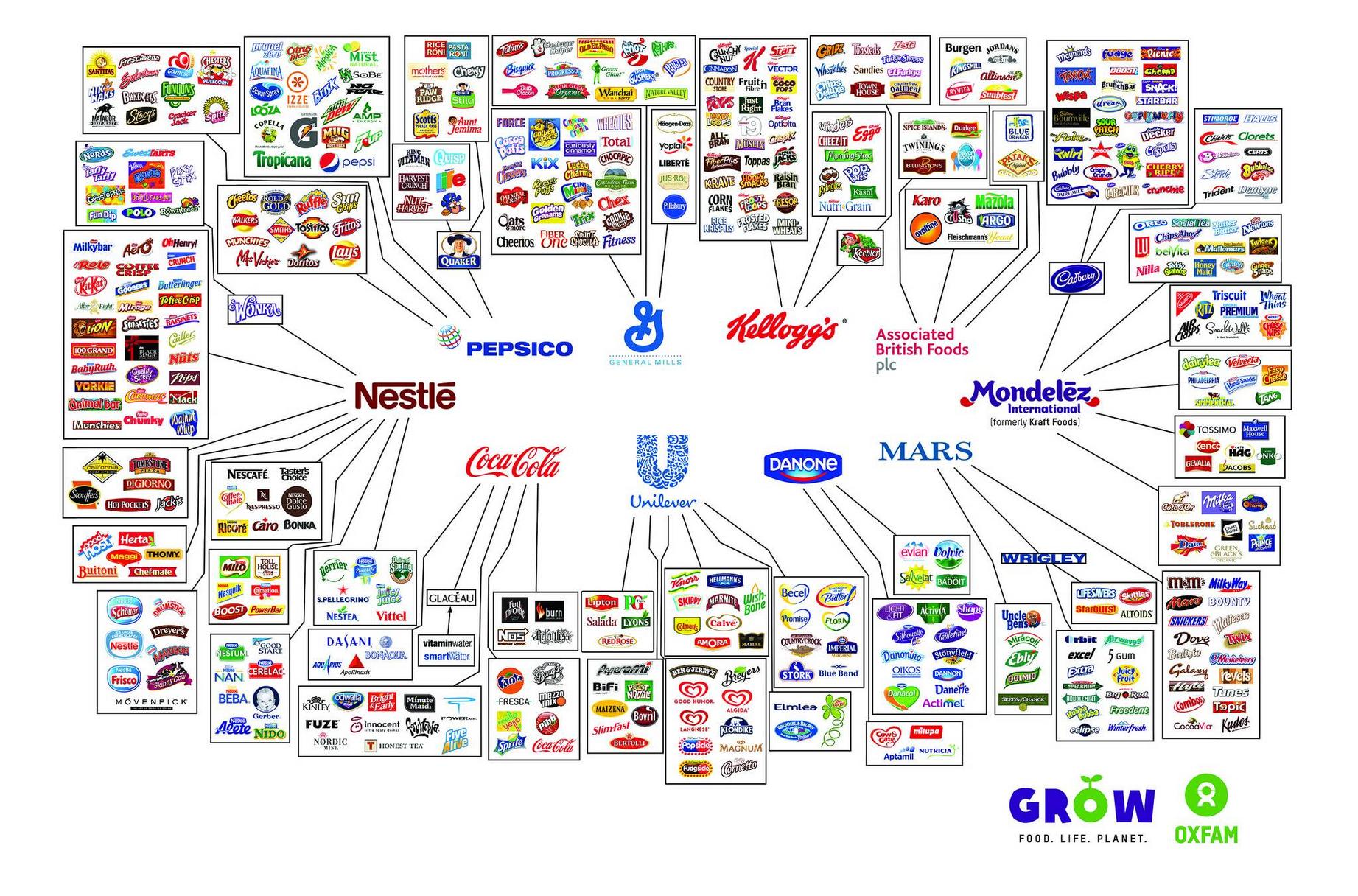
Manufacturing failures can be caused by many things. These include poor design, cost cutting initiatives, lackluster quality control, and more. There are ways to improve quality and avoid these issues.
Does lean manufacturing actually work?
In many cases companies that implement lean methods are very successful. These companies have been able to reduce waste and improve cycles times among other benefits. However, this is done with much trial and mistake and failure.
All lean practitioners agree that ownership and senior management are responsible for the majority of failures. The people in charge of the company are usually not aware of how to implement lean.
