehousing has seen automation take center stage. With the rise of ecommerce, there is a greater demand for faster delivery times as well as more efficient processes.
Warehouses must adapt quickly to meet changing customer needs. Technology is essential for warehouses to be able to adapt quickly to changing needs. Automating warehouses is a great way to save money. Here are some reasons why it's worth investing in automation:
-
Increases throughput/productivity
-
Reduces errors
-
Increases accuracy
-
Safety Boosts
-
Eliminates bottlenecks
-
Allows companies to scale more easily
-
Increases efficiency of workers
-
This gives you visibility into what happens in the warehouse
-
Enhances customer experience
-
Improves employee satisfaction
-
It reduces downtime, and increases uptime
-
This ensures that quality products are delivered promptly
-
Removes human error
-
This helps to ensure compliance with regulations
What are the requirements to start a logistics business?
To run a successful logistics company, you need a lot knowledge and skills. You must have good communication skills to interact effectively with your clients and suppliers. You need to understand how to analyze data and draw conclusions from it. You must be able and able to handle stress situations and work under pressure. You must be creative and innovative to develop new ideas to improve efficiency. To motivate and guide your team towards reaching organizational goals, you must have strong leadership skills.
It is also important to be efficient and well organized in order meet deadlines.
Statistics
- In 2021, an estimated 12.1 million Americans work in the manufacturing sector.6 (investopedia.com)
- (2:04) MTO is a production technique wherein products are customized according to customer specifications, and production only starts after an order is received. (oracle.com)
- [54][55] These are the top 50 countries by the total value of manufacturing output in US dollars for its noted year according to World Bank.[56] (en.wikipedia.org)
- It's estimated that 10.8% of the U.S. GDP in 2020 was contributed to manufacturing. (investopedia.com)
- Many factories witnessed a 30% increase in output due to the shift to electric motors. (en.wikipedia.org)
External Links
How To
How to Use Lean Manufacturing for the Production of Goods
Lean manufacturing is a management system that aims at increasing efficiency and reducing waste. It was developed in Japan during the 1970s and 1980s by Taiichi Ohno, who received the Toyota Production System (TPS) award from TPS founder Kanji Toyoda. Michael L. Watkins published the book "The Machine That Changed the World", which was the first to be published about lean manufacturing.
Lean manufacturing is often described as a set if principles that help improve the quality and speed of products and services. It emphasizes the elimination of defects and waste throughout the value stream. The five-steps of Lean Manufacturing are just-in time (JIT), zero defect and total productive maintenance (TPM), as well as 5S. Lean manufacturing eliminates non-value-added tasks like inspection, rework, waiting.
Lean manufacturing can help companies improve their product quality and reduce costs. Additionally, it helps them achieve their goals more quickly and reduces employee turnover. Lean manufacturing is a great way to manage the entire value chain including customers, suppliers, distributors and retailers as well as employees. Many industries worldwide use lean manufacturing. Toyota's philosophy is a great example of this. It has helped to create success in automobiles as well electronics, appliances and healthcare.
Lean manufacturing is based on five principles:
-
Define value - Find out what your business contributes to society, and what makes it different from other competitors.
-
Reduce Waste - Eliminate any activity that doesn't add value along the supply chain.
-
Create Flow – Ensure that work flows smoothly throughout the process.
-
Standardize and simplify – Make processes as repeatable and consistent as possible.
-
Build Relationships - Establish personal relationships with both internal and external stakeholders.
Although lean manufacturing isn't a new concept in business, it has gained popularity due to renewed interest in the economy after the 2008 global financial crisis. Many companies have adopted lean manufacturing methods to increase their marketability. According to some economists, lean manufacturing could be a significant factor in the economic recovery.
With many benefits, lean manufacturing is becoming more common in the automotive industry. These include higher customer satisfaction, lower inventory levels, lower operating expenses, greater productivity, and improved overall safety.
You can apply Lean Manufacturing to virtually any aspect of your organization. It is especially useful for the production aspect of an organization, as it ensures that every step in the value chain is efficient and effective.
There are three main types:
-
Just-in Time Manufacturing: This lean manufacturing method is commonly called "pull systems." JIT means that components are assembled at the time of use and not manufactured in advance. This method reduces lead times, increases availability, and decreases inventory.
-
Zero Defects Manufacturing (ZDM),: ZDM is a system that ensures no defective units are left the manufacturing facility. If a part needs to be fixed during the assembly line, it should be repaired rather than scrapped. This is also true for finished products that require minor repairs before shipping.
-
Continuous Improvement (CI: Continuous improvement aims to increase the efficiency of operations by constantly identifying and making improvements to reduce or eliminate waste. Continuous improvement involves continuous improvement of processes and people as well as tools.