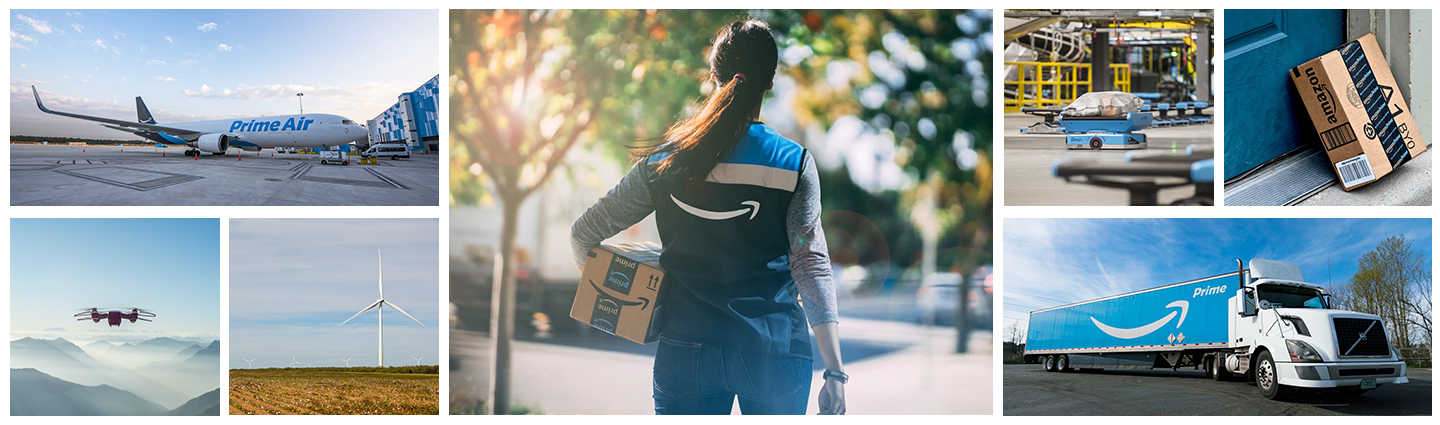
As the Internet of Things (IoT) transforms the manufacturing industry, cybersecurity for manufacturers is critical. Companies must protect their assets, customer information, designs, and intellectual property in light of rising cyberattacks. Companies can stay safe and resilient by utilizing the right technology. You can ensure the safety and security of your industrial equipment with physical security systems that include cameras, locks, access cards, and cameras.
Kaspersky Labs reports that one third of all cybersecurity incidents target manufacturers. These types of threats are more common and complex. These threats can include malware and phishing, as well as ransomware. Manufacturers must protect their intellectual property, formulas, designs, and products. It is also crucial to have a strategy in place that minimizes cyberattacks.
Cybersecurity is essential for protecting data and information of manufacturers such as customer order details, product specifications, and design plans. The plan should also include how to react to a possible cyber attack. This can run between $3 to $6 million. Companies are more vulnerable to data breaches, theft, and disruption of production. Many manufacturers find it difficult to keep up with cyberattacks.
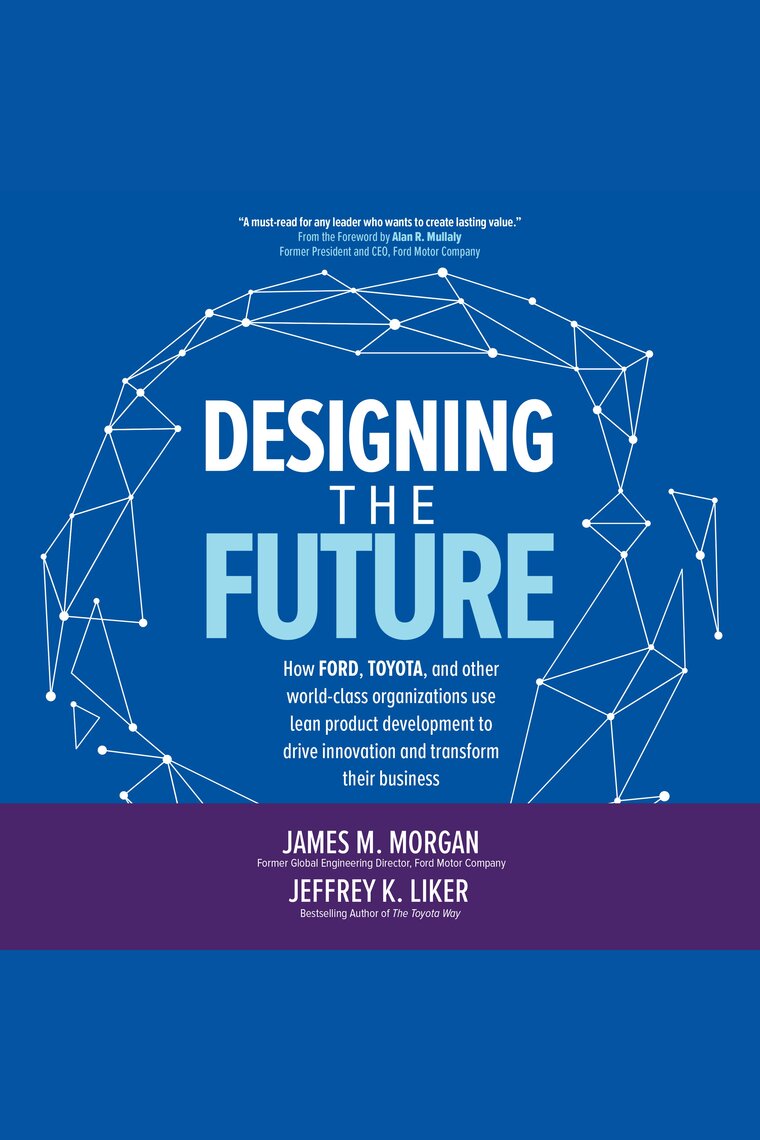
Security for manufacturers is crucial to protect employee and customer data as well the company’s reputation and revenue. It is crucial to perform a thorough audit of all your systems in order to find vulnerabilities and assess your overall readiness.
For help and resources, contact your local Manufacturing Executive Program center. Get expert advice about how to keep your business safe from cyberattacks.
It's important to not only conduct an audit of your systems but also to create a backup plan. It's also crucial to test your system regularly to ensure it works as intended. You can lower the chance of an attack by creating hard copies of key documents, and setting up a process to test the effectiveness of your system.
