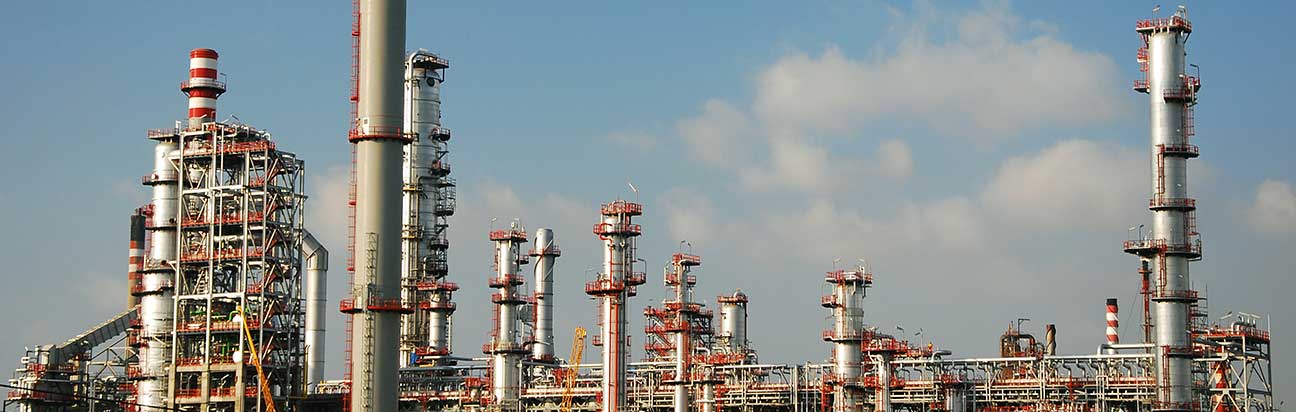
There are a wide variety of logistics jobs in Tampa. You will find many in the construction, healthcare and manufacturing industries. But you can also get a job in the wholesale industry or consult for firms that help different types of companies streamline their supply chains.
A degree or diploma in logistics can offer a range of career possibilities. An associate degree can help you find entry-level roles such as shipping clerks. However, bachelor's level jobs are reserved for those with a higher education. You can choose to specialize, depending on your interests and goals, in a particular area of logistics such as supply chain management or warehousing.
BLS data predicts that careers in logistics will grow. Between 2018 and 2028, employment for these professionals is expected to increase by 5%. Professionals who focus on business operations are projected to see even greater job growth.
You can earn a logistics degree at a community college or a four-year university. These programs often offer different logistics concentrations to help you develop your skills and be more employable.
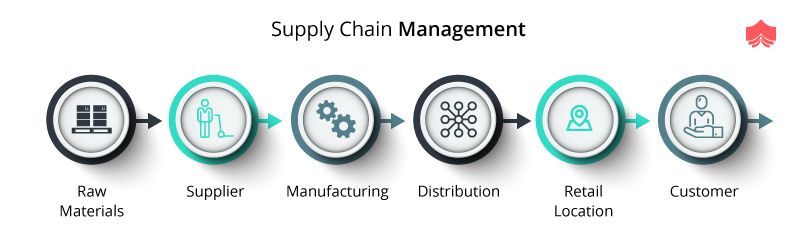
Consider networking and doing internships as part of your bachelor's program. These experiences give you valuable hands-on experience in the field, and they can help you find your first logistics job.
The logistics industry has a diverse workforce, and job prospects are generally good. There are many logistics jobs available across the nation, especially in large, growing states like California and Texas. You can find jobs in many different sectors such as oil and gas, aerospace or other.
Consider the size and capability of a company when selecting a logistics service. You should choose a 3PL who understands your business, and can provide you with a tailored solution that meets your needs. It will help you reduce costs and improve efficiency.
Supply chain management is crucial to your business' success. The right people and tools are needed to make sure that your products reach their destination at the right time and in the best condition. Select a third party logistics provider who has experience in your industry, and who can deliver your goods on time.
Sheer, an integrated 3PL with a Tampa base, can reduce costs and improve supply chain efficiency. We offer our clients a variety services, including transportation management, inventory control, and shipping.
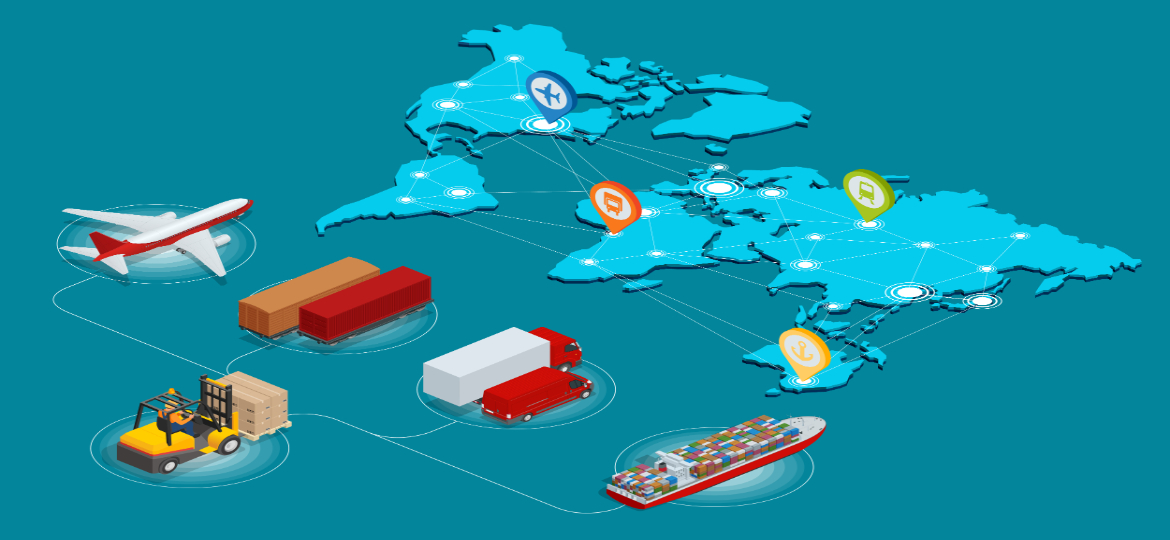
We offer a range of technology tools that will help you manage and track your supply chain. Cloud-based solutions that are integrated into your existing ERP systems make it easy to monitor, control and manage all aspects your business.
