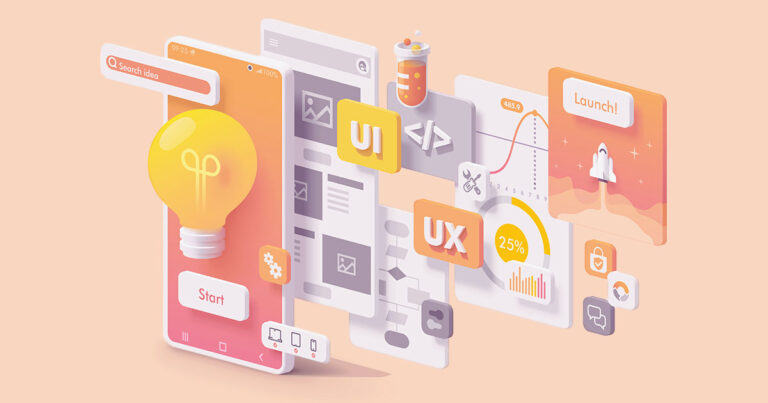
A Chemical Technician works as an artisan in the production and maintenance of chemical products. The technician is responsible for testing the materials used in manufacturing. They may work in research and development, in manufacturing lines or laboratories.
They are usually supervising by chemists. They oversee the quality of the product and test new materials. They may be promoted as they gain more experience. Pharmacists are one of the many companies that hire them. A bachelor's degree in engineering, biology, and chemistry can help you earn more.
Although pay for Chemical Technicians can vary widely by region, the typical salary for this position in the United States is $48,990. This includes bonuses and taxable wages. It also takes into account the skills, education, and experience of workers. Chemical Technicians with the highest earnings earned more than $60,000 annually.
A Chemical Technician's job duties include conducting research and developing pharmaceuticals and chemicals. These technicians analyze the ingredients of medicines, food, and other products. They are also able to supervise workers at the production line.
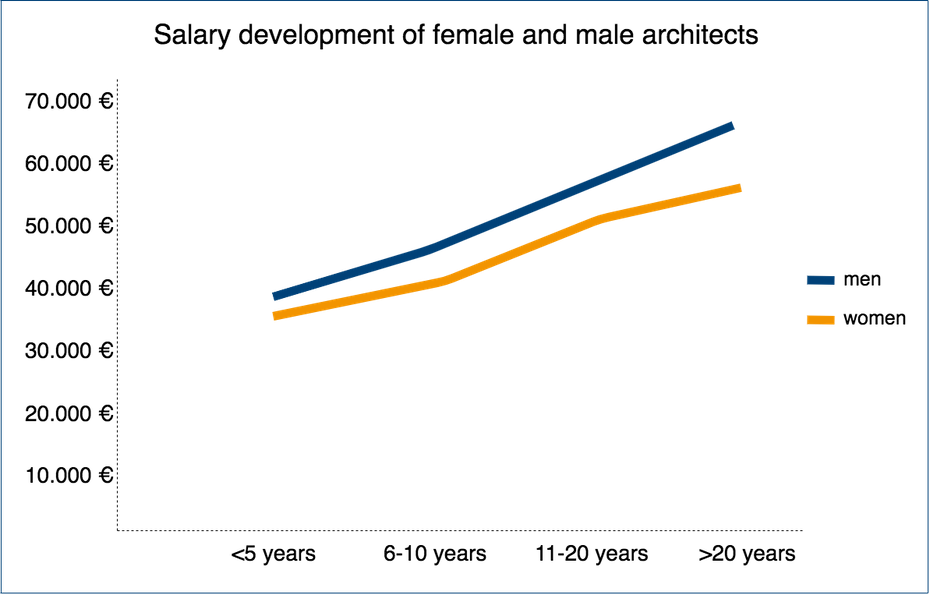
You will need an associate's/bachelor's degree to be a Chemical Technician. You can also earn a graduate degree or doctoral. Many companies prefer to hire chemical techs with college degrees. A master's degree may be required for other jobs.