Many manufacturers aren't using cybersecurity measures, such as data standards. A majority of OEMs are still using non-compliant processes, hardware, and software. But, companies are increasingly investing in digital technology. Information-related technologies, including networked devices, sensors, cloud computing and networked machines are revolutionizing the industry. While the Internet of Things (IoT) and the increased globalization of the industry have sparked new concerns, a cybersecurity strategy can ensure that your organization is protected.
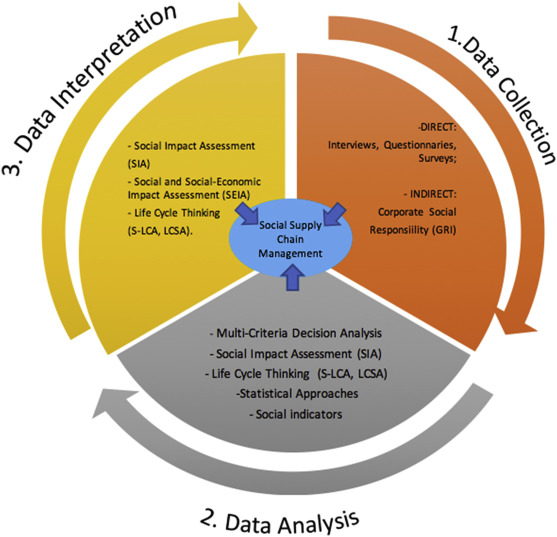
It is essential to understand the specific requirements of each manufacturing industry when designing a cybersecurity plan. Global manufacturers must comply with specific standards, based on country, region or partner, for example. However, smaller or medium-sized companies often have more stringent cybersecurity policy. No matter your company size, it is important to have a comprehensive plan in place to protect your business against cyberattacks.
The Cybersecurity Framework for Manufacturers from the National Institute of Standards and Technology (NIST) is a resource to help manufacturers protect their businesses from cyberattacks. This framework is a roadmap to manage cybersecurity activities in various sectors, including industrial manufacturing.
FAQ
What does it mean to warehouse?
A warehouse or storage facility is where goods are stored before they are sold. It can be an indoor space or an outdoor area. In some cases it could be both indoors and outdoors.
What is it like to manage a logistics company?
A successful logistics business requires a lot more than just knowledge. Good communication skills are essential to effectively communicate with your suppliers and clients. You must be able analyze data and draw out conclusions. You will need to be able handle pressure well and work in stressful situations. In order to innovate and create new ways to improve efficiency, creativity is essential. Strong leadership qualities are essential to motivate your team and help them achieve their organizational goals.