It can be difficult to motivate employees and achieve desired results. This is why it's crucial to start a skills assessment long before implementing lean methods. You will be able to avoid ambiguity when you know who can help achieve your goals and who needs to go.
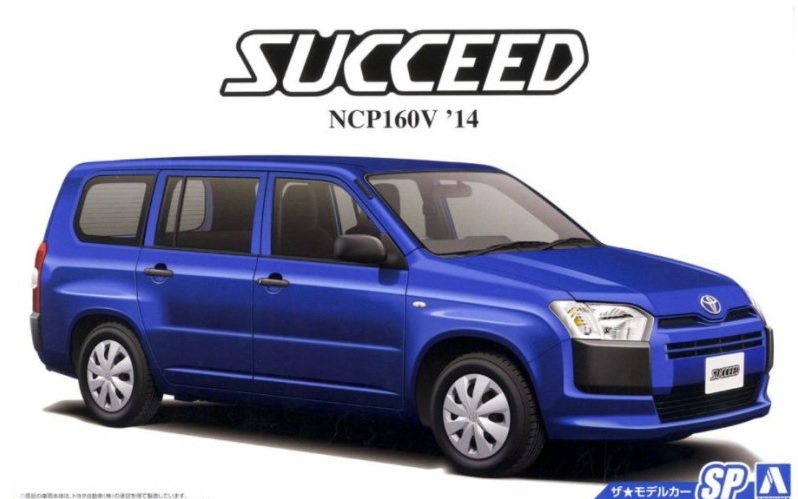
Why do manufacturers fail?
Some manufacturing mistakes are caused because the manufacturer used the wrong material or didn't implement proper quality assurance measures. Other defects are caused by manufacturing errors, which are when a product is made in a way that it's not designed to be. These mistakes can be expensive to fix and can even result in loss of revenue for the company.
These problems can be costly for the manufacturer and for consumers, which is why it's so important to ensure that products are manufactured correctly. Companies need to be able recognize failures in the early stages of manufacturing and fix them as soon possible to avoid these problems.
To achieve this goal, manufacturers must understand the causes of failures. This will help them improve their processes and reduce costs.
A manufacturer's failure is often due to a lack of capital. This can be caused by a number of different factors, but it's important to remember that a company needs to have sufficient funds to continue production and sales in the long term.
A company that lacks the funds necessary to manufacture a particular product can create problems both for the manufacturer as well as for the customer. This can lead to a variety of issues, such as a delay in delivery or lower prices for the product.
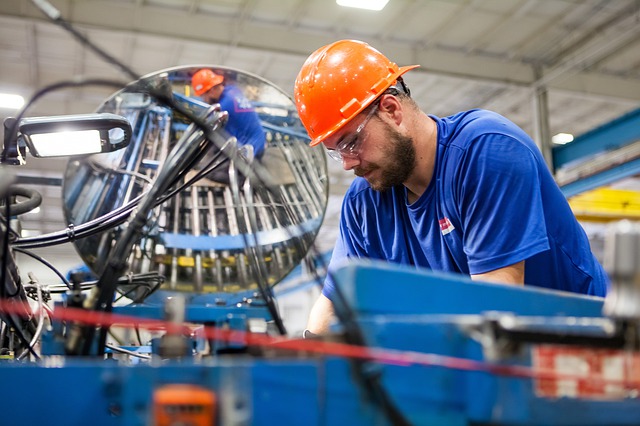
Also, the product may cause injury to a consumer who is using it in an unsafe fashion. If a person breaks their bone after playing with a lit match, the manufacturer could be held responsible for failing to warn the victim about the fire-starting risk.
This is a dangerous situation for children, who may not be familiar with handling hazardous substances. This can be an expensive problem for the manufacturer, but is vital to any business that wants to remain in business.
FAQ
What does the term manufacturing industries mean?
Manufacturing Industries are businesses that produce products for sale. Consumers are those who purchase these products. These companies use various processes such as production, distribution, retailing, management, etc., to fulfill this purpose. These companies produce goods using raw materials and other equipment. This includes all types of manufactured goods, including food items, clothing, building supplies, furniture, toys, electronics, tools, machinery, vehicles, pharmaceuticals, medical devices, chemicals, and many others.
How can overproduction in manufacturing be reduced?
Improved inventory management is the key to reducing overproduction. This would reduce time spent on activities such as purchasing, stocking, and maintaining excess stock. By doing this, we could free up resources for other productive tasks.
A Kanban system is one way to achieve this. A Kanbanboard is a visual tool that allows you to keep track of the work being done. In a Kanban system, work items move through a sequence of states until they reach their final destination. Each state represents an individual priority level.