Sheer's multimodal network can transform your supply chains from liabilities to assets. You can count on Sheer to deliver your goods safely, on time and every time.
FAQ
What are the 4 types of manufacturing?
Manufacturing is the process that transforms raw materials into useful products. It involves many different activities such as designing, building, testing, packaging, shipping, selling, servicing, etc.
What is the role of a production manager?
Production planners ensure that all project aspects are completed on time, within budget and within the scope. They also ensure that the product/service meets the client’s needs.
What does the term manufacturing industries mean?
Manufacturing Industries are companies that manufacture products. Consumers are people who purchase these goods. To accomplish this goal, these companies employ a range of processes including distribution, sales, management, and production. They create goods from raw materials, using machines and various other equipment. This covers all types of manufactured goods including clothing, food, building supplies and furniture, as well as electronics, tools, machinery, vehicles and pharmaceuticals.
What is the job of a logistics manger?
Logistics managers make sure all goods are delivered on schedule and without damage. This is done through his/her expertise and knowledge about the company's product range. He/she must also ensure sufficient stock to meet the demand.
Statistics
- [54][55] These are the top 50 countries by the total value of manufacturing output in US dollars for its noted year according to World Bank.[56] (en.wikipedia.org)
- According to the United Nations Industrial Development Organization (UNIDO), China is the top manufacturer worldwide by 2019 output, producing 28.7% of the total global manufacturing output, followed by the United States, Japan, Germany, and India.[52][53] (en.wikipedia.org)
- In the United States, for example, manufacturing makes up 15% of the economic output. (twi-global.com)
- You can multiply the result by 100 to get the total percent of monthly overhead. (investopedia.com)
- Many factories witnessed a 30% increase in output due to the shift to electric motors. (en.wikipedia.org)
External Links
How To
How to Use the Just In Time Method in Production
Just-in-time (JIT) is a method that is used to reduce costs and maximize efficiency in business processes. It allows you to get the right amount resources at the right time. This means that only what you use is charged to your account. Frederick Taylor was the first to coin this term. He developed it while working as a foreman during the early 1900s. Taylor observed that overtime was paid to workers if they were late in working. He concluded that if workers were given enough time before they start work, productivity would increase.
JIT is about planning ahead. You should have all the necessary resources ready to go so that you don’t waste money. The entire project should be looked at from start to finish. You need to ensure you have enough resources to tackle any issues that might arise. If you anticipate that there might be problems, you'll have enough people and equipment to fix them. You won't have to pay more for unnecessary items.
There are many types of JIT methods.
-
Demand-driven: This type of JIT allows you to order the parts/materials required for your project on a regular basis. This will enable you to keep track of how much material is left after you use it. You'll also be able to estimate how long it will take to produce more.
-
Inventory-based: This type allows you to stock the materials needed for your projects ahead of time. This allows one to predict how much they will sell.
-
Project-driven: This means that you have enough money to pay for your project. If you know the amount you require, you can buy the materials you need.
-
Resource-based: This is the most common form of JIT. Here you can allocate certain resources based purely on demand. If you have many orders, you will assign more people to manage them. If there aren't many orders, you will assign fewer people.
-
Cost-based : This is similar in concept to resource-based. But here, you aren't concerned about how many people your company has but how much each individual costs.
-
Price-based pricing: This is similar in concept to cost-based but instead you look at how much each worker costs, it looks at the overall company's price.
-
Material-based: This approach is similar to cost-based. However, instead of looking at the total cost for the company, you look at how much you spend on average on raw materials.
-
Time-based: Another variation of resource-based JIT. Instead of focusing solely on the amount each employee costs, focus on how long it takes for the project to be completed.
-
Quality-based JIT - This is another form of resource-based JIT. Instead of thinking about how much each employee costs or how long it takes to manufacture something, you think about how good the quality of your product is.
-
Value-based JIT: This is the latest form of JIT. In this case, you're not concerned with how well the products perform or whether they meet customer expectations. Instead, you are focused on adding value to the marketplace.
-
Stock-based: This stock-based method focuses on the actual quantity of products being made at any given time. It's used when you want to maximize production while minimizing inventory.
-
Just-in-time planning (JIT): This is a combination JIT and supply-chain management. It's the process of scheduling delivery of components immediately after they are ordered. It's important because it reduces lead times and increases throughput.