You can find out about employment opportunities by visiting a school placement office. There are many job banks available online. Another good resource is the American Chemical Society. Local chapters are often able to post job listings.
A job as a Chemical Technie is a long-term position. While most laboratories have a seven-day work week, some experienced workers are sometimes called in to perform odd-hours experiments or inspections.
Most of the Chemical Technicians' salaries range between $36,000 and $47,000. Expert workers may earn as much as $11,000 more. Entry-level workers earn between $15 and 18 an hour.
San Francisco, San Jose and San Jose are two of the top cities for Chemical Technician salary. The national average was beaten by more than 20 percent in both cities. The BLS also reported that Chemical Technicians working in these areas made more than $83,600.
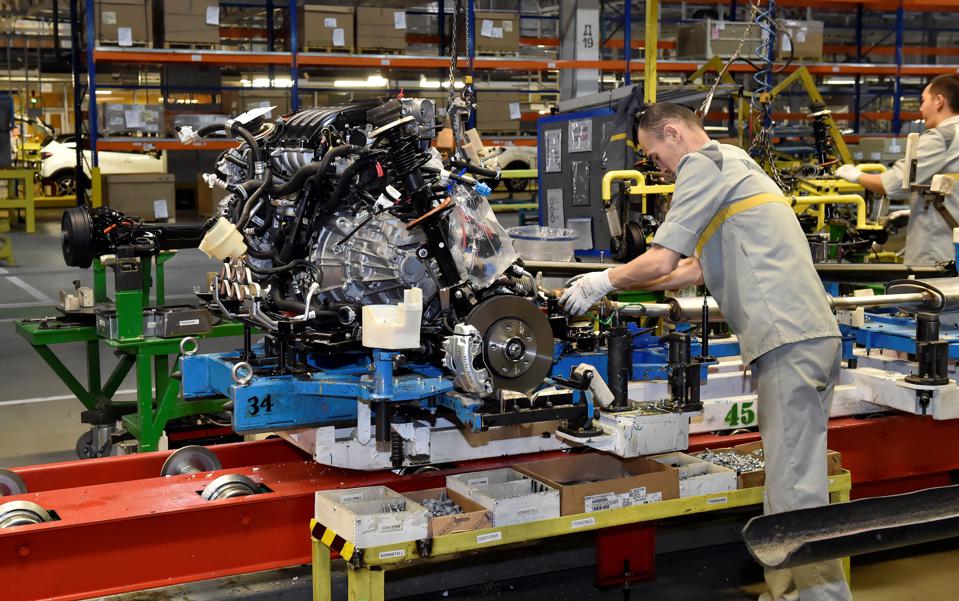
The Bureau of Labor Statistics says that Chemical Technicians' job growth will be slower than the average. While their employment is expected increase by 3 percentage points through 2014, the number will grow only by 4 percent over ten years. There will likely be a greater demand for skilled technicians because of this.
With the rise of environmental issues, the demand for chemistry R&D will increase. These workers will find the most rewarding jobs in laboratories that conduct testing on new materials.
FAQ
What skills is required for a production planner?
Being a production planner is not easy. You need to be organized and flexible. Also, you must be able and willing to communicate with clients and coworkers.
What's the difference between Production Planning & Scheduling?
Production Planning (PP) is the process of determining what needs to be produced at any given point in time. This is done through forecasting demand and identifying production capacities.
Scheduling is the process that assigns dates to tasks so they can get completed within a given timeframe.
What is the job of a manufacturer manager?
A manufacturing manager has to ensure that all manufacturing processes work efficiently and effectively. They should also be aware of any problems within the company and act accordingly.
They should also be able communicate with other departments, such as sales or marketing.
They must also keep up-to-date with the latest trends in their field and be able use this information to improve productivity and efficiency.
Are there ways to automate parts of manufacturing?
Yes! Yes. Automation has been around since ancient time. The Egyptians discovered the wheel thousands and years ago. Robots are now used to assist us in assembly lines.