As an example, if work is progressing from one stage of the process to another, then the current task is complete and can be transferred to the next. But if a task remains in the beginning stages it will stay that way until it reaches its end.
This keeps work moving and ensures no work is lost. With a Kanban board, managers can see exactly how much work is being done at any given moment. This data allows them adjust their workflow based upon real-time data.
Lean manufacturing, another method to control inventory levels, is also an option. Lean manufacturing emphasizes eliminating waste in all phases of production. Anything that doesn't add value to the product is considered waste. There are several types of waste that you might encounter:
-
Overproduction
-
Inventory
-
Unnecessary packaging
-
Exceed materials
Manufacturers can increase efficiency and decrease costs by implementing these ideas.
How can efficiency in manufacturing be improved?
First, we need to identify which factors are most critical in affecting production times. We then need to figure out how to improve these variables. If you don’t know where to begin, consider which factors have the largest impact on production times. Once you have identified them, it is time to identify solutions.
What type of jobs is there in logistics
Logistics can offer many different jobs. Some of them are:
-
Warehouse workers: They load and unload trucks, pallets, and other cargo.
-
Transportation drivers: They drive trucks and trailers and deliver goods and make pick-ups.
-
Freight handlers - They sort and pack freight in warehouses.
-
Inventory managers: They are responsible for the inventory and management of warehouses.
-
Sales representatives: They sell products to customers.
-
Logistics coordinators are responsible for organizing and planning logistics operations.
-
Purchasing agents are those who purchase goods and services for the company.
-
Customer service representatives - They answer calls and emails from customers.
-
Shippers clerks - They process shipping order and issue bills.
-
Order fillers: They fill orders based off what has been ordered and shipped.
-
Quality control inspectors (QCI) - They inspect all incoming and departing products for potential defects.
-
Others - There are many types of jobs in logistics such as transport supervisors and cargo specialists.
Can some manufacturing processes be automated?
Yes! Since ancient times, automation has been in existence. The Egyptians discovered the wheel thousands and years ago. Today, robots assist in the assembly of lines.
Robotics is used in many manufacturing processes today. These include:
-
Robots for assembly line
-
Robot welding
-
Robot painting
-
Robotics inspection
-
Robots create products
Automation can be applied to manufacturing in many other ways. 3D printing makes it possible to produce custom products in a matter of days or weeks.
What is the role and responsibility of a Production Planner?
Production planners make sure that every aspect of the project is delivered on-time, within budget, and within schedule. A production planner ensures that the service and product meet the client's expectations.
Statistics
- [54][55] These are the top 50 countries by the total value of manufacturing output in US dollars for its noted year according to World Bank.[56] (en.wikipedia.org)
- According to the United Nations Industrial Development Organization (UNIDO), China is the top manufacturer worldwide by 2019 output, producing 28.7% of the total global manufacturing output, followed by the United States, Japan, Germany, and India.[52][53] (en.wikipedia.org)
- In 2021, an estimated 12.1 million Americans work in the manufacturing sector.6 (investopedia.com)
- According to a Statista study, U.S. businesses spent $1.63 trillion on logistics in 2019, moving goods from origin to end user through various supply chain network segments. (netsuite.com)
- Job #1 is delivering the ordered product according to specifications: color, size, brand, and quantity. (netsuite.com)
External Links
How To
How to Use 5S for Increasing Productivity in Manufacturing
5S stands for "Sort", 'Set In Order", 'Standardize', & Separate>. Toyota Motor Corporation was the first to develop the 5S approach in 1954. It allows companies to improve their work environment, thereby achieving greater efficiency.
This method has the basic goal of standardizing production processes to make them repeatable. This means that daily tasks such as cleaning and sorting, storage, packing, labeling, and packaging are possible. Because workers know what they can expect, this helps them perform their jobs more efficiently.
Five steps are required to implement 5S: Sort, Set In Order, Standardize. Separate. Each step involves a different action which leads to increased efficiency. If you sort items, it makes them easier to find later. When you set items in an order, you put items together. Then, after you separate your inventory into groups, you store those groups in containers that are easy to access. Finally, when you label your containers, you ensure everything is labeled correctly.
Employees need to reflect on how they do their jobs. Employees need to understand the reasons they do certain jobs and determine if there is a better way. To be successful in the 5S system, employees will need to acquire new skills and techniques.
In addition to increasing efficiency, the 5S method also improves morale and teamwork among employees. They are more motivated to achieve higher efficiency levels as they start to see improvement.