It is important to be organized and efficient in order to meet tight deadlines.
Why is logistics important for manufacturing?
Logistics are an integral part any business. They can help you achieve great success by helping you manage product flow from raw material to finished goods.
Logistics play an important role in reducing costs as well as increasing efficiency.
What is the job of a manufacturer manager?
A manufacturing manager must make sure that all manufacturing processes run smoothly and effectively. They should also be aware of any problems within the company and act accordingly.
They should also be able and comfortable communicating with other departments like sales and marketing.
They should also be aware of the latest trends in their industry and be able to use this information to help improve productivity and efficiency.
What kind of jobs are there in logistics?
There are many kinds of jobs available within logistics. Some of them are:
-
Warehouse workers - They load trucks and pallets.
-
Transport drivers - These are people who drive trucks and trailers to transport goods or perform pick-ups.
-
Freight handlers - They sort and pack freight in warehouses.
-
Inventory managers: They are responsible for the inventory and management of warehouses.
-
Sales reps - They sell products and services to customers.
-
Logistics coordinators - They organize and plan logistics operations.
-
Purchasing agents are those who purchase goods and services for the company.
-
Customer service representatives - Answer calls and email from customers.
-
Shipping clerks – They process shipping orders, and issue bills.
-
Order fillers: They fill orders based off what has been ordered and shipped.
-
Quality control inspectors are responsible for inspecting incoming and outgoing products looking for defects.
-
Other - Logistics has many other job opportunities, including transportation supervisors, logistics specialists, and cargo specialists.
Is automation important for manufacturing?
Not only is automation important for manufacturers, but it's also vital for service providers. It allows them to offer services faster and more efficiently. It helps them to lower costs by reducing human errors, and improving productivity.
How can excess manufacturing production be reduced?
In order to reduce excess production, you need to develop better inventory management methods. This would reduce the time needed to manage inventory. This could help us free up our time for other productive tasks.
A Kanban system is one way to achieve this. A Kanban board can be used to monitor work progress. Kanban systems are where work items travel through a series of states until reaching their final destination. Each state represents an individual priority level.
To illustrate, work can move from one stage or another when it is complete enough for it to be moved to a new stage. But if a task remains in the beginning stages it will stay that way until it reaches its end.
This keeps work moving and ensures no work is lost. Managers can view the Kanban board to see how much work they have done. This data allows them adjust their workflow based upon real-time data.
Lean manufacturing is another option to control inventory levels. Lean manufacturing is about eliminating waste from all stages of the production process. Anything that doesn't add value to the product is considered waste. These are some of the most common types.
-
Overproduction
-
Inventory
-
Packaging that is not necessary
-
Overstock materials
These ideas can help manufacturers improve efficiency and reduce costs.
Statistics
- You can multiply the result by 100 to get the total percent of monthly overhead. (investopedia.com)
- It's estimated that 10.8% of the U.S. GDP in 2020 was contributed to manufacturing. (investopedia.com)
- In the United States, for example, manufacturing makes up 15% of the economic output. (twi-global.com)
- (2:04) MTO is a production technique wherein products are customized according to customer specifications, and production only starts after an order is received. (oracle.com)
- Many factories witnessed a 30% increase in output due to the shift to electric motors. (en.wikipedia.org)
External Links
How To
Six Sigma and Manufacturing
Six Sigma can be described as "the use of statistical process control (SPC), techniques to achieve continuous improvement." Motorola's Quality Improvement Department in Tokyo, Japan developed Six Sigma in 1986. The basic idea behind Six Sigma is to improve quality by improving processes through standardization and eliminating defects. Many companies have adopted Six Sigma in recent years because they believe that there are no perfect products and services. Six Sigma's main objective is to reduce variations from the production average. If you take a sample and compare it with the average, you will be able to determine how much of the production process is different from the norm. If it is too large, it means that there are problems.
Understanding how your business' variability is a key step towards Six Sigma implementation is the first. Once you've understood that, you'll want to identify sources of variation. These variations can also be classified as random or systematic. Random variations are caused when people make mistakes. While systematic variations are caused outside of the process, they can occur. If you make widgets and some of them end up on the assembly line, then those are considered random variations. If however, you notice that each time you assemble a widget it falls apart in exactly the same spot, that is a problem.
Once you've identified the problem areas you need to find solutions. You might need to change the way you work or completely redesign the process. To verify that the changes have worked, you need to test them again. If they fail, you can go back to the drawing board to come up with a different plan.