There are many applications for robotics in manufacturing today. These include:
-
Assembly line robots
-
Robot welding
-
Robot painting
-
Robotics inspection
-
Robots that create products
Manufacturing could also benefit from automation in other ways. For instance, 3D printing allows us make custom products and not have to wait for months or even weeks to get them made.
Statistics
- According to a Statista study, U.S. businesses spent $1.63 trillion on logistics in 2019, moving goods from origin to end user through various supply chain network segments. (netsuite.com)
- It's estimated that 10.8% of the U.S. GDP in 2020 was contributed to manufacturing. (investopedia.com)
- In the United States, for example, manufacturing makes up 15% of the economic output. (twi-global.com)
- (2:04) MTO is a production technique wherein products are customized according to customer specifications, and production only starts after an order is received. (oracle.com)
- According to the United Nations Industrial Development Organization (UNIDO), China is the top manufacturer worldwide by 2019 output, producing 28.7% of the total global manufacturing output, followed by the United States, Japan, Germany, and India.[52][53] (en.wikipedia.org)
External Links
How To
How to use Lean Manufacturing in the production of goods
Lean manufacturing is an approach to management that aims for efficiency and waste reduction. It was developed by Taiichi Okono in Japan, during the 1970s & 1980s. TPS founder Kanji Takoda awarded him the Toyota Production System Award (TPS). Michael L. Watkins published the original book on lean manufacturing, "The Machine That Changed the World," in 1990.
Lean manufacturing can be described as a set or principles that are used to improve quality, speed and cost of products or services. It emphasizes the elimination and minimization of waste in the value stream. Lean manufacturing is called just-in-time (JIT), zero defect, total productive maintenance (TPM), or 5S. Lean manufacturing eliminates non-value-added tasks like inspection, rework, waiting.
Lean manufacturing can help companies improve their product quality and reduce costs. Additionally, it helps them achieve their goals more quickly and reduces employee turnover. Lean manufacturing has been deemed one of the best ways to manage the entire value-chain, including customers, distributors as well retailers and employees. Many industries worldwide use lean manufacturing. Toyota's philosophy is the foundation of its success in automotives, electronics and appliances, healthcare, chemical engineers, aerospace, paper and food, among other industries.
Lean manufacturing includes five basic principles:
-
Define value - Find out what your business contributes to society, and what makes it different from other competitors.
-
Reduce Waste - Remove any activity which doesn't add value to your supply chain.
-
Create Flow - Ensure work moves smoothly through the process without interruption.
-
Standardize & simplify - Make processes consistent and repeatable.
-
Develop Relationships: Establish personal relationships both with internal and external stakeholders.
Although lean manufacturing isn't a new concept in business, it has gained popularity due to renewed interest in the economy after the 2008 global financial crisis. Many businesses have adopted lean production techniques to make them more competitive. Economists think that lean manufacturing is a crucial factor in economic recovery.
Lean manufacturing has many benefits in the automotive sector. These benefits include increased customer satisfaction, reduced inventory levels and lower operating costs.
Lean manufacturing can be applied to almost every aspect of an organization. This is because it ensures efficiency and effectiveness in all stages of the value chain.
There are three types of lean manufacturing.
-
Just-in-Time Manufacturing: Also known as "pull systems", this type of lean manufacturing uses just-in-time manufacturing (JIT). JIT refers to a system in which components are assembled at the point of use instead of being produced ahead of time. This approach is designed to reduce lead times and increase the availability of components. It also reduces inventory.
-
Zero Defects Manufacturing (ZDM),: ZDM is a system that ensures no defective units are left the manufacturing facility. If a part needs to be fixed during the assembly line, it should be repaired rather than scrapped. This also applies to finished products that need minor repairs before being shipped.
-
Continuous Improvement (CI: Continuous improvement aims to increase the efficiency of operations by constantly identifying and making improvements to reduce or eliminate waste. Continuous Improvement (CI) involves continuous improvement in processes, people, tools, and infrastructure.